Pipe Fittings: Invisible but Indispensable
In engineered piping systems, fittings are more than connectors—they are reliability points. For industrial buyers managing large-scale procurement, every fitting represents a decision that impacts system uptime, maintenance cycles, and compliance with regional or industry-specific codes.
Procurement teams sourcing fittings across sectors like HVAC, water treatment, energy, or food processing must evaluate more than just cost. Material type, pressure class, thread compatibility, and fabrication precision determine long-term performance. Choosing the right fitting reduces lifecycle costs, especially for projects involving laser cut tube sections or custom-bent stainless tubing.
This guide offers a practical framework for selecting pipe fittings based on function, material, and real-world applications. Whether you’re sourcing for bulk distribution or OEM system assembly, it outlines what matters—and why.
What Procurement Professionals Need to Know First
Pipe Fitting Tolerances for OEM Use
Precision matters. In OEM assembly or system integration, even minor dimensional deviations in fittings can cause cascading alignment issues or leak points. Buyers often ask for tolerances down to ±0.1mm, especially in systems involving laser tube cutting or bent stainless tubing.
Working with a supplier who offers GD&T documentation and machine-calibrated measuring on fittings ensures batch-level consistency, reduces time spent on adjustments during installation, and improves final system uptime.
Consider Operating Pressures and Temperatures
Different fittings perform differently under pressure. While a stainless steel elbow may suffice for standard systems, high-pressure pipelines often require forged alloy components verified against ASME B16.9. Material fatigue becomes a key issue in steam systems and laser pipe cutting assemblies.
Temperature also influences material selection. PVC, for example, softens under moderate heat, while aluminium extrusion tube offers high thermal conductivity but limited pressure resistance. Thermal expansion must be considered when combining metal materials like in bent stainless tubing lines.
Material Compatibility Isn’t Optional
Procurement teams must review both the fluid’s properties and the pipe material. Using copper on stainless steel, or combining dissimilar metals, often accelerates corrosion. This is especially risky in long-term tube laser cut assemblies where precision and longevity are critical.
Whether sourcing 3in stainless steel pipe components or specifying laser cut tube ends for automated installations, consistent material compatibility protects procurement ROI and reduces return rates.
Threading, Welding, or Flanging: Joint Types Matter
Threaded fittings are preferred for field-level installation or mobile setups. But they often loosen over time due to vibration or heat. Flanged joints offer high-pressure resistance and easier access for inspection. Welded fittings are optimal for cleanrooms and food-grade applications, such as bending stainless steel tubing into continuous runs with no leak points.
Matching fittings to connection methods saves rework costs and shortens installation timelines—key concerns in global sourcing.
DIN vs ASME Pipe Fitting Compatibility
Export buyers frequently face compatibility issues when integrating DIN-standard parts into ASME-compliant builds. The bolt-hole patterns, flange thicknesses, and pressure ratings differ subtly yet significantly.
Clarifying these details at the sourcing stage avoids rework and enhances interconnectivity across global installations.
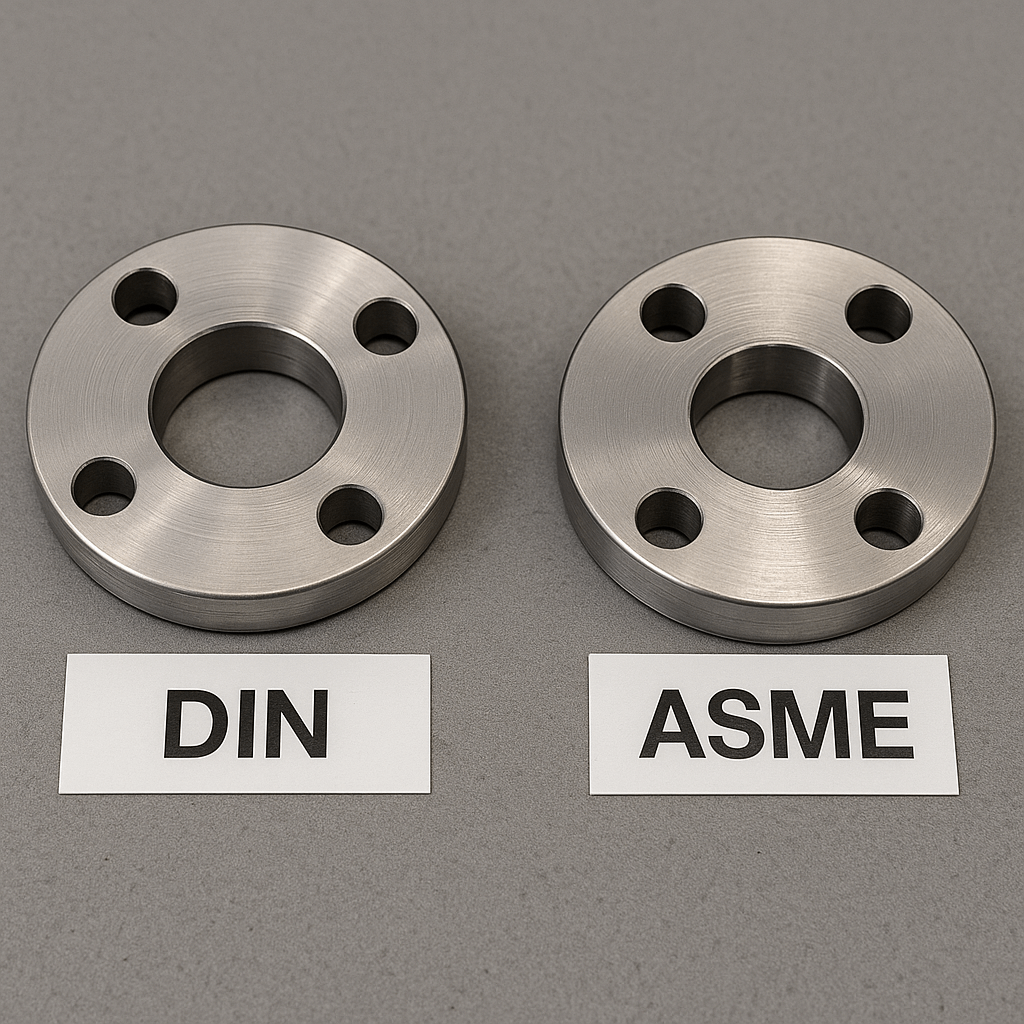
Always Align to Standards
DIN, JIS, and ASME standards do not align by default. Metric-to-imperial mismatches remain a leading cause of failed assemblies in export projects. Sourcing only DIN-compliant flanges for a North American build can lead to downtime, especially in fast-paced industries using tube laser services for modular designs.
Working with manufacturers that clearly label and test fittings to standard helps ensure delivery compatibility.
For high-volume RFQs, many buyers also inquire about ISO 9001 lot tracking, pallet labeling, and bulk packaging specifications. Clarifying these upstream helps prevent shipment delays.
Real Buyer Case Example
A European OEM building portable water treatment systems sourced 15,000 units of SS304 elbows from YISHANG. Their concern wasn’t just price—it was repeatability across batches and flange-hole consistency to match their automation templates.
We standardized the batch with lot-level traceability to ensure dimensional repeatability and weld alignment during assembly.
This showcases YISHANG‘s strength as a bulk stainless pipe fitting exporter in China, capable of delivering OEM-grade consistency across large orders. By leveraging precision laser tube cutting on all pre-weld components, the buyer reduced assembly time by 18% and reported a 0.01% rejection rate over two years.
Looking to streamline your fitting specification or confirm batch traceability in advance? Let YISHANG’s engineering team support your next RFQ with actionable insights and full-process documentation.