Introduction
For global wholesalers and electrical sourcing teams, knowing whether to offer a breaker box or a fuse box isn’t just a technical comparison—it shapes catalog relevance, client safety, and future product line success. With infrastructure demands rising across housing, EV charging, and modular equipment systems, the right enclosure design can reduce downstream risk and drive purchasing decisions.
This article offers a practical, manufacturing-driven perspective for professionals navigating procurement and specification choices. Drawing from real-world applications, code requirements, and industry trends, YISHANG brings 26+ years of metal fabrication and enclosure integration experience to help B2B buyers align with market expectations. Whether you’re bidding on municipal projects or developing smart vending solutions, this guide delivers actionable clarity without overcomplicating the decision process.
1. System Fundamentals: How the Structure Informs Specification
In a fuse box, fault protection is achieved through a sacrificial component—the fuse—designed to melt under excess current. Once blown, it must be physically replaced. Breaker boxes use a switch mechanism that trips under overload and resets easily.
For industrial buyers, this difference has real implications. Breakers minimize downtime, reduce part replacement logistics, and allow technicians to diagnose and restore circuits quickly. Fuse-based systems require more inventory control and technician presence on-site, increasing post-sale support demands.
Breaker systems also allow modular expansion and smart integration. Most are DIN-rail mounted, supporting communication relays and digital load tracking. These features are critical when managing smart lockers, battery cabinets, or laser cut boxes designed for tech-driven environments.
Feature | Fuse Box | Breaker Box |
---|---|---|
Replacement | Required after each fault | Resettable switch |
Compliance Potential | Limited to legacy zones | Global code-ready |
Modularity | Fixed | Configurable & scalable |
Use in Smart Equipment | Rare | Common with PLC/IoT infrastructure |
These specs impact your client’s installation timelines, field service model, and long-term user satisfaction.
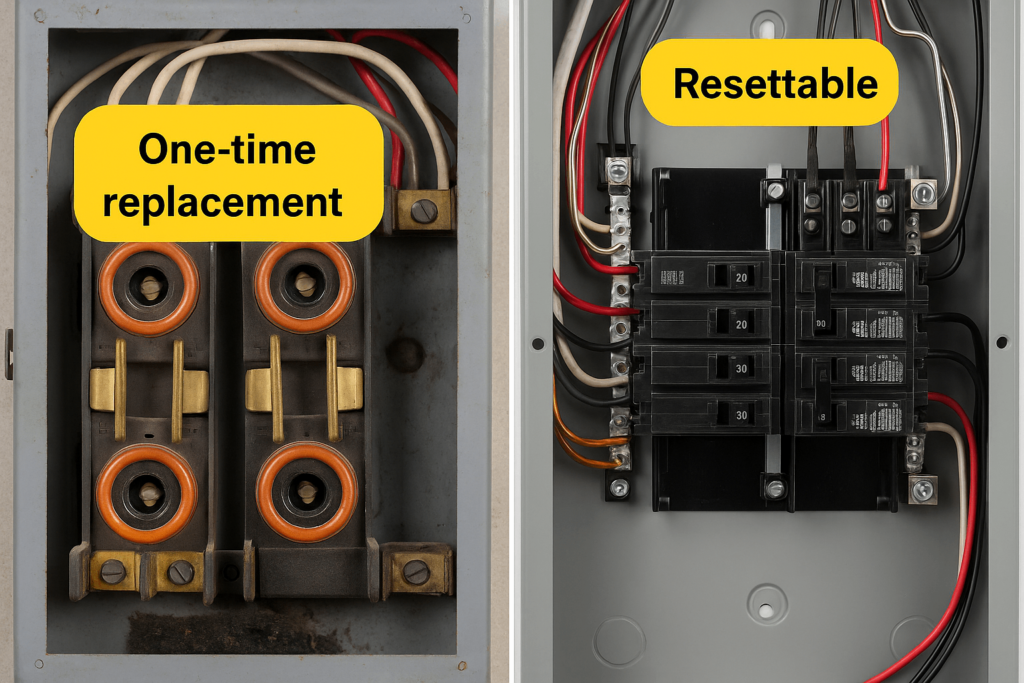
2. Compliance and Code Alignment: Mitigating Regulatory Bottlenecks
Procurement isn’t just about cost—it’s also about risk exposure. Regulatory frameworks like NEC, IEC, and UL are increasingly strict about electrical distribution safety. A fuse box might meet basic function, but lack AFCI/GFCI integration, surge protection compatibility, or fault reporting support.
Many institutional buyers (schools, hospitals, EV infrastructure) now reject bids with outdated electrical panels. UL 67 and IEC 61439 are just two of several panelboard standards breaker systems commonly meet. Fuse systems struggle to comply, even in jurisdictions with more lenient building codes.
From a wholesaler’s view, the last thing you want is inventory that fails inspection in key export regions. Your product catalog should help buyers clear safety reviews—not cause bid disqualification. Supplying breaker-ready enclosures improves pass rates, limits rework, and reduces shipping delays due to non-compliance.
In the insurance market, outdated systems may also result in higher premiums or coverage denials. For example, a 2022 US-based insurer survey revealed that 1 in 5 claims involving fire damage involved improperly rated or fused systems.
Compliance is no longer just about ticking boxes—it’s directly tied to sell-through velocity and after-sales performance.
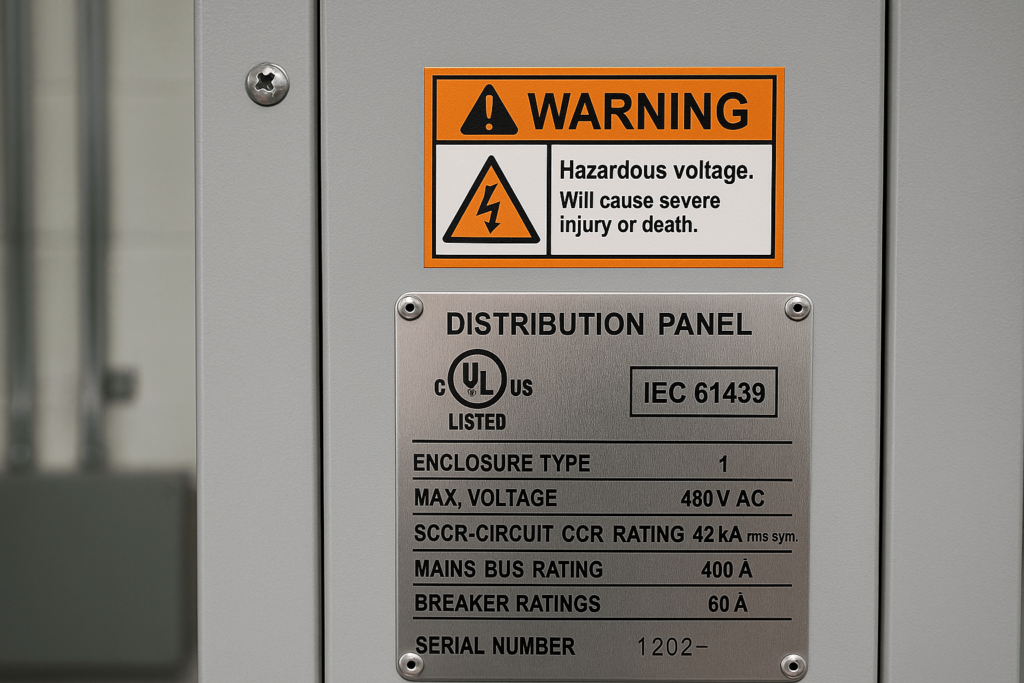
3. Market Fit: Matching the Panel to the Project Scale
Not every end customer needs a fully expandable breaker system. For low-load applications—like pop-up kiosks, rural monitoring stations, or micro-agriculture sites—a basic fuse system may suffice. These markets prioritize simplicity and cost per unit.
However, for most modern applications—multi-unit housing, telecom cabinets, laser cut enclosures with embedded logic—the electrical ecosystem demands more. Breakers support controlled expansion, solar-ready grid interfacing, and EV load balancing. A fuse box cannot.
As a B2B supplier, providing flexibility within your product line means serving both market ends. But overstocking outdated systems carries long-term risk. A buyer may accept a fuse panel today but come back next quarter with a demand for modular expandability, fault isolation, or smart interface wiring.
Providing only minimal-capacity enclosures leaves you underprepared. Align your panel offerings with real electrical use cases—not legacy defaults.
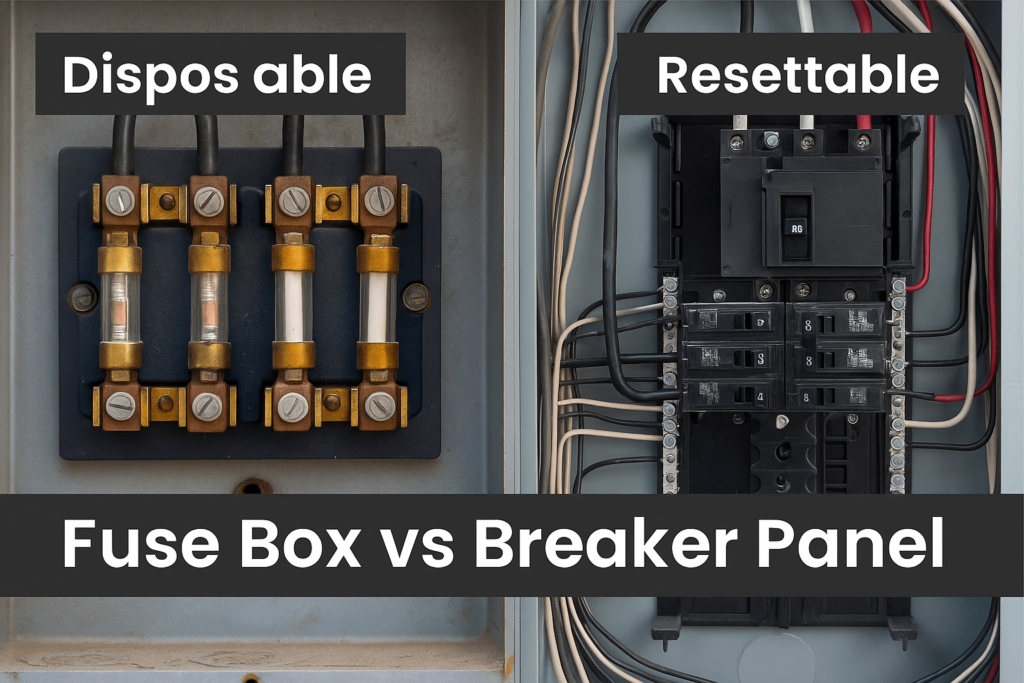
4. Financial Perspective: Upfront Cost vs Long-Term Payback
Breaker panels generally cost more upfront. But for procurement teams managing full project scopes or resale chains, the math changes quickly.
Installation Efficiency: Breakers simplify load grouping and minimize installation time.
Maintenance Savings: Fewer truck rolls, faster resets, and no need for consumables.
Compliance ROI: Pass inspections without delays or retrofits.
A 2023 case study in a European housing retrofit program showed that breaker-based distribution saved 18% in field service cost over two years, despite a 15% higher panel price.
As more markets adopt smart infrastructure (EV-ready housing, energy storage lockers, connected vending systems), a breaker-based enclosure becomes an enabler of value, not just a regulatory hurdle.
Fuse boxes may win budget-based bids, but for projects with lifecycle service contracts, client feedback loops, or compliance-linked incentives, their limitations cost more than they save.
5. OEM Manufacturing Perspective: System Efficiency Starts at the Panel
For OEMs, every design decision affects lead time, testing, and integration. Breaker systems offer standardization, faster wiring, and better fault protection alignment with intelligent devices. They reduce heat-related risk, simplify pre-assembly, and enable diagnostic feedback.
At YISHANG, we manufacture custom metal breaker enclosures for international brands in vending, energy, and industrial storage. Our boxes support breaker integration from leading brands (e.g., ABB, Eaton, Schneider), with layout precision for safe internal air clearance and cable management.
Key OEM applications include:
Application | System Challenge | Breaker Advantage |
EV Charging Cabinet | Variable load & power surge | Configurable breaker sizing |
Smart Locker | Fault isolation & quick recovery | Modular trip + reset |
Kiosk Panel | Component heat management | Breaker spacing + airflow support |
From laser cut boxes to CNC-fabricated shells, our enclosures meet IP and NEMA ratings, with optional grounding studs, gaskets, and mounting flanges. For procurement teams, this means less redesign and fewer surprises during installation or field deployment.
Conclusion: A Smarter Offer Drives Smarter Procurement
The breaker box vs fuse box debate isn’t just about choosing an electrical part—it’s about supplying a system your customer can count on.
As global codes evolve and smart systems become standard, your product line should reflect forward-compatibility, service efficiency, and safety assurance.
Fuse systems still have limited applications—but breaker enclosures dominate in terms of compliance, uptime, and commercial fit. When it’s your catalog on the line, future-ready is no longer optional.
Looking to standardize your breaker system sourcing with reliable OEM enclosures? Partner with YISHANG for engineered results and dependable global delivery.
Trusted by 50+ global OEM clients across energy, vending, and telecom sectors.