Introduction: Why This Distinction Matters for Global Electrical Projects
For international wholesalers and project-based buyers, terminology can directly affect procurement accuracy. In cross-border sourcing, confusing an “electrical panel” with a “breaker box” can result in under-specification, shipment returns, or regulatory failure.
Whether you’re sourcing enclosures for solar systems, EV infrastructure, vending machines, or modular data centers, understanding the practical difference between these two terms helps ensure you’re specifying the right component from the start.
This guide provides technical clarity for professionals involved in purchasing, integration, or OEM manufacturing—combining application examples, fabrication standards, and decision-making insights from YISHANG, a trusted supplier of custom electrical panel enclosures.
Terminology That Impacts Global Procurement
An electrical panel—often referred to as a load center or panelboard—is an engineered enclosure that houses circuit breakers, bus bars, grounding paths, and input/output terminals. It serves as the distribution hub for commercial, industrial, or infrastructure-grade electrical systems.
Meanwhile, a breaker box is a term more commonly used in North American residential contexts. It generally refers to simpler setups that often lack smart integration, surge protection, or scalable modularity.
In procurement documentation, the use of the wrong term can lead to sourcing mismatches. For instance, specifying a “breaker box” in a tender that requires a 400A NEMA 4X outdoor-rated unit may mislead vendors into offering substandard products.
To avoid such risks, international buyers are encouraged to use terms like panelboard, distribution board, or UL-listed enclosure, especially when exporting to regulated markets. Referring to standards such as UL 67, IEC 61439, or NEC 408 can help suppliers align better with your technical needs.
Functional Differences with Direct Sourcing Impact
Functionally, commercial electrical panels are built for system complexity. With bus bar ratings of 250–600A, optional surge modules, and expandable layouts, they are ready for integration with smart infrastructure, energy metering, and renewable energy systems.
In contrast, breaker boxes are usually limited to under 150A, with a fixed number of breaker slots and basic steel enclosures lacking weather resistance or heat dissipation considerations.
From a sourcing standpoint, this means a panelboard opens the door for OEM configuration—custom DIN rail layout, hole positions, or pre-assembled terminals. A “breaker box” offers no such flexibility and often requires field modifications.
Projects involving solar combiner panels, EV charging nodes, or PLC control cabinets should default to specifying custom panels. These enclosures allow for high-precision fabrication—something YISHANG offers with CNC punching, folding, welding, and coating capabilities.
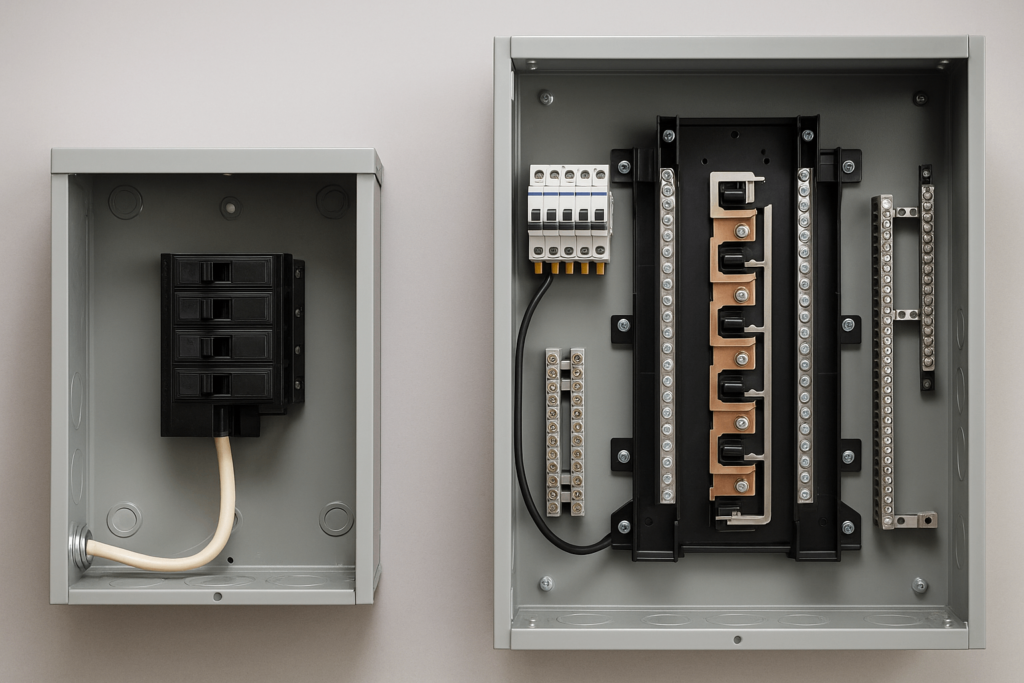
Safety, Compliance, and Standards Buyers Must Consider
International electrical projects are governed by diverse certification schemes. Buyers should prioritize products that meet RoHS, ISO 9001, and are compliant with UL 508A, CE, or region-specific NEMA/IP ratings.
Custom panels must accommodate:
AFCI/GFCI protection requirements
Labeling per CE or NEC standards
Surface finish suitable for outdoor or marine environments
Older or generic breaker boxes frequently fail these criteria. Their lack of grounding points or IP-rated gaskets can result in failed inspections, especially in jurisdictions requiring third-party product verification.
YISHANG’s products, for example, are fabricated to meet enclosure classifications such as NEMA 4X or IP65, which are standard in industrial kitchens, telecom shelters, and grid-tied solar systems.
For large-scale procurement, ensuring compliance upfront avoids delays at customs clearance or installation audits, especially for export-bound products.
Addressing Modern Infrastructure Demands
As projects increasingly demand integration with smart energy systems, remote fault detection, and renewable compatibility, the panel’s role is evolving. Today’s buyers expect panels to support:
Smart controllers and communication ports
Heat dissipation zones for inverter circuits
Surge modules or SPD compartments
Breaker boxes are typically not designed for this level of complexity. Modifying them post-delivery adds time, cost, and introduces uncertainty in system performance.
Applications such as:
Energy storage system (ESS) cabinets
EV infrastructure (AC/DC charging)
Public lighting controls or smart city sensors
…are now considered baseline in many large-scale projects. To meet these demands, YISHANG offers custom-fabricated panels with internal mounting brackets, cable routing cutouts, heat-dissipating backplates, and corrosion-resistant coatings.
These features reduce time spent on-site and ensure better compatibility with industry-grade electronics, including inverters, power optimizers, and monitoring modules. For OEM clients, starting with a scalable enclosure design is the most efficient way to manage mass production and product consistency across global installations.
YISHANG has supplied over 300 custom electrical enclosures for industrial projects across Southeast Asia, particularly in solar and battery storage deployments. These UL 508A compliant export panelboard solutions helped reduce lead times by up to 15% and minimized retrofitting costs at job sites.
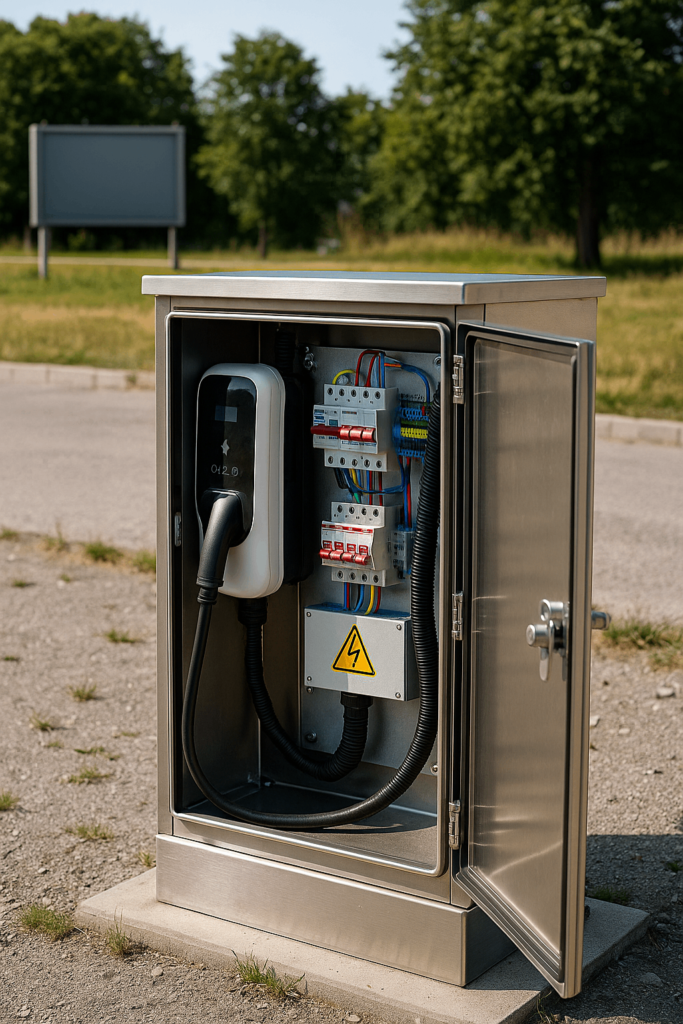
Buyer-Focused Decision Making
Distributors should stock panels rather than basic breaker boxes to address industrial and infrastructure clients. Panels offer configuration flexibility, reduce returns due to mismatch, and increase margins through value-added integration. Custom-fitted enclosures help avoid over-engineering and reduce on-site fitting cost by up to 20% in large installations.
EPC contractors benefit from specifying modular panel solutions. The ability to support 2–3X circuit expansion is critical in solar, energy storage, or BMS deployment. YISHANG panels, for instance, allow pre-mounted protection relays or combiner module bays—saving up to 25% in field assembly time.
OEM buyers gain precision with tailored fabrication. Whether it’s 1.5mm galvanized steel or brushed aluminum with IP-rated gaskets, panel enclosures can be cut and bent to exacting tolerances, including hinge types, laser-engraved labels, and bus bar punch-outs. We are a preferred OEM metal breaker box supplier for international integrators seeking long-term production stability.
Procurement Focus | Breaker Box | Electrical Panel |
---|---|---|
Smart Integration Support | ✖ | ✔ |
Global Compliance Options | ✖ | ✔ |
Custom Enclosure Sizes | ✖ | ✔ |
Weather/Corrosion Resistance | ✖ | ✔ |
OEM Configuration Support | ✖ | ✔ |
This comparison makes the sourcing decision clear when targeting professional-grade applications. For buyers searching for custom electrical enclosures for industrial projects, the electrical panel is the adaptable, scalable choice.
Conclusion: Clearer Terms, Better Orders
Procurement decisions affect installation success, client satisfaction, and product longevity. Knowing the difference between an electrical panel and a breaker box isn’t pedantic—it’s foundational to successful sourcing.
Specifying a certified, configurable panel system reduces on-site rework, enables regulatory clearance, and ensures compatibility with evolving tech requirements. It’s a strategic sourcing decision, not a technical formality.
YISHANG supports global buyers with RoHS-compliant, ISO-certified metal enclosures custom-engineered for industrial and commercial power distribution systems. We are a trusted UL 508A compliant export panelboard manufacturer with full-service OEM capacity.