Introduction
In industrial production, knurled textures aren’t just cosmetic—they are engineered features that directly impact product reliability and user functionality. For procurement teams sourcing large volumes of mechanical components, understanding knurling isn’t just technical—it’s commercial.
This article explains how knurling contributes to efficient mass production, superior component performance, and lower downstream failure rates. Whether you’re a purchasing manager evaluating a new supplier or coordinating RFQs across categories, the goal is the same: source functional, high-quality components with confidence.
Over the past two decades, we’ve helped hundreds of overseas buyers reduce production risks through consistent knurling performance. YISHANG, with over 26 years in precision metal manufacturing, supports B2B buyers worldwide with custom knurled parts designed for performance, compatibility, and cost-effectiveness.
What Is Knurling, Really?
Knurling is a machining process that produces patterned ridges on metal surfaces. These patterns—typically diamond, straight, or helical—enhance grip, enable mechanical mating, and improve tactile control.
In procurement contexts, knurling adds tangible value. It minimizes assembly slippage, improves torque performance, and helps meet ergonomic standards. More importantly, it ensures components perform consistently across thousands of units in production environments.
This process is carried out using specialized tools on a lathe. Depending on design and function, engineers select the right knurling type and pitch to meet grip requirements, visual specifications, or interference fit tolerances. It’s a functional feature—not a surface embellishment.
In real terms, a well-knurled shaft can eliminate the need for secondary adhesives in press-fit assemblies. That means faster production and fewer quality issues—key concerns for procurement teams balancing unit cost and throughput.
How Knurling Works: Materials, Methods & Mechanics
Materials Suitable for Knurling
Buyers sourcing large quantities of knurled components need assurance that suppliers are matching materials to process appropriately. Knurling results depend heavily on metal ductility and grain structure.
Table 1: Knurling-Compatible Materials
Material | Recommended Method | Common Use Cases |
---|---|---|
Aluminum | Form Knurling | Lightweight handles, electronics |
Stainless Steel | Cut Knurling | Medical instruments, food-grade hardware |
Brass/Copper | Form Knurling | Decorative mechanical components |
Mild Steel | Either | Automotive parts, tool shafts |
Using the wrong combination leads to uneven patterns, cracks, or premature tool wear—all of which compromise consistency across large orders. YISHANG uses internal material checklists and test runs to validate matchups before entering full production.
Methods: Forming vs. Cutting
There are two industry-standard techniques:
Form Knurling displaces metal into patterns without removing material. It’s efficient for softer metals and high-speed production.
Cut Knurling shaves material using sharp-edge tools. It’s suitable for harder materials and applications requiring clean finishes.
Each method has unique implications for tooling, feed rate, and dimensional tolerance. Buyers should confirm with suppliers which method is used, especially for critical parts like knobs, connectors, or torque-transfer components.
YISHANG supports both processes, using CNC programming to ensure pattern consistency even across thousands of units.
Patterns with Purpose: Functional Knurling Designs
Pattern type directly correlates to functionality. For global buyers issuing technical specifications, pattern clarity is essential.
Diamond Knurling maximizes grip in multiple directions. Ideal for handheld parts and consumer-facing components.
Straight Knurling offers axial traction, commonly used in slider systems or linear assemblies.
Helical Knurling improves twist-based engagement, often applied in fasteners or rotary interfaces.
Table 2: Pattern Functionality Breakdown
Pattern Type | Grip Direction | Ideal Use |
Diamond | Multidirectional | Tools, knobs, flashlights |
Straight | Axial | Shafts, rails, linear sliders |
Helical | Rotational | Screws, torque couplings |
Specifying the correct pattern can reduce end-user complaints and field failures. Buyers benefit from more predictable part behavior in their downstream product lines.
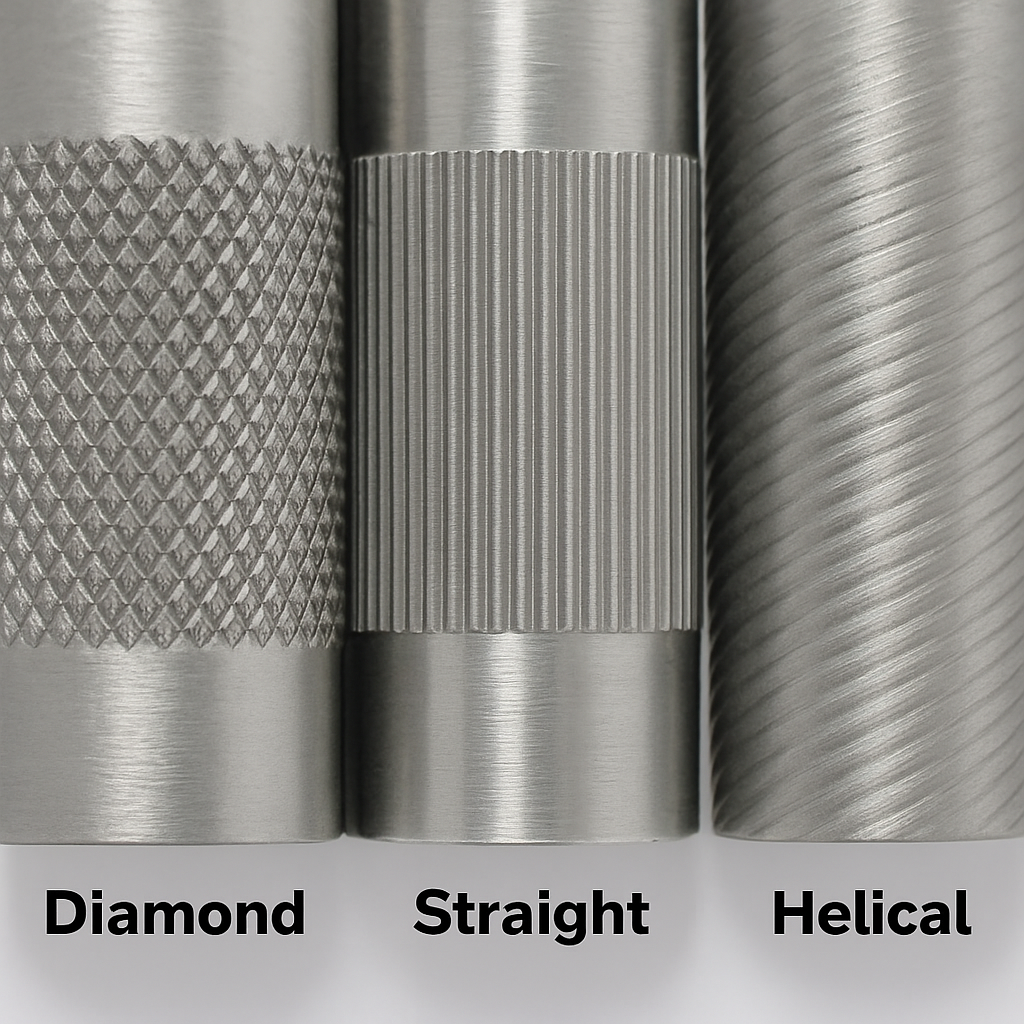
From Design to Delivery: A Procurement-Oriented Knurling Workflow
Design Considerations
A supplier’s knurling ability starts at the CAD file. Overseas buyers should confirm:
Clear indication of knurled zones
Desired pitch or TPI (teeth per inch)
Material thickness requirements
Poorly defined drawings can delay orders or result in incorrect samples. At YISHANG, every inquiry undergoes pre-production design review to validate feasibility and optimize manufacturability.
Tooling & Process Controls
CNC-controlled tooling allows us to:
Match pitch to diameter digitally
Calibrate feed speed by material type
Conduct visual inspections in-line to ISO 4287
Every production run includes dimensional verification, reducing the chance of shipment rejections or in-field failures. For repeat orders, process parameters are archived to maintain consistency.
For purchasing professionals, this consistency means fewer surprises, lower defect rates, and reduced time managing back-and-forth communications.
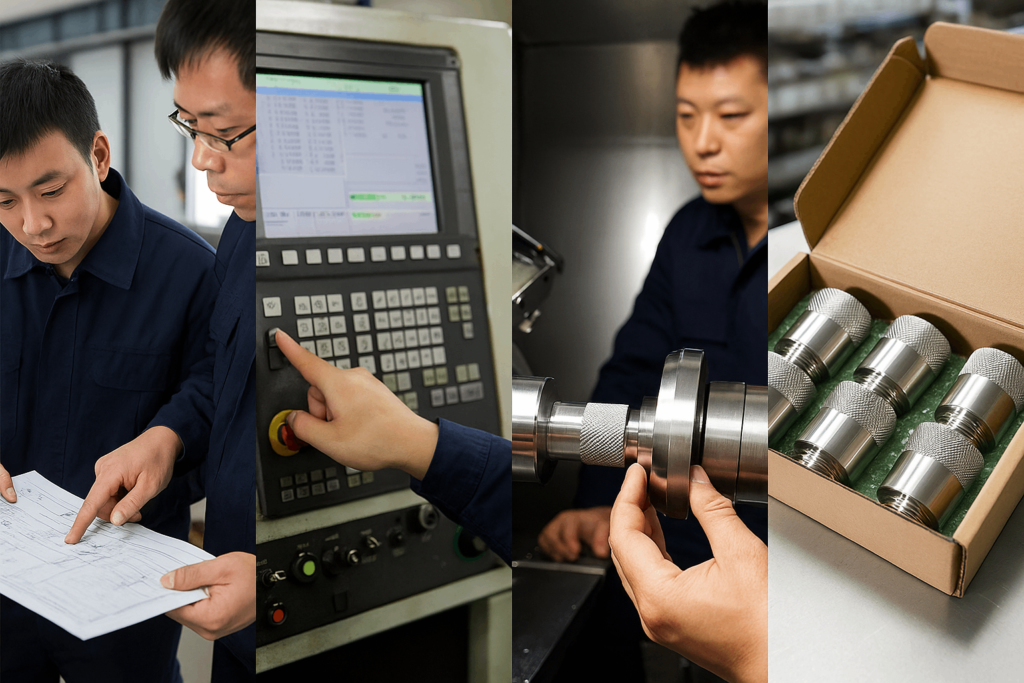
Preventing Common Knurling Issues
Common Defects and Their Procurement Impact
Tool Wear can flatten knurls, reducing grip and appearance.
Double Tracking results in overlapping patterns—usually a setup error.
Material Springback affects pattern depth, especially in stainless steel.
YISHANG addresses these risks through routine tool maintenance, trained operators, and digitally assisted setup. Our preventive focus supports high-volume orders with tight deadlines.
Procurement teams should always confirm a supplier’s QA process and whether defect reports are available per batch. For large-scale orders, even a 2% rejection rate can add substantial cost.
Cross-Industry Applications Backed by Data
Automotive: Knurled inserts in connectors improve torque resistance. Studies show 35% improved joint retention when knurled parts are used.
Medical Devices: Fine-pitch patterns meet hygienic requirements while improving handling.
Consumer Products: From flashlight bezels to camera dials, knurling communicates quality and enhances user experience.
Power Tools: Coarse diamond knurls maintain grip in oil or dust environments—critical in jobsite conditions.
YISHANG supplies knurled parts to over 50 countries, supporting industries with different compliance needs, including FDA-compliant assemblies, UL-certified parts, RoHS lot-level documentation, and other regulatory standards such as ASTM B209 for aluminum and DIN 82 for knurling specifications.
Conclusion
For B2B buyers, knurling is not a decorative detail—it’s a mechanical necessity. It supports grip, strength, and assembly precision at scale.
Choosing a supplier with advanced tooling, multi-metal capability, and reliable QA practices can significantly impact your downstream efficiency and product performance.
YISHANG brings decades of experience, cross-industry know-how, and export-ready systems to support your knurled part needs.
FAQ: Common Questions from Overseas Buyers
What is the best knurling for grip?
Diamond knurling provides the most effective multidirectional grip, making it ideal for tool handles and industrial dials where slip prevention is critical.
Can aluminum be knurled?
Yes, aluminum is highly suitable for knurling, especially using the form knurling method. YISHANG often processes aluminum components per ASTM B209 standards.
Knurling in press-fit applications
Knurled shafts are commonly used in press-fit joints to avoid adhesives or welding. The texture increases friction and ensures tighter tolerance fits, particularly in high-vibration applications.
Let’s Work Together
Need high-volume custom knurled parts from a trusted metal manufacturing partner?
Contact YISHANG to discuss your specifications and request a quick quote.