Melting Point of Aluminum: Why This Number Drives Industrial Decisions
Aluminum’s melting point—660.3°C (1220.5°F)—is more than a scientific detail. It directly influences manufacturing processes like extrusion, die casting, welding, and coating. For sourcing professionals managing overseas aluminum fabrication shops, this value determines alloy selection, thermal budget, and compatibility with fabrication methods.
Why Buyers Should Care About Aluminum’s Behavior Near the Melting Point
Melting begins gradually. The behavior of aluminum just before and during melting—such as heat absorption and structural breakdown—affects fabrication accuracy. In processes like aluminum CNC machining or aluminum extrusion, thermal overshoot can cause distortion, disrupting aluminum fabrication tolerances.
Thermal expansion during the pre-melt phase can also create microgaps or slight shifts in extrusion die pressure, which may not be visible until post-processing inspection. For procurement teams, this means hidden quality risks unless thermal control is verified upfront.
Which Alloy Should You Choose Based on Melting Range?
Pure aluminum is rare in industrial use. Alloys like 6061, 7075, and 2024 have varied melting behaviors that affect their use in structural and high-temperature settings.
Alloy | Melting Range (°C) | Melting Range (°F) |
---|---|---|
6061 | 582–652 | 1080–1205 |
7075 | 475–635 | 887–1175 |
2024 | 500–638 | 932–1180 |
The 6061 aluminum melting point range supports high ductility and thermal conductivity, while 7075 aluminum, known for its strength, requires tighter heat control due to lower melting thresholds. Consider whether aluminum anodizing or aluminum powder coating is required—some alloys handle post-processing heat better.
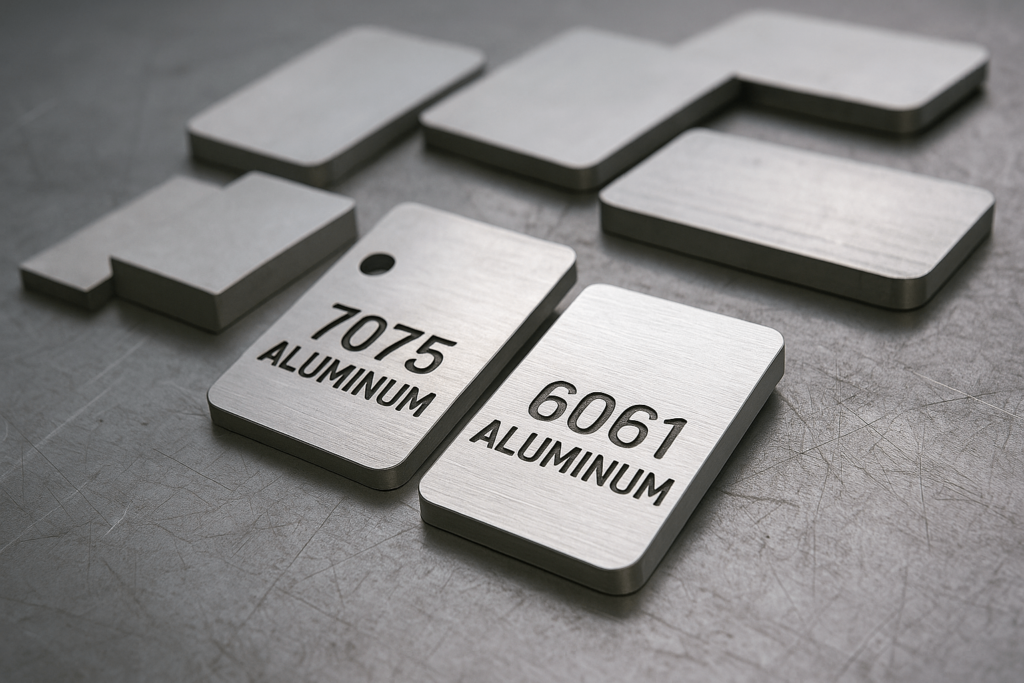
What Affects Aluminum’s Melting Behavior?
Impurities can lower the melting point, introducing flow interruptions or aluminum casting defects. During aluminum die casting, excess silicon or iron can cause brittleness or incomplete fill. That’s why aluminum die casting melting temperature control is critical.
In additive manufacturing or micro-part injection molding, finer aluminum particles melt faster and less evenly, increasing porosity risk—especially relevant in aerospace brackets and energy enclosures.
External factors such as atmosphere (argon vs. air), pressure, and heat rate must be controlled to prevent phase distortion. Buyers should validate whether aluminum extrusion process and casting operations incorporate controlled environments.
Aluminum Extrusion: How Melting Point Impacts Quality
The aluminum extrusion process requires precise control of billet temperature. Ideal pre-extrusion heating is 470–500°C. Overheating—especially past 540°C—can lead to internal cracking, grain coarsening, or texture variation in 2020 aluminum extrusion and 80/20 modular systems.
Without adequate melt control, post-treatment processes like aluminum powder coating and anodizing may suffer from poor bonding or inconsistency. For example, powder coated aluminium railings used in outdoor structures fail corrosion testing when melting stages are poorly managed.
Melting Point vs. Defects: What Buyers Should Watch For
Unstable melt temperatures often lead to cold shuts, shrinkage cavities, and inclusions. In thin-walled parts, even a 5°C variance can compromise dimensional integrity. This is especially critical when sourcing aluminum die casting parts for electronics or energy enclosures.
Buyers should request process data: What’s the melt curve control range? Are IR thermocouples or pyrometers used? Has the supplier implemented aluminum casting defect classification protocols (NADCA or ASTM B85 standards)?
Tolerances Near Melting Zones: An Overlooked Procurement Factor
As aluminum approaches its melting range, minor expansion can result in deviation from standard tolerances. This is most evident in aluminum CNC service operations or aluminium laser cutting near heat-sensitive outlines.
For aerospace brackets or automotive fixtures, aluminum fabrication tolerances need to remain under ±0.05 mm. Any heat-induced warpage makes high-precision assembly difficult, increasing post-machining and QC costs. Buyers should ask for documented heat stabilization strategies.
Recycling: Why Melting Point Still Matters
Recycled aluminum saves up to 95% energy but introduces melt variability. When reused without precise sorting, different alloying elements can shift the melting curve significantly.
During remelt, dross formation must be tightly managed to prevent defect carryover into products like aluminum extrusion parts or aluminum anodized finishes. Facilities like YISHANG monitor melt ranges between 650–665°C using automated pyrometry, with dross rejection rates under 0.8%.
When Melting Point Made or Broke Projects
Telecom enclosures warped due to excessive iron in 6061 aluminum.
Beverage die casts failed due to over-melting and incomplete cavity fills.
Aerospace housings using 7075 aluminum powder showed porosity due to uncontrolled heat flux during molding.
Aluminum mold failures occurred when mold release agents triggered phase fluctuation near the melting point.
These examples underscore why thermal control must be a sourcing conversation—not just a factory issue.
Key Takeaways for Buyers
Instead of just asking “what temperature does aluminum melt at,” consider:
Which aluminum alloy is best for high-temperature applications?
What aluminum fabrication tolerances does the supplier control?
Does melting point affect aluminum extrusion quality?
What thermal checks exist to prevent aluminum casting defects?
Can the supplier provide melt control logs for aluminum die casting?
Engineer’s Note:
Keep billet temperatures below 650°C in extrusion.
7075 aluminum yield strength drops 12% past 610°C.
Aluminum anodizing and powder coating should follow stabilized heat treatment only.
YISHANG applies strict melt profiling and thermal consistency monitoring across aluminum extrusion, die casting, CNC machining, and finishing. Ask us how we ensure quality in every molten drop.
FAQs
Q1: What aluminum alloy is best for high-temperature applications?
6061 is widely used due to its balance of strength and thermal resistance. For higher performance, 7075 offers strength but requires tighter heat control.
Q2: Does melting point affect aluminum extrusion quality?
Absolutely. Overheating alters grain structure and causes tearing. Proper melt monitoring ensures dimensional precision and finish consistency.
Q3: What are common aluminum casting defects linked to melting issues?
Shrinkage cavities, cold shuts, gas porosity, and oxide inclusions often arise from poor melt control.
Q4: How can buyers ensure aluminum fabrication tolerances are maintained near the melting zone?
Ask for data on thermal expansion management, toolpath compensation in CNC machining, and post-process inspection protocols.
Q5: What alloy works best for powder coated aluminium structures?
6061 is a popular base, but for high-load structures, consult on 5052 or 7075 with your aluminum fabrication shop. The surface should be treated post-extrusion and pre-powder coating.
Q6: Can recycled aluminum match primary aluminum performance?
Yes, if melt temperature is stabilized and alloy blending is controlled. YISHANG uses 3-stage filtering and melt logging to ensure parity.