Sheet Metal Welding Service
At YISHANG, we don’t just provide welding services; we deliver precision, reliability, and unmatched expertise that help businesses achieve their goals. Our commitment to quality and our attention to detail have earned us a trusted reputation in various industries, including automotive, construction, and electronics.
Unparalleled Expertise: With over 26 years of experience, YISHANG specializes in delivering top-quality welding solutions, whether it’s MIG, TIG, or arc welding. Our skilled team ensures that each weld is clean, precise, and strong, meeting industry standards and exceeding customer expectations.
Custom Solutions for Every Project: We understand that no two projects are alike. That’s why we work closely with our clients to offer tailored welding solutions that align with their specific requirements. Whether you need a small batch of prototypes or large-scale production, YISHANG has the capacity and expertise to meet your needs.
Advanced Equipment for Superior Results: YISHANG uses the latest welding technologies and equipment, ensuring a flawless finish and consistent results across every project. This commitment to state-of-the-art tools gives us the ability to handle even the most complex welding tasks with precision.
What Is Sheet Metal Welding?

Sheet metal welding is the process of joining thin metal sheets using heat, pressure, or both to create strong, durable bonds. Unlike thicker metals, welding sheet metal requires precise control to prevent warping and maintain material integrity.
This technique often involves a filler material, which melts and fills gaps between metal pieces to form a seamless, strong connection.
Used in industries like automotive, aerospace, and construction, sheet metal welding enables the creation of complex, lightweight, and robust assemblies critical for both structural and aesthetic purposes.
Methods Of Welding Sheet Metal
Now, let’s take a comprehensive look at some methods for melding metal sheets.
1.MIG Welding
MIG welding, or Gas Metal Arc Welding (GMAW), is a versatile and efficient welding process using a continuous wire electrode and a shielding gas to prevent oxidation.
Ideal for joining metals like steel, aluminum, and stainless steel, MIG welding creates strong, high-quality welds quickly. Its speed and adaptability make it perfect for larger and thicker sheet metals, commonly used in industries like automotive and construction.
While it offers excellent weld strength, controlling the weld puddle can be challenging, leading to imprecise results without proper skill.

2.TIG Welding

TIG welding, or Gas Tungsten Arc Welding (GTAW), uses a non-consumable tungsten electrode to produce precise, high-quality welds.
Unlike MIG welding, the electrode doesn’t melt; instead, filler metal is manually fed into the weld. This method offers superior control, making it ideal for thin metals and projects requiring clean, strong welds with minimal distortion.
Although slower and more skill-intensive than MIG, TIG welding excels in applications like aerospace, automotive, and custom fabrication due to its precision and reduced heat output.
3.Stick Welding
Stick welding, also known as Shielded Metal Arc Welding (SMAW), uses a consumable electrode coated in flux. As the flux burns, it creates a gas shield that protects the weld from contamination, eliminating the need for external shielding gas.
Unlike TIG or MIG, stick welding is versatile and works well on rough, dirty, or rusty materials, making it ideal for outdoor and heavy-duty applications like construction and shipbuilding.
Its portability and ability to handle tough metals like iron and steel set it apart from other welding methods.
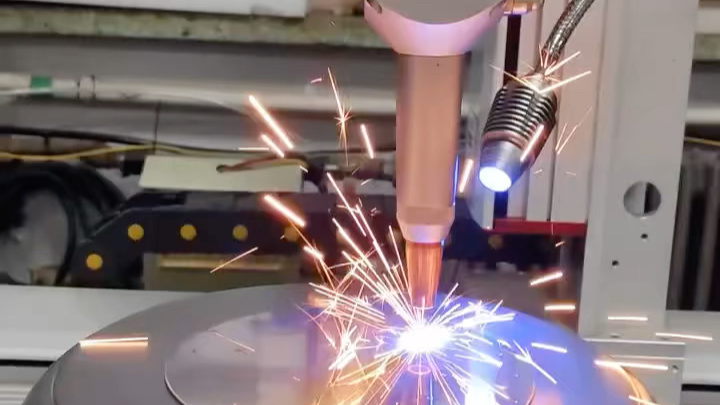
4.Plasma Arc Welding
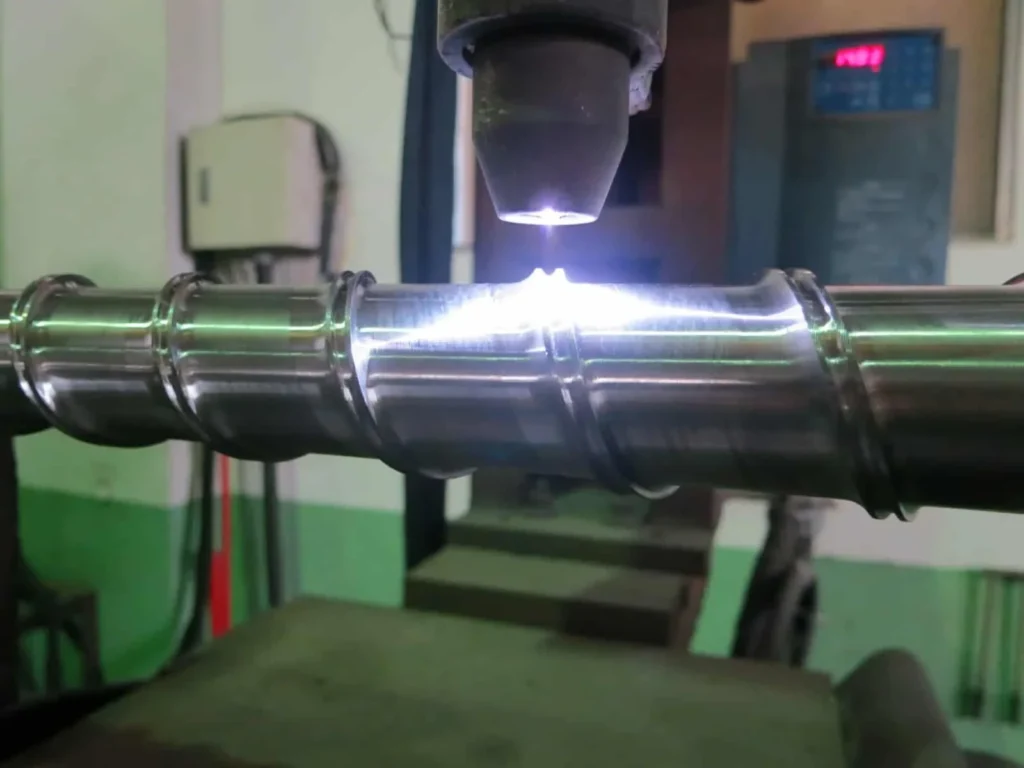
Plasma Arc Welding (PAW) is similar to TIG welding but uses a highly concentrated plasma arc, allowing for deep penetration and precise welds.
Unlike other methods, PAW utilizes pressurized gas to form a hot plasma, melting metals together with minimal heat-affected zones. This precision makes PAW ideal for industries like aerospace and marine.
Unlike TIG, it operates faster and does not require filler materials, producing high-quality welds with less finishing. PAW’s ability to focus energy in small areas sets it apart from other welding techniques.
5.Laser welding
Laser welding uses a concentrated laser beam to melt and fuse materials with high precision, allowing for deep, narrow welds and minimal distortion.
Laser welding includes two primary types: cosmetic (or conduction) and keyhole. The cosmetic weld uses a defocused laser to create a smooth, wide seam.
In contrast, the keyhole weld penetrates through the first layer into the second, forming a strong joint as the molten material solidifies. Keyhole welding is chosen for applications requiring a secure seal rather than a smooth appearance.
Unlike TIG and MIG welding, it requires no filler material, making it ideal for smaller parts and tight gaps under .005”.
This method is fast, offering speeds up to 80” per minute, and is commonly used in industries like medical devices, electronics, and automotive manufacturing, where accuracy and aesthetics are critical. Its high energy density and minimal heat input set it apart from traditional welding methods.

6.Gas Welding

Gas welding, also known as oxy-fuel welding, uses a torch to mix gases like oxygen and acetylene to create a high-temperature flame that melts metals for joining.
This method is highly portable and does not require electricity, making it economical and versatile for both ferrous and non-ferrous metals.
Unlike more modern techniques, gas welding can be slower and less precise but is valued for its simplicity and effectiveness in tasks like pipe welding and repairs.
It excels in applications where gradual heating and cooling are needed but falls short of the high temperatures achievable with methods like arc welding.
7.Spot welding
Spot welding(or resistance welding)joins metal sheets by applying pressure and localized heat through copper electrodes. This method generates intense heat through electrical resistance, creating small weld pools at specific points.
Unlike MIG or TIG welding, which involve continuous welding, spot welding is ideal for high-volume production with minimal warping.
It’s particularly effective in automotive manufacturing, offering robust, permanent joints without the need for filler materials.

Consider Surface When Choosing Sheet Metal Welding Methods

When selecting a sheet metal welding method, surface considerations play a crucial role. Key factors include:
Surface Cleanliness: Methods like TIG welding require clean surfaces for optimal weld quality, while MIG welding is more forgiving of surface impurities.
Surface Coating: Coated metals may need specialized processes like laser welding to avoid damage to the coating, ensuring the final product retains its finish.
Material Thickness: Thinner materials are more prone to distortion, so low-heat methods like resistance welding are preferable to minimize surface warping.
Oxidation Resistance: Some metals are prone to oxidation during welding, requiring protective gases like argon in processes such as TIG or MIG welding to preserve the surface quality.
Considering surface characteristics helps in selecting the most appropriate welding method for durable and high-quality results.
Sheet Metal Welding Tips You Should Know
Welding sheet metal requires precision and proper techniques to achieve strong, clean welds. Here are some essential tips to ensure high-quality results:
Choose the Right Welding Process
Each metal type requires a specific welding process. MIG is faster and suitable for thick materials, while TIG ensures precision and clean welds for thinner metals like aluminum.
Choose the Right Welding Process
Each metal type requires a specific welding process. MIG is faster and suitable for thick materials, while TIG ensures precision and clean welds for thinner metals like aluminum.
Select the Proper Filler Metal
The filler metal should match the base metal in strength and composition. A thinner filler is preferred for sheet metal to reduce the risk of overheating and distortion.
Control the Heat
Managing heat is critical for preventing distortion. Skip or tack welding minimizes overheating, while using backing bars and pulse techniques helps dissipate excess
Ensure Surface Cleanliness
Contaminants like oil or rust can weaken weld quality. Clean the workpiece of oils, oxides, and debris before welding to avoid defects like porosity or lack of fusion in your weld.
Employ Proper Fixturing
Clamps, jigs, and backing bars stabilize the metal during welding. This reduces movement, ensures alignment, and aids in even heat distribution for consistent weld quality.
Choose a Small Wire Diameter
When using MIG welding, select a small wire diameter for better control and to minimize spatter. Smaller wires also reduce heat input, improving weld quality on thinner sheet metal.
Test and Adjust Settings
Always test your welding technique on scrap metal before starting production. Adjust heat, wire speed, and shielding gas for the best results, ensuring you minimize defects.
By following these tips, you’ll improve your sheet metal welding outcomes, ensuring strong, durable welds suitable for various applications.
The Benefits of Professional Welding Services
Choosing the right welding service provider is essential for ensuring that your parts and products are durable, functional, and of the highest quality. Here’s why working with YISHANG gives you a competitive edge:
Enhanced Durability: Our expert welding services create strong, long-lasting joints that stand up to the demands of harsh environments and high-stress applications.
Cost-Effective Manufacturing: By optimizing welding processes, we minimize waste, reduce rework, and keep production costs low while maintaining high-quality standards. This makes YISHANG a smart choice for companies seeking efficient and cost-effective solutions.
Customization and Flexibility: Whether you need intricate, detailed welds or simple, sturdy connections, our welding services can be customized to fit your specific design and material requirements. We provide the flexibility to create parts and products that match your exact specifications.
Conclusion
Looking for expert sheet metal welding services? Whether you’re tackling a DIY project or need professional help, YISHANG offers top-notch solutions.From precise laser cutting to custom welding, our skilled team is here to bring your vision to life.
Choose YISHANG for quality, reliability, and exceptional results.