Why Material Choice Matters More Than Ever
For overseas procurement professionals, choosing the right material is not just a matter of cost—it’s a strategic decision that impacts production reliability, compliance, and long-term profitability. The global trend toward lightweight engineering, energy efficiency, and production scalability has made aluminum alloys an increasingly important part of procurement portfolios.
Among die-casting materials, ADC10 aluminum stands out for its balance between manufacturability, structural integrity, and cost control. For companies managing large-scale production with precision and consistency requirements, ADC10 offers more than acceptable performance—it provides proven process stability, global availability, and excellent integration into automated workflows.
At Yishang Metal Products Co., Ltd., we understand that procurement professionals are not just sourcing alloys—they’re sourcing reliability. That’s why we developed this article to support informed sourcing decisions by aligning technical insights with real-world manufacturing considerations.
Understanding ADC10 Aluminum from the Inside Out
ADC10 belongs to the Al-Si-Cu aluminum alloy family and is tailored for high-pressure die casting. Its standardized composition includes 7.5–9.5% silicon and 3.0–4.0% copper, with the remaining content primarily aluminum. Trace elements like zinc, magnesium, and iron further influence flow behavior and casting quality. The alloy’s formulation prioritizes dimensional stability, excellent flow in thin-wall molds, and minimal shrinkage during solidification.
Globally, ADC10 maps closely to A380 (ASTM), EN AC-46500, and JIS H5302. However, buyers should note that even small variances in iron or zinc levels can impact corrosion resistance or thermal stress tolerance. At Yishang, we conduct lot-to-lot chemical validation to maintain strict consistency for customers across the US, EU, and Southeast Asia.
ADC10’s Material Behavior in the Real World
From a mechanical standpoint, ADC10 offers dependable mid-range strength. Tensile values range from 195–317 MPa, with yield strength averaging around 159 MPa. This makes it ideal for brackets, covers, and enclosures that require structural rigidity without load-critical expectations. Elongation at 2.5% confirms its unsuitability for post-casting forming or impact-intensive applications.
Thermally, the alloy supports thermal conductivity values up to 109 W/m·K—a valuable feature for battery casings, LED lighting systems, and inverters. Its electrical resistivity (~0.00000264 ohm-cm) supports EMI shielding while remaining cost-efficient. These characteristics position ADC10 as a viable alternative to more expensive alloys in heat and signal management environments.
Property Type | Metric Value | Application Relevance |
---|---|---|
Tensile Strength | 195–317 MPa | Enclosures, covers, electronics frames |
Yield Strength | 159 MPa | Structural parts with static loads |
Elongation at Break | 2.5% | Limited post-cast flexibility |
Thermal Conductivity | 109 W/m·K | LED housings, power modules |
Electrical Resistivity | 0.00000264 ohm-cm | EMI shielding, electronics |
Fatigue Strength | 138 MPa | Medium-stress industrial parts |
Hardness | 80 HB | Machining stability, wear resistance |
At Yishang, we test each production batch for mechanical conformance to ensure consistent downstream performance, reducing requalification cycles for our OEM clients.
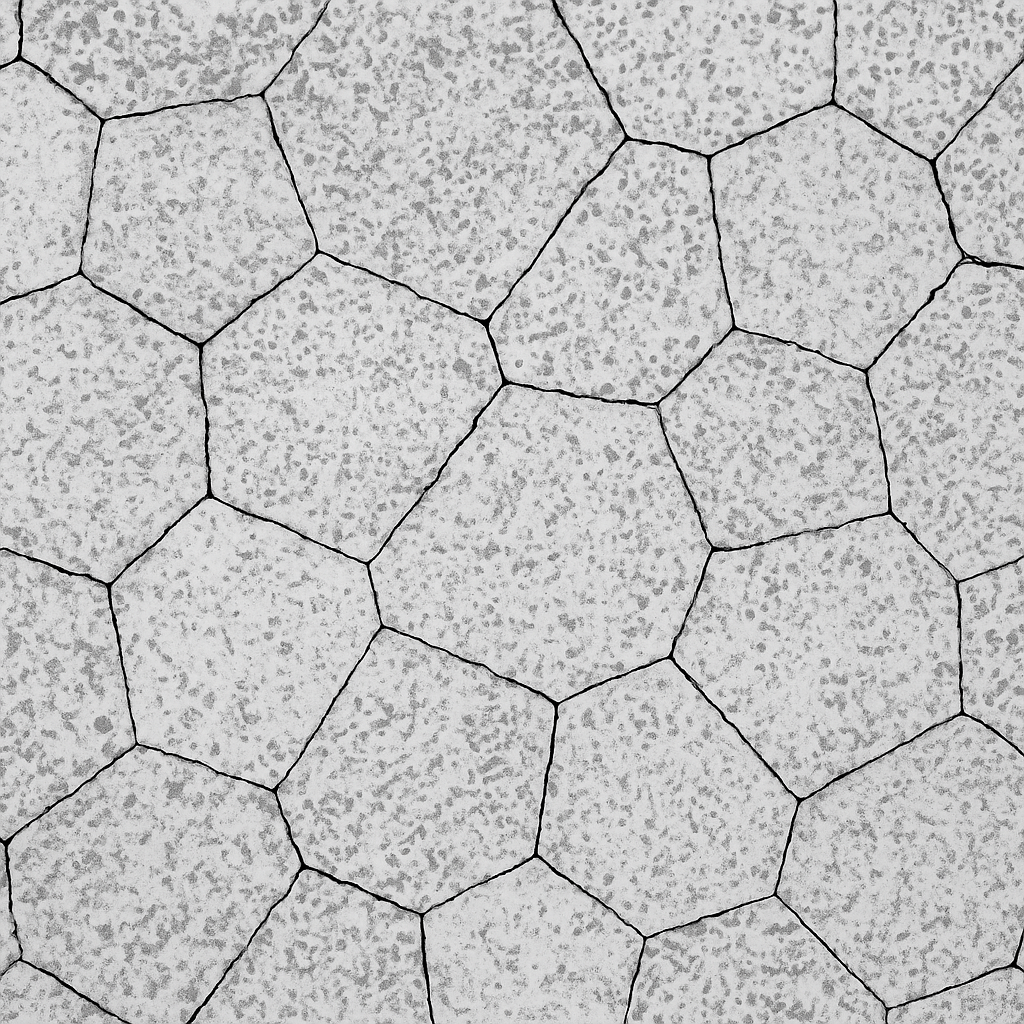
Processability in Mass Production
From a procurement and engineering standpoint, ADC10’s strongest feature is its processability. It casts cleanly, tolerates high-speed injection, and allows for tight part tolerances. Its melt range of 640–760°C and solidification behavior ensure lower porosity and better mold fill in complex geometries. This leads to fewer rejected parts, faster cycle times, and more predictable outcomes for production planning.
With machinability rated at 50%, ADC10 allows efficient secondary machining when supported by proper toolpath design and lubrication. At Yishang, we routinely achieve fine-thread tapping, hole accuracy of ±0.05 mm, and Ra 1.6 μm surface finishing for clients who require CNC post-processing. These are key benchmarks for international customers who rely on precision fits.
Anodizing ADC10 is less common due to its metallurgical composition, but e-coating, powder coating, and painting are reliable. At Yishang, we advise clients during DFM reviews on which coatings are most compatible, depending on end-use environmental exposure and assembly method.
Process Stage | Recommended Range |
Melt Temperature | 640–760°C |
Casting Temperature | 655–740°C |
Annealing Temperature | 260–271°C |
Aging Temperature | 177–260°C |
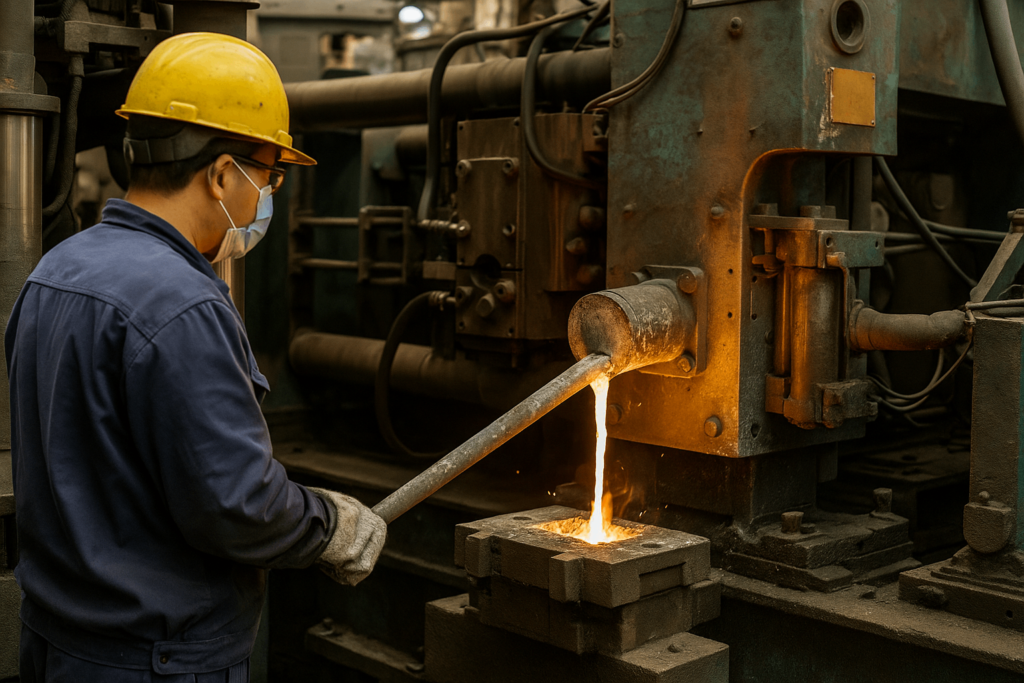
Application-Driven Choices for Global Buyers
Is ADC10 Better Than ADC12?
One of the most frequently asked questions by overseas buyers is how ADC10 compares to ADC12 in real-world use. While ADC12 offers slightly higher strength and improved pressure tightness, ADC10 surpasses it in terms of castability, flowability, and lower hot cracking risk. This makes ADC10 the preferred choice for thin-walled or complex components that demand high dimensional accuracy.
From a procurement standpoint, ADC10’s lower defect rates in production lead to reduced rework costs and improved supply chain predictability. For buyers concerned with tooling life and overall yield in high-volume production, ADC10 is typically the smarter option. That said, for parts with high structural load or heat exposure, ADC12 might remain more favorable depending on the design envelope.
ADC10 is the right choice when you need consistent production output, moderate structural integrity, and cost-effective processing. In automotive, it is used for non-load-bearing components like timing covers, sensor brackets, and structural shells.
In electronics, global customers source ADC10 for power inverter housings, LED modules, and battery casings. These parts benefit from the alloy’s blend of heat tolerance and dimensional accuracy. The alloy’s stability ensures minimal warping during mass production and allows for accurate assembly fits across large batches.
At Yishang, we supply ADC10 parts to clients in consumer electronics, medical devices, and outdoor enclosures. Because of our vertically integrated service—from die design to surface treatment—our overseas customers reduce lead time and avoid multi-supplier coordination headaches.
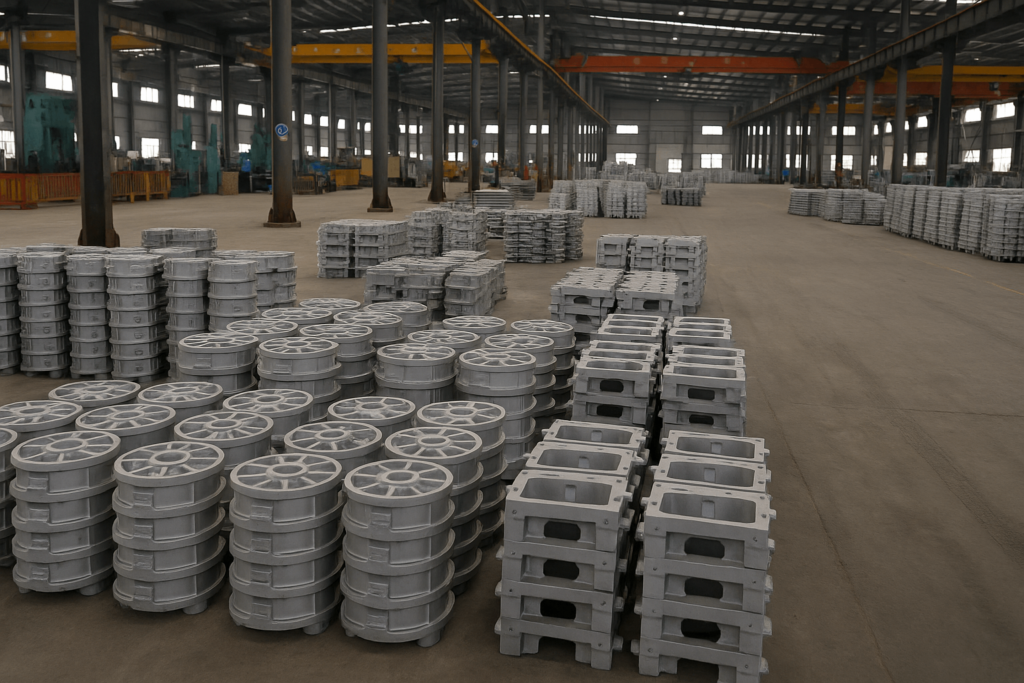
The Hidden Costs: When NOT to Use ADC10
Despite its versatility, ADC10 is not suitable for every use case. Its low ductility and fatigue resistance mean it should not be used in safety-critical or high-impact components. For example, we recommend alternatives like ADC6 or A356-T6 for suspension mounts, structural beams, or energy absorption parts.
Similarly, ADC10 is not weld-friendly. Due to silicon and copper content, weld zones often become brittle and susceptible to cracking. We guide our clients toward mechanical fastening or redesign strategies when post-cast joining is needed.
Lastly, exposure to corrosive or marine environments without coating can lead to premature degradation. We offer pre-coating and sealing services or recommend compatible anodized alternatives for such settings.
Market & Sustainability Perspectives
Sourcing ADC10 is straightforward due to its broad adoption across Asian and global foundries. It aligns well with international standards, allowing multinational procurement teams to scale production across sites. Its cost stability, compared to wrought aluminum, adds predictability to BOM planning.
From a sustainability lens, ADC10 is a strong performer. Recycled content ratios exceed 30% in our typical batches, and its low energy melting profile reduces overall emissions. Our ISO 9001 and RoHS certifications support traceability and compliance.
As an OEM-focused manufacturer, Yishang also offers PPAP, material certification reports, and compliance documentation tailored to each customer’s market (EU REACH, US Prop 65, etc.).
What You Can Expect from a Qualified ADC10 Supplier
Overseas buyers need more than a capable material—they need a partner that can turn specifications into scalable, repeatable outcomes. At Yishang, we offer tooling design consultations, rapid prototyping, and flexible MOQ support for pilot runs.
Case Example:
We’ve worked with procurement teams across five continents to supply millions of ADC10-based parts for EV systems, telecom hardware, and industrial automation. Our process expertise reduces scrap rates, stabilizes timelines, and simplifies cross-border logistics.
All shipments include dimensional inspection data, compliance certificates, and custom packaging options. Whether shipping 1,000 or 100,000 units, our QA team ensures consistency batch to batch.
Final Thoughts
ADC10 aluminum is not just another casting alloy—it’s a tested solution for international manufacturers seeking material consistency, manufacturing reliability, and cost control. It balances performance with process efficiency and supports scalable, repeatable production outcomes.
If your team is sourcing for consumer electronics, light automotive components, or commercial enclosures, ADC10 is worth strong consideration. And with Yishang Metal Products Co., Ltd. as your supplier, you gain not only a proven material, but a manufacturing partner fluent in the language of global production.
📩 Ready to evaluate ADC10 for your project? Send us your drawings or technical specifications, and our engineering team will respond within 24 hours with a custom quote and feasibility assessment.