A Real-World Problem: Why Parts Fail Despite Being "In Tolerance"
Global wholesale buyers often experience a frustrating scenario: components arrive from suppliers with dimensionally “acceptable” tolerances, yet they don’t fit properly during final assembly. It’s a quality risk that quietly drives up costs through returns, delays, and rework.
This happens when dimensional tolerancing doesn’t reflect actual fit functionality. Even when every part passes gauge inspection, mismatched fits at the assembly line can occur. These aren’t isolated incidents—they’re common in high-volume procurement, especially in sectors like industrial hardware, vending equipment, and smart enclosures.
At YISHANG, we’ve helped global buyers transition to tolerance frameworks that factor in geometric behavior—starting with Maximum Material Condition (MMC). It’s not just a GD&T principle; it’s a purchasing safeguard.
What Is MMC—and Why Procurement Teams Should Care
MMC defines the state where a feature contains the most material: the smallest hole or the largest shaft, within its dimensional limits. But for wholesale buyers, the relevance is practical.
By specifying MMC in a GD&T feature control frame, the allowed positional tolerance expands as the feature’s size departs from its maximum material state. This built-in tolerance flexibility—known as Bonus Tolerance—translates to fewer rejections, less rework, and more efficient production.
According to ASME Y14.5, this approach isn’t about compromising precision. It’s about defining acceptable variation that supports function. For buyers, this means faster approval cycles and higher yield without design concessions.
How MMC Enhances Quality and Cost Control in Metal Fabrication
In real-world procurement, success is measured not just by specs, but by consistency. When MMC is applied to holes, slots, and tabs on sheet metal parts, more units pass inspection—even with natural process variation—while maintaining functional interchangeability.
Consider this scenario: an EV charging cabinet has a mounting plate with multiple fastening holes. Without MMC, parts with minimal location deviation may fail QA. With MMC, those same deviations are permissible if the hole size is slightly over MMC, ensuring proper fit and reducing unnecessary rejections.
At YISHANG, clients across energy storage, telecom, and vending systems benefit from MMC usage. We’ve seen NCR rates drop by over 20% in projects where Bonus Tolerance was properly applied. This isn’t just better engineering—it’s better purchasing assurance.
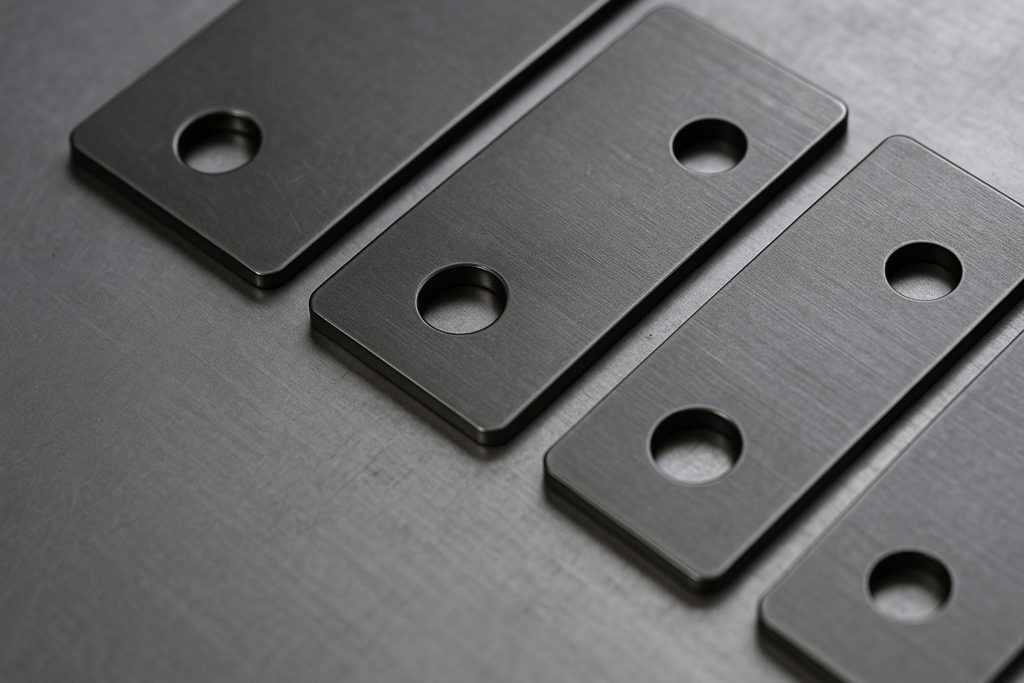
Understanding Bonus Tolerance: The Hidden Advantage
Here’s a simplified use case:
Feature | MMC Size | Actual Size | Basic Tolerance | Bonus | Total Positional Allowance |
---|---|---|---|---|---|
Hole | 10.00 mm | 10.20 mm | 0.20 mm | 0.20 mm | 0.40 mm |
As the hole size increases beyond MMC, extra tolerance is added. From a supplier’s standpoint, this increases the process window. From a buyer’s perspective, it reduces false failures in inspection reports—especially at third-party labs or CMMs overseas.
Misunderstood as a “loophole,” Bonus Tolerance is a legitimate cost-control mechanism. It bridges engineering intent with procurement goals: dimensional quality that supports real-world assembly.
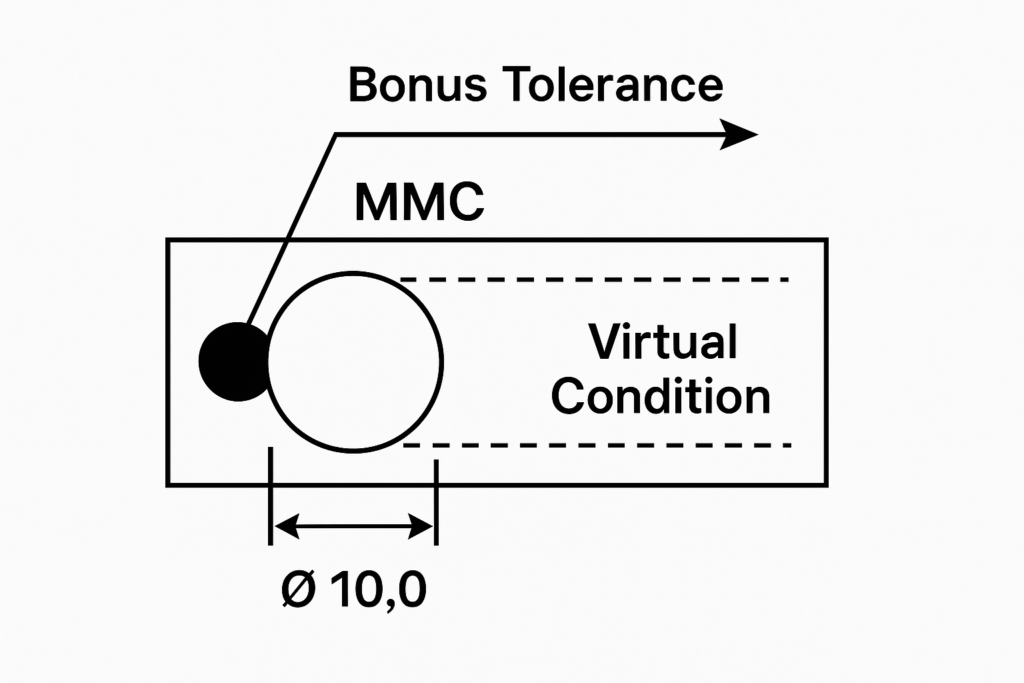
MMC in Practice: How We Inspect for Functional Compliance
Buyers routinely ask us how tolerances are enforced across mass production. MMC shapes the answer.
Rather than inspecting all features strictly at nominal size, we use Go/No-Go gages and MMC-aligned inspection tooling to verify that parts meet functional criteria. This eliminates unnecessary scrap and supports batch traceability.
Where required, our CMM routines are programmed to factor in Bonus Tolerance dynamically. Using Zeiss and Hexagon systems, we provide inspection reports showing:
Actual feature size
Bonus calculations
Pass/fail status based on functional zones
This methodology reduces audit friction and supports compliance with your internal AQL standards and supplier scorecards.
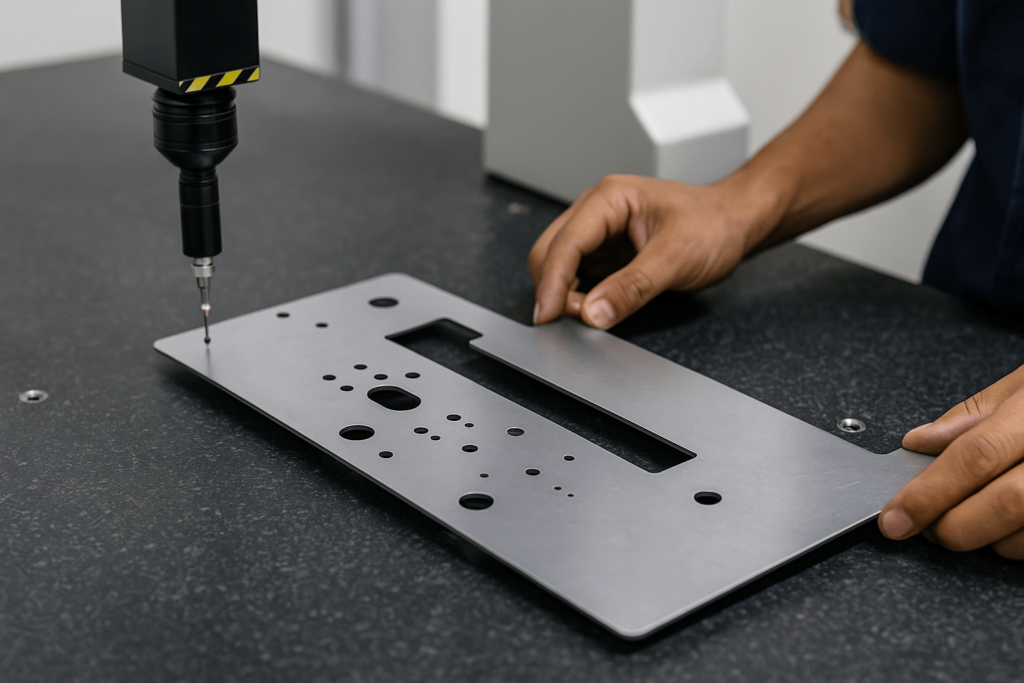
Where MMC Can Be Misused—And How to Avoid It
Applying MMC where it doesn’t belong is counterproductive. Common errors include:
Applying MMC to non-functional surfaces or cosmetic elements
Using MMC on flexible sheet areas where distortion affects geometric readings
At YISHANG, we don’t blindly accept technical drawings. Our pre-production reviews flag improper MMC applications and suggest alternatives, helping procurement teams avoid long-term inspection issues.
Buyers value this: it de-risks purchasing decisions and aligns factory inspection with design function.
Strategic Use: When Wholesale Projects Benefit from MMC
MMC is most effective in:
Mounting holes for brackets, PCB standoffs, or modular fixtures
Slot features that receive fasteners or guide pins
Datum references in multi-component assemblies
MMC is less effective when:
Surface appearance is a priority (e.g., front panels)
Tolerances drive user experience (e.g., handle alignment)
If you’re managing RFQs or transitioning a design to a new supplier, let our DFM support team review your tolerancing. We can offer refinements that reduce inspection ambiguity and improve process reliability across your global fulfillment chain.
FAQs: Answering Buyers’ Technical and Procurement Questions
Can YISHANG help optimize my drawings with MMC recommendations?
Yes. We routinely support buyers with tolerancing strategies during RFQ review and product introduction.
What QC documentation do you provide?
You’ll receive reports with MMC logic: actual dimensions, bonus tolerances, and compliance judgments. Certification for gauges is also available.
Does MMC reduce QA failure rates?
It can significantly reduce rejections, especially for parts with tight positional tolerances. One client in telecom hardware saw a 23% inspection pass-rate improvement.
How does MMC affect third-party inspection or CMM auditing?
Proper MMC application ensures wider acceptance within defined limits. Our CMM reports comply with standard GD&T protocols, including virtual condition assessment.
Final Thought: MMC Helps You Procure with Confidence
For purchasing professionals handling custom sheet metal, MMC is more than an engineering term. It’s a tool for reducing cost-per-unit, improving delivery consistency, and easing final assembly.
At YISHANG, we don’t just manufacture—we collaborate. Whether you’re sourcing for telecom enclosures or EV control boxes, our team ensures tolerances support function and scale.
Let’s make quality predictable. Reach out to our engineers today.