For global steel buyers, choosing between hot rolled and cold rolled steel is not a technical formality—it’s a sourcing decision with direct consequences for cost, lead time, assembly efficiency, and long-term performance.
At YISHANG, we specialize in helping procurement professionals across 50+ countries make data-informed decisions when specifying steel for enclosures, frames, industrial machinery, and custom components. This article provides a comparative analysis of hot rolled vs cold rolled steel from the perspective of wholesale buyers and OEM project managers.
You’ll find insights that go beyond the question of what is hot rolled steel or what is cold rolled and hot rolled steel—this is about choosing the right material strategy to streamline production, reduce waste, and improve quality at scale.
Hot Rolled vs Cold Rolled: Manufacturing Process and Buyer Implications
Understanding the production process gives sourcing professionals context around pricing, finish quality, and availability.
Hot rolled steel is manufactured at high temperatures (above 1700°F / 927°C), making it easier to shape large volumes. After cooling naturally, it forms a surface scale that often needs to be removed. This steel is commonly used in construction frames, agricultural equipment, and large-format parts.
Cold rolled steel, in contrast, is processed at ambient temperature, enhancing surface smoothness, tolerance precision, and strength through work hardening. These features make it better suited for electronics housings, vending machine panels, and appliance structures.
For procurement managers, the key takeaway is not just the difference between hot and cold rolled steel—but how that difference affects post-processing needs, defect rates, and final assembly quality.
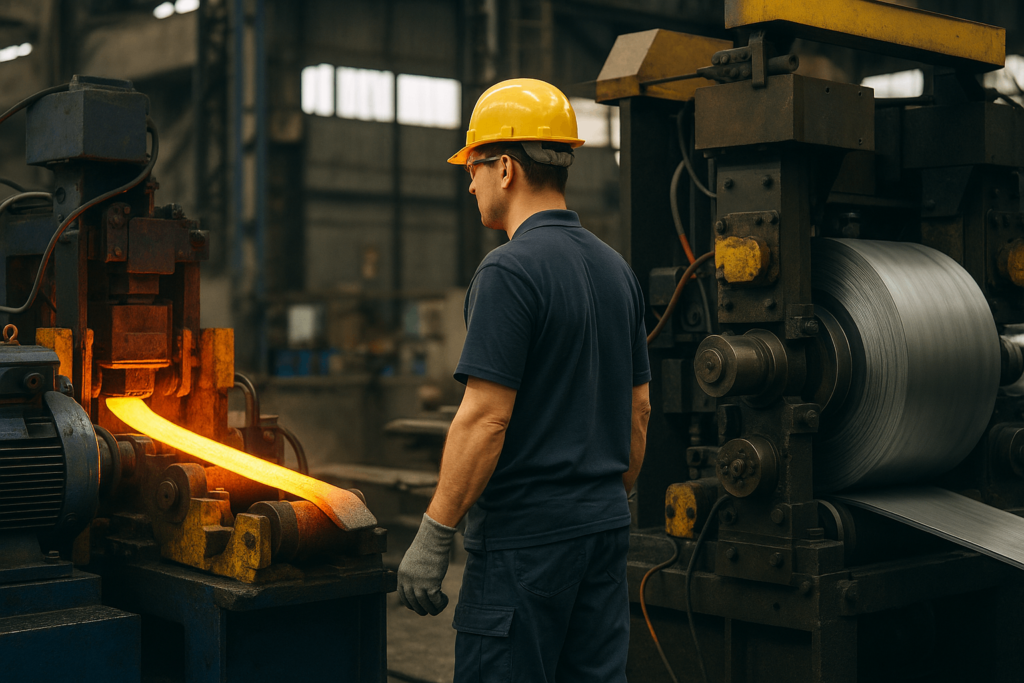
Global Market Trends: Why Cold Rolled Demand is Rising
According to market research from Grand View Research, the global cold rolled steel market size surpassed $120 billion in 2023, and is projected to grow at a CAGR of 4.2% from 2024 to 2030. Growth is primarily driven by demand in automotive, electronics, and consumer appliances, where surface finish and dimensional precision are critical.
In contrast, the hot rolled steel market remains dominant in terms of volume—especially in infrastructure and heavy equipment sectors—but pricing volatility and rising environmental regulations on high-energy processes have made cold rolled a more appealing option for many OEM buyers.
For sourcing professionals, this trend underscores the importance of matching material capabilities with consumer-grade product expectations, particularly when competing in markets with high cosmetic or performance demands.
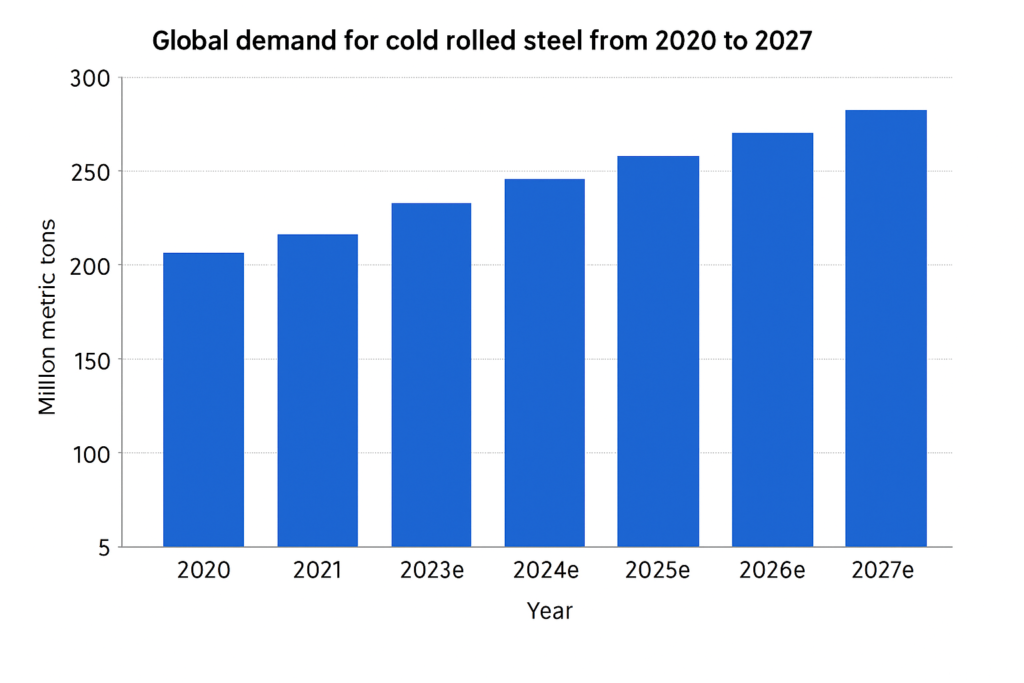
Mechanical Performance and Procurement Trade-Offs
Grain structure determines how a material behaves under stress. Hot rolled steel cools quickly, resulting in looser grain patterns. It provides solid ductility and impact resistance, ideal for heavy-duty, low-finish applications.
Cold rolled steel features elongated, compact grains due to strain hardening. This translates to higher tensile and yield strength, but less ductility. It can maintain shape under stress yet may crack if over-formed.
From a sourcing angle, understanding these traits helps prevent mismatches between material capability and part requirements. For example, cold rolled steel may eliminate the need for bracing in thin enclosures, reducing total part count and saving cost.
In terms of fatigue resistance, both materials perform well when used appropriately. Cold rolled products may perform better in static precision structures, while hot rolled is suitable for flexing components.
Dimensional Accuracy and Surface Finish: Precision Matters
Cold rolled steel is the clear winner on dimensional control. Tolerances can be held consistently across long runs—ideal for buyers supplying automated production lines or high-accuracy assemblies.
Its smooth finish also improves paint adhesion, engraving consistency, and reduces the need for secondary finishing. This makes cold rolled an excellent choice for brands that prioritize visual quality or customer-facing components.
Surface treatment options also vary. Cold rolled steel is compatible with powder coating, electrophoretic coating, and chrome plating due to its clean finish. Hot rolled steel typically requires descaling and surface grinding before applying galvanization, powder coating, or electroplating.
Buyers should factor in post-processing costs when comparing cold rolled vs hot rolled steel. A cheaper base material may create more expense during coating, cutting, or fitting.
Welding, Forming, and Machining: What Affects Production Speed
Hot rolled steel, due to its ductility and lower internal stress, offers easier welding and forming. It’s less prone to cracking, even in field conditions or low-prep welding environments.
Cold rolled steel, with higher internal tension, may require preheating or tighter welding parameters. In CNC environments, its increased hardness causes more tool wear. For parts requiring deep cuts, multiple holes, or tight internal geometry, buyers should confirm machining compatibility with their vendors.
When evaluating hot rolled vs cold rolled steel for forming, remember that springback is more common with cold rolled material. For brackets, panels, or angular features, your fabrication partner may need to adjust tooling or angles, which adds lead time.
In short, cold rolled delivers finish and precision, but often at the cost of processing efficiency. Hot rolled allows faster fabrication, but may require finishing steps.
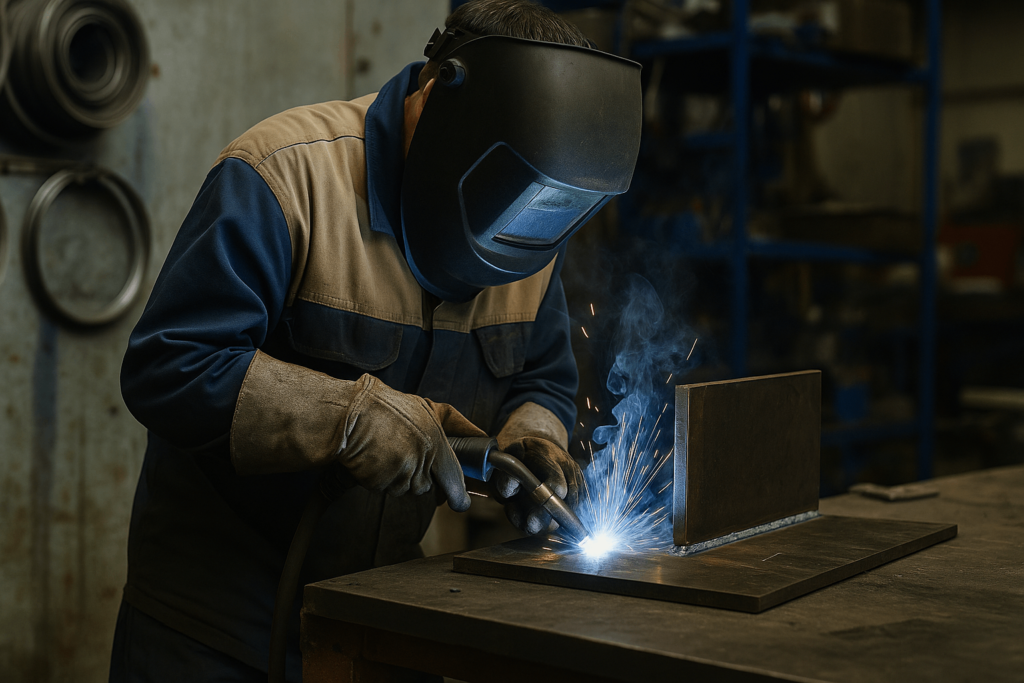
Total Cost Comparison: Going Beyond Per-Kilo Price
While hot rolled is generally lower in price per ton, that figure alone can mislead. Let’s look at a practical example comparing parts made from each material:
Cost Factor | Hot Rolled Steel | Cold Rolled Steel |
---|---|---|
Base Material Cost | $700/ton | $950/ton |
Surface Finishing | Required (e.g., deburr) | Often unnecessary |
Machining Tool Wear | Moderate | Higher |
Welding Efficiency | High | Medium (needs control) |
Reject Rate (est.) | 4–6% | 1–2% |
Lead Time Flexibility | Shorter for large runs | Longer for prep/setup |
The difference between hot rolled and cold rolled steel becomes clearer when viewed through total cost of ownership. Cold rolled steel’s upfront cost may be higher, but downstream savings in coating, reject reduction, and assembly precision can justify the investment.
For long-term production programs or products with a customer-facing visual requirement, cold rolled may be more economical.
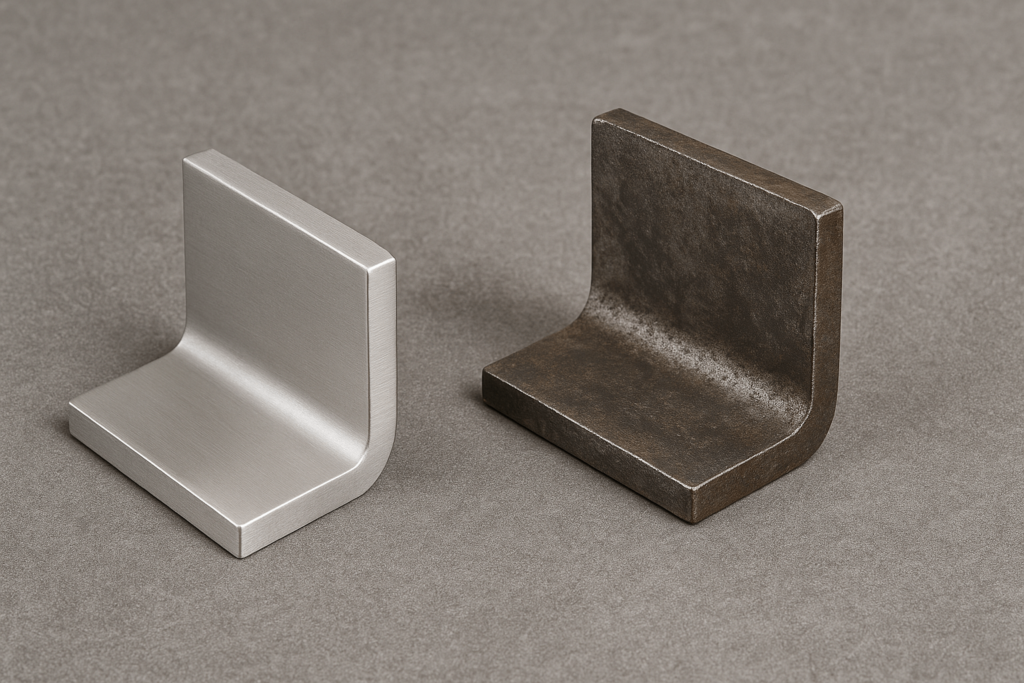
Real-World Use Case: From Cost Overruns to Smart Sourcing
One of YISHANG’s European clients—a vending machine OEM—initially chose hot rolled steel for all housing and frame components to cut raw material costs. However, the post-weld scale removal, machining inconsistencies, and frequent repainting drove up total unit cost.
After consultation, we recommended switching to cold rolled steel for external panels and precision mounting frames. The client saw:
27% reduction in secondary processing cost
13% faster assembly time due to better part fit
0.8% improvement in monthly QA pass rate
This hybrid-material approach (cold rolled for precision, hot rolled for structure) is now part of their global BOM strategy—demonstrating that informed material selection has lasting financial impact.
Sector-Specific Applications: How Buyers Should Choose
Automotive: Chassis and brackets favor hot rolled. For doors, dashboards, and trim panels, cold rolled offers better alignment and appearance.
Construction: Beams, bars, and support structures lean toward hot rolled. For elevator panels, door frames, and interior fittings, cold rolled is preferred for its finish.
Electronics & Appliances: Cold rolled steel is the default. It offers stable panel sizing, compatibility with powder coating, and easy laser engraving.
Agriculture & Heavy Equipment: Hot rolled is cost-effective for frames and guards. For maintenance panels or branded covers, cold rolled adds value.
Your material choice impacts not just durability or form—but inventory control, return rates, and customer satisfaction. Sourcing teams should align selection with their product’s end-use exposure, finish requirements, and form factor constraints.
Supplier Support Makes the Difference
At YISHANG, we support buyers with technical consultations during the sourcing phase. We analyze not just the difference between cold rolled steel and hot rolled steel but also their implications across surface treatment, forming performance, and batch production stability.
As a certified RoHS + ISO 9001 supplier, we provide:
Customized cutting, punching, bending, welding, and surface treatment
Material traceability documentation
OEM and ODM design assistance
Guidance on tolerance and coating compatibility
Whether you need advice on what is cold rolled steel used for in your industry or how to improve precision during mass production, our team collaborates from prototype to shipment.
Frequently Asked Questions (FAQ)
What is the difference between hot rolled and cold rolled steel?
Hot rolled steel is processed at high temperatures, making it easier to form and more cost-effective for structural applications. Cold rolled steel is rolled at room temperature, offering better dimensional precision and a smoother surface, ideal for parts that require tight tolerances and clean finishes.
Is cold rolled steel always better for surface finish?
Yes, cold rolled steel generally offers a smoother, more uniform surface finish straight from the mill. This makes it better suited for applications requiring paint, coating, or a polished appearance. However, it may need stress relief or pre-processing depending on the forming process.
Can hot rolled steel be used for precise applications?
Yes, but it usually requires additional machining or surface grinding to meet tight dimensional tolerances. Hot rolled steel is better for applications where finish is not critical, but with proper processing, it can be adapted for more precise use cases.
Conclusion
Material choice is not a one-size-fits-all answer. It depends on volume, usage, aesthetic requirement, and supply chain capacity.
For structural needs, short lead times, and low cost, hot rolled steel is often sufficient. For tight tolerance components, customer-visible surfaces, or minimal rework, cold rolled steel is more strategic.
Understanding the difference between hot rolled and cold formed steel helps prevent overengineering or underperforming choices. The key is to select based on total operational value—not just base price.
Need help selecting the right steel for your next order? Contact YISHANG for sourcing guidance and a quick quote.