Introduction: Powder Coating Lifespan Isn’t Just a Number
When wholesale buyers ask, how long does powder coating last?, the real concern is durability under real-world stress—UV exposure, corrosion, impact resistance, and supplier quality control. This question isn’t about years alone. It’s about performance, consistency, and risk reduction in sourcing.
This article gives procurement professionals and technical buyers an in-depth view of what determines powder coating longevity. Through lab testing standards, industry data, and manufacturing insights, we help you understand what impacts service life, and how to choose the right powder coating factory to meet your application demands. This is a decision-making tool—not general education.
Redefining “Lifespan” in Powder Coating: Performance Before Numbers
For commercial and industrial procurement, powder coating durability must be tied to three metrics—not vague timelines:
Aesthetic Durability: Will the gloss, texture, or color of your black powder coat fade or chalk after 2 years in sun?
Structural Performance: Does the coating resist edge cracking or abrasion during shipping or use?
Functional Resistance: Will powder coated steel rust under salt spray or in humid warehouses?
Under ASTM B117 testing, standard polyester coatings may last 1,000 hours before rust onset, while fluoropolymer types can exceed 4,000. But if steel powder coating is applied without phosphate prep, corrosion starts within months—especially at edges.
If your clients rely on outdoor durability, “15 years” means nothing unless the powder type, curing, and pretreatment align. At YISHANG, we validate all coatings through UV exposure and adhesion tests to match the real-use cycle.
Surface Prep: The Most Common Source of Failure (But Often Ignored)
Your supplier’s surface treatment process will make or break your coating ROI. Over 70% of powder coated metal failures trace back to poor pretreatment.
We’ve seen it happen: a buyer orders a bulk batch of powder coated aluminium railings, only to see blistering within 8 months due to skipped chromate pretreatment.
At YISHANG, all base materials—aluminum, galvanized steel, stainless—undergo degreasing, deionized rinsing, and phosphate conversion. For powder coating galvanised steel, zinc residues must be removed to ensure adhesion. Otherwise, expect delamination.
We also round weld seams and prep corners, since thin film on edges is a key vulnerability. If your parts have sharp contours or deep weld joints, request edge radius confirmation and sealing procedures in QA.
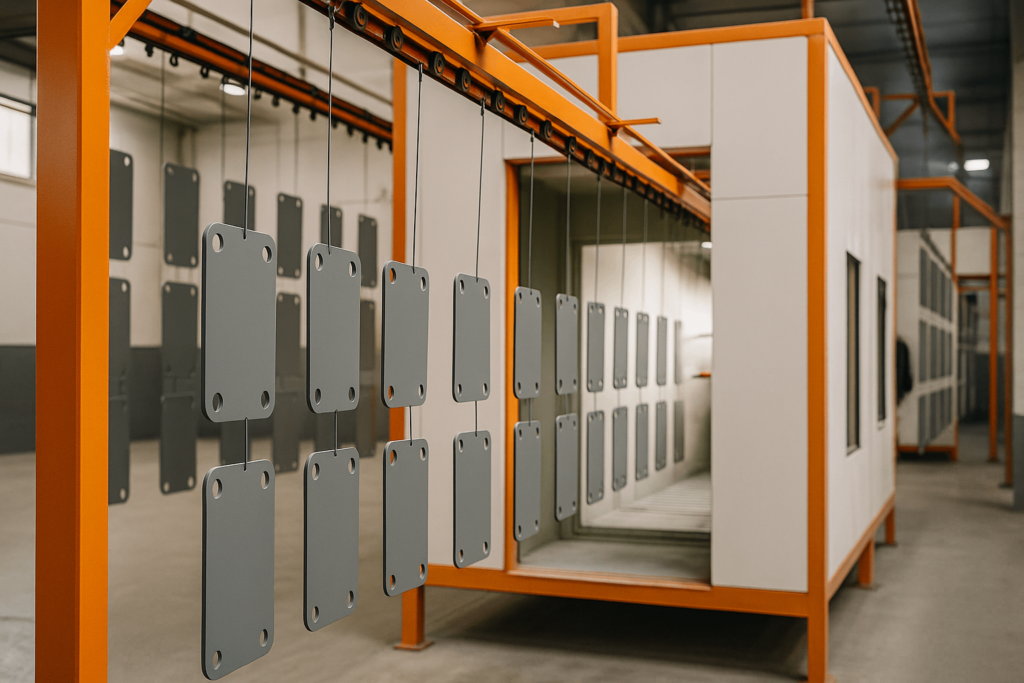
Powder Chemistry: Picking the Right Coating for ROI, Not Shelf Life
In B2B supply chains, mismatching coating type to application is a recurring issue. “Polyester is fine” isn’t always true.
Here’s a field example: A buyer specs white powder coat finish for outdoor HVAC units but uses epoxy powder—within 2 years, units yellowed and cracked.
To optimize cost vs. longevity:
Epoxy = Best indoor, chemical resistance, but chalks outdoors.
Polyester = General outdoor, UV stable, decent abrasion resistance.
Polyurethane = Better toughness for powder coated patio furniture or construction gear.
Fluoropolymer = Best for sun, salt, and architectural-grade coating. Ideal for powder coated fence systems near coastlines.
YISHANG helps clients select powder type based on substrate, use case, and expected exposure, not just catalog availability. We also document powder coating powder batch specs—ensuring coating repeatability and traceability.
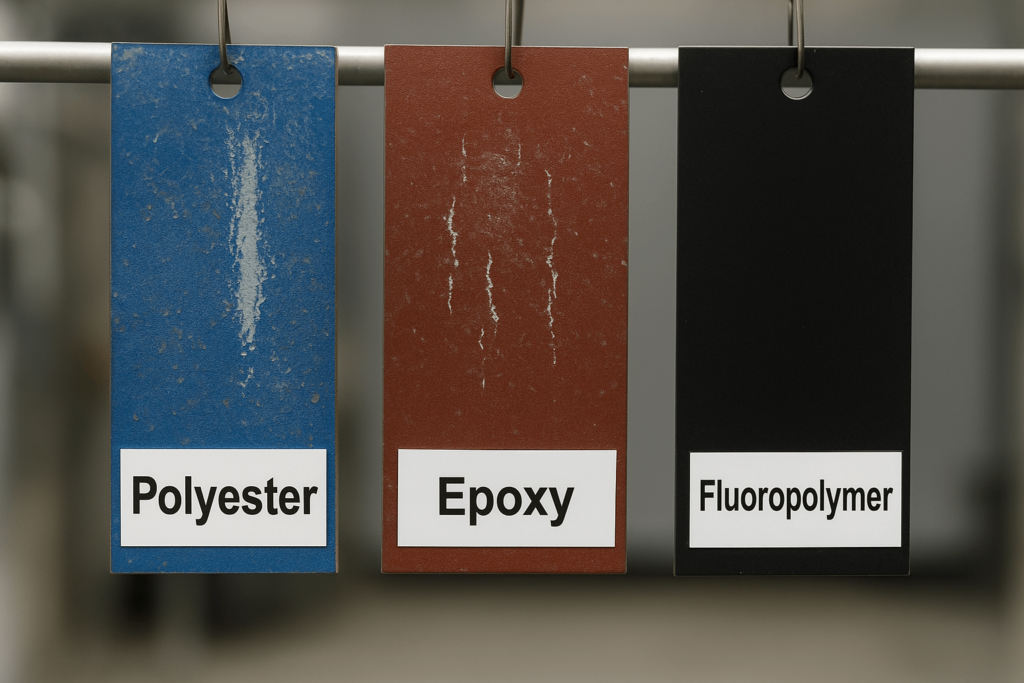
Curing: The Most Overlooked Technical Risk for Bulk Orders
Powder coating process steps aren’t complete until precise thermal curing occurs. Even a well-applied coating of powders can fail without correct oven calibration.
Industrial buyers often face this challenge when ordering large, thick parts or multi-batch lots: inner edges may be undercured, even if the surface seems fine.
We monitor cure profiles with embedded thermocouples. Our ovens are zoned for uniformity across batches. We also document powder coat thickness to ensure optimal range—too thin invites corrosion; too thick leads to brittleness.
Be wary of suppliers who skip post-cure testing. At YISHANG, every order passes solvent rub and pencil hardness assessments to confirm cross-link integrity.
Real-World Exposure: Where Cheap Coatings Fail First
Can powder coated steel rust? Yes—especially without the right prep and chemistry. Exposure environments are rarely gentle.
From snow to sun, coastal spray to acidic air, your product’s destination matters. Many powder coated surfaces fail because of one factor: assumption.
That’s why we test all systems under:
ASTM B117 salt spray
ASTM D4587 UV chamber
ASTM D3359 adhesion (tape pull)
For industrial powder coating, we match powders to site profiles. A matte finish used for black powder coated metal in retail might crack outdoors. A high heat powder coat for automotive brake parts must resist thermal cycling.
If your order will be exposed, request a documented powder coating description of its UV inhibitors, binder resin type, and salt spray rating.
Design Choices That Impact Durability (And Reduce Coating Claims)
Some buyers overlook design impacts. But in our experience, even minor geometry changes—such as avoiding tight inside corners or adding water drainage holes—can extend powder coating durability by years.
For example, flat panels on powder coated fence posts collect water unless angled. Buffing powder coat surfaces before recoating saves time, but poor prep allows future failure.
We often support customers in CAD optimization. If you’re designing powder coated aluminium parts or steel powder coating brackets, we can suggest weld type adjustments, hang hole placement, or grounding points for better coverage.
Maintenance: An Afterthought That Affects Warranty Costs
B2B buyers rarely consider maintenance, but it directly impacts complaints and returns. Let clients know:
Clean powder-coated material with pH-neutral cleaners.
Avoid pressure washers or acidic solutions.
Inspect coated metal annually for edge rust or chips.
We provide care guides for bulk orders. For powder coated car components or metallic powder coat decorative parts, we also offer touch-up kits and recoating instructions.
A note: powder coating over paint is risky. Adhesion suffers unless surface is mechanically abraded. If retrofitting, consult us before attempting powder coat over paint workflows.
Supplier Criteria for High-Volume Projects
For wholesalers and importers, it’s not just about price—it’s about risk control. A failed batch can destroy customer trust.
Here’s how YISHANG builds procurement trust:
RoHS + ISO 9001 certified
ASTM-validated testing (salt spray, adhesion, gloss)
In-house fabrication + powder coaters
Real-time batch QA records and photos
We are more than metal powder coaters—we engineer durability. Whether for automotive powder coating, commercial powder coating, or retail hardware, we offer complete process transparency.
Conclusion: Build Coating Confidence Into Your Supply Chain
How long does powder coating last? With the right materials, curing, and prep—20–30+ years. Without them? Failure in months.
Your customers won’t ask about powder paint chemistry—but they’ll notice if their powder coated surface fades or rusts. Make your sourcing decisions based on performance, not just appearance.
YISHANG helps procurement teams lower long-term cost, improve quality metrics, and protect brand trust through certified, engineered coatings.
FAQ: Powder Coating — Common Questions from Buyers
Can powder coating prevent rust?
Yes, when properly applied with correct pretreatment, powder coating provides a durable barrier that prevents moisture and air from reaching the metal substrate. However, powder coated steel can still rust if surface preparation is poor, edges are exposed, or the coating is chipped or undercured.
What is the best coating for outdoor steel?
For outdoor steel, polyester or fluoropolymer powder coatings offer the best UV and corrosion resistance. Fluoropolymer is ideal for marine or high-humidity environments. Always confirm that the powder is rated for exterior use and that the substrate has been phosphate-treated.
How long does powder coating last on steel?
On average, powder coating on steel can last between 15 to 25 years, depending on the environment, coating chemistry, and maintenance. In harsh outdoor or coastal conditions, selecting the right powder and pretreatment is essential to achieve this lifespan.
Can powder coating be used over previously painted surfaces?
Powder coating over existing paint is not recommended unless the paint is fully removed or abraded. Without proper mechanical bonding, powder coat over paint may result in poor adhesion and premature failure.
Is powder coating better than paint for industrial use?
Yes. Powder coating offers superior durability, chemical resistance, and cost-efficiency over time. It creates a uniform, thick finish without runs or drips and emits no VOCs, making it a preferred method in industrial powder coating applications.