For global buyers sourcing precision metal parts, accuracy, reliability, and supplier capability are top priorities. Wire EDM (Electrical Discharge Machining) has become a preferred process in high-precision manufacturing thanks to its ability to create intricate, burr-free features in hardened and conductive materials. It meets tight tolerances, maintains surface integrity, and supports both prototyping and batch production.
This guide is tailored to the needs of international wholesale buyers, sourcing managers, and technical procurement professionals. We focus on practical insights: how Wire EDM works, how it impacts production quality and lead times, and how YISHANG delivers consistent value across every custom part order.
What Is Wire EDM and Why It Matters to Buyers
Wire Electrical Discharge Machining is not just a manufacturing process—it’s a value enabler in the supply chain. It uses spark erosion to cut precise paths through electrically conductive materials. This is done by discharging high-frequency electrical pulses between a wire electrode and the workpiece, both submerged in a dielectric fluid.
Why should this matter to a procurement specialist? Because it eliminates many common defects found in mechanical cutting: tool marks, thermal deformation, and inconsistent tolerances. For parts that require precision, whether in tooling, connector frames, or custom fixtures, Wire EDM can ensure each piece meets exact specifications with minimal secondary work.
Buyers prioritizing quality control, repeatability, and on-time delivery can rely on Wire EDM for critical parts—particularly when sourcing high-mix, low-to-medium volume orders where conventional tooling isn’t practical or cost-effective.
How Does Wire EDM Work?
The Technical Principle: Spark Erosion Simplified
Wire EDM operates without physical contact between tool and part. A continuously fed wire, often brass or molybdenum, is tensioned and guided along a CNC-programmed path. Sparks generated in a micro-gap between the wire and workpiece melt and vaporize the material, while deionized water flushes away debris.
Each spark removes a tiny amount of metal, allowing for extreme control. This is crucial for parts requiring tolerances within ±2–5 microns. Because the wire is consumed during cutting, each part is machined with a fresh electrode edge—maintaining consistency across entire production runs.
Why the Process Benefits Your Procurement
From the buyer’s perspective, Wire EDM reduces rework, lowers the risk of rejects, and improves first-pass yield. Parts do not warp or stress under cutting pressure. There is no need for expensive hard tooling or ongoing tool maintenance. For smaller batch orders or development cycles, this means faster project starts and simplified supplier coordination.
Key Parameters That Define Wire EDM Precision
For sourcing teams comparing cutting methods, Wire EDM delivers standout metrics:
Parameter | Typical Range |
---|---|
Tolerance | ±2 to ±5 μm |
Surface Finish (Ra) | 0.1 to 1.5 μm |
Material Thickness | Up to 300 mm |
Wire Diameter | 0.1 to 0.33 mm |
Spark Rate | 10,000+ sparks/sec |
Understanding these benchmarks helps buyers confirm supplier capability. When tolerances are critical to part function, relying on precise EDM parameters ensures that every shipment meets spec.
Core Components of the EDM Process Chain
Buyers selecting suppliers should evaluate not only price, but process infrastructure. At YISHANG, we invest in advanced EDM platforms that integrate the following:
Pulse Power Generators for adaptive spark control based on material type
CNC Wire Drive Units that maintain consistent tension and feed
Dielectric Management Systems with automated filtration and conductivity control
Fixture Design Customization for irregular or complex parts
Multi-axis CNC Control for tapers, curves, and undercuts
This level of machine capability ensures the stable, reproducible cutting performance that international procurement teams demand.
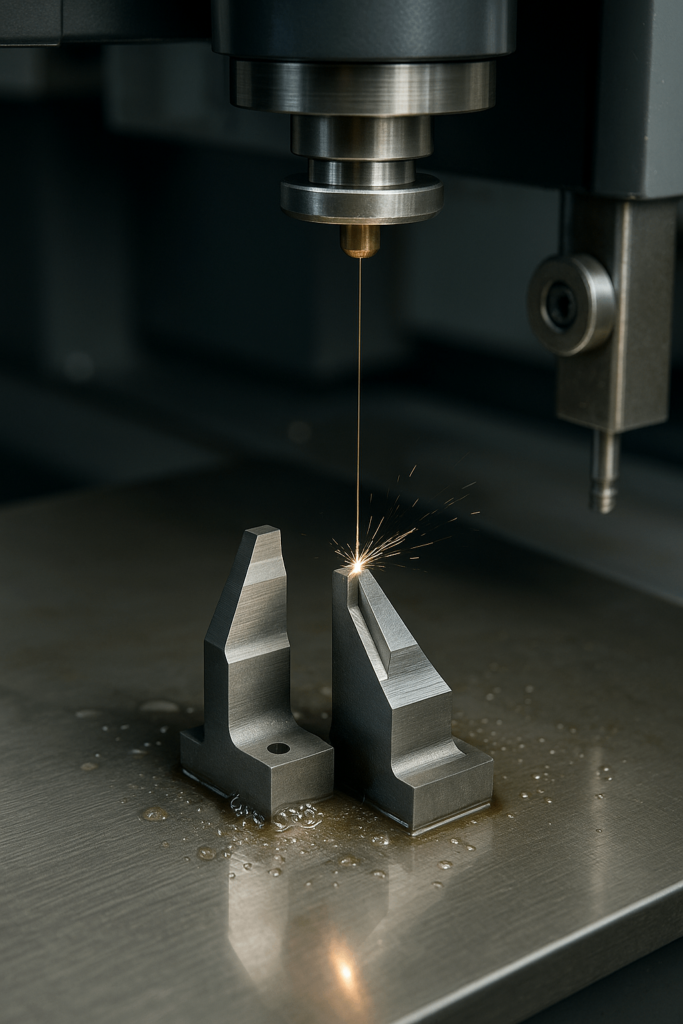
What Materials Are Suitable for Wire EDM?
Wire EDM is compatible with a wide range of conductive metals. For buyers sourcing hard-to-machine materials, EDM provides a unique path to achieve precise results with no tool deflection.
Common EDM Materials for Export Parts:
Hardened tool steels (D2, H13)
Medical-grade stainless steel (316L)
Aerospace titanium and Inconel
Electrical-grade copper and brass
Tungsten carbide and hardened dies
Whether you are producing wear-resistant dies or precision-aligned connectors, EDM handles these alloys with minimal thermal effect. This preserves both dimension and material properties—critical for OEM and ODM part buyers managing performance-critical supply chains.
Why Wire EDM Fits Precision Procurement Needs
Buyers responsible for overseas metal part procurement must balance lead time, tolerance, surface finish, and cost. Wire EDM offers:
High Consistency: Maintains accuracy across batches.
No Hard Tooling Required: Reduces up-front investment.
Ideal for Complex Shapes: Sharp corners, closed channels, and fine profiles.
Stress-Free Processing: Preserves structural and fatigue strength.
When you receive parts produced by EDM, dimensional reports usually confirm tolerances on the first delivery—reducing costly delays caused by rework or spec deviation.
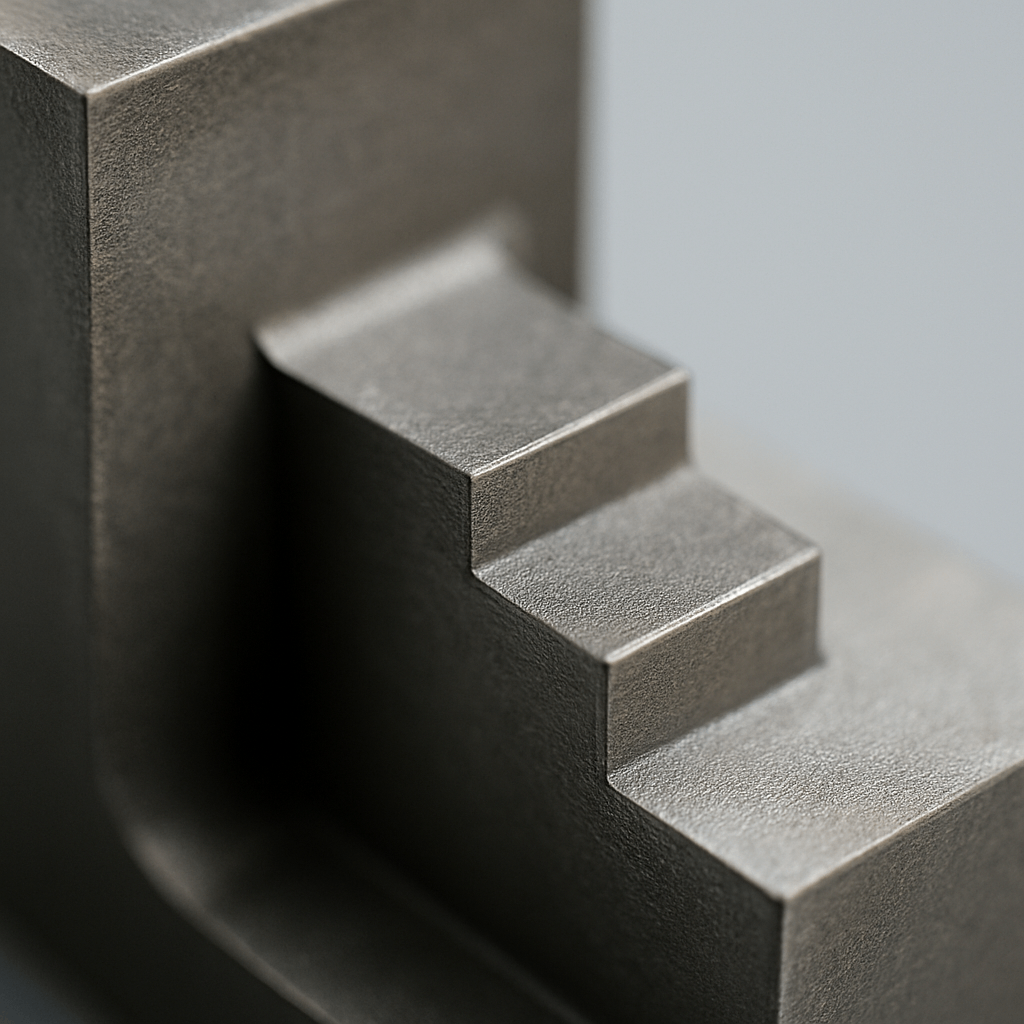
Where EDM Outperforms Other Cutting Methods
Method | Tolerance | Best Use Cases |
Wire EDM | ±2–5 μm | Mold cores, fine slots, tool inserts |
CNC Milling | ±5–10 μm | Blocks, contours, open profiles |
Laser Cutting | ±20–50 μm | Sheet metal profiles |
Waterjet | ±50–100 μm | Large thick plates, soft composites |
Sinker EDM | ±5–10 μm | Mold cavities, hardened die shapes |
EDM is particularly strong in jobs that involve high hardness, tight spaces, or heat-sensitive parts. For buyers, this translates into fewer supplier limitations, more design freedom, and lower sourcing risk.
Real-World EDM Applications That Matter to Buyers
Instead of listing industries, let’s focus on functional value. If you’re a procurement officer, you’re asking: “Can this process deliver what my project requires?”
Custom Prototypes Without Tooling: Enables fast turnaround for short runs.
Post-Hardening Operations: Machines heat-treated parts without cracking.
Internal Detail Cutting: Ideal for blind slots, closed holes, and fine patterns.
Batch Quality Matching: Every part cut from new wire—zero degradation.
For instance, buyers sourcing precision tooling cores often request ±3 μm tolerances with mirror-like surfaces. EDM can meet these needs in one setup, without grinding or polishing.
Innovations That Support Procurement Strategy
Suppliers like YISHANG leverage automation and smart controls to support reliable global delivery:
Automatic Wire Threading: Speeds up production cycles
Real-Time Monitoring: Ensures spark conditions remain optimal
CAD/CAM Integration: Shortens design-to-manufacture lead time
Eco-Friendly Systems: Dielectric recycling cuts waste and cost
With these systems in place, buyers get not only a part—but a process they can trust to deliver on spec, at volume, across repeat orders.
Conclusion
For international sourcing professionals, Wire EDM represents more than a precise cutting process—it’s a strategic tool for building dependable, cost-effective supply chains. It gives procurement teams confidence that their designs will be produced accurately, consistently, and on time.
With support from a supplier like YISHANG, Wire EDM becomes a value-added capability—one that enables efficient fulfillment of even the most demanding parts.