Why This Isn’t Just Another Alloy Comparison
For international wholesale buyers, the core question isn’t just what metal is stronger or more corrosion-resistant—it’s which material delivers the right results in production, assembly, and supply chain integration. When choosing between bronze and brass, your decision directly impacts costs, quality, and the long-term performance of your end products.
At YISHANG, we’ve worked with OEM/ODM clients from over 50 countries, supplying customized brass and bronze components across a variety of sectors—from electronics to construction. This article shares our experience-backed insights to help global buyers make confident sourcing decisions.
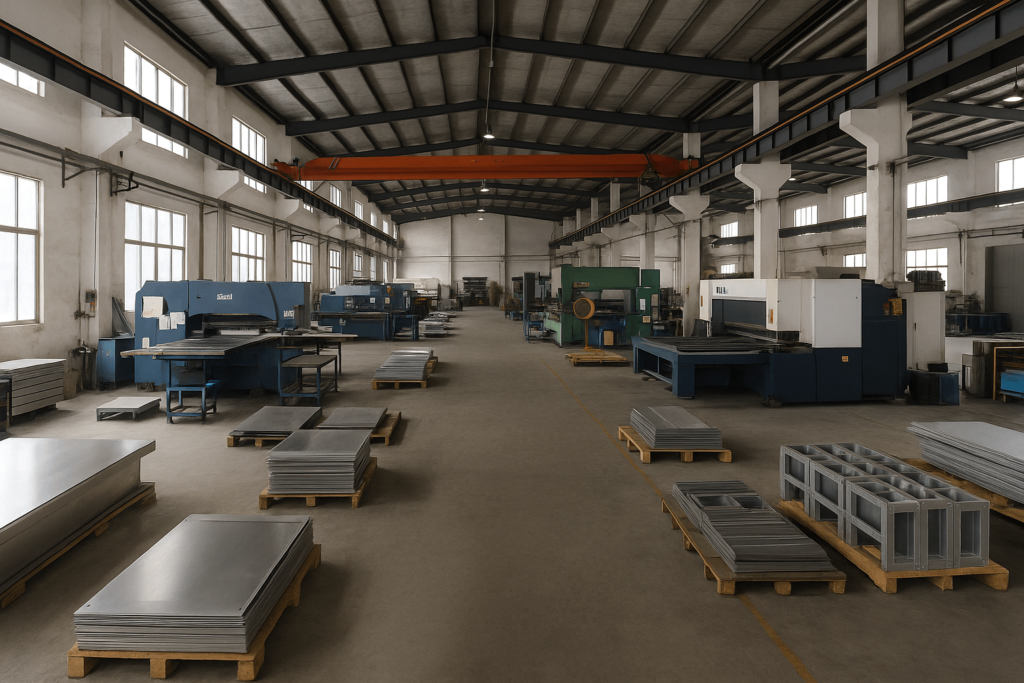
What Sets Bronze and Brass Apart?
Both alloys belong to the copper family. Brass is a copper and zinc alloy, while bronze is primarily copper and tin, though variations include aluminum bronze, silicon bronze, and others. That small difference in alloying elements translates into significant functional distinctions.
Brass offers excellent machinability and is ideal for components requiring high production throughput, such as electrical terminals, decorative hardware, and enclosures. Its relatively low cost and ease of forming make it attractive for large-scale manufacturing.
Bronze, particularly aluminum or phosphor bronze, has higher tensile strength, better fatigue resistance, and superior durability. It’s often used in demanding applications like bearings, gears, and marine parts. For buyers seeking longevity in critical environments, bronze often yields higher ROI over time.
Industry Evolution and Procurement Logic
Brass and bronze have evolved with industrial needs. Bronze, one of the earliest alloys in human history, has been used for centuries in maritime and military applications due to its strength and resistance to corrosion.
Brass gained popularity in the modern industrial era thanks to its formability, appearance, and cost-efficiency. From a sourcing standpoint, the choice between the two depends less on historical usage and more on material behavior under operational demands.
For buyers, understanding this evolution means identifying which alloy aligns better with your volume goals, processing methods, and intended use conditions.
Performance in Real Conditions
Mechanical Strength and Fatigue Resistance
Bronze alloys, such as C95400 aluminum bronze, offer tensile strength up to 850 MPa. They maintain structural integrity under stress, which is critical for rotating parts like bronze gears or load-bearing bushings.
Brass, especially 360 brass alloy, provides enough strength for low-load parts and performs well where intricate machining is needed. It’s suitable for 2mm brass components like plates or fixtures in consumer hardware.
Corrosion Resistance & Environmental Behavior
Bronze excels in corrosive environments. Its natural resistance to oxidation and biofouling—especially in alloys like naval bronze—makes it ideal for marine hardware and outdoor assemblies.
High-zinc brass alloys are more vulnerable to dezincification, especially when exposed to chlorides. However, in dry indoor environments, brass offers good resistance and is easier to finish with coatings or plating.
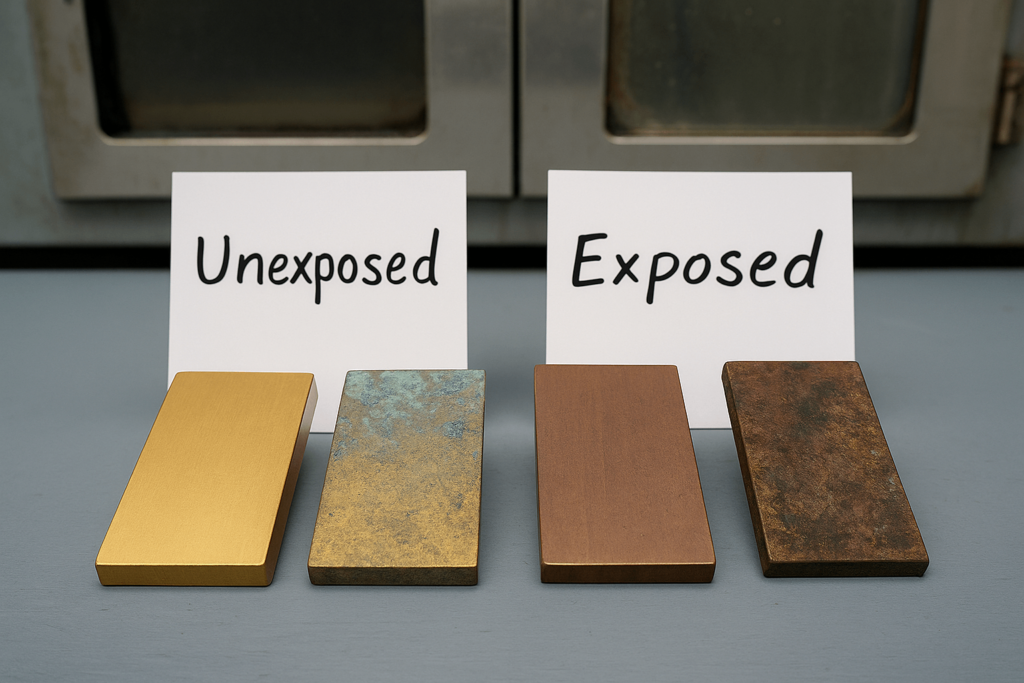
Electrical and Thermal Conductivity
Brass electrical conductivity (up to 28% IACS) surpasses that of bronze, making it better suited for conductive components, switch terminals, and low-voltage bus bars. It also offers better heat dissipation, making it preferable for thermal-contact parts.
Bronze conductivity is lower, but it remains stable under both heat and mechanical load, making it effective in heat-resistant structural elements.
Fabrication, Lead Time, and Waste Rates
Sourcing professionals don’t just compare alloy specs—they assess production realities. Brass offers excellent performance in CNC turning and high-speed machining. For instance, 360 brass alloy machining supports minimal tool wear, tight tolerances, and fast cycle times.
Bronze is more abrasive and reduces tool life, though certain grades like C93200 strike a balance. In return, bronze may reduce the need for additional treatment steps due to its built-in hardness and bronze corrosion resistance.
For buyers managing third-party manufacturing, material behavior affects scrap rates, rejection rates, and tooling investment. Brass allows high-speed stamping and drawing, while bronze may require pre-heating or annealing, which affects lead time.
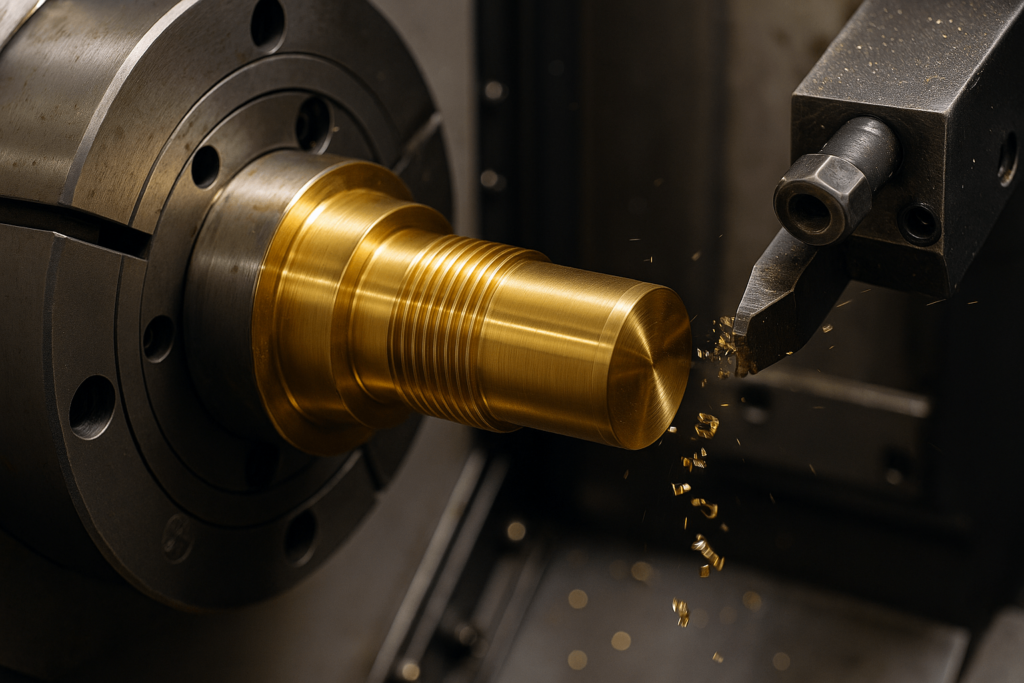
Application Logic: Matching Alloys to Procurement Goals
Sourcing decisions must reflect not just performance, but how each metal aligns with manufacturing strategy.
Brass (Copper + Zinc) Advantages:
Low cost per kg and high volume yield
Best for mass-produced decorative fittings and housings
Excellent machinability for brass CNC operations
Used in anodized aluminum bronze color matching for cosmetic parts
Bronze (Copper + Tin and others) Advantages:
Long service life in outdoor, corrosive, or mechanical load environments
Suitable for bronze machine parts like bushings or bronze gear applications
Ideal for applications with high specific heat and resistance to deformation
Popular for bronze metal composition applications requiring resistance to saltwater or chemicals
At YISHANG, we guide clients through function-based material selection that aligns alloy type with component durability, ease of processing, and assembly lifecycle.
Beyond Price Per Kilogram
Alloy Type | Price (USD/kg) | Machinability | Service Life | Typical Use |
---|---|---|---|---|
Brass (C36000) | $3.50–$5.00 | Excellent | Moderate | Connectors, housings |
Bronze (C93200) | $5.50–$7.50 | Good | High | Bearings, sliders |
Bronze (C95400) | $6.50–$9.00 | Moderate | Very High | Marine gear, valves |
Don’t rely on weight-based pricing alone. Buyers must evaluate:
Cost per finished part, including material loss
Tooling changeover costs (brass outperforms in tool longevity)
Frequency of replacement or maintenance
Freight and packaging efficiency—brass is easier to stack and palletize
These practical metrics are how real procurement teams justify their decisions.
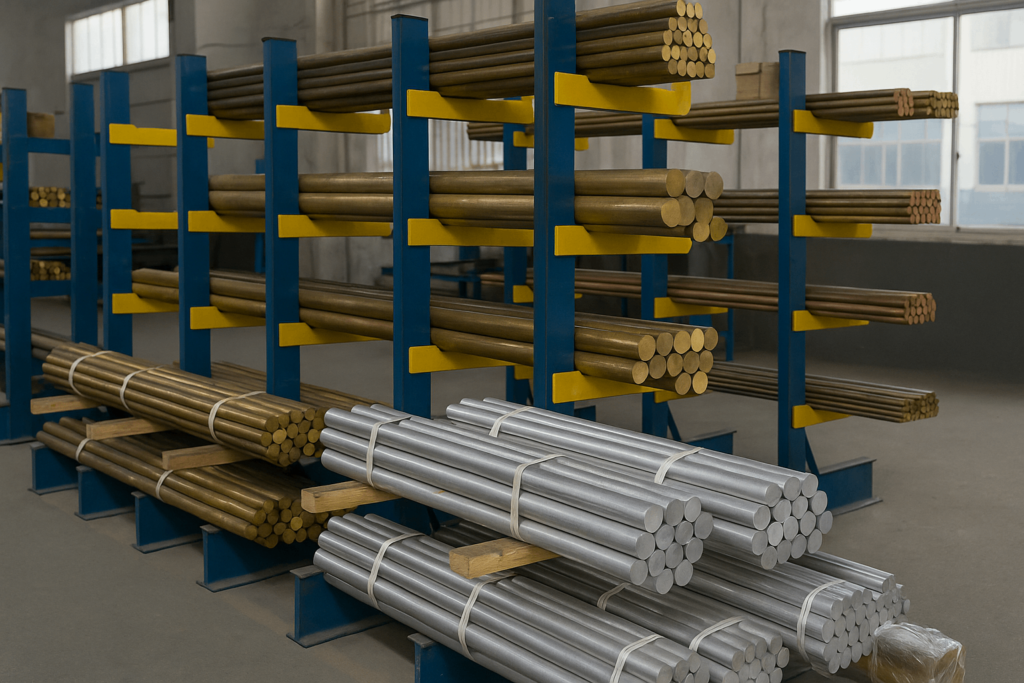
Alloy Alternatives and Substitution Guidance
Some buyers may face restrictions in availability or pricing on preferred alloys. Understanding possible substitutes is key to uninterrupted production.
Original Alloy | Viable Alternative | Key Benefit | Compromise |
C93200 (Bearing Bronze) | C86300 Manganese Bronze | Higher strength | Slightly harder to machine |
C36000 (Free Machining Brass) | C37700 Forging Brass | Better hot forming | Slightly reduced machinability |
C95400 (Aluminum Bronze) | C63000 Nickel-Aluminum Bronze | Superior corrosion resistance | Higher cost |
YISHANG routinely helps clients evaluate cross-material substitution when cost, availability, or technical upgrades are required. Always validate substitutes against end-use conditions.
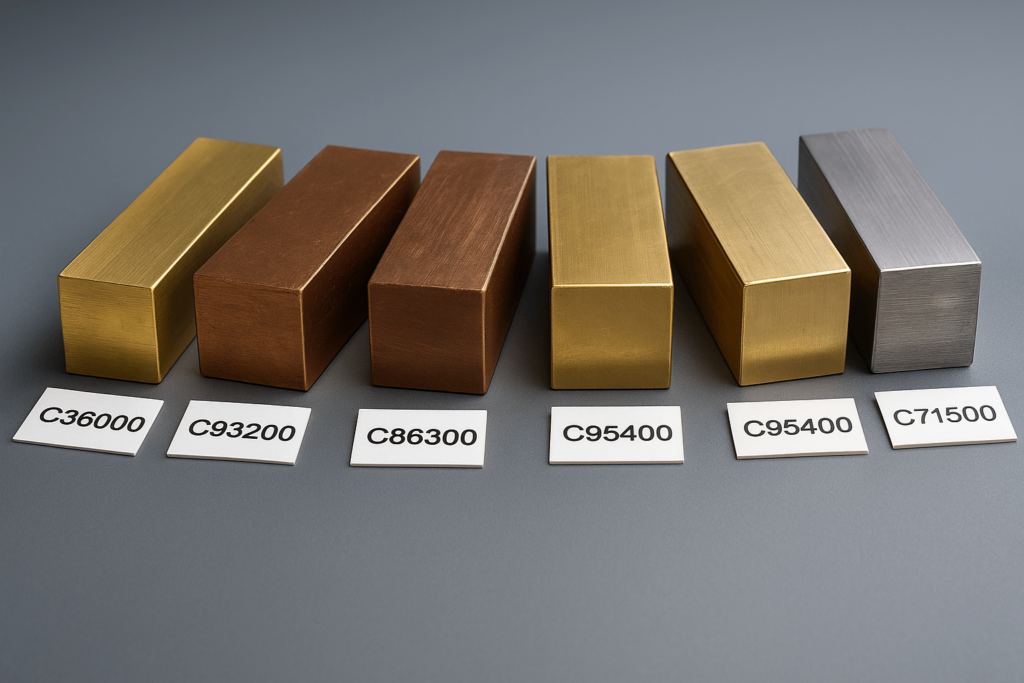
Industry-Informed FAQs
Can I use brass instead of bronze in gears?
Not ideally. Bronze gears handle torque and friction better. Brass wears faster.
Is brass an alloy of copper and zinc?
Yes. Brass is an alloy, not an element. Common grades include C36000, C26000, and red brass.
What is bronze made of?
Bronze is copper and tin, often with aluminum or phosphorus added for enhanced properties.
What’s the melting point of bronze?
It ranges from 950–1050°C. The bronze melting point depends on composition.
How much does bronze cost?
Typically between $5.50 and $9.00 per kg, depending on alloy and order volume.
Choose an Alloy. Choose the Right Supplier.
The difference between bronze and brass is about more than just metals—it’s about how your business performs under real-world conditions. A good material choice supports lower reject rates, fewer warranty claims, and more predictable production cycles.
At YISHANG, we bring 26+ years of experience in brass bronze copper component production, supporting OEM buyers across 50+ countries. We provide full services from material selection and CNC turning to packaging and export logistics.
Let’s talk about how we can support your next order with the right materials and the right guidance.