CNC Bending Service
At YISHANG, we offer CNC bending services, a specialized metal fabrication process that uses advanced CNC press brake machinery to precisely bend and shape sheet metal or metal plates into various forms and angles.
Key Benefits of Choosing YISHANG for CNC Bending
Precision and Accuracy
Our CNC bending process guarantees high precision in every part. Using state-of-the-art equipment, we achieve tight tolerances and consistent results, ensuring that each bend meets your exact specifications. Our ability to form intricate geometries with accuracy makes us a reliable partner for demanding projects.
Material Versatility
YISHANG is proficient in working with a wide range of materials, including stainless steel, aluminum, copper, and more. Whether it’s thin, high-strength materials or thicker, more rigid metals, we tailor our approach to suit the specific properties of each material, ensuring optimal results.
Efficiency
Our CNC bending services are designed for both small-scale prototype runs and large-volume production. Our machines are programmed for efficiency, enabling us to meet deadlines without compromising on quality. Whether it’s a few parts or thousands, YISHANG delivers consistent, high-precision results in a timely manner.
Engineering Expertise
Our engineering team works closely with clients from the design phase to optimize the bending process. We provide technical expertise to ensure that your designs are suitable for bending, reducing material waste and improving the overall efficiency of the production process.
What Is Metal Bending?
Metal bending is a fabrication process that involves deforming sheet metal by applying force to create specific angles or shapes without breaking or cracking the material.Also known as press braking, flanging, die bending, folding and edging, this method is used to deform a material to an angular shape.
Basic Sheet Metal Bending Terms
Understanding key terms in sheet metal bending is crucial for effective design and manufacturing. Here’s a guide to the fundamental terms:
- Bend Radius:The radius of the inside curve of a bend. It determines the tightness of the bend and affects the strength and appearance of the finished part.
- Bend Allowance:The amount of material added to the flat pattern to account for the material stretching during the bending process. It ensures the final part dimensions are accurate.
- Flange:The portion of the sheet metal that extends from the bend. Flanges are often used to add strength or provide attachment points.
- Bend Line:The line on the sheet metal where the bend occurs. This line is critical for accurately aligning and positioning the material before bending.
type of cnc bending
V-bending
In V-bending, the sheet metal is positioned over a die with a V-shaped opening.
A punch with a matching V-shape then descends and presses the metal into the die, creating a bend.
The angle of the bend is determined by the depth to which the punch presses into the die.
There are three main types of V-bending based on the depth of the punch’s engagement with the die:

Coining

This method uses high force to thin the metal at the bend, providing the highest accuracy and eliminates spring-back, resulting in extremely sharp and consistent angles.
Due to the high pressure used, coining thins the metal slightly at the bend, creating a well-defined edge.
It’s ideal for applications requiring precise bends, but it demands more force and energy compared to other methods like air bending or bottoming.
Coining is often used when tight tolerances are essential.
Bottoming
The sheet is pressed fully into the die, making it conform to the exact angle and shape of the die.
This method reduces spring-back, leading to more accurate and consistent bend angles compared to air bending. Bottoming requires higher force and specific tooling for each angle, but it results in clean, sharp bends and is ideal for applications where precision is crucial.
While more rigid than air bending, it offers greater control over the final shape of the part, making it popular in high-precision fabrication.
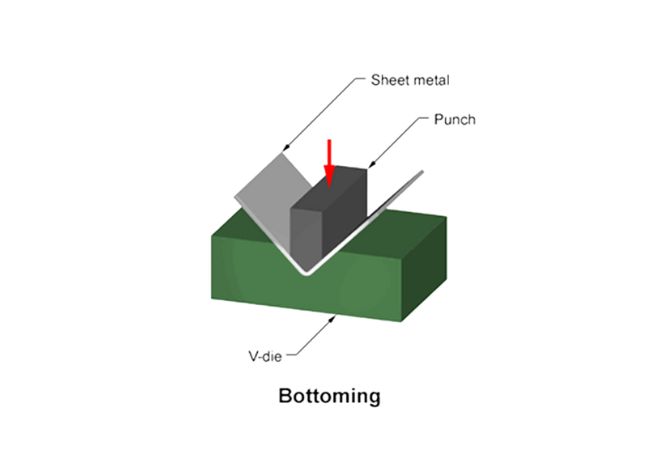
Air Bending

Unlike bottoming or coining, air bending allows the sheet metal to form at various angles by controlling how far the punch descends. This method requires less force and offers flexibility, as the same tooling can produce different bend angles.
However, it may result in less precision due to spring-back, requiring adjustments to achieve the desired bend angle.
Air bending is widely used for its efficiency and adaptability across various materials and thicknesses.
U-Bending
In U-bending, the metal is bent into a U-shape using a similar process to V-bending. However, the punch and die are shaped to create a U profile rather than a V.
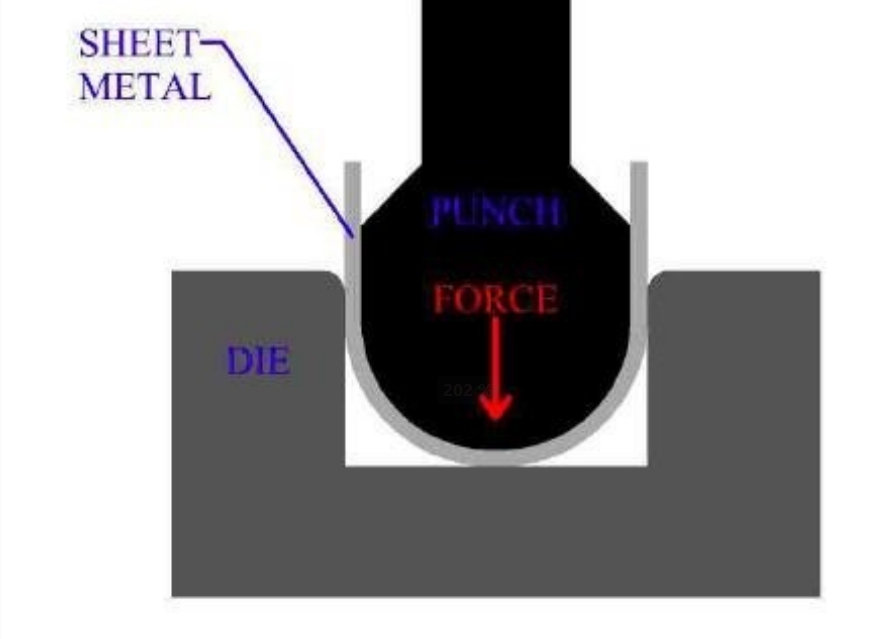
Wipe Bending
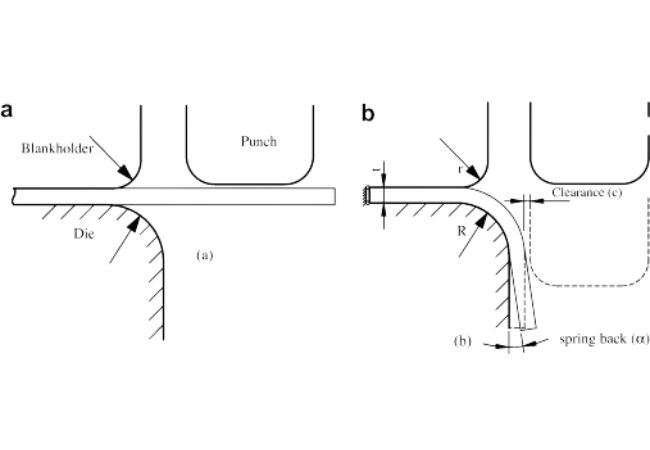
In wipe bending, the sheet is held in place against a die while a punch presses against the edge of the metal, bending it around the edge of the die.
This method is often used for making smaller, more intricate bends in the metal.
Roll Bending
Roll bending is a process used to bend large sheets of metal or produce cylindrical shapes, such as tubes, tanks, and pipes.
By passing the sheet metal between rollers and adjusting their position, the sheet is gradually bent into curves or full circles, making this method ideal for creating large-radius bends and cylindrical forms.
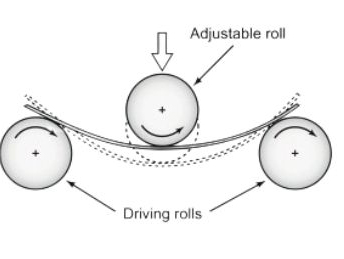
Rotary Bending
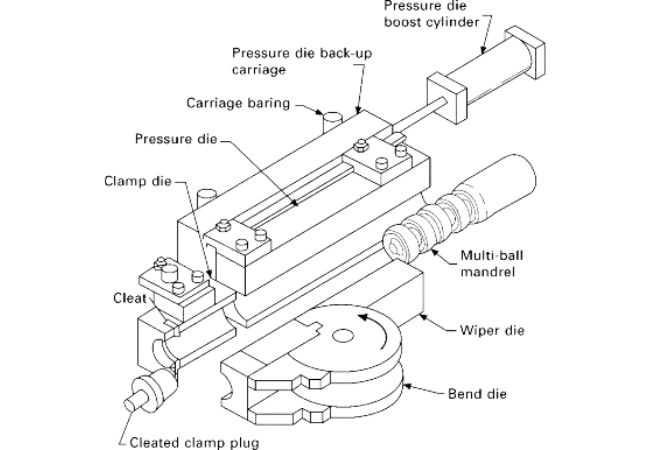
Rotary draw bending is a widely used metal forming process that shapes smooth, precise curves in tubing, pipes, or bars.
The workpiece is clamped to a rotating die, while a pressure die helps bend it along the die’s contour. A mandrel is often used to maintain shape and avoid collapse.
This method delivers high-precision, tight-radius bends, ideal for automotive, aerospace, and construction industries, producing clean and repeatable results with minimal distortion or wrinkling.
Folding
Folding is a precise sheet metal bending process that uses a folding machine or press brake to create defined angles. The metal is clamped securely, and force is applied to bend it along a straight line, producing components like flanges, boxes, and panels.
This method ensures accuracy and consistency without compromising the material’s integrity.

Metals Used in Sheet Metal Bending
- Aluminum alloys, known for their adaptability, come in various types with distinct properties.
- Aluminum 5052 is highly malleable and easy to bend, typically only facing cracking issues during reworking.
- Aluminum 6061, on the other hand, can be difficult to bend due to its tendency to crack, though its malleability improves with annealing.
- Overall, aluminum’s light weight and high workability make it an excellent choice for applications that require bending with minimal cracking.
- Mild steel offers a good balance of strength and flexibility, making it cost-effective and versatile for bending. It’s readily available but prone to rust, requiring coatings like galvanization for protection.
- Stainless steel provides high strength and excellent corrosion resistance, ideal for structural applications. However, its hardness makes it challenging to bend, necessitating more advanced machinery and increasing costs.
- Copper’s high ductility allows for easy bending without cracking, making it suitable for specialized applications like plumbing. While it offers excellent conductivity, its cost and tendency to tarnish can be drawbacks.
Tools and Equipment for Sheet Metal Bending
Press Brake
- A press brake is the primary machine used for sheet metal bending. It consists of a punch and die, and can be manual, hydraulic, or CNC-controlled.
- CNC Press Brakes: These computer-controlled machines offer precision and consistency, allowing for complex and repeatable bends in large production runs.
Dies and Punches
- Dies and punches come in various shapes and sizes to accommodate different bending needs.
- V-Dies: The most commonly used die, with a V-shaped opening, is used for V-bending.
- U-Dies: Designed for U-bending, these dies form U-shaped profiles.
- Offset Dies: Used to make two bends in one stroke, creating a Z-shaped bend.
Roll Benders
- For roll bending, specialized machines with multiple rollers are used to form curved shapes, such as cylinders or arcs.
Wiping Dies
- Used in wipe bending, these dies hold the sheet metal while a punch presses against the edge, creating a bend.
Conclusion
Sheet metal bending is crucial for precise fabrication.With our expertise and this guide’s insights, you can achieve optimal shapes and designs.Choose us for expert bending and high-quality results tailored to your needs.