Quality Control Services for Metal Products
At YISHANG, quality control (QC) is the cornerstone of our metal fabrication services. With over 26 years of experience, we ensure that every product we deliver meets the highest standards. We understand the importance of delivering high-quality, reliable products on time. Our rigorous QC processes guarantee precision, performance, and efficiency, all while reducing costs and minimizing defects.
By applying a structured QC process, we help your business meet deadlines, lower production costs, and avoid costly errors.
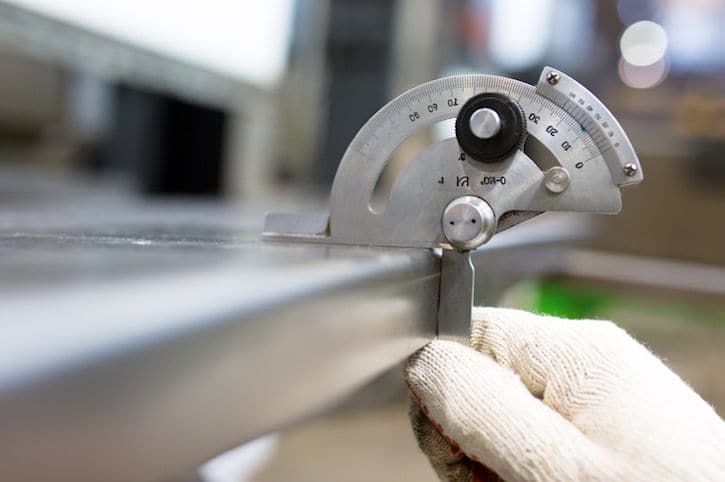
Our Quality Control Process
At YISHANG, we implement a three-phase QC system: IQC (Incoming Quality Control), IPQC (In-Process Quality Control), and OQC (Outgoing Quality Control). This ensures every part is manufactured with precision and meets the required specifications.
1. Incoming Quality Control (IQC)
Before production begins, we verify that all materials meet the necessary standards. This step ensures that only high-quality materials enter production, which reduces the risk of defects later in the process.
Material Certification: We verify that materials meet industry standards, ensuring that they are suitable for use.
Dimensional and Visual Inspections: Materials are inspected for defects and measured for accuracy before production starts.
Random Sampling: For larger orders, we conduct random tests to ensure the consistency of material quality.
By inspecting materials at the start, we eliminate potential issues before they affect production.
2. In-Process Quality Control (IPQC)
During production, we continuously monitor every stage to ensure that the process stays on track. We track key production parameters, perform regular inspections, and adjust the process as needed.
Real-Time Monitoring: Parameters such as temperature, pressure, and machine settings are continuously monitored during critical processes.
Operator Inspections: Regular visual and dimensional inspections ensure the product meets specifications throughout production.
Immediate Adjustments: Any discrepancies are corrected immediately, preventing defects from advancing further down the line.
This process ensures consistent quality while improving efficiency by catching potential issues early.
3. Outgoing Quality Control (OQC)
After production, we conduct a final inspection to confirm that the product meets customer specifications. The OQC process includes dimensional checks, performance testing, and aesthetic inspections.
Dimensional Verification: We use tools like CMMs to check the precision of every part.
Functional Testing: We test parts to ensure they meet functional requirements such as load-bearing capacity or heat resistance.
Surface Inspections: We check for any cosmetic defects to ensure the product is flawless.
Packaging Inspection: Finally, we ensure that the product is packaged securely to avoid damage during shipment.
Only after passing these checks do we approve the product for shipment.
How Quality Control Benefits Your Business
Our quality control process doesn’t just improve product quality—it also brings measurable benefits to your business operations:
1. Consistent Product Quality
Through our rigorous QC system, we ensure that every product is made to exact specifications, reducing variability and ensuring consistency across production runs. This is especially important for industries like automotive and aerospace, where precision is critical.
2. Cost Efficiency
Quality control helps minimize waste and rework, which reduces production costs. By catching defects early in the process, we prevent costly errors that could affect the entire production run, helping you save time and money.
3. Faster Production and Delivery
Our streamlined QC process ensures quicker turnaround times. By identifying potential issues early, we can resolve them quickly, preventing delays and ensuring that your products are delivered on time.
4. Risk Mitigation
QC reduces the risk of defects that could lead to failures, product recalls, or safety issues. By inspecting products at every stage, we ensure that every part meets the required safety and performance standards.
5. Regulatory Compliance
Our QC processes ensure that products meet necessary industry standards, including ISO 9001 and RoHS certifications. Compliance is critical in sectors such as aerospace, automotive, and medical devices, and we ensure that every product meets these requirements.
Why Choose YISHANG for Your Quality Control Needs
YISHANG offers more than just high-quality metal fabrication; we provide reliable solutions for your QC needs. Here’s why our services stand out:
Proven Expertise: With over 26 years of experience, we understand your needs and deliver solutions tailored to your industry.
ISO 9001 Certification: We adhere to internationally recognized quality management systems, ensuring reliable and consistent results.
Custom Solutions: We work closely with clients to develop QC plans tailored to their specific requirements.
Cost-Effective: Our efficient QC processes help reduce waste, improve production efficiency, and ultimately save costs.
Contact YISHANG Today
At YISHANG, we are committed to delivering high-quality, precision-driven metal parts. Contact us today to discuss how our quality control processes can streamline your manufacturing needs and ensure consistent, reliable results.