The Strategic Role of Sheet Metal Covers
Sheet metal covers directly affect product performance, compliance, and longevity. For wholesale buyers, they influence maintenance costs, warranty rates, and approvals.
Functional and Procurement Value
Precision housings offer structural integrity, EMI shielding, and RoHS/CE compliance—vital in energy systems, vending units, and medical devices. Certified suppliers help reduce lead times and lifecycle costs. Used in telecom hardware, kiosks, battery systems, and control panels, sheet metal covers support scalable production across industries.
From Design Fit to Prototyping: Ensuring System Integration
Covers must support wiring, airflow, mounting, and maintenance access, seamlessly integrating with the product’s structure.
Design Fit & Engineering Collaboration
Suppliers should anticipate part fit, heat paths, and mechanical loads. Early manufacturability input (DFM) reduces revisions. For example, one telecom client resolved mounting conflicts during review, preventing post-production rework.

Prototype-to-Production Continuity
Using the same equipment for prototyping and production ensures form and function remain consistent across phases. This accelerates validation and reduces transition risk.
Material Strategy Based on Use Environment
Choosing the right material affects product cost, durability, and compliance. Buyers should evaluate both structural and environmental requirements.
Application-Based Material Matching
Aluminum: Lightweight and conductive—ideal for EV battery trays and telecom modules.
304 Stainless: Resists corrosion; widely used in kiosks and enclosures.
316L Stainless: For salt-laden or chemically aggressive settings (marine, medical).
Galvanized Steel: Economical for indoor/low-exposure installations.
Copper/Brass: Premium conductivity and finish; for panels, terminals, or visible parts.
Material | Core Benefits | Best Use Cases |
---|---|---|
SS 304 | Corrosion resistant, strong | Kiosks, cabinets |
SS 316L | Marine-grade durability | Medical, marine hardware |
Galvanized Steel | Cost-effective | HVAC, server trays |
Aluminum | Lightweight, conductive | Battery, telecom enclosures |
Copper/Brass | Aesthetic, conductive | Control panels |
Quality Execution at Production Scale
Consistency, traceability, and tolerances define production quality. Especially in high-volume or regulated sectors, quality gaps can result in costly failures.
Design Optimization for Manufacturing
Design for Manufacturing (DFM) reviews resolve conflicts before tooling. In one case, adjusting fastener spacing improved throughput by 8%.
Fabrication Tolerances That Reduce Assembly Time
YISHANG uses ±0.1 mm laser cutting and ±0.2° bending, reducing alignment errors in assemblies and supporting precision sheet metal products.
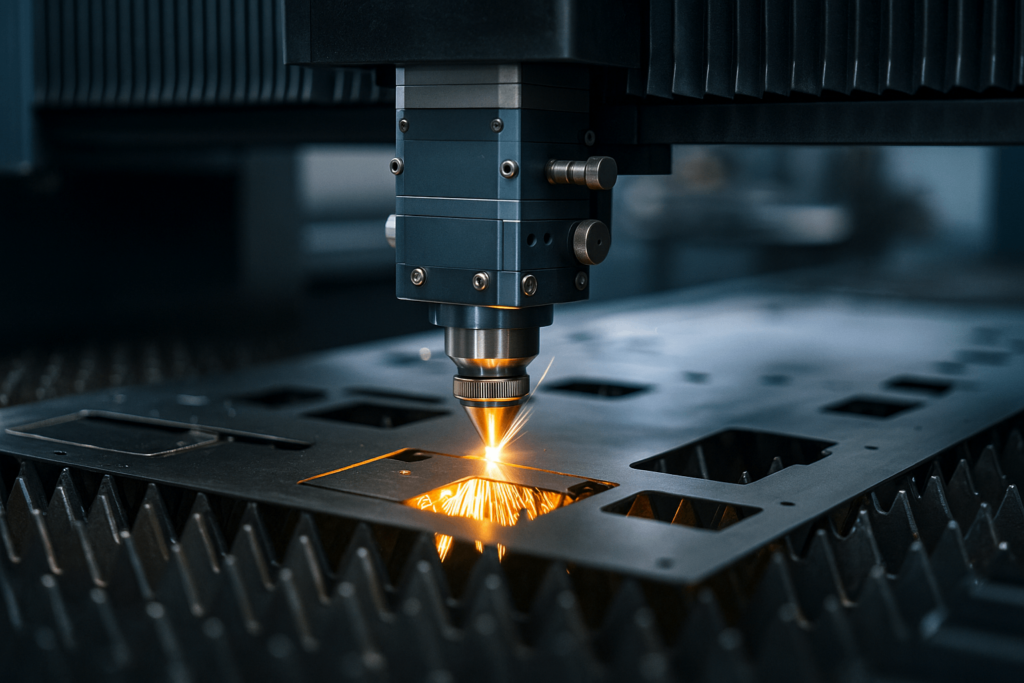
Surface Treatment & Regulatory Assurance
All finishes are RoHS-compliant, with coating durability validated by ISO 9227 salt spray testing. This ensures long-term corrosion resistance and audit compliance.
Stage | Tolerance/Standard | Buyer Benefit |
Cutting | ±0.1 mm | Repeatable accuracy |
Bending | ±0.2° | Tight assembly fit |
Welding | Structural & cosmetic | Lower labor cost |
Coating | Salt spray >500h | Extended lifespan |
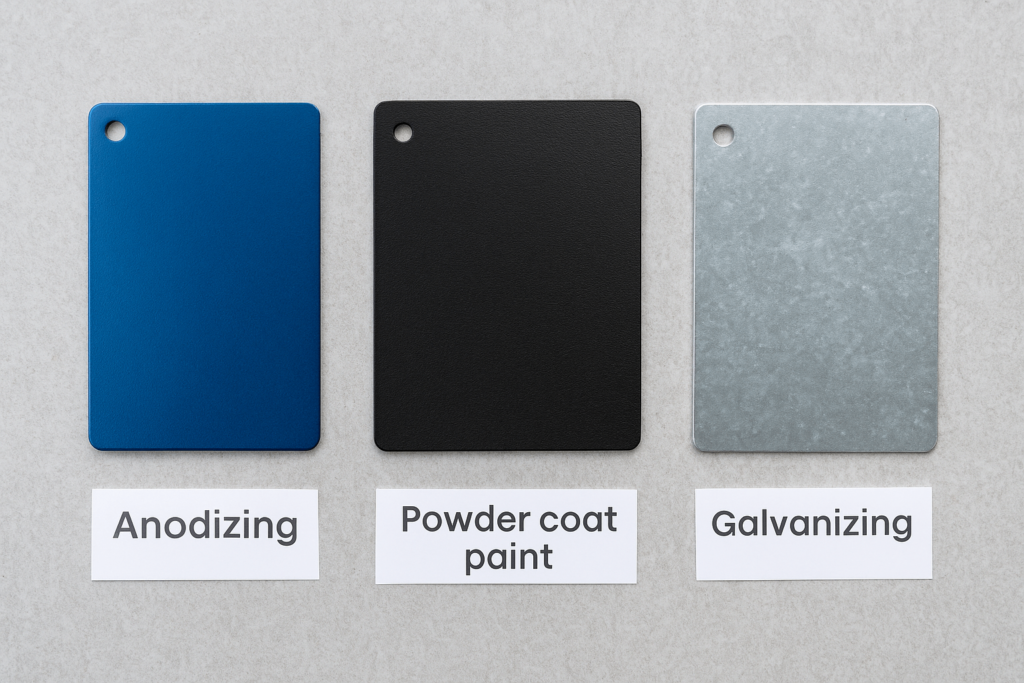
Maintaining Consistency in Volume Batches
Across telecom, energy storage, and kiosk sectors, consistent fit and finish reduce inspection time and ensure interoperability between units.
Common Procurement Pitfalls and How to Avoid Them
Thermal or Ventilation Oversights
Ignoring airflow in sealed enclosures leads to thermal throttling or component failure. Add passive vents, perforations, or fan mounts during early design.
Mounting Incompatibilities & Finish Misalignments
Misaligned brackets or under-specified coatings are major delay factors. Define installation environment early and validate via 3D model fitting or mockups.
Supplier Partnership Beyond Just Manufacturing
Choosing a supplier that supports you through planning, forecasting, and compliance improves speed-to-market and lowers risk.
CAD-to-Production Workflow Integration
YISHANG offers review-ready CAD input formats and feedback loops, ensuring seamless transition from digital file to finished product.

Volume Planning & Compliance Alignment
With blanket orders and rolling forecasts, we stabilize lead times. ISO 9001 systems and full batch traceability support third-party audits and internal QA.
FAQ – Technical Questions from Buyers
Q: What is the minimum bend radius for stainless steel 304 sheet metal?
A: Typically 1 to 1.5x sheet thickness, based on tooling and grain.
Q: Can aluminum enclosures be used outdoors without powder coating?
A: Not recommended. Aluminum oxidizes—protective coatings extend life.
Q: What are tolerance standards for CNC-formed sheet metal parts?
A: ±0.1 mm for cutting, ±0.2° for bending. Custom options available.
Q: How long does prototyping take?
A: Most parts require 3–7 days. Complex designs may take up to 10.
Q: Do you offer RoHS-compliant finishes?
A: Yes—powder coating, anodizing, and zinc plating included.
Selecting the Right Supplier Affects the Entire Product Lifecycle
Your sheet metal partner impacts quality, cost, and delivery. YISHANG combines design review, QA control, and global compliance—delivering long-term value.
Planning your next enclosure build? Connect with YISHANG’s team and scale with confidence.