The Problem Beneath the Surface
When a finished metal part corrodes, flakes, or wears prematurely, the issue often lies not in the material—but in its surface finish. For procurement managers sourcing thousands of metal components, an inconsistent or insufficient surface treatment can disrupt supply chains, increase failure rates, and inflate total cost of ownership.
At YISHANG, we’ve supported wholesale buyers in over 50 countries with surface-treated sheet metal parts across a wide range of industries. With over 26 years of manufacturing experience and more than 100,000 parts delivered annually, we understand that surface finishing is not decorative—it’s decisive.
A common case involved an international buyer whose aluminum vending enclosures began rusting less than a month after deployment. The root cause: improper pre-treatment and inadequate powder-coated surface protection. That failure emphasized a critical truth—surface treatment is a functional layer, not an afterthought.
How Surface Treatments Change Performance—From Microns to Markets
Surface treatments manipulate more than just appearance. They determine how a part will perform in real-world conditions. Treatments alter surface roughness, electrochemical reactivity, and mechanical resistance. That’s why engineers and purchasing leads must understand what’s truly happening at the micron level.
Some processes add material. Others chemically transform it. For example, anodizing doesn’t just coat aluminum—it converts the surface into a durable oxide layer. Electropolishing, on the other hand, removes material to enhance smoothness. For a 125 surface finish, electropolishing can reduce micro-peaks and valleys, ensuring a more uniform 63 Ra surface finish or better.
Understanding this balance between material addition and removal—especially in tolerance-sensitive parts—is essential for any sourcing decision involving surface specifications.
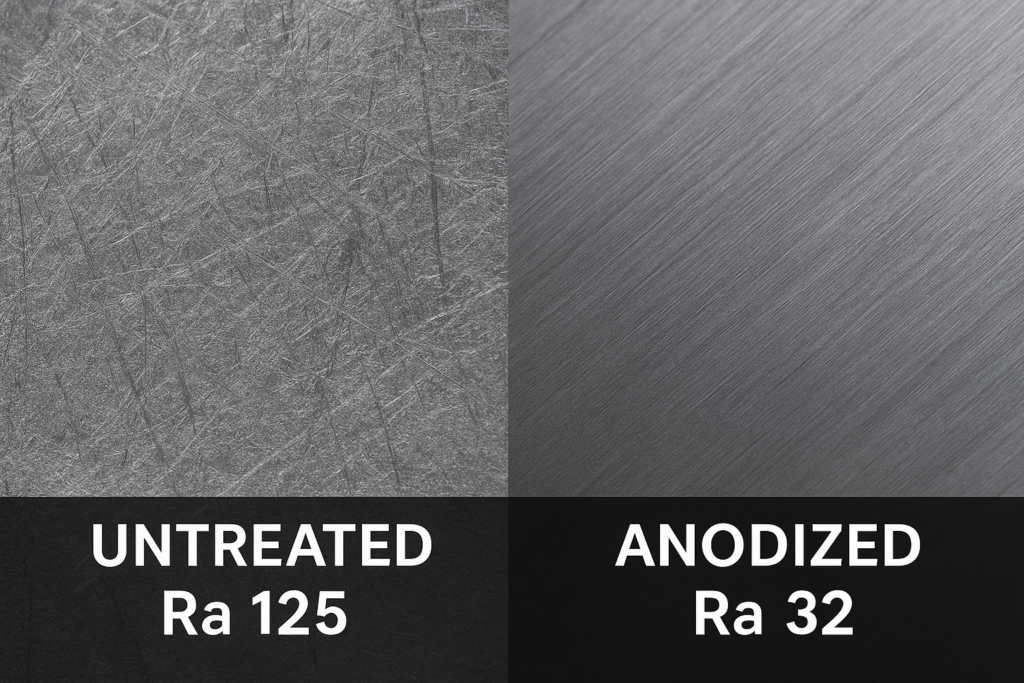
What Each Process Really Does—And Where It Belongs
Anodizing is ideal for aluminum surface finishes. It creates a corrosion-resistant, porous oxide layer that can accept dyes or sealing. It’s suitable for 32 Ra surface finish targets in architectural and electronics enclosures.
Electroplating adds an external metal layer—like zinc or nickel—to boost wear resistance or conductivity. It is common for steel connectors and fasteners requiring a 125 RMS surface finish standard.
Phosphating enhances paint adhesion, typically used before powder coating or e-coating in automotive or appliance housings. It’s a crucial step when targeting Class A surface finish levels where visual appeal and performance converge.
Burnishing and bead blast surface finish techniques improve fatigue resistance and aesthetic smoothness. For example, bead blast surface finish charts often target uniform matte textures around 63–125 Ra, balancing visual appeal with mechanical properties.
PVD and CVD coatings provide ultra-thin, ultra-hard finishes for cutting tools and wear parts—ideal when 8 Ra surface finish is required on high-precision equipment.
Each method serves a distinct purpose, and choosing the wrong one—even if technically feasible—can result in overengineering or performance shortfalls.
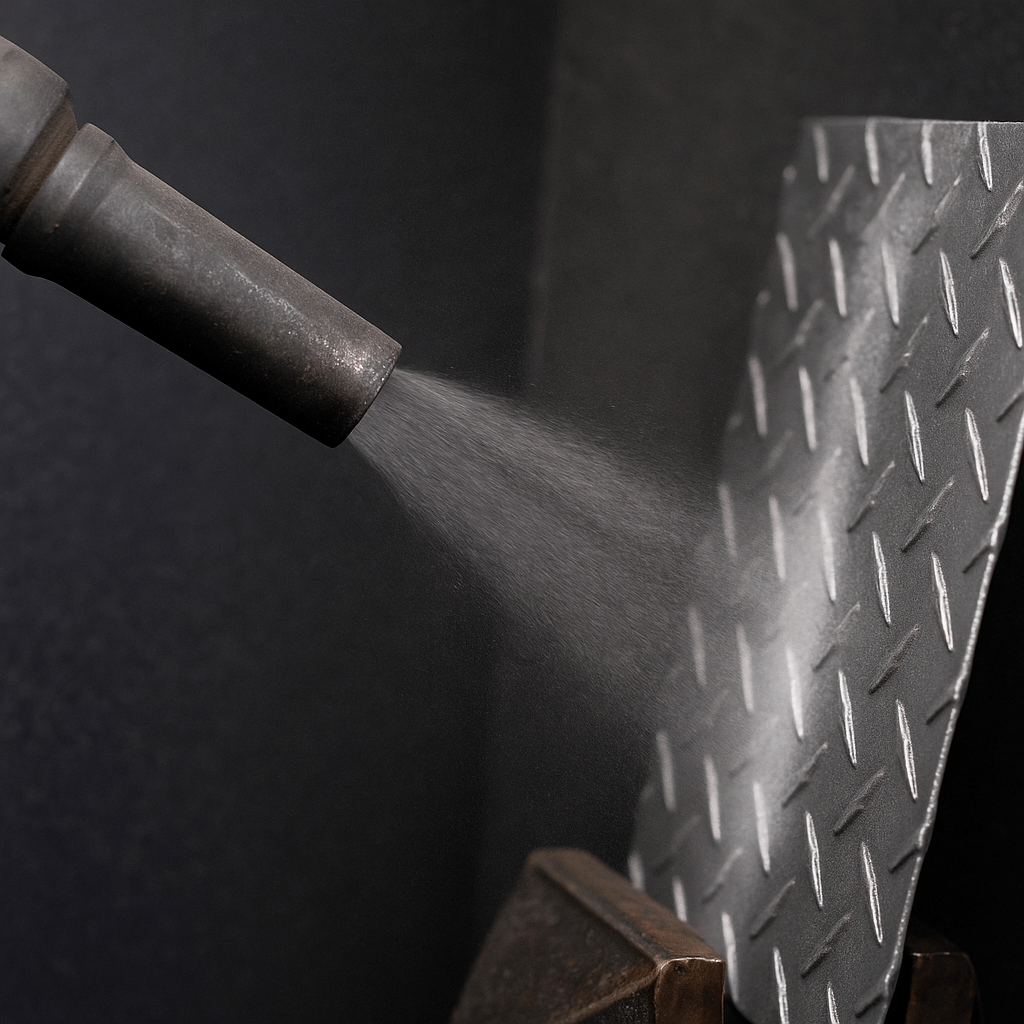
Surface Treatment Selection Isn’t Cosmetic—It’s Commercial
Surface Treatment Method | Typical Applications | Ra / RMS Finish | Relative Cost |
---|---|---|---|
Anodizing | Electronics, medical | 32–125 Ra | $$ |
Powder Coating | Automotive, outdoor | 63–125 Ra | $$ |
Zinc Plating | Fasteners, enclosures | 125 RMS | $ |
Zinc-Nickel Plating | Harsh environments | 125 RMS | $$ |
Electropolishing | Medical, cleanroom | ≤16 Ra | $$$ |
Bead Blasting | Visual/aesthetic use | 63–125 Ra | $$ |
PVD Coating | Cutting tools | ≤8 Ra | $$$$ |
Buyers rarely search “types of surface finishes.” They search for: What will protect my part in this environment? or What’s the lowest cost finish that still meets spec?
That’s why finish selection should start with:
Application environment: Moisture, UV, chemicals, friction?
Material compatibility: Steel? Aluminum? Copper alloy?
Compliance needs: RoHS? ISO? UL?
Expected lifecycle: Is this part disposable or 10-year service?
A 250 surface finish might suffice on a buried chassis. A 16 Ra surface finish may be mandatory in cleanroom conditions. Choosing between powder-coated surfaces and anodized finishes isn’t just technical—it’s strategic. For example, zinc plating typically provides 96-hour salt spray resistance, while zinc-nickel plating extends protection to over 500 hours—making it far more suitable for coastal or humid conditions.
Procurement professionals also consider cost-effectiveness. Over-finishing adds waste; under-finishing adds risk. A calculated surface roughness, such as 3.2 Ra surface finish for functional parts, often balances cost and protection perfectly.
From Design to Delivery: How YISHANG Integrates Surface Processing
Surface finishing isn’t a department—it’s part of the flow. At YISHANG, we integrate treatment planning as early as the CAD stage.
Our in-house process includes:
Design review for tolerance stack-up post-treatment
CNC machining with finish-ready specifications (e.g., 125 Ra targets)
Pretreatment: alkaline cleaning, phosphating, sandblasting
Coating: powder coating, plating, anodizing based on spec
Post-inspection: ISO 9001 quality audits, gloss testing, salt spray (ASTM B117)
Packaging: humidity-controlled, foam-lined crates for finish-sensitive goods
Standard turnaround is 7–15 business days, depending on surface type and complexity. We meet Class A finish expectations with real-world shipping precision.
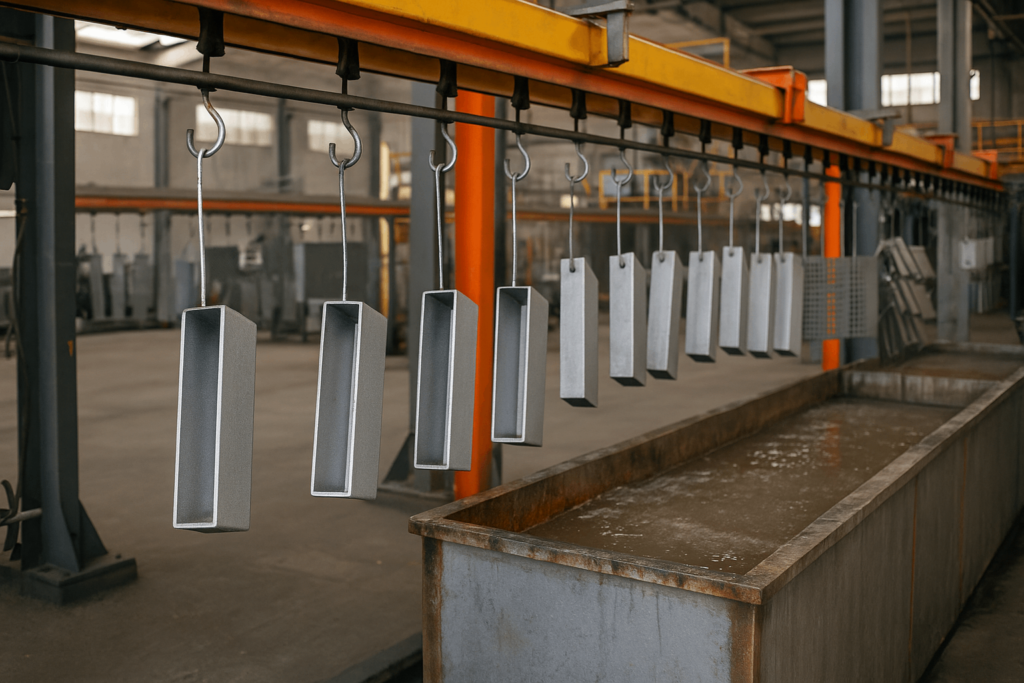
Industry-Specific Solutions: What Buyers Need—Not Just What Works
Automotive Buyers: Seek corrosion resistance + visual uniformity. We supply parts finished with zinc-nickel plating plus sealers, supporting 500+ hour salt spray performance. These finishes typically meet 40 surface finish targets for fastener threads.
Medical Device Procurement: Emphasize bio-compatibility. Our electropolished 316L stainless steel components maintain 16 Ra surface finish in inches, complying with ISO 10993 standards and sterilization protocols.
Energy & Storage OEMs: Need thermal and electrical reliability. We deliver aluminum surface finishes—powder-coated and anodized—that meet EMI shielding specs and 125 RMS surface finish for housing components.
Infrastructure & Outdoor Hardware: Require durability in salt and UV exposure. Our dual-treated powder-coated surface with phosphated base layers ensure >1,000-hour corrosion protection.
Every sector has its own requirements. But every purchase order should ask: what are my end-use risks, and how is the surface finish engineered to reduce them?
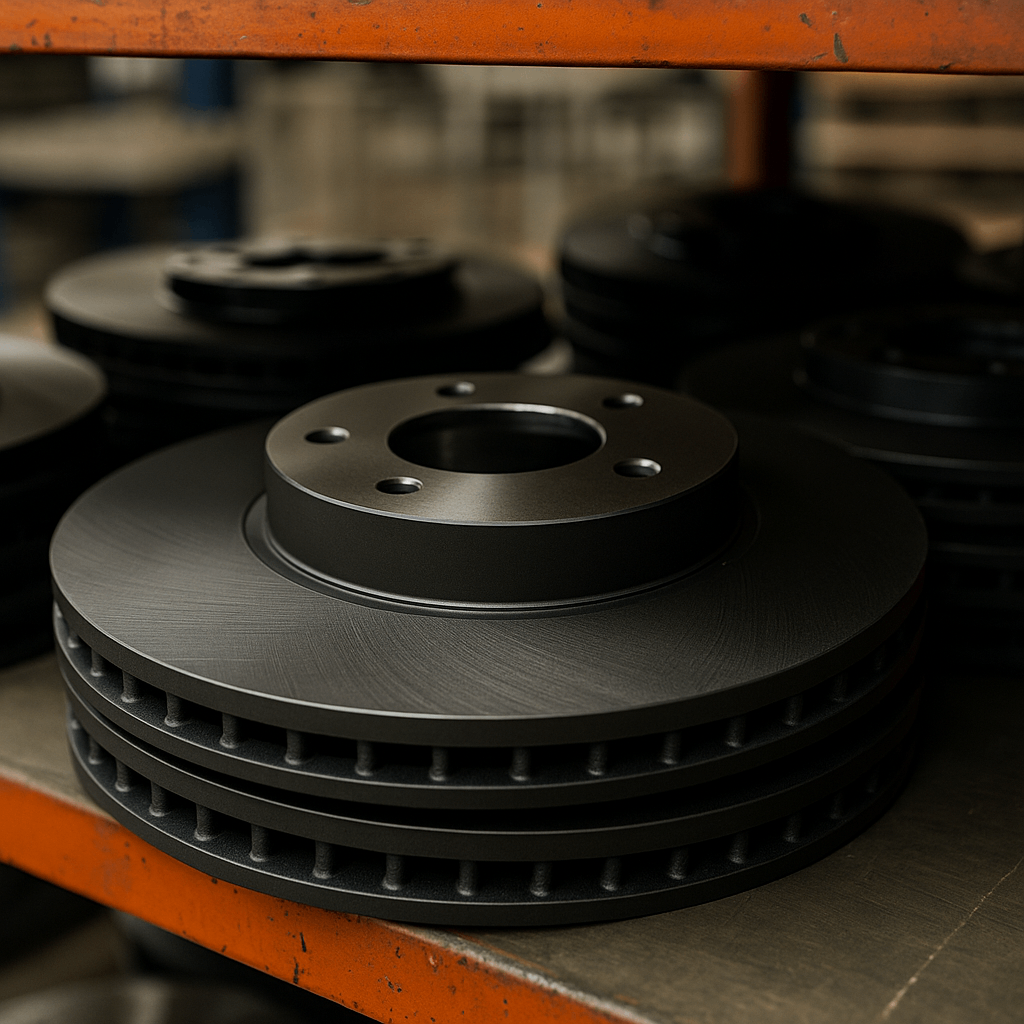
What Can Go Wrong—And How to Catch It Before It Ships
According to recent industry data, surface treatment-related failures account for nearly 20–25% of total product returns in sectors such as automotive and outdoor equipment. Improper adhesion, inconsistent roughness, or coating porosity are among the leading causes.
In North America, most industrial components are expected to meet finish standards between 63–125 Ra for mid-performance and ≤32 Ra for critical sealing or contact interfaces.
Failure doesn’t always appear in production. Sometimes it happens 90 days after installation.
Common surface-related defects include:
Flaking: caused by poor pre-cleaning
Inconsistent gloss or color drift: linked to curing errors
Corrosion beneath coatings: often due to porosity in finish layer
These issues are preventable with standards and process control. YISHANG uses:
Crosshatch adhesion test (ASTM D3359)
Salt spray test (ASTM B117)
Surface profile measurement (including arithmetic mean surface roughness methods)
Our QC team flags deviations before delivery, ensuring fewer returns and better field performance.
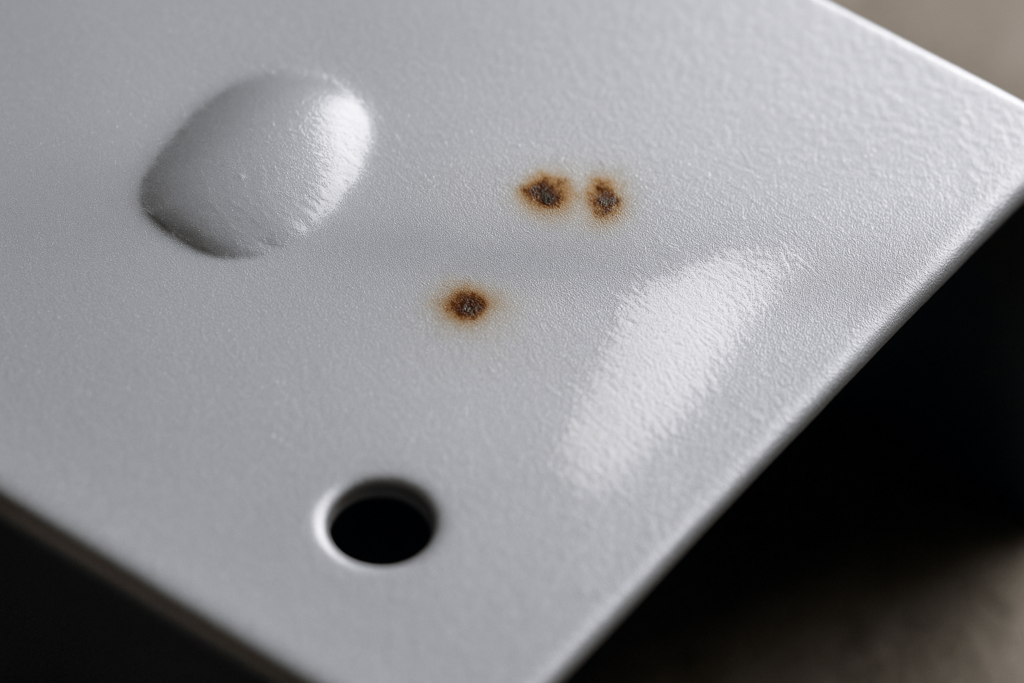
Trends Buyers Should Watch: What’s Real vs. What’s Ready
The shift to low-VOC, water-based, and eco-friendly finishing is real—and irreversible.
Yet, some innovations are not procurement-ready. For example, nano-ceramic coatings with 25z surface finish performance look impressive but remain niche due to high cost and limited durability testing.
Meanwhile, bead blasting and powder-coated surface systems continue to offer scalability, visual appeal, and lifecycle performance at accessible price points.
We advise procurement teams to favor solutions proven by ASTM or ISO standards—and verified through 3.2 Ra surface finish or 63 surface finish benchmarks where necessary.
Asking the Right Questions in Your Next RFQ
Buyers don’t need to be metallurgists. But they do need to ask the right surface questions:
What finish class is required for function or market?
Do we need anodizing, plating, or powder-coated surface?
Are there limits on arithmetic mean surface roughness?
Will these finishes withstand my shipping, handling, and storage environments?
YISHANG isn’t just a factory. We are a surface solution partner. We assist with:
Design-for-manufacturing (DFM) advice on finish strategies
Sample-first processing for new projects
Multi-step inspections (Ra, gloss, thickness)
International logistics and packaging customization
Surface Finish Is the First Line of Performance
Surface finishing is procurement-critical. It affects quality perception, product performance, and total lifecycle cost.
YISHANG supports wholesale buyers with tailored surface solutions—whether you need a 125 RMS surface finish for precision housing, or a 32 Ra aluminum surface finish for an outdoor application.
Let us help you simplify your spec, stabilize your supply chain, and surface smarter.
Ready to discuss your surface finish requirements? Contact YISHANG today.