Introduction – The Overlooked Power of Detail
In global sourcing for architectural and industrial applications, cove moulding rarely gets the attention it deserves. Yet for procurement professionals, especially those managing OEM and ODM production, this component affects everything from assembly precision to brand finish consistency.
At YISHANG, we’ve worked with buyers across 50+ countries who require scalable, reliable, and precision-fabricated cove moulding solutions. This article provides actionable insights—not decorative explanations—about what cove moulding can do in real production environments, how to select the right materials, and how to avoid common pitfalls in supplier engagement.
Cove Moulding’s Functionality in Industrial and OEM Applications
Cove moulding serves as a transitional interface, smoothing structural joints while reinforcing panel assemblies. For OEM clients, this means fewer visible gaps, improved vibration control, and a sleeker, brand-aligned product finish.
When applied in stainless steel cleanroom equipment, it eliminates tight angles where contaminants can collect—making sanitation more efficient. When used in aluminum vending machines or kiosks, it protects external corners and improves internal assembly tolerance.
One EU-based vending machine OEM reduced their enclosure assembly time by 23% using YISHANG’s custom aluminum moulding. The enhanced edge fit also minimized post-assembly adjustments. This kind of improvement isn’t aesthetic—it’s operational.
Lighting manufacturers also use cove mouldings to integrate indirect LEDs without visible fasteners. The trims serve double duty: as visual accents and functional thermal barriers. In display cases and POS terminals, the profile helps redirect light and maintain structural integrity.
Choosing the Right Material: Beyond Aluminum vs. Steel
Aluminum Moulding for Adaptability and Weight Reduction
Aluminum remains the first choice in many OEM programs due to its strength-to-weight ratio. It also supports a materials capability of being moulded into precise curves and angles.
YISHANG offers aluminum profiles in wall thicknesses from 0.8–2.0mm. These can be brushed, powder-coated (RAL-matched), or anodized. Whether you’re working on lighting systems, display cabinets, or aluminium injection moulding components, we support your required finish and tolerance.
The benefits of injection moulding don’t apply directly to metal forming, but many of the same logic paths—tooling control, repeatability, and cycle speed—exist in CNC and die-formed cove profiles.
Stainless Steel: Sanitation and Impact Resistance
304 and 316 stainless are ideal for environments demanding hygiene or abrasion resistance. Think public restrooms, food-service counters, and laboratory benches.
Our profiles meet RoHS and ISO 9001 requirements, and we perform salt spray or passivation tests upon request. We also help clients compare aluminum mould vs. stainless alternatives to meet both regulatory and performance specs.
Specialty Metals: Brass & Copper
Luxury environments occasionally call for brass or copper trims. While more niche, these materials offer lasting finish and character. They’re especially useful in boutique hotel lobbies or art galleries where aesthetics weigh equally with durability.
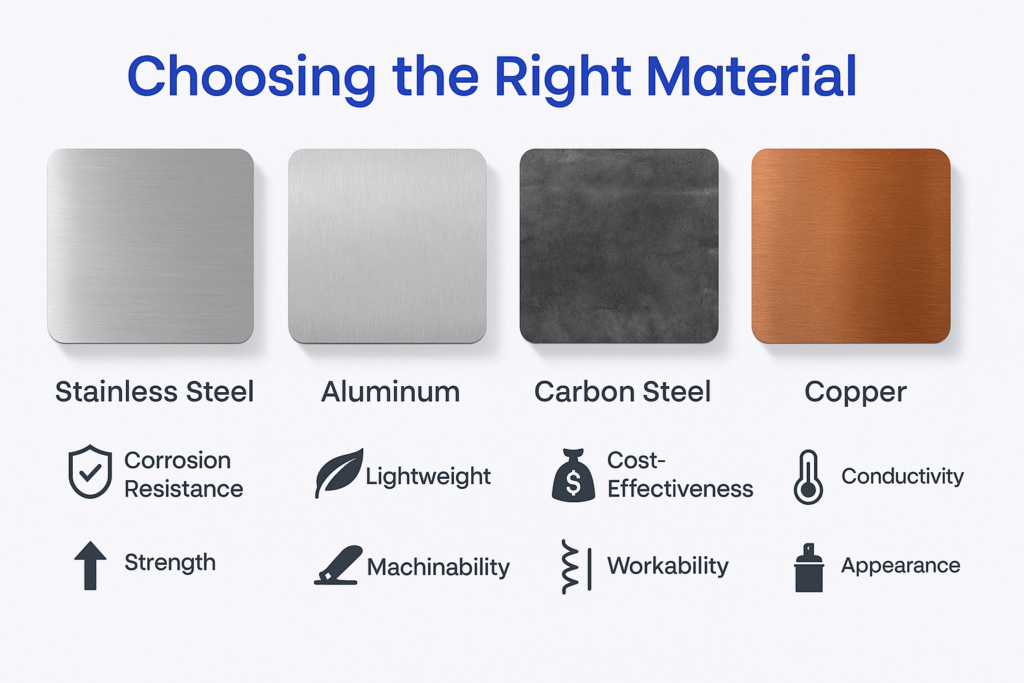
Real Applications: Where Buyers Gain Operational Value
Enclosures & Cabinets
For buyers sourcing metal trim for equipment housings—be it battery modules, telecom cabinets, or server racks—the use of precision-matched cove moulding means fewer gaps, fewer fasteners, and lower installation variability.
YISHANG recently supplied powder-coated aluminum mouldings to a U.S. retail systems integrator. The client deployed 1,200+ POS units using our profiles, achieving consistent build quality across locations.
Cleanroom & Medical Equipment
Stainless steel mouldings ensure compliance with ISO 14644 and FDA sanitation expectations. Cove trims reduce cleaning time and eliminate dirt traps at structural joints.
In one U.K. biosafety lab project, YISHANG supplied Ra ≤ 0.8 µm stainless profiles that supported both functional sealing and visual consistency across 75 lab cabinets.
Lighting & Display Fixtures
LED lighting troughs, ceiling reveals, and exhibition displays often integrate custom aluminium moulds that combine function and design. Our profiles are engineered with heat dissipation channels and optional tool-free covers for maintenance.
Applications of injection moulding typically involve thermoplastics, but aluminum forming allows us to mimic those advantages in terms of design complexity and modularity.
Manufacturing Process: From Engineering to Export
Design & DFM
We review STEP, DWG, and DXF files. If you’re reverse-engineering a legacy product, we offer sample-based duplication. Our DFM team ensures:
Proper bend radius and angle tolerance
Consistency in anodizing or powder layers
Profile match to adjacent components (±0.2 mm)
Fabrication Workflows
Stage | Precision | Notes |
---|---|---|
CNC Cutting | ±0.1 mm | Aluminum and stainless sheets |
Bending | ±0.5° | Consistent for 1,000+ units |
Welding/Slotting | As needed | For corner integration |
Finishing | Custom | Ra ≤ 1.6 µm standard, others on request |
Our CNC lines replicate precise geometry across batches, supporting aluminum moulding in modular production lines.
QA and Surface Finishing
Whether you require brushed aluminum, mirror-polished stainless, or matte black powder finishes, we provide:
Surface test reports
Thickness & adhesion confirmation (ASTM D3359)
Corrosion performance certificates
We also offer laser etching or barcode tracking upon request.
Packaging & Lead Time
Foam wrap + carton box + moisture protection
Palletized or loose-packed by request
Sample: 5–7 days | Production: 15–25 days (depending on volume)
All exports ship with HS code, COO, and RoHS documentation. We support DDP for clients in the US/EU to simplify customs clearance.
Procurement Considerations: What Global Buyers Should Evaluate
Total Cost vs. Piece Price
An OEM buyer knows the piece price is only part of the story. Consider:
Installation time (fast-fit profiles vs. traditional mount)
Fit accuracy (reduced rework)
Packaging density (cartonized vs. bundled)
Even a $0.30 increase in part cost can result in labor or logistics savings 2–3x higher.
MOQ and Supply Flexibility
Parameter | Detail |
MOQ | 300 pcs (custom profiles) |
Repeat Orders | Color, radius, length variants supported |
Warehousing | Available for staged delivery |
Lead Time | Samples: 5–7 days; Production: 15–25 days |
Logistics | FOB Shenzhen / CIF preferred port / DDP for US/EU |
ERP Tracking | Full batch traceability and production status updates |
Global distributors value our stable delivery timelines and flexible order structures, especially when aligning with multi-phase project rollouts.
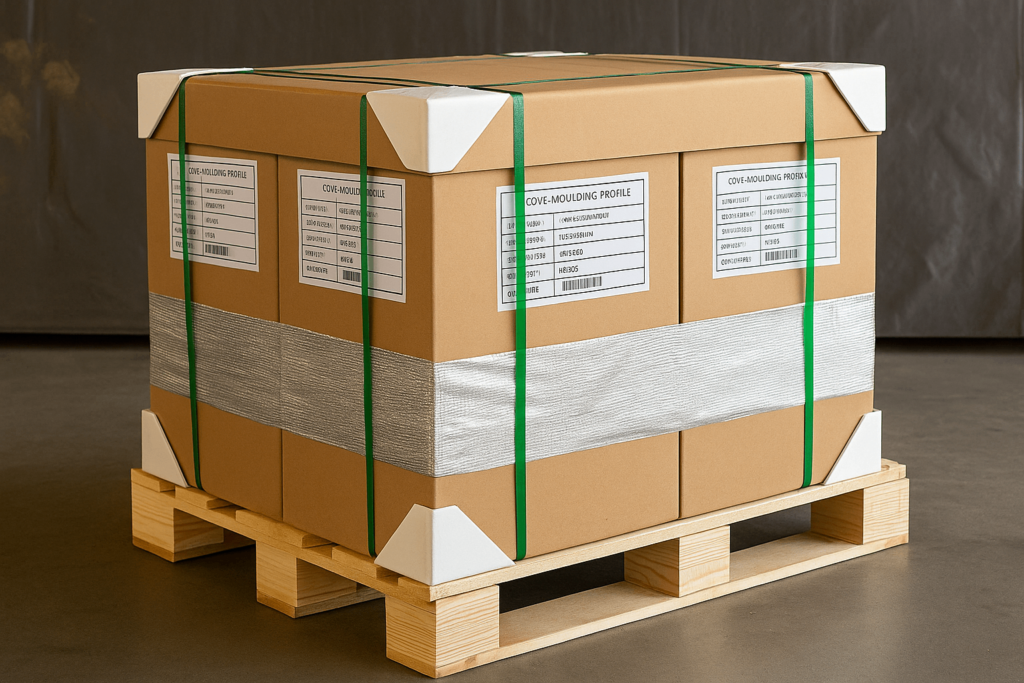
Drawing Quality & Spec Communication
Time is lost when specs are unclear. Please include:
Profile views with radius/angle specs
Material and finish codes (e.g., RAL 9016, SUS 304)
Quantity forecast and shipment mode
We can provide 2D confirmation drawings within 24–48 hours after inquiry.
Global Reach & Industry Impact
YISHANG has delivered custom moulding solutions to clients in over 50 countries, including the United States, Germany, Australia, the UAE, and South Korea. Our solutions have been widely adopted in industries such as:
Vending & Smart Retail Systems
Medical Equipment Manufacturing
LED Lighting Fixtures
Storage & Energy Systems
Architectural Interiors
We support both established multinational brands and regional equipment distributors with flexible procurement models, multilingual support, and technical co-development.
Quick Questions Buyers Often Ask
Q: What’s your typical lead time for custom cove moulding?
A: 5–7 days for samples, 15–25 days for mass production. Rush orders possible for repeat clients.
Q: What’s your MOQ for custom aluminium moulding?
A: 300 pieces per profile, with repeat flexibility for color or radius variants.
Q: Can I send a physical sample if I don’t have a CAD file?
A: Yes. We offer reverse engineering and 2D confirmation drawings within 48 hours.
Q: Which certifications do you support?
A: All materials are RoHS-compliant. Our facility is ISO 9001:2015 certified. Test reports can be included with each shipment.
Q: Can you help reduce my installation time?
A: Yes. Our DFM review focuses on bend tolerance, radius match, and tool-free assembly options to save time on site.
Conclusion
Cove moulding may seem minor, but for procurement professionals managing enclosure assembly or fixture consistency, it plays a strategic role. The right material and profile reduce rework, elevate product finish, and accelerate installs across thousands of units.
At YISHANG, we provide engineered cove moulding built around your product—backed by international standards, 26+ years of experience, and export to over 50 countries. From aluminum injection moulding components to stainless trims for medical use, we deliver results that scale.