Why Bump Forming Is More Than Just a Bending Technique
In global sheet metal procurement, bump forming has become a preferred method for OEM and wholesale buyers seeking both precision and flexibility. This forming process, commonly referred to as step bending, enables manufacturers to produce large-radius curves without relying on costly custom dies.
Bump forming supports a variety of batch sizes, making it a strategic solution for buyers requiring custom specifications, low minimum order quantities (MOQs), and fast delivery. Rather than depending on large-volume roll forming or cast forming setups, bump forming—executed through CNC-controlled press brake forming—offers agility and cost-efficiency, particularly in custom sheet metal fabrication projects that need frequent design updates or market-driven adaptations.
At YISHANG, our bump forming capabilities are tailored for global delivery. As a China bump forming supplier, we offer RoHS-compliant, ISO 9001-certified production with full documentation, export-ready packaging, and forming steel sheet expertise—serving industries from electric mobility to architectural systems. This enables our clients to reduce procurement friction and minimize downstream modifications.
The Mechanics Behind Precision: How Bump Forming Really Works
Bump forming operates through a sequence of precisely programmed small-angle bends. These incremental bends gradually create a smooth curve without compromising structural integrity. CNC press brake forming plays a key role here, especially when consistent tolerances and geometric repeatability are critical for project success.
Using CAM tools, our team calculates spacing, angle increments, and force levels based on material behavior. Advanced clients often provide full 3D files, and we integrate these with our CAM workflow—what CAD full form implies in action. For more complex geometries, we also run finite element simulations to anticipate material springback and control stress distribution. This is essential when working with metals known for their ability to resist deformation, such as stainless steel or aluminum 6061.
To help reduce procurement friction, we guide buyers through these setup variables, ensuring the final part performs exactly as expected—minimizing surprises and secondary adjustments. For example, a 1000mm-wide aluminum sheet with a 600mm target radius might require 35–50 press hits depending on thickness and grade. That’s where experience and software-based simulation matter. Our accurate performance machining helps clients avoid secondary corrections, saving both time and money.
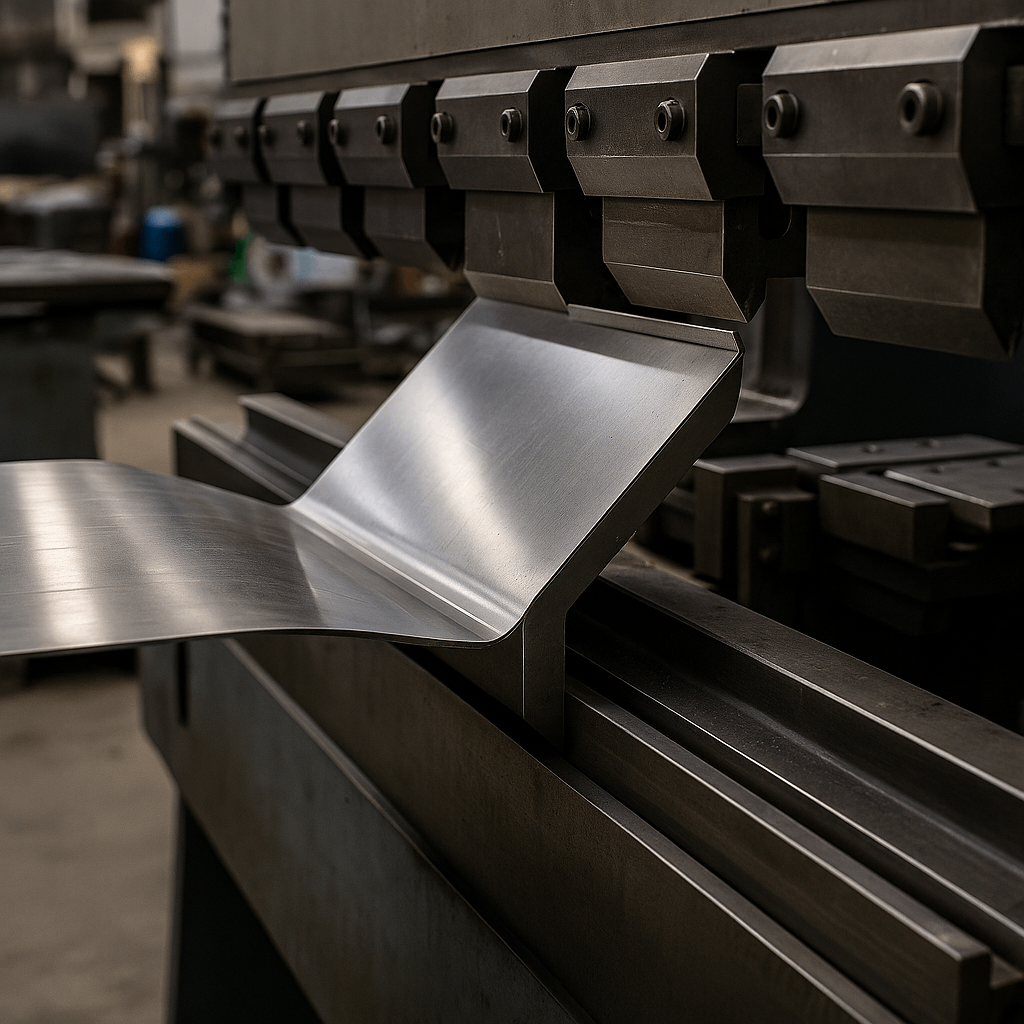
Designing with Geometry: Engineering for Efficiency and Accuracy
Procurement professionals often focus on pricing and timelines—but geometry defines feasibility. The ability to define consistent radii, minimize edge distortion, and align hole placement can significantly affect forming cost and speed.
Buyers can reduce rework and form error by providing uniform profile paths and eliminating tight, mixed-radius transitions in their design. YISHANG engineers assist in optimizing part geometry during quotation—delivering predictability for both the production team and procurement department.
We use predictive bend mapping to model forming complexity and quote accordingly. This eliminates hidden costs from overlooked geometrical variables, especially in complex parts like multi-bend enclosures or display housing components. That means fewer surprises for procurement teams aiming to meet internal cost and delivery KPIs.
Material Behavior and Forming Response: Matching Selection with Function
Material choice directly impacts formability, cost, and delivery timelines. For instance, aluminum 6061 is strong but has high springback, while 5052 offers better ductility. Galvanized steel forms well but may require protective die layers to avoid surface abrasion.
Here’s our reference matrix for common bump forming materials:
Material | Min. Radius (Rec.) | Hit Spacing (mm) | Springback Factor |
---|---|---|---|
SS 304 (2mm) | 3.0 x thickness | 8–12 | Moderate |
Aluminum 5052 | 2.5 x thickness | 6–10 | Low |
Aluminum 6061-T6 | 4.0 x thickness | 8–15 | High |
Galvanized Steel | 2.0 x thickness | 6–8 | Moderate |
All our forming tolerances follow DIN 6935 guidelines for sheet bending accuracy.
Procurement managers focused on accurate costing should factor in forming difficulty per metal type. For example, brass (noted for its strength and thermal conductivity) is used in some control panel covers but has chemical composition limitations that must be planned around.
As a leading OEM forming China partner, we guide buyers through material trade-offs to meet design intent while avoiding overengineering—reducing cost without sacrificing integrity.
Human + Machine: How Bump Forming Is Executed on the Shop Floor
Automated press brakes ensure accuracy, but expert interpretation ensures consistency. Operators at YISHANG monitor bending forming behavior in real time—adjusting parameters based on material behavior, humidity, and coating resistance.
Each job starts with a first-article inspection. We check CAD alignment, test material thickness, and run simulation-calibrated bends. Press forces and hit distances are adjusted dynamically as the job progresses.
Post-forming, our QA team verifies all parts using a three-point system:
Dimensional validation
Profile radius scan comparison
Surface quality and finish check
This process ensures compliance with client specs—critical for sensitive industries like medical devices or embedded electronic components.
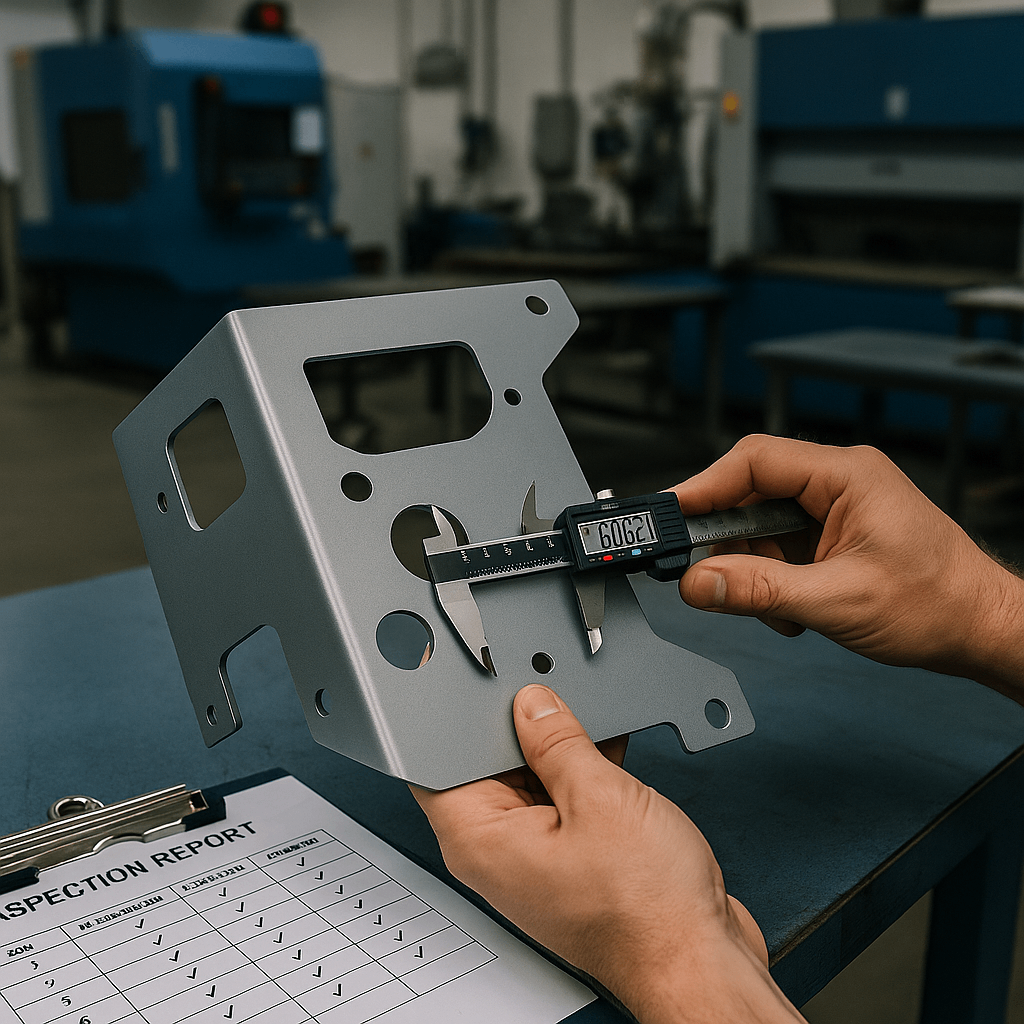
Real-World Value: Why Bump Forming Solves the Right Problems
Procurement is a balancing act: cost, lead time, consistency, and supplier reliability. Bump forming hits the sweet spot for small to mid-volume orders, product iteration cycles, or highly customized parts.
A European client needed a batch of curved aluminum sensor covers in under two weeks. Traditional tooling quotes exceeded $9,000. YISHANG’s CNC bump forming method completed the job with no tooling investment—and met all dimensional requirements.
Another client, a North American EV brand working with an automotive sheet metal supplier, ordered battery trays with long-radius bends. We delivered within a ±0.4mm tolerance using predictive hit mapping and 5052-grade aluminum. No secondary straightening was needed.
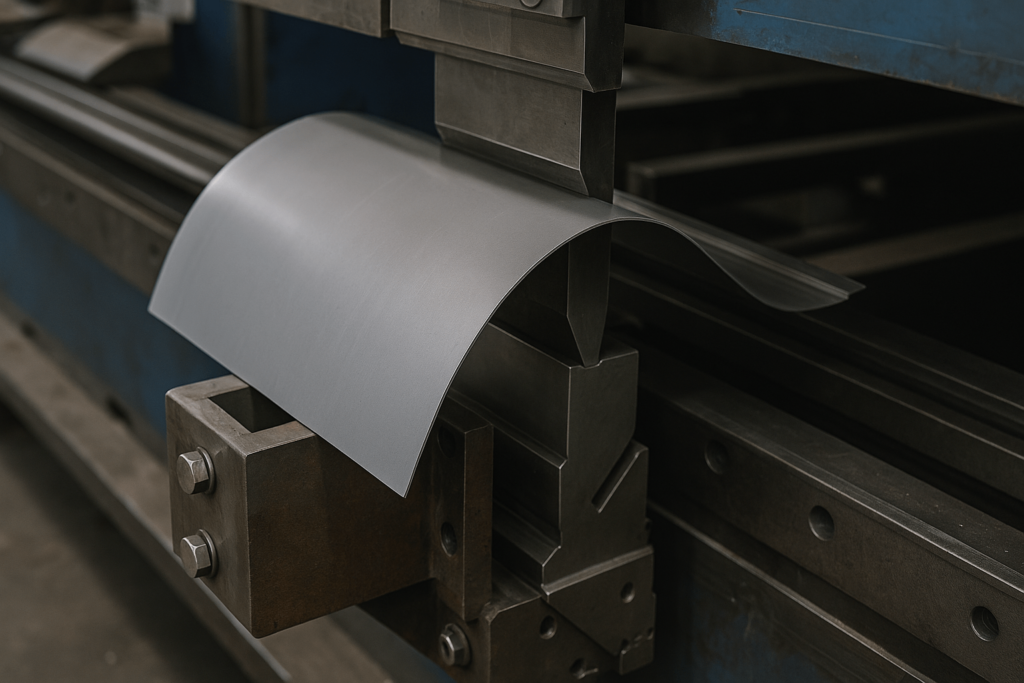
Bump Forming vs. Die Forming: Choosing the Right Tool for the Job
When lead times are tight and flexibility matters, bump forming offers critical advantages. Traditional die forming is cost-effective for static, high-volume orders—but unsuitable for markets with fast change cycles or multiple SKUs.
Use Case | Best Method |
High volume (10,000+ units) | Die forming |
Prototyping & pilot runs | Bump forming |
Frequent geometry changes | Bump forming |
Extremely tight tolerances | Die forming |
Regional test launches | Bump forming |
Cost Structure Comparison
Cost Factor | Bump Forming | Die Forming |
Tooling Cost | $0 | $8,000–$20,000 |
Prototyping Time | 2–5 days | 7–15 days |
Unit Cost | Moderate | Lower (in high volume) |
Design Flexibility | High | Low |
Change Cost | Low | High |
At YISHANG, we often help buyers blend both methods within a lifecycle strategy—starting with bump forming for early validation, then transitioning to dies once demand stabilizes. This hybrid approach supports both project velocity and budget clarity.
We benchmark against practices used by major suppliers such as Superior Metal Forming Inc., adapting them for SME-scale procurement flexibility.
Risks, Myths & Optimization Tips
Misunderstandings about bump forming can block adoption. Some assume it always leaves visible lines—yet our tooling can produce a nearly seamless arc with proper spacing and radius dies.
Others question consistency, but we routinely maintain ±0.5mm accuracy over multi-meter profiles. Smart forming paths and inspection automation minimize operator variability.
Procurement teams should:
Share CAD files early
Include surface finish expectations in the RFQ
Clarify part usage to help us recommend optimal forming methods
Grouping parts by radius/material also improves forming efficiency, especially for regional warehousing orders.
The Future of Bump Forming: Automation, Software, and AI
Bump forming is evolving fast. At YISHANG, we’re implementing visual inspection AI and smart gauge systems across our press brake lines.
Data from each job informs future setups—supporting predictive hit spacing, adaptive force tuning, and real-time QA flagging. This mirrors the lean systems seen in superior metal forming inc.-inspired plants, adapted for mid-volume global buyers.
Buyers can access digital project dashboards and multilingual communication support, giving full transparency into production status without delay.
What Buyers Need to Know
Typical lead time for prototypes: 5–7 days
MOQ: None (bump forming supports low-volume orders)
CAD compatibility: .STEP, .IGES, DXF supported
Compliance: RoHS / ISO 9001
Export experience: 50+ countries
First Article Inspection: Included by default
FAQ
Q: What materials are best suited for bump forming?
A: Stainless 304, aluminum 5052, and mild steel are most common. We support materials from 0.8mm to 4mm thickness.
Q: How do I send drawings for a bump forming quote?
A: Please submit .STEP or .IGES CAD files via our inquiry form. If needed, our team can assist with file conversion.
When Bump Forming Aligns with Your Procurement Strategy
Bump forming is ideal for metal component prototyping, especially for low-volume custom sheet metal projects where traditional tooling costs are a barrier. As a trusted partner in custom sheet metal fabrication, YISHANG delivers scalable flexibility and technical insight buyers can rely on.
Let’s collaborate on your next metal forming project. Reach out to YISHANG to get started.