Industrial Chains Are Not Created Equal: Rethinking Their Role in High-Performance Manufacturing
Industrial chains are among the most underappreciated components in manufacturing systems, often dismissed as simple mechanical parts. Yet, their influence on production efficiency, mechanical reliability, and cost optimization is far from negligible. Whether in heavy-load lifting or high-speed conveying, industrial chains transmit mechanical power with precision and endurance where other systems—like belts or gears—might falter.
More than just links of steel, they are critical interfaces between drive mechanisms and movement. In sectors such as automotive, food processing, logistics, and energy storage, their performance directly impacts uptime and safety. Understanding this fundamental role sets the foundation for a more strategic approach to chain selection, tailored not by convenience but by function.
Application Context First: How Chains Perform Differently Across Industries
Chain performance is not one-size-fits-all. Each industry demands unique load characteristics, environmental resistance, and chain geometries. By framing chain use through the lens of application, we unlock a more targeted and effective method of selection.
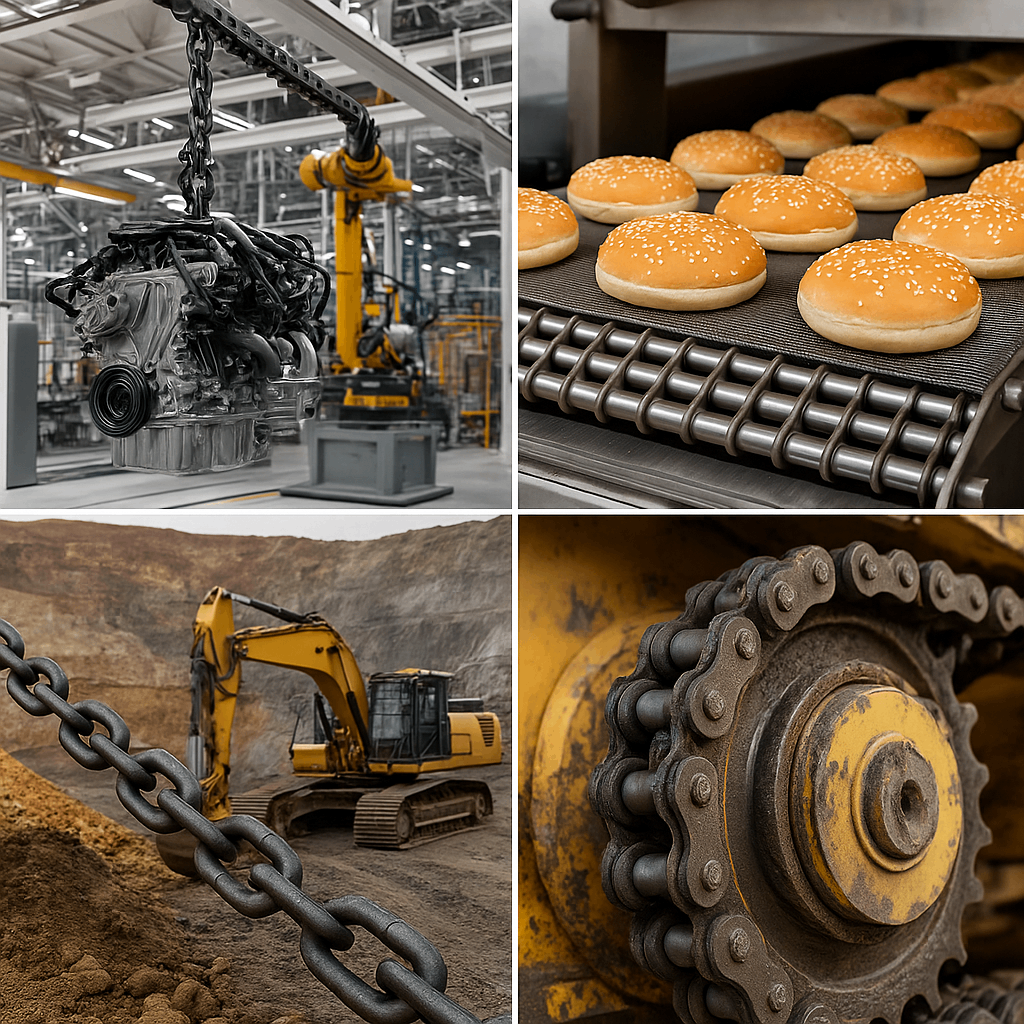
Automotive and Assembly Lines
High-speed production lines require chains that can operate continuously under synchronized motion with minimal noise and wear. Roller chains are prevalent here due to their precision and reliability. Silent chains, with their smooth tooth-like engagements, are increasingly adopted in automated systems where vibration and acoustic levels matter.
Food, Medical, and Electronics
Hygiene-sensitive industries mandate corrosion resistance and cleanability. Stainless steel chains (304 or 316 grades) are the default, offering resistance to moisture and chemicals. Plastic chains and self-lubricating solutions are also common, reducing contamination risk and maintenance cycles—crucial for sterile environments.
Construction, Agriculture, and Mining
In high-dust, high-load environments, leaf chains and engineering steel chains shine. Their rugged construction allows for better shock absorption and high tensile loads. Here, corrosion-resistant coatings and extended pitch designs support both durability and cost-effectiveness in the field.
Energy Storage and Automation
Modern conveyor systems for batteries, solar components, and warehouse automation rely on flexible chain designs. Hollow pin chains enable modular fixtures and tooling adaptation, streamlining assembly and sorting operations.
Chain Type is Only Half the Story: Why Material, Grade and Geometry Matter More Than You Think
While chain “type” (roller, leaf, conveyor) offers an initial classification, material, grade, and dimensional geometry ultimately define real-world performance.
Chain Materials: More Than Metal
Material choice dictates everything from corrosion resistance to weight and tensile strength. Carbon steel remains a cost-effective standard, but it lacks resistance to humidity and chemicals. Stainless steel, especially grades 304 and 316, is the go-to for food and chemical handling. Nickel-plated or alloy steel chains extend durability under abrasion and impact conditions.
Grades: More Than Just Numbers
Industrial chain grades are often misunderstood. Each grade—30, 43, 70, 80, 100, and 120—reflects a specific strength and application profile:
Grade | Typical Application | Working Load Limit (WLL) |
---|---|---|
30 | General utility (light duty) | Low |
43 | High test, transportation | Moderate |
70 | Transport chain (DOT approved) | Medium |
80 | Lifting (OSHA approved) | High |
100 | Overhead heavy lifting | Very High |
120 | Ultra-heavy-duty, niche use | Extreme |
Choosing the right grade prevents both underengineering and costly overengineering.
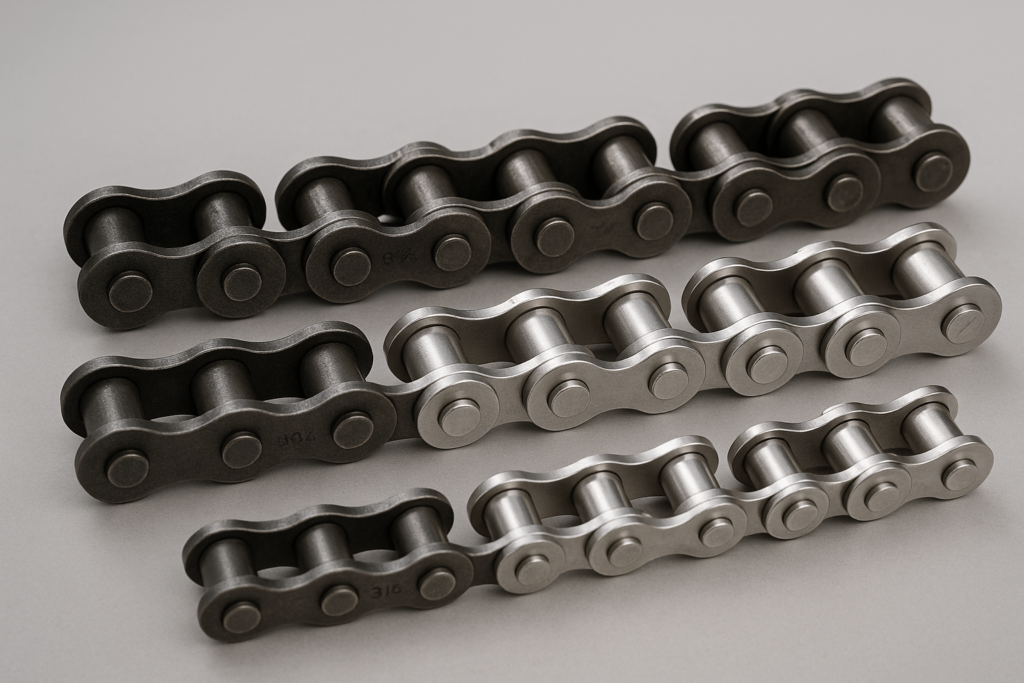
Geometry: Design for Fit and Performance
Key factors like chain pitch, roller diameter, and plate thickness define compatibility with sprockets and overall system efficiency. For example, extended pitch chains reduce speed but increase load capacity, ideal for slow, heavy-duty conveyors. Misalignment due to incorrect geometry leads to premature wear and potential system failure.
How Engineering Teams Should Actually Choose Chains (And Where They Go Wrong)
Chain selection should be an engineering decision—not a procurement checkbox. Unfortunately, many failures stem from mismatched assumptions rather than mechanical defects.
Start by mapping the actual load profile: is it constant or shock-loaded? Is the motion linear or rotational? How much ambient heat, dust, or moisture is present? Environmental variables must be modeled alongside mechanical needs.
Too often, companies choose chains based on familiarity or catalog availability. But this shortcut ignores application-specific demands. For example, selecting a standard roller chain in a wet washdown facility might save costs upfront but result in system failure due to corrosion.
Professional selection frameworks include:
Load capacity matching: WLL and breaking load alignment
Environmental fit: Material and coatings for specific exposure
System integration: Geometry matching with sprockets, guides, and tensioners
Lifecycle cost analysis: Evaluating replacement frequency, maintenance needs, and total cost of ownership
By shifting chain selection from purchasing to engineering, companies can reduce downtime, improve safety, and optimize operational ROI.
Chain System Lifecycle, Maintenance and Failure Prevention
Even the best chain will fail if misused or poorly maintained. Understanding a chain system’s lifecycle—from commissioning to decommissioning—ensures longer service life and cost control.
Wear and Elongation
All chains experience elongation over time due to pin and bushing wear. An elongation of more than 3% often signals imminent failure. Measuring elongation periodically allows predictive maintenance.
Lubrication and Cleaning
Lubrication intervals vary by chain type and environment. In dusty conditions, dry lubrication reduces grit accumulation. In cleanrooms, food-grade lubricants or self-lubricating chains are preferable. Over-lubrication can attract debris, accelerating wear.
Environment | Lubrication Interval | Recommended Lubricant |
Dry and dusty | 2 weeks | Dry film lubricant |
Wet or corrosive | 1 week | Synthetic or food-grade oil |
High-speed operation | 1–2 days | High-viscosity chain oil |
Alignment and Tensioning
Improper alignment leads to uneven load distribution and roller skewing. Use laser alignment tools or shimming techniques to correct offset. Chain sag should not exceed 2% of center distance under load.
Establishing inspection routines—weekly for heavy-use, monthly for moderate use—adds to operational safety. Maintaining documentation of failure rates and downtime builds a knowledge base that informs future chain selection and design.
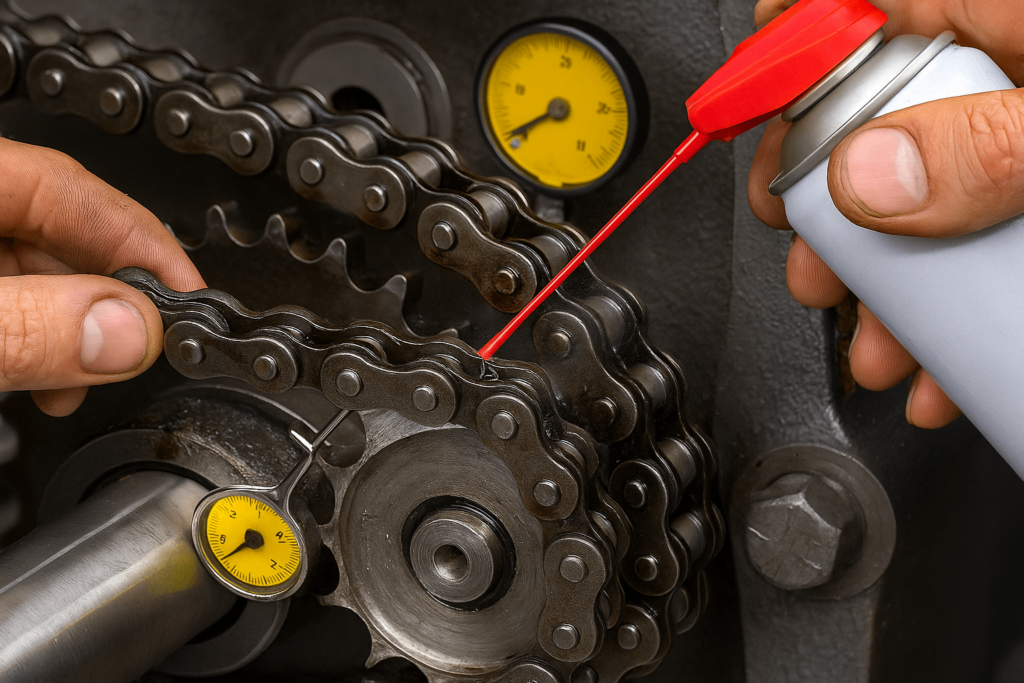
Innovation Watch: Where Industrial Chains Are Evolving in 2025 and Beyond
Chain technology has traditionally evolved slowly, but with digitization and materials science breakthroughs, we’re witnessing rapid transformation.
Self-Lubricating and Maintenance-Free Chains
Advanced bushings and coatings now enable chains to operate thousands of hours without relubrication. In food or pharmaceutical plants, this innovation cuts contamination risk and maintenance costs.
Smart Chains and Sensor Integration
IoT-enabled chains with embedded vibration, tension, or temperature sensors offer predictive maintenance insights. When connected to central monitoring systems, these chains notify operators before a failure occurs—essential for high-throughput environments.
Lightweight Materials and Hybrid Composites
Aluminum-link chains or reinforced polymer chains are gaining ground in weight-sensitive sectors like aerospace logistics or robotics. Though not suitable for all high-load applications, these designs are increasingly common where weight-to-performance ratio matters.
These innovations suggest that chains are not static technology but evolving assets that contribute to Industry 4.0 goals.
Chain Selection as a Strategic Decision
When viewed as a strategic asset rather than a consumable, chain systems unlock value across procurement, engineering, and operations. They influence machine uptime, worker safety, product quality, and even energy efficiency.
Too often, companies fall into reactive replacement cycles—waiting for failure to justify upgrades. Instead, integrating chain selection into equipment planning and facility layout stages ensures better outcomes.
This strategic view also extends to supplier choice. Partnering with OEMs or contract manufacturers like Yishang Metal Products Co., Ltd. allows customization to fit exact needs—whether it’s material grade, precision manufacturing, or application-specific geometry. With over 26 years in metal fabrication and chain component support across sectors, Yishang brings both the engineering and production capabilities to deliver optimized solutions.