Mercury Isn’t Just a Heavy Liquid — It’s a Design Constraint
Mercury’s exceptional density—13.534 g/cm³ at 20°C—makes it a crucial factor in industrial design, impacting structural integrity, packaging, and calibration. This property directly influences the performance, safety, and regulatory handling of components in industries from sensors to energy systems.
At YISHANG, we’ve seen that mercury’s high density is a recurring topic in RFQs involving sealed instruments, mercury-filled components, fluid flow systems, and precision devices. For OEM design teams and global wholesalers sourcing engineered parts or custom enclosures, knowing how this property affects fabrication and functionality can prevent rework, downtime, and customer returns.
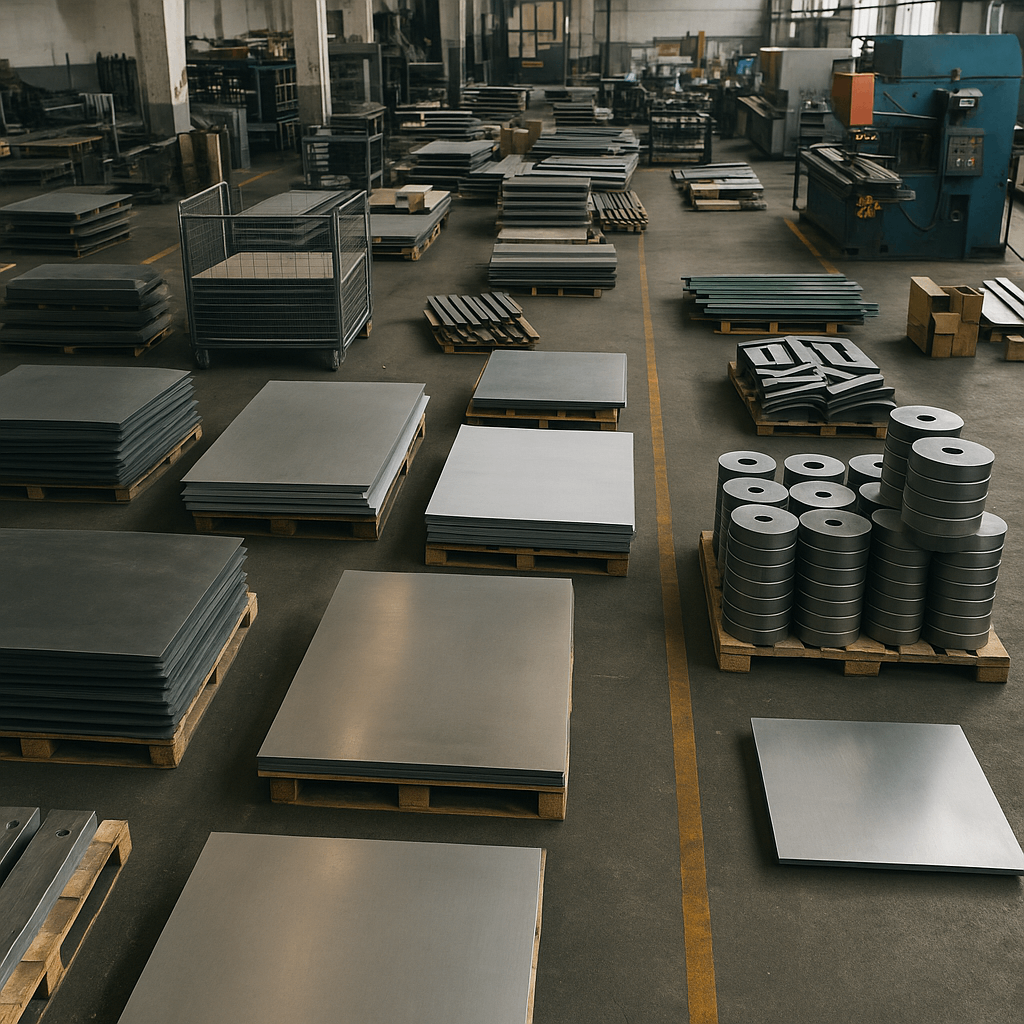
The Hidden Weight: What Mercury's Density Really Means in Industrial Use
To the technical buyer, mercury’s density isn’t trivia—it’s a constraint. It means more mass per unit volume, which translates into higher internal pressures, heavier transport weight, and the need for structural reinforcement. Compared to water (1 g/cm³) or even lead (11.34 g/cm³), mercury is exceptionally dense, with direct implications for enclosure strength and thermal balance.
This property enables the miniaturization of pressure-based devices like barometers, thermostats, and fluid regulators. For industrial procurement, this means less material for more functionality—but only when the design accounts for the associated force load. Knowing what the density of mercury is and what it implies allows teams to select more appropriate metals or define safety tolerances when mercury is involved.
Comparative Density Table
Material | Density (g/cm³) | State at Room Temp |
---|---|---|
Water | 1.00 | Liquid |
Ethanol | 0.79 | Liquid |
Lead | 11.34 | Solid |
Mercury | 13.534 | Liquid |
Gold | 19.32 | Solid |
This liquid metal density comparison illustrates why mercury is often preferred where compactness and precision matter most.
Measuring Mercury Density in Industrial Settings
Lab-Based Measurement Techniques
Most procurement specialists don’t need to measure mercury themselves, but they need to trust that a vendor knows how to do it right. Density is typically measured using a pycnometer or hydrostatic weighing method—accurate, but limited to lab environments. These methods help ensure that mercury content aligns with its declared purity, which directly affects performance and compliance.
Inline Density Monitoring Systems
For continuous or automated applications, manufacturers use oscillating U-tube densitometers. These allow for real-time density checks during production, improving consistency and traceability. That’s why at YISHANG, when sourcing or processing components involving high-density metals or engineering fluids, we rely on precise measurement to validate upstream materials before welding, forming, or enclosure sealing.
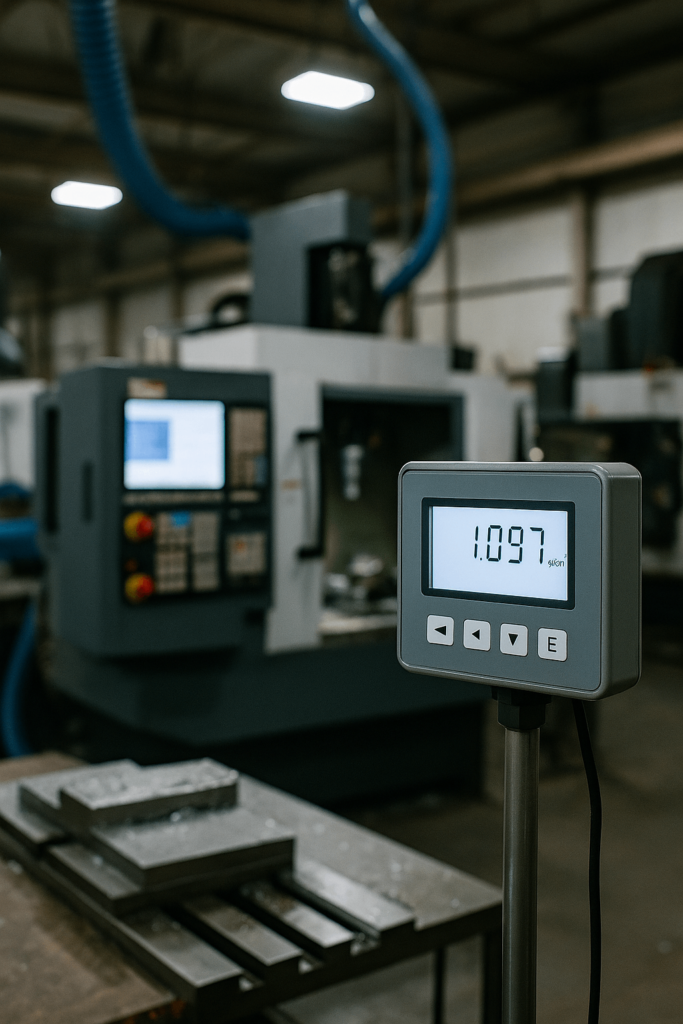
Variables You Can’t Ignore: What Changes Mercury’s Density
Temperature Variations
Industrial buyers often ask why a mercury-based component might fail calibration over time. One overlooked factor is how its density varies under different operating conditions. Three key variables affect the stability of mercury’s density: temperature, pressure, and purity.
Temperature affects expansion. At 100°C, mercury’s density drops to around 13.29 g/cm³. For equipment exposed to heat cycles, this can lead to minor inaccuracies—especially in enclosed volumes or high-resolution instruments.
Pressure Effects
Pressure, although having minimal impact in moderate conditions, can influence behavior in vacuum-sealed environments or at great depths. Buyers procuring for oil and gas, marine, or aerospace applications must confirm density reliability across pressure ranges.
Purity and Contamination
Impurities such as oxides or residual processing agents alter fluid properties and may affect sensor calibration or device longevity. We recommend sourcing mercury compliant with ASTM D287 and ISO 4788 to avoid quality deviations during acceptance testing or third-party audits. Understanding these density tolerances in engineering fluids is crucial to ensuring consistent product behavior.
High Density in Procurement: Load, Safety, and Compliance
shipping cost, design load, and installation safety. Components involving mercury need sealed enclosures, shock-absorbing mounts, and often double-wall containment.
We’ve supported buyers who underestimated the structural load of mercury-instrument housing in battery modules or HVAC sensors. The result: cracked seals, thermal fatigue, or shifting calibration. That’s why buyers should validate the material specs of their suppliers and request load simulations if mercury is involved. In many cases, metal fabrication for high-density fluids demands reinforced structures and advanced weld integrity.
Mercury-handling devices must meet EPA, REACH, and OSHA requirements. Failure to comply can delay customs clearance or trigger penalties. If you’re sourcing across borders, confirm your vendor uses proper sealed containers for mercury transport and leak-prevention design.
Case Study: When Density Was Overlooked
In one case, a European client ordering pressure-level transmitters for an underground pump system requested a redesign after their initial housing failed pre-installation drop testing. The issue stemmed from not accounting for the density-driven inertia of mercury during transport. YISHANG’s engineering team helped redesign the mounting bracket and used reinforced steel alloys to solve the issue in the final batch.
Worth noting: Even a 0.2 g/cm³ deviation in expected mercury density can shift flow rate readings or cause devices to drift out of calibration range, leading to product returns or system misfires.
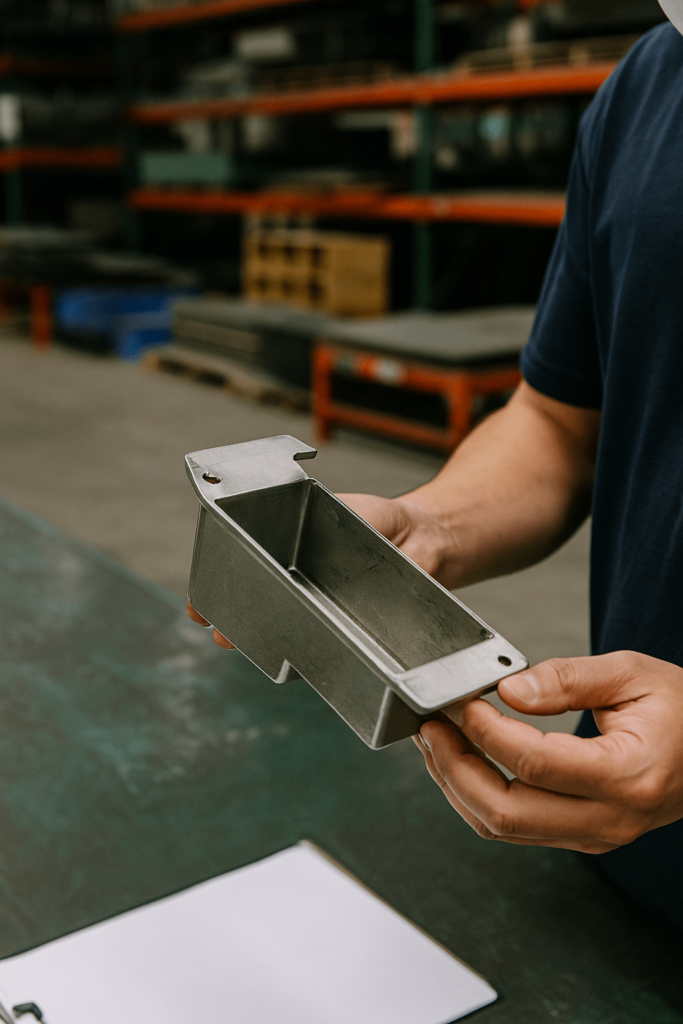
Why Mercury is Still Used in Some Industrial Applications
Performance Under Pressure and Heat
Despite regulatory pressure, mercury remains unmatched in specific, performance-critical applications. In pressure measurement devices, no alternative fluid offers the same combination of high density, thermal stability, and minimal vapor pressure. This allows for more compact designs and consistent accuracy in environments where reliability is non-negotiable.
In high-temperature tilt-sensing systems, mercury’s conductivity ensures consistent readings with minimal recalibration. These properties are particularly valued in scientific-grade and industrial-grade sensors still in operation. Understanding these practical considerations helps procurement teams balance innovation with reliability.
Legacy System Compatibility
Many OEM buyers still support equipment installed decades ago, where mercury-based sensors or relays remain standard. In these cases, sourcing components with equivalent density and form factor becomes critical. Mercury allows continued support without redesigning the entire system, reducing both risk and cost. For procurement teams, understanding legacy compatibility isn’t about resisting innovation—it’s about sustaining performance and uptime.
How Density Data Informs Strategic Procurement
Quality Assurance and Material Selection
When you’re evaluating suppliers or materials, density is more than a technical detail—it’s an indicator of production quality, traceability, and compliance. For buyers involved in RFQs or sourcing custom components, asking about density verification shows technical diligence.
If you specify tolerance levels for mercury-based devices, you reduce the risk of downstream failure or return disputes. Most responsible vendors should be able to show alignment with NIST traceability, offer pre-shipment inspection reports, or simulate how density changes under operating conditions.
Evaluating Alternatives and Lifecycle Trade-offs
Even when considering substitutes like Galinstan or dense silicone fluids, understanding these trade-offs enables smarter lifecycle decisions—not just up-front savings. Whether you’re issuing an RFQ specification for mercury devices or evaluating OEM mercury component sourcing, accurate density data enhances procurement efficiency and product reliability.
Frequently Asked Questions (FAQ)
Here are common questions technical buyers and engineers ask when sourcing mercury-related components:
Q1: What is the density of mercury and why does it matter in industrial applications?
Mercury’s density is 13.534 g/cm³ at 20°C. This affects component size, structural load, and calibration accuracy in instruments and sensors.
Q2: Can changes in mercury density cause system failure?
Yes. Even small deviations can disrupt flow readings or pressure calibration, especially in sealed or thermally dynamic systems.
Q3: What standards should mercury-related components comply with?
ASTM D287, ISO 4788, REACH, EPA, and OSHA depending on application and region.
Q4: Is mercury still used despite environmental regulations?
Yes, in niche but critical applications such as legacy tilt sensors, barometric devices, and high-temperature control systems.
Q5: What alternatives exist to mercury, and are they effective?
Options include Galinstan and silicone-based fluids, but trade-offs exist in density, thermal behavior, and compatibility.
Precision Starts With the Right Questions
If your business involves sourcing sensors, metal enclosures, or temperature-sensitive control modules, understanding mercury’s density allows buyers to specify components that perform reliably under real-world loads and conditions.
YISHANG supports buyers in energy storage, instrumentation, and automation with custom fabrication where performance and compliance go hand-in-hand. Whether you need density validation, part redesign, or sourcing advice—we’re ready to help.
Send us your specs—we’ll help you optimize performance without compromising compliance.