This guide is tailored for global OEM procurement teams, mechanical system integrators, and sourcing specialists evaluating clevis fasteners for high-reliability applications.
👉 Need fast turnarounds for EV parts? Looking for clevis pins under 0.1 mm tolerance? You’re in the right place.
Introduction: When a Small Part Brings a Big System Down
If you’re sourcing clevis fasteners for automotive fastener kits, actuator assemblies, or industrial robotics, you’re not just buying parts—you’re managing system risk.
While larger structural elements grab attention, it is fasteners—especially clevis fasteners—that silently uphold system performance. A single failure here can trigger machine downtime, quality issues, or even customer dissatisfaction.
Whether used in auto panel fasteners or actuator linkages, clevis systems play a quiet but mission-critical role. These aren’t just pins and holes. They are engineered interfaces requiring tolerance control, load mapping, and smart material selection.
At YISHANG, we design and manufacture clevis fasteners for OEM and industrial customers in over 50 global markets. With 26+ years in automotive fasteners and mechanical assemblies, we’ve supported over 120 OEM procurement projects involving clevis or linkage fastener systems.
Over the past decade, one client in Poland integrated our clevises into their robotic assembly line across 4 production plants—reducing downtime and improving retention reliability.
We support purchasing teams handling mid-to-high volume fastener projects across North America, Southeast Asia, and Europe. From MOQ-based prototypes to full-scale certified runs, we deliver to your specs, timelines, and quality standards.
Clevis Fasteners and the Mechanics of Structural Trust
Clevis fasteners typically include a U-shaped yoke, a clevis pin, and a retention clip or cotter pin. The assembly allows controlled pivoting, essential for systems requiring both strength and movement.
Their relevance extends across high-load environments—agricultural equipment, auto fastener systems, robotic actuators—where angular tolerance and easy maintenance matter.
For automotive fastener system designers, the ability to allow controlled movement without loss of structural alignment makes clevises valuable.
📌 Key takeaway: Clevis fasteners combine movement flexibility with mechanical integrity—ideal for pivoting or misaligned load paths.
Additionally, clevis fasteners are often part of broader auto fastener kits used by manufacturers and panel builders. Their modularity reduces replacement time and improves serviceability in volume production environments.
Avoid Costly Mistakes: How the Right Clevis Prevents Warranty Claims and Downtime
If you’ve ever dealt with clevis pins loosening post-deployment or premature ovalization at pin holes, you know the cost of underspecifying these fasteners.
Load Direction Ignored
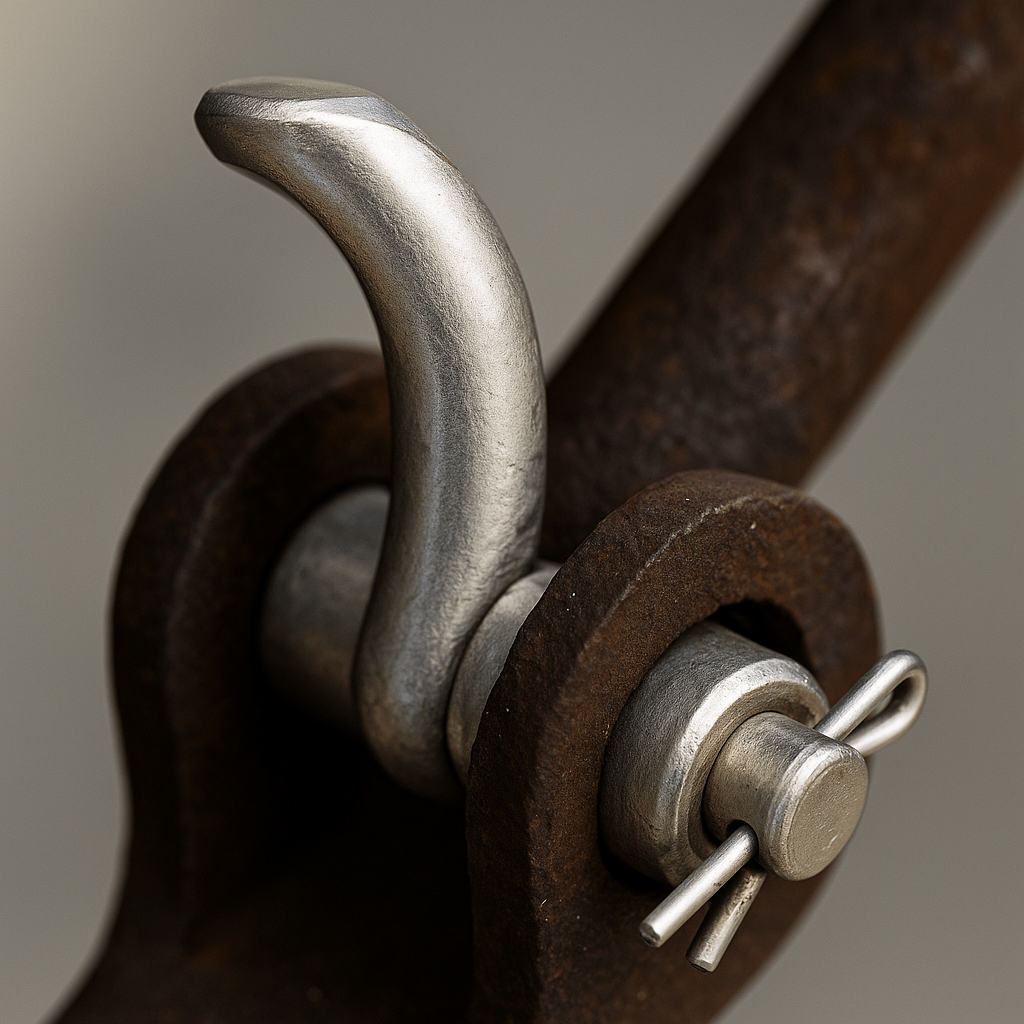
Clevises designed for axial loads fail quickly under lateral forces. For example, one automotive fasteners manufacturer reported pin distortion in their steering linkage due to incorrect load vector assumptions.
📌 Key takeaway: Always match clevis geometry to load path—axial, bending, or combined. Misalignment invites fatigue.
Incorrect Steel Grade
304 stainless may resist indoor corrosion but lacks chloride resilience. For outdoor and marine systems—like auto paint and fasteners exposed to salt fog—316 stainless is a must.
📌 Key takeaway: Use 316SS for high-salt environments to prevent warranty issues and reduce inspection cycles.
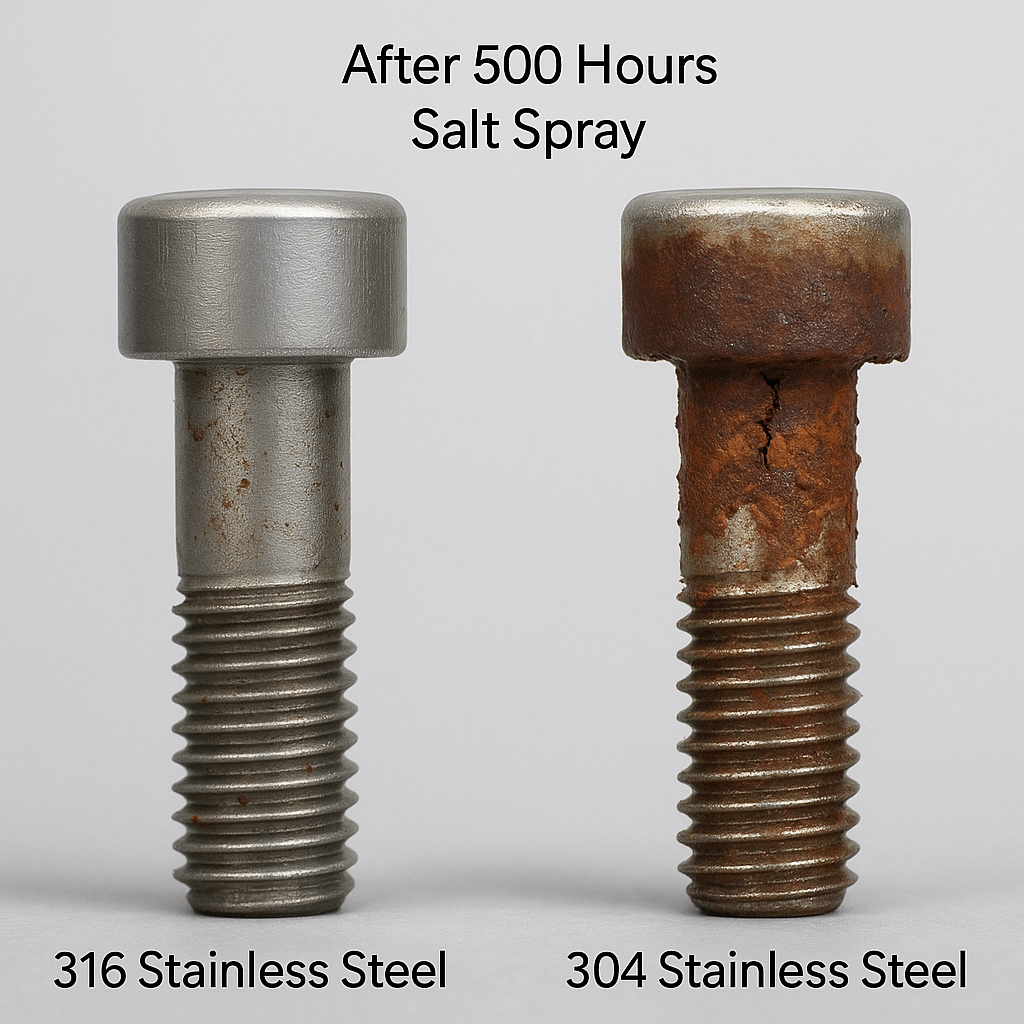
Loose Fit or Poor Tolerance
Tolerances for clevis pins should be matched to ISO or DIN standards. We often recommend 0.1–0.2 mm clearance in most automotive fastener applications, verified through GO/NO-GO gauging.
Locking Failures Under Vibration
We supply cotter-pinned or lockwired clevises for conveyor systems, hydraulic arms, or auto body fastener kits operating under repeat shock conditions.
Sourcing Custom Clevis Pins for Automotive Assembly Systems
Not every supplier understands the nuances of sourcing clevises for dynamic automotive environments. Here’s how to align specifications with purchasing priorities:
Define max axial and shear loads
Identify vibration cycle expectations
Match material grade to corrosion exposure
Specify tolerances on pin fit and yoke gap
Choose retention systems that match service intervals
📌 Key takeaway: A clevis isn’t just a component—it’s an interface between mechanical logic and system serviceability.
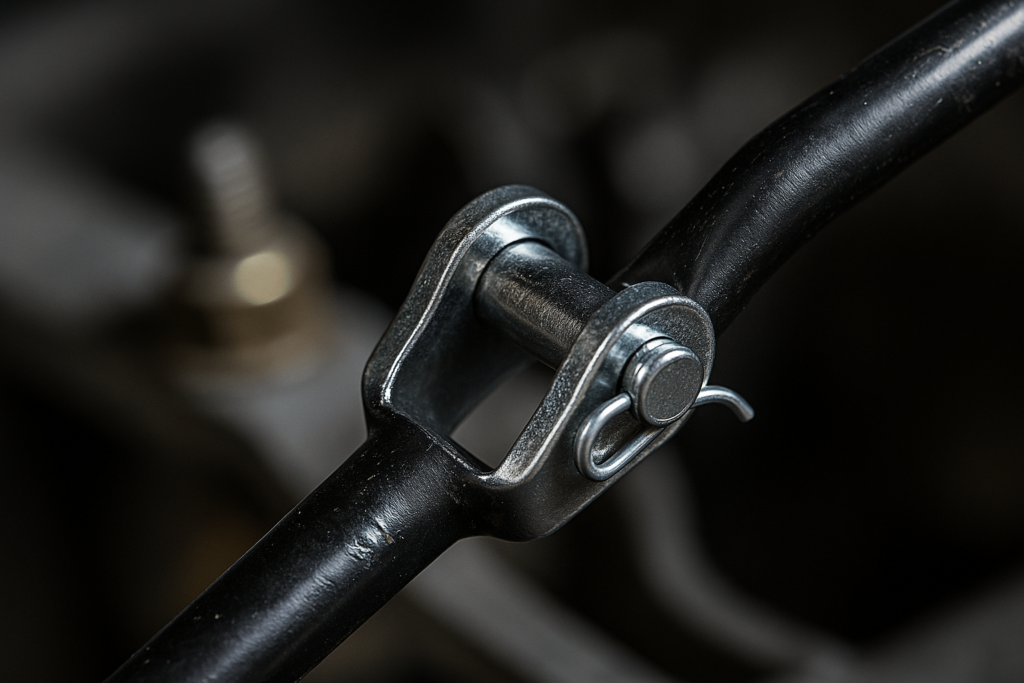
✅ Yishang Clevis Fastener Capabilities Summary
Item | Details |
---|---|
Customization | OEM & ODM from CAD / BOM / samples |
Material Options | SS304, SS316, Galvanized Steel, Alloy Steel |
Production Capacity | 100,000+ pcs/year |
MOQ | As low as 500 pcs depending on complexity |
Certifications | ISO 9001, RoHS |
Lead Time | 7–21 days based on batch & process |
Application Expertise | Automotive, Industrial Machinery, Robotics, Energy |
All clevis fasteners are batch-tested and traceable under our in-house QA protocols.
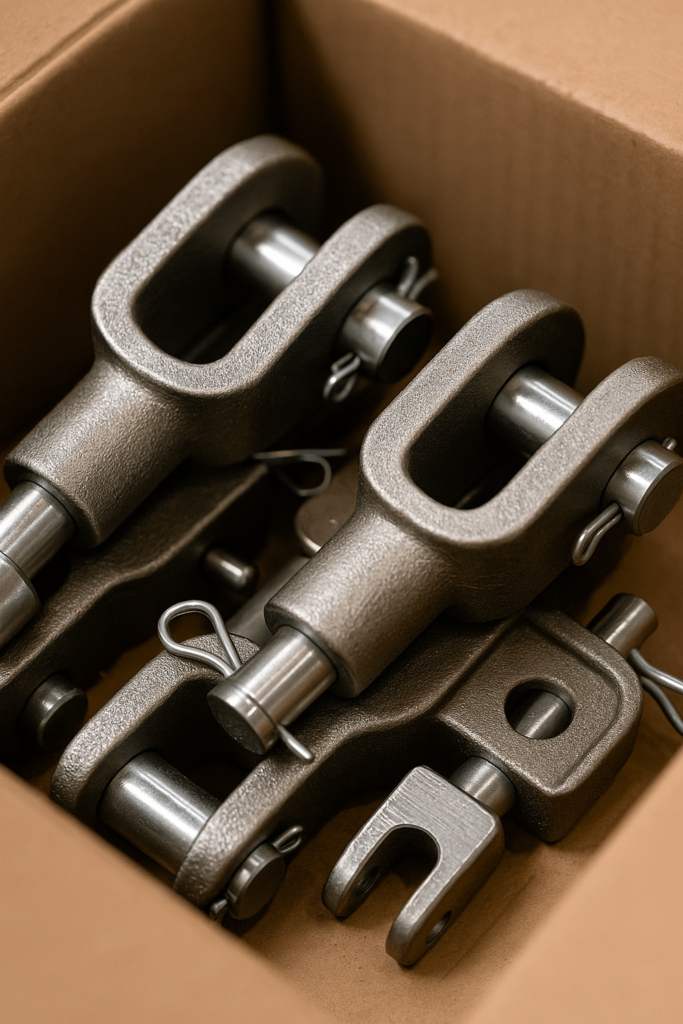
What to Ask Your Clevis Fastener Supplier Before Mass Orders
Before committing to a production batch, procurement specialists should confirm:
Does the supplier provide traceability reports and batch test data?
Can they produce both threaded and unthreaded clevis pins?
What’s the longest clevis pin they’ve produced under 0.05 mm tolerance?
What certifications back their heat treatment or coating processes?
📌 Key takeaway: The right supplier prevents production delays, rework costs, and late-stage field failures.
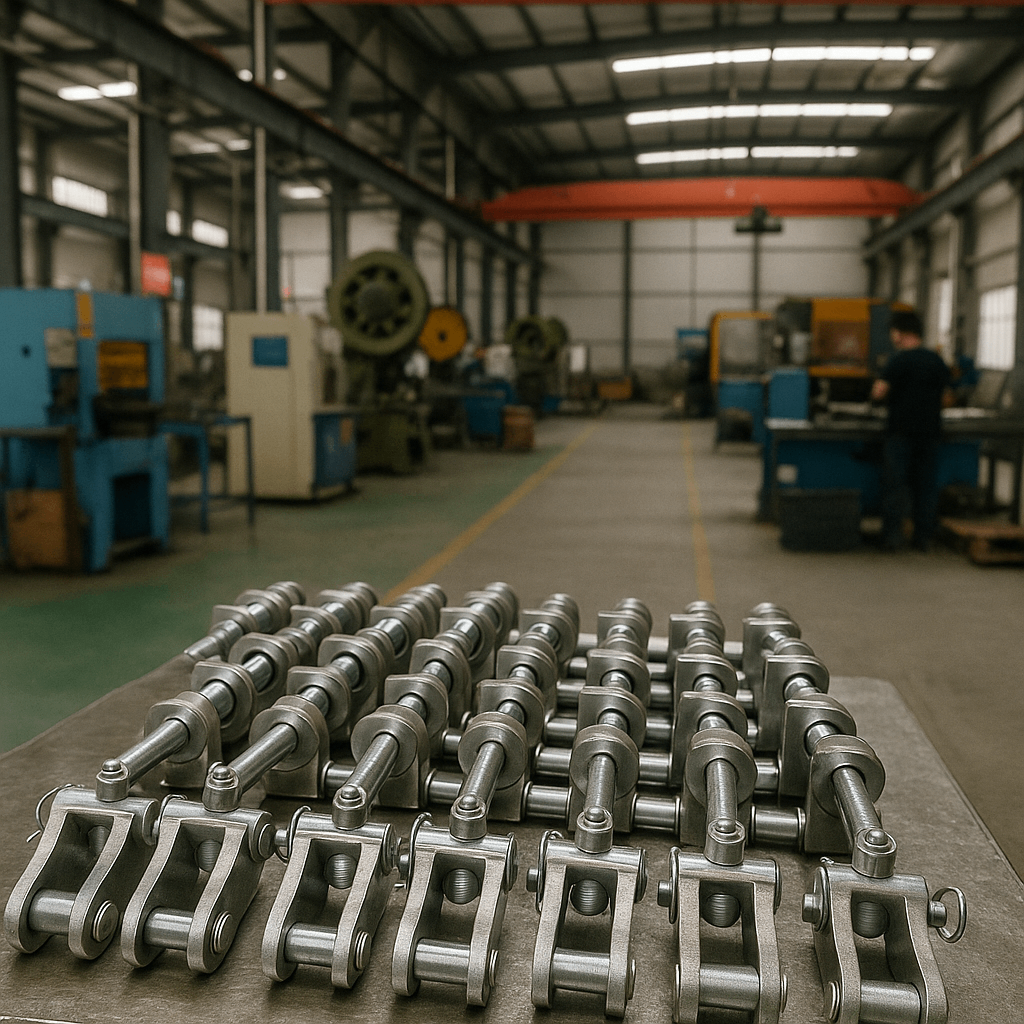
Send your clevis fastener drawings to YISHANG—we’ll review and quote fast, with the engineering support your supply chain needs.