Introduction: Why Global Buyers Should Understand Sintering in MIM
When overseas sourcing professionals evaluate high-volume precision metal parts, understanding the process of metal injection molding (MIM)—especially sintering—is more than technical curiosity. It’s business-critical.
Sintering transforms molded powders into fully functional, dense, and load-bearing components. For bulk buyers of automotive injection parts, electronic housings, or energy storage connectors, this step often determines whether a product delivers on durability, accuracy, and cost-efficiency.
At YISHANG, we’ve supported OEM and ODM clients across 50+ countries. We help them reduce unit variation, shorten lead times, and avoid post-processing expenses—primarily through controlled sintering. This article explains how sintering aligns with your key procurement priorities: consistent quality, repeatable tolerances, and long-term ROI.
How Sintering Fits into the MIM Production Line (And Why It Matters to You)
The MIM process includes four stages: feedstock preparation, injection molding, debinding, and sintering. While molding defines geometry, sintering is what makes parts functional and durable.
At YISHANG, we optimize this thermal process with hydrogen and vacuum furnaces, enabling densification above 97%. The result? Parts that are structurally equivalent to machined steel, but at scale and lower cost.
Shrinkage control—typically around 15–20%—is crucial to maintain tolerance consistency. When sintering is poorly managed, dimensional variance can impact product fit, especially in automotive injection assemblies or electronic enclosures. We address this with mold compensation simulations and zoned temperature profiles.
This ensures you get what you ordered, batch after batch.
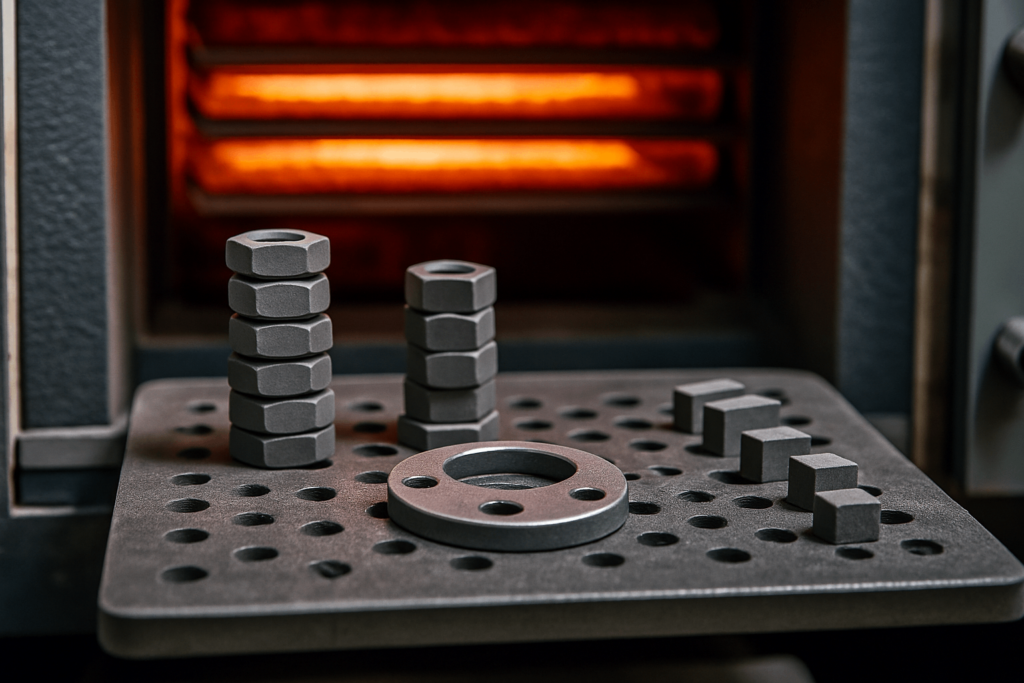
How Sintering Enhances Material Performance in Final Parts
Reliable parts start at the microstructure level. Controlled sintering closes internal voids and promotes uniform grain structure, improving mechanical integrity and fatigue resistance.
For example, sintered 17-4PH stainless steel from YISHANG regularly reaches 900 MPa tensile strength and 35+ HRC hardness—ideal for locking systems and structural supports. This performance rivals CNC or die-cast alternatives but with fewer secondary steps and lower tooling costs.
In real client cases, consistent sintering reduced part failure by 22% in surgical clamps and improved customer satisfaction with fewer RMAs. Fatigue-prone applications—such as in small battery connectors or moving mechanical linkages—benefit the most.
This is particularly important when working with materials like aluminum injection molding alloys, where lightweight performance still requires strength.
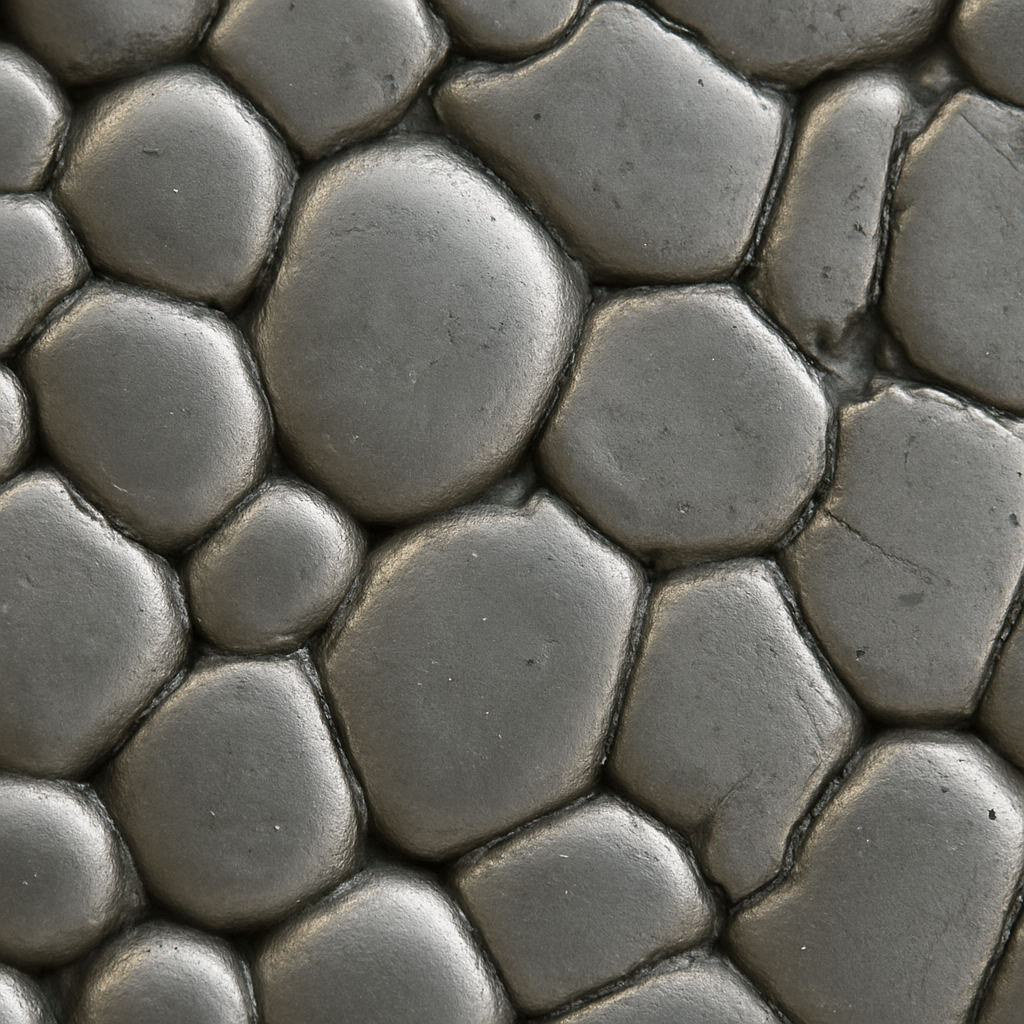
Enabling Design Freedom Without Manufacturing Risk
Sintering supports one of MIM’s greatest strengths: complex geometries at volume. But only when the sintering phase maintains design integrity during shrinkage.
Buyers in consumer electronics, medical tooling, and EV connectors often request parts with intricate lattices, thin walls (as thin as 0.25 mm), or multi-function consolidation. These are risky to manufacture using traditional aluminum injection molds due to cost or feasibility.
YISHANG addresses this with thermal simulations and support tooling strategies. Whether it’s a smartwatch shell, a mini sensor mount, or a housing for assist injection systems, we preserve part fidelity across sintering cycles.
Result? Faster product launches, fewer tooling changes, and fewer dimensional nonconformities.
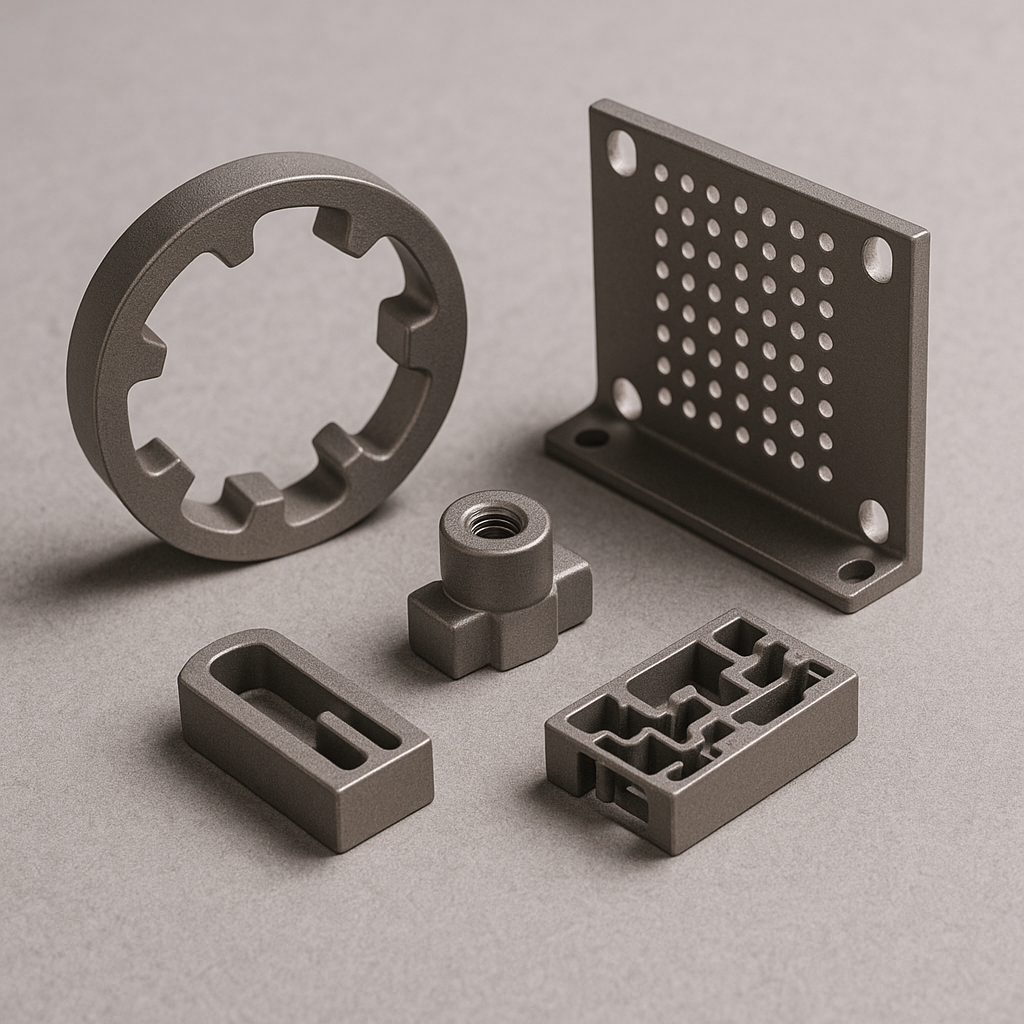
Predictability and Profitability: How Sintering Controls Cost and Quality at Scale
For B2B buyers, the ideal supplier offers more than just attractive pricing—they deliver predictable quality and scalable output. That’s where sintering proves its value beyond metallurgy.
Material Efficiency: Our MIM lines achieve >95% raw material utilization, compared to 65% typical in machining or aluminum injection molding. For high-volume orders, this dramatically lowers scrap and cost.
Tool Longevity: Sintering enables lower injection pressures, which protects aluminum injection mold tool life—especially important in multi-cavity high-output scenarios.
Energy and Cycle Cost: Batch sintering reduces energy consumption per part by 15–18%, optimizing kilowatt-per-yield across thousands of units.
Repeatability and Yield: With real-time gas analysis, thermocouple zoning, and shrinkage mapping, YISHANG consistently delivers first-pass yields over 98%. That translates to fewer reworks and more accurate delivery forecasting.
In one UAV project, our client transitioned from machined titanium to MIM sintered frames and saved $88K annually—all while maintaining component performance.
Whether you’re managing alta injection molding Airdrie-type outputs or seeking to consolidate your vendor list, stable sintering enables smarter sourcing decisions.
Where Sintered MIM Parts Are Already Delivering Global Value
You’ll find sintered MIM parts powering modern product lines globally.
Sector | Component Types | Key Value for Buyers |
---|---|---|
Automotive | Lock barrels, fuel valve pins, cam shafts | Strength, automation-ready, durable |
Electronics | EMI shields, sensor holders, phone casings | Thin walls, tight tolerances, no polish |
Energy Storage | Battery connectors, housings, contact grids | High conductivity, light weight |
Medical | Orthodontic parts, implant frames, microtools | Biocompatibility, corrosion resistance |
These applications benefit from sintering’s dimensional consistency and ability to consolidate parts. Buyers reduce assembly time, improve product lifespan, and cut inventory SKUs.
This is why the advantages of injection moulding through MIM + sintering are most visible at scale—not just in lab tests.
FAQs: What Buyers Often Ask About Sintering in MIM
How does sintering affect MIM part tolerance?
Sintering causes predictable shrinkage—typically 15–20%—as metal particles bond and densify. At YISHANG, we use mold compensation algorithms and thermal simulations to manage shrinkage within ±0.3%, even on thin-walled or high-precision parts. This ensures your MIM components remain within tight tolerance windows, reducing the need for post-machining.
What atmosphere is best for sintering stainless steel parts?
Hydrogen and vacuum atmospheres are preferred. Hydrogen reduces oxides, ensuring better surface quality and grain bonding. YISHANG utilizes monitored hydrogen atmospheres for critical applications to achieve high-density, corrosion-resistant parts.
Can sintering help reduce total manufacturing cost?
Yes. Efficient sintering cuts down secondary processing, reduces tool wear, and minimizes energy cost per unit. It also increases consistency, lowering the risk of rejections and returns. For large-volume procurement, this offers measurable savings.
Final Thoughts: Why Smart Buyers Pay Attention to Sintering
For B2B buyers focused on performance, price stability, and delivery timelines, sintering matters. It reduces risk by anchoring part quality in a repeatable, controlled thermal process.
If you’re sourcing for applications of injection moulding beyond simple brackets—say, for automotive injection systems or miniaturized aluminum injection molding components—ask your supplier how they ensure consistency.
At YISHANG, sintering is where our precision promise becomes reality. We don’t just sell parts; we deliver process control that reduces your back-end risk.