Metal is Not Just Material—It’s the Soul of Modern Making
In today’s industrial economy, metal is not merely a raw input—it’s the cornerstone of scalable manufacturing. Yet the true value of metal only emerges when it is transformed into precision components that deliver function, reliability, and long-term performance.
This transformation doesn’t happen by chance. It is the result of engineering foresight, smart material choices, digitally controlled processes, and rigorous quality systems. For overseas buyers sourcing custom sheet metal fabrication or OEM parts, understanding how metal is transformed provides key insights into supplier capability, quality consistency, and value creation.
The Hidden Logic of Transformation: What It Really Means to 'Transform Metal'
For international buyers, especially those procuring on contract terms, “metal transformation” isn’t just a technical term—it’s a promise of process stability, specification accuracy, and production repeatability.
Modern fabrication views each metal sheet as a programmable input. From CAD design to shipment-ready component, the transformation process incorporates every critical stage—cutting, forming, joining, surface treating, and packaging. In practice, this means more than forming shapes; it’s about optimizing for load-bearing requirements, fitment precision, thermal resistance, and material integrity.
For OEM projects, where parts are expected to perform under extreme or long-term use, transformation must produce components with repeatable outcomes across thousands of cycles. This requires a workflow that blends precision engineering with scalable execution.
Transformation Begins Before the First Cut: How Material Choices Shape the Entire Process
The success of any project begins with choosing the right base material. B2B buyers often seek components that are corrosion-resistant, structurally reliable, and economically feasible. Stainless steel (304 or 316), aluminum, copper, and galvanized steel each offer trade-offs in formability, welding response, and environmental compatibility.
At YISHANG, we frequently work with clients to evaluate trade-offs between 304 and 316 stainless steel. While 316 offers higher corrosion resistance (especially in marine or medical environments), 304 may be preferable for less harsh settings with tighter budgets. These early discussions help ensure the selected material is compatible with project goals and compliance standards such as RoHS.
Procurement professionals are increasingly focused on lifecycle cost and traceability. That’s why we document all alloy grades, batch origins, and processing specs. This transparency aids regulatory clearance and strengthens the reliability of supply chains.
The Real Transformation Happens Here: Inside the Process Core
Once materials are sourced, the actual transformation begins—with CNC-driven processes designed for precision and speed. Sheet metal fabrication often starts with laser cutting or turret punching. At YISHANG, our Trumpf fiber lasers cut with ±0.1 mm tolerance and optimal kerf width to support downstream accuracy.
Subsequent bending, deep drawing, and pressing operations require compensation for springback, an inherent behavior of metals. Our engineers simulate toolpaths and form angles in advance to ensure conformance to design specs. This helps avoid costly delays or assembly misalignment.
In welding, we apply TIG and MIG methods tailored to material thickness and joint profile. Each joint is calibrated for strength-to-weight ratio and is inspected to prevent HAZ-related defects. For high-visibility parts, surface quality is prioritized using automated polishing or powder coating.
Surface finishing doesn’t only impact corrosion resistance—it shapes first impressions. A powder-coated bracket may not only last longer but present a cleaner aesthetic, especially in visible consumer-facing applications. For example, YISHANG helped a North American pet appliance wholesaler design and deliver 30,000 powder-coated support frames with uniform sheen and precise branding alignment for retail display.
Here’s a sample reference chart illustrating transformation steps:
Process Step | Equipment Used | Tolerance | Standard |
---|---|---|---|
Laser Cutting | Trumpf 3030 Fiber Laser | ±0.1 mm | ISO 2768-m |
Bending | Amada Press Brake | ±0.2 mm | ISO 2768-m |
Welding | Panasonic TIG/MIG Welders | N/A | AWS D1.1 |
Surface Finishing | Gema Powder Coater | N/A | ISO 12944 |
This precision workflow ensures that even in large batch runs, each part retains conformity and meets application needs.
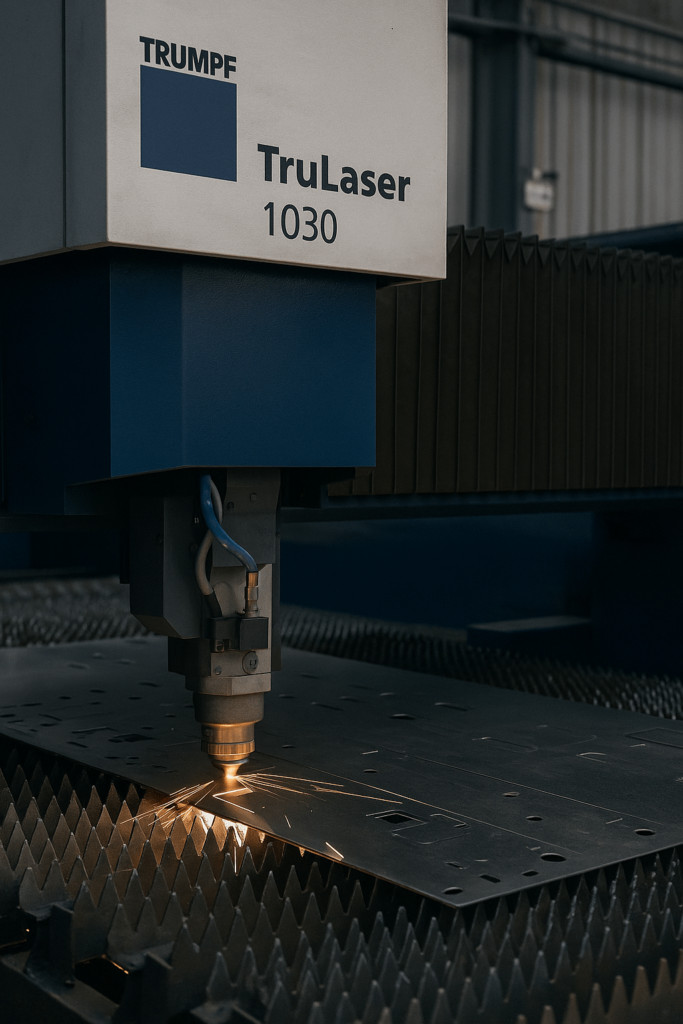
Precision Is Not Optional: The Science Behind Tight Tolerances
Precision is not a luxury—it’s an operational baseline. For industries like automotive, aerospace, and medical devices, parts must conform to tight geometric tolerances. Deviations can result in fitment failure, performance drops, or system-wide malfunctions.
YISHANG employs high-accuracy CMMs and 3D laser scanners to verify profiles, angles, and concentricity in real-time. Our QA process follows ISO 9001 protocols and includes dimensional reports, batch records, and visual inspections.
Tooling wear, machine vibration, and environmental factors are accounted for during production simulation. In fact, we benchmark tool drift to ensure die performance over extended runs. These controls directly benefit B2B buyers by minimizing the risk of non-conformity and reducing hidden rejection costs.
Where Sustainability Intersects with Precision
Eco-conscious production isn’t just a regulatory checkbox—it impacts your long-term product viability. At YISHANG, we’ve engineered our workflows to achieve both environmental compliance and cost efficiency.
We use energy-efficient CNC platforms that reduce per-unit power consumption by up to 25%, supported by nesting software that maximizes raw material yield. Closed-loop water filtration in finishing lines ensures compliance with ISO 14001 and helps reduce chemical discharge.
More importantly for buyers, sustainable practices often translate to leaner, more predictable supply chains. Recyclable scrap, digital batch tracking, and optimized packing formats mean your order leaves fewer variables to chance.
True Transformation at Scale: From Small Batches to Global OEM Supply
International buyers often need both flexibility and volume capacity. Whether you’re sourcing 100 control panel enclosures or 20,000 EV brackets, the requirement is the same: accuracy at scale.
At YISHANG, we support a variety of order types—pilot runs, small-series fabrication, and long-term OEM contracts. We offer lot control, serialization, and customized packaging that aligns with assembly-line compatibility.
Our standard lead time for repeat orders averages 12–18 working days, and export packaging is tailored to reduce customs delays and minimize freight damage. This ensures your parts arrive ready for immediate assembly.
Our global clients include vendors in electronics, clean energy, medical devices, and industrial automation. Because every project carries different logistical and compliance demands, we adapt our process routing to suit those conditions, offering real-time production updates and post-delivery traceability.
The Future Isn’t 3D Printing—It’s Real-time Adaptation
While metal additive manufacturing has its place, the future of sheet metal fabrication lies in agile systems that adapt in real time. This isn’t theoretical—we’re already integrating AI-assisted controls, digital twins, and predictive analytics into our daily workflows.
For instance, our brake presses adjust bend angles automatically based on in-process sensor feedback. Welding torch paths adapt dynamically to mitigate bead inconsistency. And digital twin systems allow customers to validate their geometry before the first cut is made.
Why does this matter to procurement? Because it means faster iterations, fewer defects, and better alignment with your go-to-market timelines. Precision is no longer just technical—it’s strategic.
What Makes a Metal Truly Transformed?
Metal is truly transformed when it meets functional expectations—mechanically, visually, and economically. The shape is just the surface. Beneath it lies process discipline, material science, and supplier accountability.
YISHANG brings 26+ years of experience, ISO-backed processes, and RoHS-compliant infrastructure to every project. We’ve helped hundreds of OEM buyers scale from concept to high-volume production while controlling cost, quality, and lead time.