Why Shearing Still Matters in High-Volume Sheet Metal Supply
While modern cutting technologies like laser and plasma receive more attention, sheet metal shearing remains a preferred solution for bulk production. Especially for international buyers sourcing thousands of repeatable parts, it delivers a combination of speed, efficiency, and low per-unit cost that is hard to match.
YISHANG uses shearing to fulfill frequent orders for telecom panels, vending housings, and storage systems—industries that rely on consistent cut quality and short turnaround. Compared to thermal methods, shearing is cleaner, faster, and more material-efficient. These advantages are tangible in cost control and delivery timelines.
In today’s sourcing landscape, buyers need more than just a fabrication vendor—they need production partners who can scale. This is where precision shearing continues to offer practical value for bulk metal fabrication services.
Shearing: How the Process Works and Why It’s Reliable
How Cold Shearing Protects Material Integrity
Shearing involves pressing a sheet between two blades—one fixed, one moving—along a defined linear path. There’s no heat involved, which keeps coatings intact and avoids microstructural distortion. This “cold cut” is ideal for aluminum, copper, galvanized steel, and especially 304 stainless.
Why Precision Matters in Bulk Cutting
The process is governed by tight mechanical tolerances and known shear strength parameters. For instance, 304 stainless shear strength averages around 450 MPa. Machines calibrated for such data deliver predictable results in large batches.
Procurement teams working with coated or thermally sensitive materials often prefer shearing because it simplifies downstream finishing. Edge quality is consistent, and part geometry is stable. When you’re sourcing CNC shearing services for aluminum 5052 or 304 SS, this level of control matters.
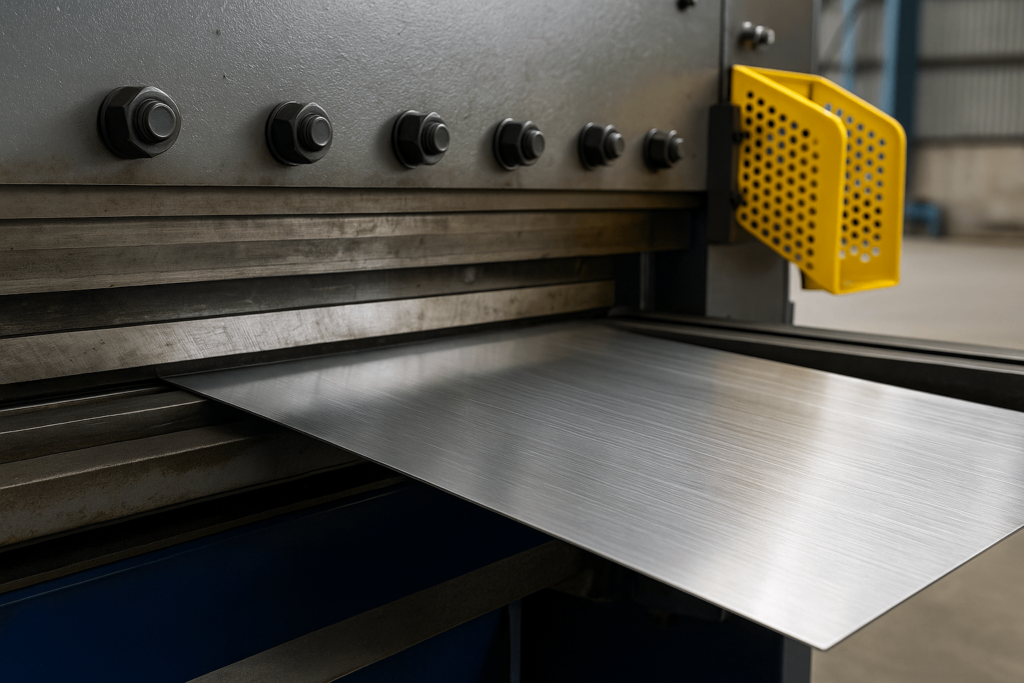
Getting Technical: Force and Clearance in Real Orders
Successful shearing begins with understanding shear strength and force equations. A standard formula is: Force = Length × Thickness × Material Shear Strength
For a 500mm panel of 2mm 304 SS: Force = 500 × 2 × 450 = 450,000 N (450 kN)
The optimal clearance between blades is typically 5–10% of thickness. So for 2mm sheet, that’s 0.1 to 0.2mm. Proper clearance avoids burrs, deformation, and excess wear. CNC machines at YISHANG auto-adjust this to match batch material specs.
These technical settings aren’t just engineering trivia—they ensure that the 10,000th piece in a PO matches the first, reducing waste and post-processing in any bulk sheet metal cutting service.
When Shearing Is the Smartest Choice for Buyers
Shearing makes the most sense when parts are rectangular or involve straight-edge forms. Examples include display backplates, inverter covers, equipment mounts, and structural stiffeners.
Procurement teams should consider shearing when:
Orders exceed 500+ units
Part edges don’t require complex curvature
Time-to-market is critical
Surface treatment (e.g., powder coat) must remain undisturbed
If you’re sourcing for vending machine frame cutting or solar enclosure prep, shearing offers the fastest path from order to delivery.
Equipment Insight: Understanding the Shearing Line
YISHANG uses three types of shears:
Mechanical Shears for carbon steel and repetitive cuts
Hydraulic Shears for variable thickness and stable hold-down
CNC Shears with programmable back gauges and blade gap control
Understanding your supplier’s machinery helps buyers validate production capacity and quality control potential. Blade sharpness and gap calibration are regularly monitored, and digital logs ensure consistency across shift changes.
Buyers can ask for data such as:
Daily output capacity per shear
Last maintenance or blade change cycle
Accuracy logs from the last batch
Quality Assurance: Preventing Tolerances and Deformation
Common Shearing Defects and Causes
Every buyer’s concern is part accuracy. Shearing can sometimes produce:
Burrs from poor blade maintenance
Twist in narrow parts
Camber from off-center hold-downs
YISHANG’s Inspection and Control System
YISHANG maintains tolerances typically within ±0.2mm on mild steel and ±0.3mm on stainless or aluminum. For high-volume precision shearing, this level of tolerance supports reliable assembly downstream.
Defect | Likely Cause | Control Strategy |
---|---|---|
Burr | Excess clearance | Auto-adjusted CNC clearance |
Bow | Uneven pressure | Calibrated hold-down systems |
Camber | Dull blade edge | Regular sharpening, digital alert |
Our team performs real-time inspections with laser back-gauges and samples every 50–100 units, based on ISO 9001 protocols.
Different Metals, Different Results
Material Behavior During Shearing
Material response matters. A supplier’s ability to control results across alloys speaks to their capability.
304 SS shear strength is high, needing precise force and clearance.
Aluminum 6061 shears easily but can roll on edges without blade polish.
Copper and Brass are ductile; good support prevents ripple and twist.
Galvanized steel creates more friction, so blades must be harder.
How YISHANG Calibrates for Each Alloy
YISHANG adjusts shearing profiles per job spec,, ensuring each batch remains within tolerance and edge integrity expectations. We also handle custom sheared aluminum parts with edge burr control and uniform finish.
Maintenance: The Hidden Factor in Consistent Output
Blades wear faster than most buyers realize. If you’re sourcing thousands of parts, maintenance practices matter.
Our SOP requires blade inspection every 6,000 strokes for stainless and every 10,000 for mild steel. Logs are kept digitally and linked to job IDs for traceability.
A well-maintained shearing line avoids drift in tolerance and surface scarring—two issues that drive up rejection rates. Buyers should ask suppliers how they control for these over time.
Shearing in Smart Factories: What Buyers Should Look For
More suppliers now integrate shearing with robotic loaders, part sorters, or MES systems. YISHANG uses programmable lines that combine shearing with punching or bending.
This means:
Lower cycle times
Minimal part mix-ups
Automated quality checkpoints
It’s not just about the machine—it’s about how it’s embedded in the workflow. Buyers prioritizing accuracy and throughput should check for full-line integration, not standalone tools.
Comparing Processes: Why Shearing Still Wins for Simplicity
Method | Ideal Use | Speed | Cost | Finish | Complexity |
Shearing | Flat shapes, high volume | High | Low | Good | Low |
Laser | Custom or prototyping | Low | High | Best | Very High |
Punching | Forming + holes | Medium | Medium | Medium | Medium |
Blanking | Mass production blanks | High | Medium | Good | Low |
For 90% of YISHANG’s bulk orders, shearing is either the primary or prep process. Laser is often reserved for small-batch, complex work or where post-processing time is less of an issue.
The Sustainable and Economic Edge
Shearing reduces energy consumption versus laser/plasma—up to 70% by some industrial studies. It also avoids gas emissions and reduces filtering or cooling equipment.
Material loss is minimal. Uniform offcuts can be recycled efficiently. These efficiencies support both green goals and cost savings, especially for long-term supply contracts. As a bulk sheet metal cutting supplier, YISHANG focuses on minimizing waste and maximizing yield.
Where Shearing Creates Real Buyer Impact
A European EV cabinet buyer reduced cost-per-unit by 12% after switching from laser to CNC shearing for rear panels. Another North American vending OEM eliminated one QC step by sourcing pre-sheared parts from YISHANG.
These shifts improved cash flow, reduced rework, and shortened project timelines—key outcomes for buyers managing scale and deadlines.
What to Ask When Sourcing Sheared Parts
If you’re comparing fabrication suppliers, focus not only on price per part but:
How is clearance managed across different metals?
What’s the supplier’s max daily shear capacity?
Can they provide a tolerance report by batch?
YISHANG supports OEM procurement teams with consistent sheet metal output at scale, backed by RoHS and ISO 9001 standards.
Let us know if you’d like a sample or want to review a past-case comparison. We’re here to support your decision-making, not push a product.