Why Hydroforming Is Back in the Spotlight
For international wholesale buyers, sourcing metal components isn’t just about price—it’s about part reliability, consistent quality, and reducing procurement risk. As global demand grows for lightweight, high-strength metal solutions across EVs, HVAC, and infrastructure, hydroforming is seeing renewed relevance.
Hydroforming helps reduce SKU complexity by consolidating parts and minimizing welding. This supports leaner inventory and reduces defects—ideal for scalable programs. Unlike press brake forming or standard bending forming, it uses hydraulic pressure to shape metal precisely and repeatably, with better thickness distribution and surface finish.
Buyers aiming to reduce downstream variability are increasingly shifting to this method.
Understanding the Process Without Getting Lost in Jargon
To assess a hydroforming supplier like YISHANG, it’s key to understand its two main categories: tube and sheet hydroforming.
Tube Hydroforming
A metal tube is inserted into a form and expanded by internal fluid pressure. Ideal for chassis beams, HVAC conduits, and energy system frames, this method enables uniform expansion for variable cross-sections.
Sheet Hydroforming
A flat sheet is shaped using a diaphragm and fluid pressure. It’s well-suited for forming steel sheet or lightweight casings where precision and surface finish matter, such as appliance housings and aerospace skins.
Hydroforming often outperforms aluminum molding or casting molding processes by reducing welds, minimizing thinning, and eliminating secondary finishing. Material and geometry decisions should be made early, as they directly affect cost and tool feasibility (explored in Section 5).
Design-Driven Forming: Procurement Value Through Engineering Flexibility
For B2B buyers, hydroforming isn’t just a forming option—it’s a way to simplify supplier networks and reduce part variation.
It enables integrated features like flanges, bosses, or channels in one shot, reducing QA checkpoints and improving consistency. This streamlines production and enhances long-term reliability.
Compared to aluminum injection molding or cast molding process paths, hydroforming delivers seamless structural geometry with lower fatigue failure risk—especially important in multi-part assemblies.
The Real Constraints Procurement Teams Need to Understand
Hydroforming requires careful feasibility evaluation. Materials like 304/316 stainless steel, red brass, and aluminum base molding grades are excellent candidates. Low-ductility metals may instead require CNC EDM machining or cast forming.
Designs with tight corners or flat areas are more prone to splitting, much like failure risks in cavity molding or arbor milling. Hydroforming thrives when parts have flowing curves and consistent wall sections.
The process becomes cost-effective above ~300–500 units per batch. For lower volumes, advanced prototype molding or china rapid prototyping can validate formability before committing to full tooling. Sample lead times are typically 7–10 business days, and aluminum or steel dies are ready in 4–6 weeks.
Cost Breakdown: How Hydroforming Influences Your Total Cost of Ownership
Hydroforming carries an initial tooling investment, but offers savings in secondary steps, QA, and logistics.
Cost Category | Traditional Forming | Hydroforming |
---|---|---|
Tooling Investment | Low to Medium | Medium to High |
Post-Processing Steps | High (grinding, welding) | Minimal |
Tolerances | Moderate (±0.5–1.0 mm) | Tight (±0.2 mm typical) |
Assembly Complexity | High | Low (fewer welds/parts) |
Long-Term Stability | Variable | High |
YISHANG clients have reduced rework rates by 20%+ through form accuracy and better wall consistency. Simplified geometries also lower freight dimensions and classification costs—an edge for global supply chains.
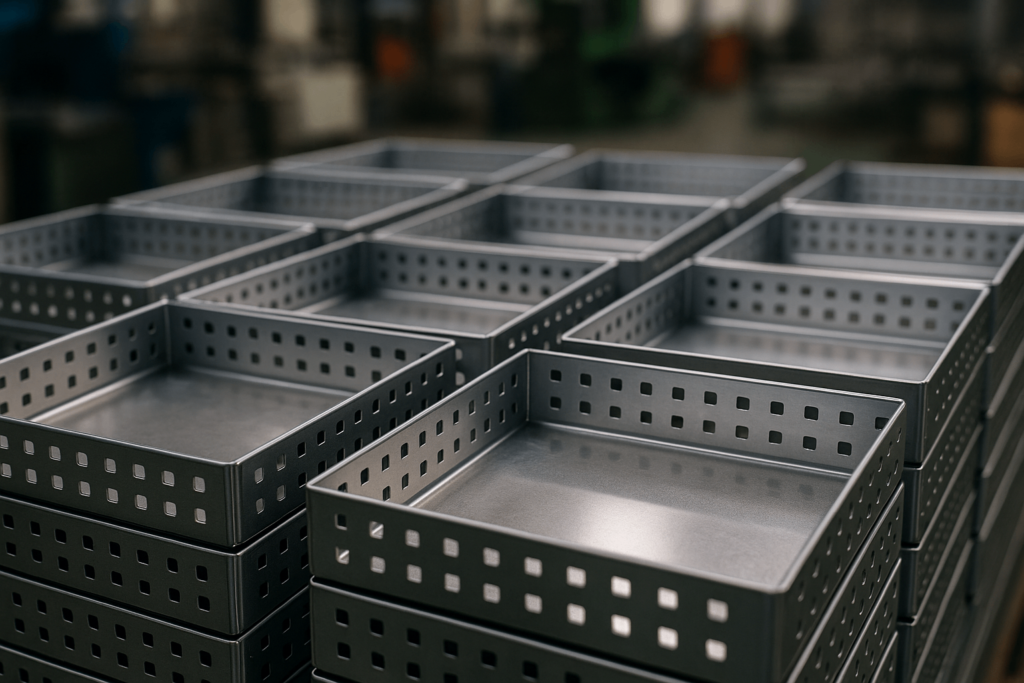
Misconceptions That Undermine Good Procurement Decisions
“Hydroforming isn’t viable for small batches.”
Soft-tooling and additive dies now support batches as low as 50 units. YISHANG’s trial-run support lets buyers test geometry affordably.
“It’s only for auto parts.”
Beyond automotive, hydroforming is being adopted in medical housing, data cabinets, power electronics, and advanced molding technologies.
“Any supplier can do hydroforming.”
Precise control of wall thinning and forming force requires simulation and tooling expertise. YISHANG provides dimensional reports and ISO 9001/RoHS documentation with every delivery.
Clarifying these myths can prevent costly sourcing mistakes.
Application Highlights: Why Global OEMs Choose Hydroformed Parts
In performance-driven sectors like aerospace and automotive, hydroforming supports fatigue resistance and lightweighting.
In hygiene-critical applications such as medical enclosures, it eliminates weld seams that trap contaminants.
Hydroformed parts are also used in:
Automotive: Battery trays and subframes with fewer parts and improved strength.
Aerospace: Skin panels with superior surface quality and aerodynamic properties.
Medical & Equipment: Sterile, seamless enclosures where cleanliness is crucial.
Energy & Infrastructure: Custom rail enclosures, structural components with embedded features like cam shapes.
Buyer-Focused Assessment: Is Hydroforming Right for Your Business?
Ask your team:
Does this part require structural uniformity with fewer seams?
Can we reduce tooling changeovers across SKUs?
Is our defect rate or QA effort increasing due to weld failures?
Will consolidated geometry improve shipping and classification?
Can rapid prototyping help accelerate new product launch?
If the answer is “yes” to most, hydroforming deserves a sourcing evaluation. YISHANG offers DFM collaboration pre-RFQ to improve feasibility and tooling ROI.
A Process That Speaks to Strategic Buyers
In fast-paced OEM cycles, hydroforming offers a clear path to structural consistency, form accuracy, and simplified workflows.
For manufacturers scaling globally, hydroforming supports reliable execution from prototype to production.
Ready to evaluate hydroforming for your next build? Contact YISHANG for engineering feedback or send us your drawing for a free DFM evaluation.