Introduction: Why This Coating Choice Still Matters
For global buyers sourcing large volumes of metal parts, the coating isn’t just a detail—it’s a business-critical decision. Coatings like enamel paint influence product lifespan, cross-border compliance, and field-level maintenance. In competitive supply chains, finishing impacts both operational cost and perceived quality.
This guide focuses on how enamel paint compares in real-world B2B manufacturing, especially for OEM/ODM suppliers. You’ll gain clarity on its technical fit, lifecycle performance, and integration with modern fabrication lines—so your next procurement is faster, safer, and more strategic.
Enamel Paint Isn't Just Paint — It's a Performance Layer
Industrial-grade enamel is engineered to deliver durable performance on steel, aluminum, and galvanized parts. It cures into a hard, chemically resistant shell ideal for products exposed to handling, abrasion, and UV.
Unlike basic spray paint or powder paint used in decorative applications, enamel undergoes oxidative curing, forming a dense cross-linked layer. In comparative tests (ASTM D3363, ISO 2810), it consistently outperforms waterborne or acrylic coatings in gloss retention and scratch resistance.
Enamel-coated parts are less prone to damage during shipping, which reduces rework and warranty claims. For brands operating in high-mix, high-volume sectors—like retail kiosks or electrical panels—it provides aesthetic reliability and structural protection in one layer.
Where Enamel Paint Wins — And Where It Doesn’t
Enamel excels when the priority is durability and surface clarity over time. It performs well across painted and powder coating workflows, offering a more affordable alternative to powder coat over paint in some instances.
Industries such as energy, medical devices, and export machinery favor enamel for its predictable cost-per-cycle. Its film integrity supports field cleaning with alcohol-based agents and light mechanical contact.
However, in applications needing fast turnaround, flexible substrates, or powder coating over paint compatibility, buyers may prefer epoxy systems. Similarly, aluminum anodizing and painting plants may require hybrid solutions for conductivity or bonding layers.
At YISHANG, we assess your total supply chain rhythm—lead times, part complexity, and finishing stage—to ensure enamel fits without slowing your production.
The Hidden Battle: What Happens Before the Paint Hits the Metal
The best coatings fail without proper surface prep. Enamel requires a clean, abrasion-ready surface—especially for fasteners, chassis frames, or anodized aluminum paint applications.
At YISHANG, we meet SSPC-SP10 blast specs, achieving a 50–75μm anchor profile with automated media equipment. For high-volume runs, our teams validate salt levels (ISO 8502-6), primer adhesion, and DFT specs across samples.
Clients benefit from traceable QA documentation at every stage. This is key when exporting to regulated markets or when integrating with powder finish paint stages in hybrid finishing systems.
Application Isn’t Just Technique — It’s System Thinking
In OEM supply chains, application methods impact everything from throughput to warranty rates. Our automated enamel spray systems include inline DFT sensors, delivering consistent 50–80μm coatings across complex geometries.
We offer both ambient and oven-curing workflows. For example, in auto paint and fasteners, oven curing improves scratch resistance and bonding reliability.
B2B clients should avoid generalist finishing approaches. Ask about curing curves, coating flow rates, and compatibility with follow-up processes like laser marking or packaging.
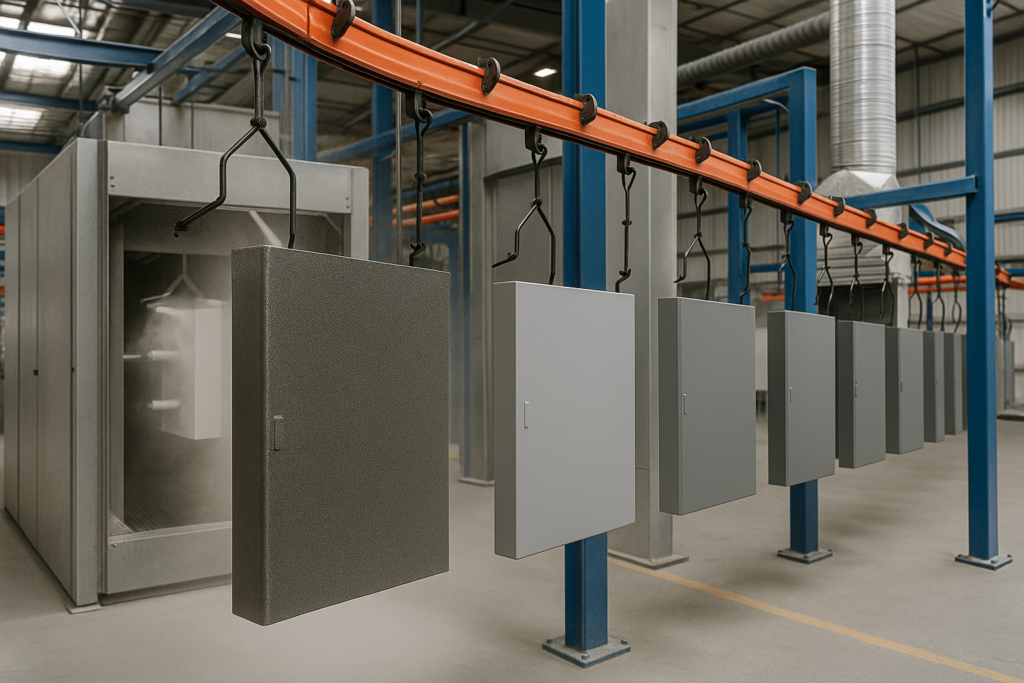
Metal Fabrication Use Cases: When Enamel Paint Makes the Most Sense
Enamel coatings are best suited to use cases where appearance, corrosion resistance, and field resilience must align with cost targets and procurement KPIs such as lower rejection rates, higher first-pass yield, and streamlined post-processing.
Export vending units: Exposed to weather and vandalism; enamel reduces visual wear and returns.
Battery control enclosures: Withstand humidity, dust, and thermal shifts while maintaining coating integrity.
Hospital furniture: Requires alcohol cleaning and long-term gloss retention, lowering maintenance cycles.
Enamel is often favored over spray paint over powder coated metal due to reduced failure risk and better cross-border compliance. For many buyers, it offers a cost-effective balance between longevity and finish clarity.
Application | Enamel Advantage | Buyer Impact |
---|---|---|
EV charge panels | High UV/gloss stability | Fewer field failures |
Industrial signage | Clean finish in large runs | Easier bulk QA |
Smart locker doors | Scratch-resistance in transit | Less repolishing, fewer claims |

From Spec Sheet to Shop Floor: How to Choose the Right Enamel Paint
Selecting the right enamel system means more than color matching. Wholesale buyers should factor in VOC compliance, shelf life, dry film hardness, and local regulations.
For example, we supply formulations compliant with RoHS, REACH, and Prop 65, suitable for both North American and EU distribution. Our team conducts comparative testing vs. powder coating systems or hybrid powder coat over paint processes when needed.
In some instances, enamel is also compared against anodized aluminum paint workflows where conductivity or layer thickness is a constraint. Our lab supports both destructive and non-destructive testing so your purchase decision is risk-checked.
Ask the Right Questions Before You Paint
Before selecting enamel paint for metal, ask:
What are the expected cleaning agents the part will contact?
Will there be heat exposure or friction in shipping?
Do parts need to match pre-anodized or powder coat finishes?
B2B sourcing teams often gain the most value by integrating coating logic early. At YISHANG, we collaborate during drawing reviews and part modeling to ensure your specification won’t fail in transit, assembly, or compliance.
FAQs: Enamel Paint for Metal in Procurement
Q1: Is enamel paint better than powder coating for metal parts?
A: It depends. Enamel paint offers better flexibility in touch-ups, gloss retention, and cost per part for medium volumes. Powder coating generally offers greater impact resistance but can be over-spec’d for indoor or aesthetic uses.
Q2: Can enamel be applied over powder coated metal?
A: Not directly. Unless the powder layer is stripped or specially pre-treated, adhesion will be compromised. We help assess feasibility during technical reviews.
Q3: What’s the best paint for galvanized metal?
A: Enamel works well with proper primer. YISHANG uses etch primers to ensure optimal bonding with galvanized substrates.
Q4: Does enamel paint require baking?
A: It depends on the formulation. We offer both air-dry and oven-cured systems based on your assembly line configuration.
Q5: Can you match enamel paint colors to RAL or Pantone?
A: Absolutely. We offer precise matching within Delta E<1.0 tolerances for high-consistency batches.
Conclusion: What Enamel Paint Tells Us About Smart Metal Finishing
Enamel is more than a topcoat—it’s a procurement decision that shapes lifecycle cost, logistics damage rate, and visual brand equity. Unlike decorative paints, it delivers technical consistency at a manageable price point.
Whether you’re integrating into powder-coating plants, aluminum anodizing workflows, or direct-to-assembly packaging, enamel offers scalable predictability. YISHANG helps you spec smarter, not just paint better.
Discuss your project specs with YISHANG. We help global buyers finish strong with tested, scalable enamel systems.