When Metals Don’t Match: Why Welding Stainless Steel to Carbon Steel Is a Unique Challenge
Welding stainless steel to mild steel is a frequent requirement for global B2B buyers sourcing structural frames, commercial cabinets, or equipment enclosures. For procurement teams and project engineers, the reliability of this joint involves more than compatibility—it determines downstream durability, product safety, and cost efficiency.
Mismatched base metals create disparities in thermal behavior and corrosion performance, all of which hinge on choosing the right filler rod. Poor filler selection may not show issues in trials but often leads to field failures, rework, or failed audits.
YISHANG brings 26+ years of precision metal fabrication experience to help buyers make technically sound, commercially smart decisions.
Metallurgical Differences That Complicate Welding Stainless Steel to Other Metals
Stainless steel—especially 304 and 316 grades—is corrosion-resistant due to its chromium and nickel content. Mild steel is more weldable and cost-effective, but lacks these alloys. Their mismatch creates unique welding challenges:
Thermal expansion differences cause residual stress or warping.
Weld dilution can create brittle or porous zones.
Galvanic corrosion arises in humid or outdoor environments.
Welding stainless to galvanized or black steel amplifies these issues. These risks must be managed proactively through rod chemistry, joint design, and post-weld treatment.
What Rod to Use When Welding Stainless to Other Metals: Beyond Just 309L
ER309L is the common filler rod for stainless-to-carbon steel welding due to its balanced chromium and nickel content. But suitability depends on more than metal type—it depends on structural load, compliance needs, and post-processing.
Use ER309L for standard 304-to-mild applications needing moderate strength.
Use ER312 for uncertain steel grades or high-stress joints. It tolerates more dilution and resists cracking.
Filler Rod | Chromium | Nickel | Application Example |
---|---|---|---|
ER309L | ~23% | ~13% | Display frames, vending panels |
ER312 | ~29% | ~9% | Outdoor kiosks, dynamic load racks |
As noted above, ER308L is designed for stainless-to-stainless only and should not be used in carbon interfaces.
In regulated sectors like food equipment manufacturing, welding 304 stainless to A36 steel with compliance in mind requires selecting rods that meet AWS A5.9 standards and support traceable welding assembly.
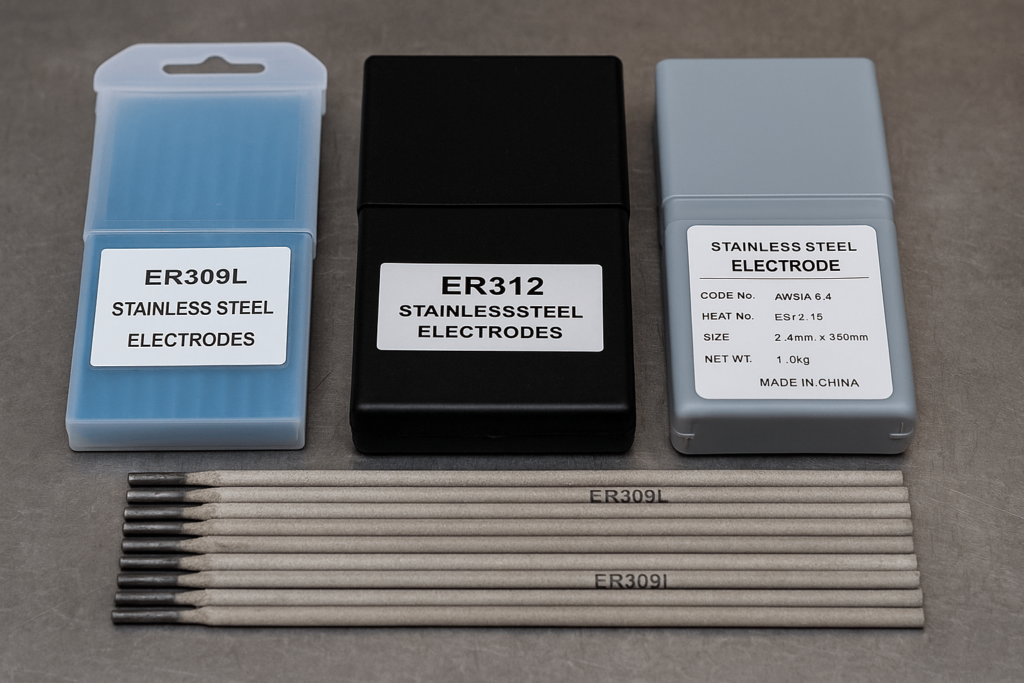
Best Welding Methods When Using 309L or 312 Rods
The welding process affects filler rod performance. B2B buyers managing contract welding should match process to use-case:
TIG (GTAW)
Ideal for visible, sanitary, or precision welds—such as in 316 stainless food service counters. TIG with ER309L and argon shielding ensures clean, corrosion-resistant joints.
MIG (GMAW)
Suited to scalable manufacturing. MIG with ER309L and 75/25 argon-CO₂ gas is efficient for sheet metal and cabinet weldments. Avoid pure CO₂ to minimize porosity and weld discoloration.
Flux-cored options are available for outdoor or vertical welds but require tight moisture control to prevent porosity. The advantages and disadvantages of MIG welding depend heavily on shielding gas control and operator consistency.
Welding aluminum to stainless is not viable via traditional methods due to incompatible melting points and oxide behavior. Aluminum welding requires different filler systems and is best kept separate in manufacturing planning.
Stick (SMAW)
Useful for job-site or rugged outdoor settings. E309L electrodes provide good strength but rougher appearance. Often used in utility fabrication, pipe racks, or when bead finish is secondary.
Application Snapshots from International Buyers
Stainless Tops on Steel Frames (USA)
NSF-certified food prep counters required TIG-welded 316 SS to mild steel frames using ER309L and post-weld acid passivation. The filler rod enabled clean joints and audit-ready hygiene.
Stainless Doors on Vending Machines (EU)
MIG welding with ER309L connected powder-coated chassis to 304 doors. This ensured reliable bonding and compatibility with powder coating for stainless steel.
Outdoor Display Units (APAC)
Unknown steel batches were joined with ER312 rods. Stick welding offered portability, and bead blasting stainless steel post-weld gave consistent appearance across batches.
These scenarios highlight how rod chemistry, weld method, and post-treatment together affect lifecycle and design-for-welding success.
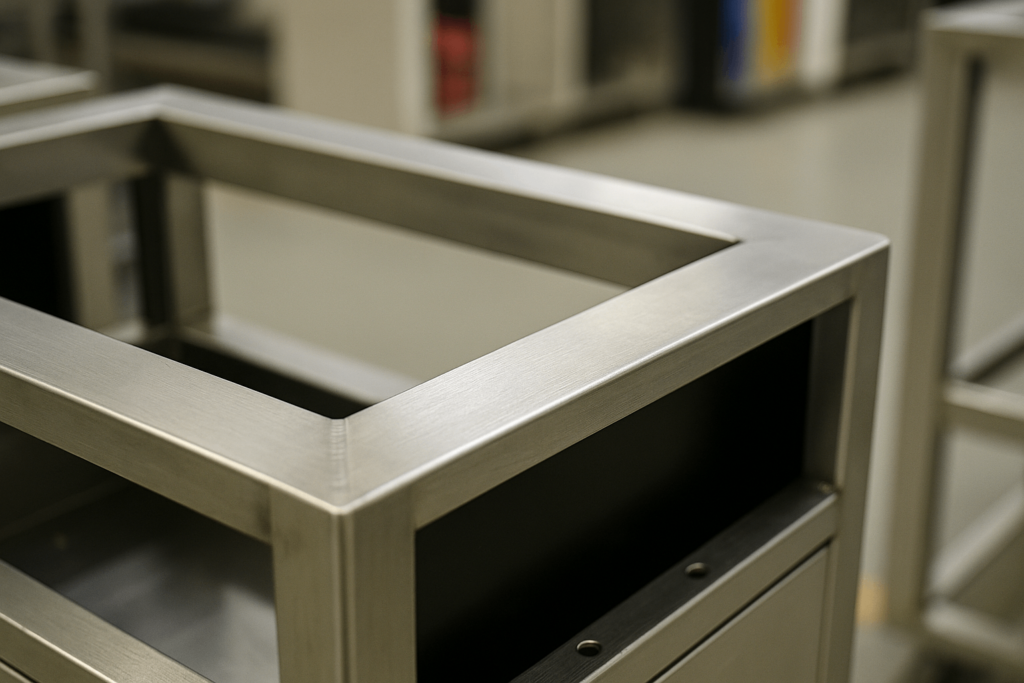
Procurement Risk Triggers and Matching Rod Strategy
Global buyers should consider the following:
Using ER308L instead of ER309L or ER312 for dissimilar joints (as noted above)
Relying on 100% CO₂ shielding gas
Overlooking post-weld discoloration or corrosion proofing
Use Case | Recommended Rod + Method |
Food-grade (304/316 to mild) | ER309L + TIG + passivation |
Structural with vibration or outdoor use | ER312 + MIG or Stick |
High-volume sheet metal (powder-coated) | ER309L + MIG + powder prep |
Mixed/unknown carbon steel grades | ER312 for alloy mismatch resilience |
Ensure vendors provide WPS documentation with rod type, gas blend, polarity, and weld positions. For critical applications, request material test reports (MTRs) and ensure rods meet ISO 14343 or AWS A5.9.
Design for welding also means planning rod compatibility with welding method, shielding gas, and finish expectations from the outset.
Quality Standards, Shelf Life, and Documentation for Consistent Welds
For repeatable production quality, verify that:
Rods have MTRs, AWS A5.9 or ISO 14343 certification
Moisture-sensitive rods are sealed or oven-dried
Flux-cored wires have documented shelf life
Rods or assemblies comply with ASTM A967 passivation or ANSI/AWS D1.6 where applicable
Porosity in welding is often caused by improper storage, contaminated gas blends, or misused filler metal. These are key causes of weld porosity and directly affect long-term integrity. Store rods carefully and batch-weld to reduce variation. YISHANG ensures batch traceability and operator certifications as part of its welding services—ensuring superior welding assembly quality control.
FAQs Buyers Ask About Welding Stainless Steel to Metal
What rod is best for welding stainless to galvanized steel?
ER312 is preferred for better impurity tolerance.
What rod to use for welding stainless steel to black steel?
ER312 or ER309L, depending on finish needs. Post-weld coating is advised.
Can stainless be welded using 7018 rods?
No. Use ER309L or ER312—7018 is for mild steel only.
Difference between ER309 and ER312?
ER312 offers more tolerance for unknown steels or stress loads; ER309 is for standard dissimilar joints.
Is TIG or MIG better for stainless-to-carbon?
TIG for clean appearance; MIG for high-output production.
Can you weld stainless to aluminum or brass?
Not with standard welding rods. Use mechanical fasteners or explosion welding.
Can you powder coat stainless after welding?
Yes. Smooth weld, prime, and apply powder coat.
Causes of weld porosity?
Moisture in rods, dirty gas mix, improper storage. See welding assembly notes above.
Soldering versus welding: what’s the difference?
Soldering uses lower temperatures and is for electrical or light metal joining, while welding fuses metals at high heat, ideal for structural applications.
Choose Smart, Weld Strong
For B2B buyers, selecting the right filler rod when welding stainless steel to other metals affects product quality, compliance, and cost efficiency.
YISHANG offers documented, spec-aligned welding assemblies that ensure long-term performance and traceability.
YISHANG’s team has delivered over 12,000+ custom metal welding assemblies to 50+ countries.
Let us help you optimize your stainless-to-metal welding plan today.