For international wholesale buyers, surface marking isn’t a minor detail—it plays a critical role in quality control, product traceability, and global regulatory compliance. When choosing between etching and engraving, your decision can directly influence durability, branding presentation, and total production efficiency.
This guide is designed to help you evaluate which metal marking method—etching or engraving—is the most appropriate for your procurement needs. Whether you’re sourcing vending machine panels, industrial enclosures, or medical housing components, understanding the marking method helps minimize rework, simplify audits, and ensure consistency across large-volume orders.
YISHANG operates its own in-house fabrication and marking lines with more than 260,000 parts processed annually for global clients. All marking operations are conducted under strict ISO 9001 quality management protocols to ensure consistent output and traceability.
What’s the Difference Between Etching and Engraving? — Process, Tools & Output
Etching and engraving differ significantly in execution, despite both being permanent metal marking methods. Etching uses either chemicals or lasers to alter the surface without deep penetration. It’s fast, scalable, and suitable for branding and serial markings on thin materials. Chemical etching is cost-efficient for fixed designs, while laser etching is ideal for short lead-time custom batches.
Engraving physically removes metal using either mechanical or laser techniques. CNC machines or rotary tools dig into the substrate, creating deeper, wear-resistant markings. Laser engraving, which uses fiber or CO₂ lasers, offers precision without tool degradation—crucial for long production runs.
Understanding the difference between engraving and etching is important for determining compatibility with production speed, marking depth, and substrate type. Etching is typically better suited for smooth, aesthetic branding. Engraving, with its durability and tactile texture, excels in traceability and long-term industrial use.
In practice, materials like stainless steel 304, aluminum, and galvanized metal are commonly used for both. However, for harder metals or parts subject to friction, engraving provides better retention. Many wholesale buyers ask: laser etching vs engraving—which lasts longer? The answer depends on how deep and durable the mark needs to be.
Below is a quick reference for material compatibility with each marking method:
Material | Recommended Marking Method |
---|---|
Stainless Steel 304/316 | Laser Etching / Engraving |
Aluminum | Chemical Etching / Laser Etching |
Galvanized Steel | Laser Etching |
Copper / Brass | Chemical Etching / Engraving |
Mild Steel | Laser Engraving |
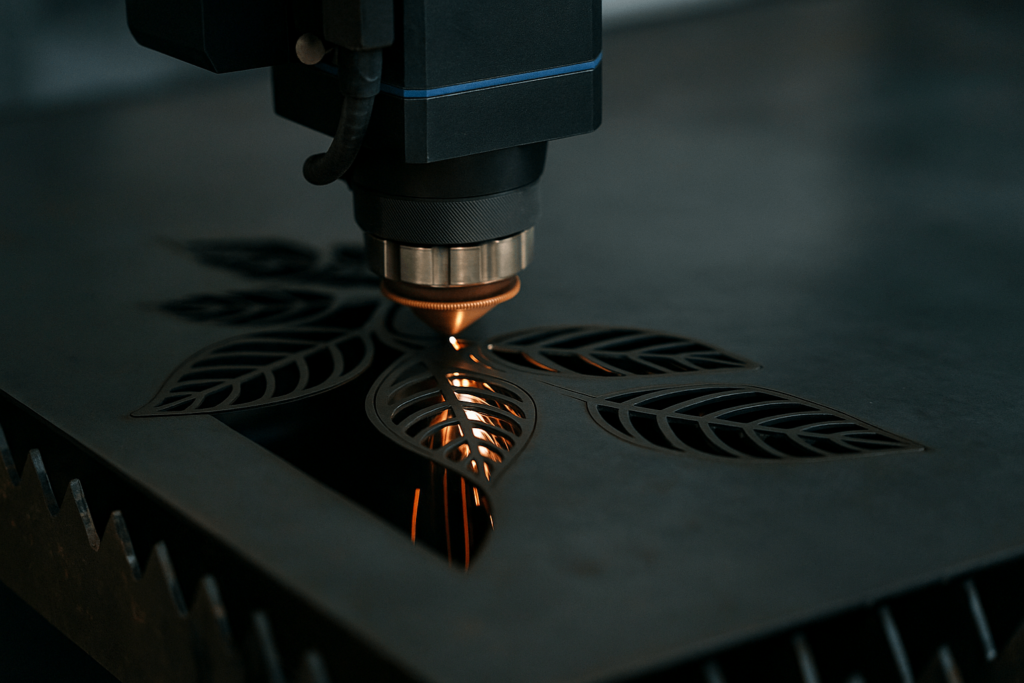
Core Comparison — Performance, Appearance, and Durability
From a sourcing perspective, consistency and longevity are essential. Engraving creates deeper marks—between 0.1 and 0.5 mm—ensuring that part numbers, compliance codes, or safety warnings remain readable after transport, assembly, and field use. These marks don’t fade under pressure, cleaning, or abrasion.
Laser-etched markings, while fast and precise, are more superficial. They offer high-definition graphics and contrast, ideal for branded plates or interface panels. But under heavy handling or outdoor exposure, they can degrade faster. This is where laser engraving vs laser etching becomes a key consideration in evaluating product lifecycle.
B2B buyers managing international shipments also prioritize barcode and QR code readability. Deep engraving maintains clarity during customs inspection, third-party handling, and post-sale servicing. While etching may initially look sharper, it often lacks the physical depth required to endure industrial wear or chemical cleaning agents.
In short: if the product’s surface will be touched, scrubbed, or exposed to harsh elements, engraving provides added insurance against illegibility.
Cost, Speed, and Production Considerations
Cost control is central to any large-scale procurement plan. In this regard, etching—especially chemical etching—offers excellent economies of scale. When designs remain unchanged, masks can be reused across thousands of units. This makes it attractive for static branding and decorative applications in bulk.
Laser etching strikes a balance by eliminating the need for physical masks, allowing for agile production changes with minimal downtime. You can switch from one SKU to another in minutes using digital files, a major benefit for buyers managing SKU variation.
Engraving is often costlier upfront due to longer marking times and higher equipment investment. But it pays off in high-risk or compliance-heavy scenarios. Laser engraving, in particular, reduces the likelihood of rework or recalls caused by unreadable serials or failed audits. Suppliers like YISHANG optimize this process with automated jigs and material handling systems, ensuring high throughput without sacrificing accuracy.
Procurement teams should also weigh post-processing time. Etched parts might need chemical neutralization or protective coating. In contrast, engraved parts typically come production-ready, reducing time-to-assembly and simplifying warehouse flows. All of these factors affect your total landed cost.
Decision Guide — How to Choose Based on Your Product’s Needs
For buyers focused on reducing procurement risk, this section offers a quick framework to determine which marking method aligns with your project goals.
Start by answering:
Will the parts be exposed to frequent handling, heat, or solvents?
Do you require serialized markings, QR codes, or compliance IDs?
Is the design static, or will you rotate SKUs frequently?
How critical is surface finish and brand presentation?
Depending on your answers, the table below can serve as a sourcing decision tool:
Use Case Scenario | Preferred Method |
High-volume, unchanged design | Chemical Etching |
Low-volume, variable orders | Laser Etching |
Harsh operating environments | Laser Engraving |
Aesthetic faceplates or panels | Laser Etching |
Long-term product identification | Deep Engraving |
This approach helps procurement managers align marking method selection with operational realities such as lead time, production flexibility, and after-sales requirements.
Application Validation — Performance Evidence from Production Cases
A global electronics wholesaler sourcing stainless steel panels for vending systems faced failures with chemically etched tags—QR codes faded after high-humidity shipping. By switching to laser engraving with YISHANG, barcode readability improved across all regions. Return rates fell by over 15% within one quarter.
In the agriculture equipment sector, a European OEM opted for laser etching to mark galvanized metal housings. Though not intended for extreme exposure, the etched codes remained legible for over three years under moderate sun and water conditions. This validated the process for mid-durability applications.
YISHANG has supported bulk projects in industries including automotive systems, commercial appliances, medical enclosures, advertising displays, and power storage equipment. These experiences allow us to advise on marking strategies tailored to real-world durability, certification, and logistics demands.
These outcomes emphasize that etched vs engraved isn’t a one-size-fits-all question. Each case proves that the right marking method depends on usage intensity, logistics conditions, and downstream serviceability. By making the right choice early, buyers reduce long-term costs and improve customer confidence.
Conclusion
Understanding the difference between engraving and etching can prevent costly errors, delays, and compliance issues in global procurement. For volume branding or dynamic product ranges, etching provides speed and flexibility. For mission-critical traceability and field resilience, engraving remains unmatched.
YISHANG delivers both technologies under ISO 9001 and RoHS standards, with full OEM/ODM support for global buyers. Our process control ensures markings meet performance needs across industries—from medical to construction to energy.
Contact YISHANG today for expert advice on the best marking solution for your bulk metal components.
📩 Request a quote now and simplify your sourcing process with confidence.