The Invisible Backbone: Why Tolerance Isn’t Just a Number
Defining the Role of Tolerance in Engineering
In precision manufacturing, no part is truly perfect. Every component carries a small but critical margin of error—commonly known as engineering tolerance. This allowable variation in a physical dimension is not a defect but an intentional, controlled parameter.
For those unfamiliar, what is tolerance in engineering? It’s the functional boundary that allows design to meet production realities. Without tolerance, even advanced machines would struggle to produce interchangeable, mass-manufactured components.
Why It Matters to Global OEM Buyers
For overseas buyers sourcing metal enclosures or structural parts, understanding tolerance is essential. Even a 0.1 mm deviation can affect assembly compatibility, product lifespan, or cost.
In custom fabrication and large-scale production, tighter tolerances require specialized tools, complex setups, and longer lead times. At YISHANG, we help OEM clients define functional tolerance zones to ensure manufacturability and avoid unnecessary cost drivers.
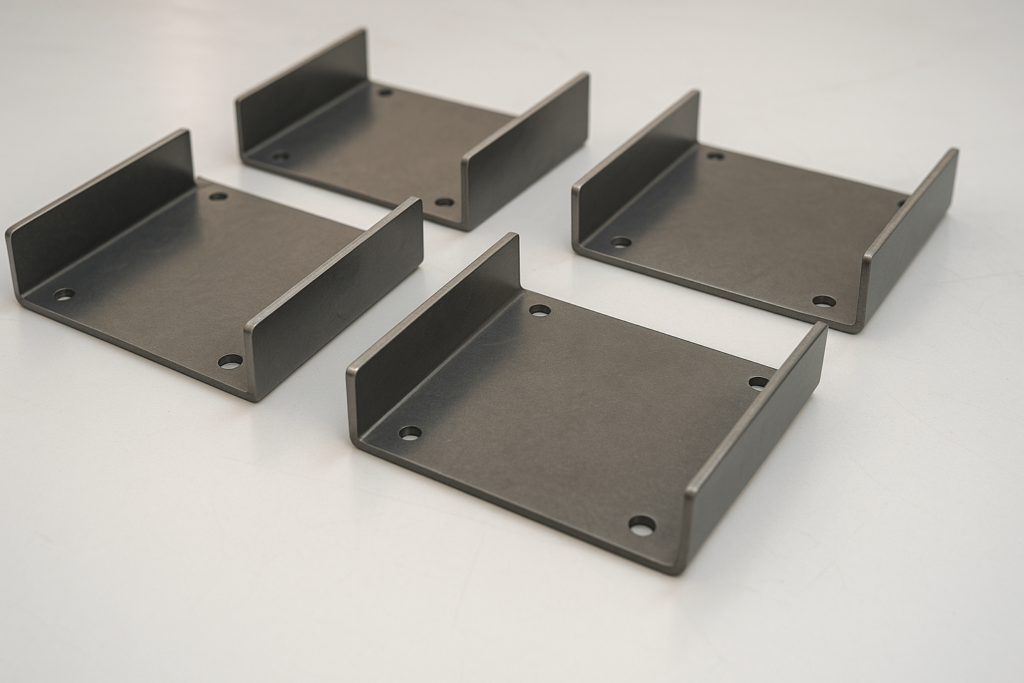
Engineering Tolerance Is a Language—But Who’s Reading It?
Tolerance communicates acceptability. When used clearly, it enables quality and consistency. When vague, it leads to rework and disputes.
Cross-Border Sourcing Challenges
Overseas projects often involve varied standards—ISO, ASME, and local specs. Unclear tolerance calls, especially in bilateral tolerancing, often result in misalignment or scrap.
Communication Breakdown Risks
Many quality issues stem from ambiguous tolerancing. Early engagement between engineering and suppliers helps prevent tolerance oversights. Context beats over-specification.
Digital Engineering Workflow Enhancements
CAD-integrated tolerance models (Model-Based Definition) reduce misinterpretation and streamline CNC programming. For buyers, this shortens development cycles and improves sourcing reliability.
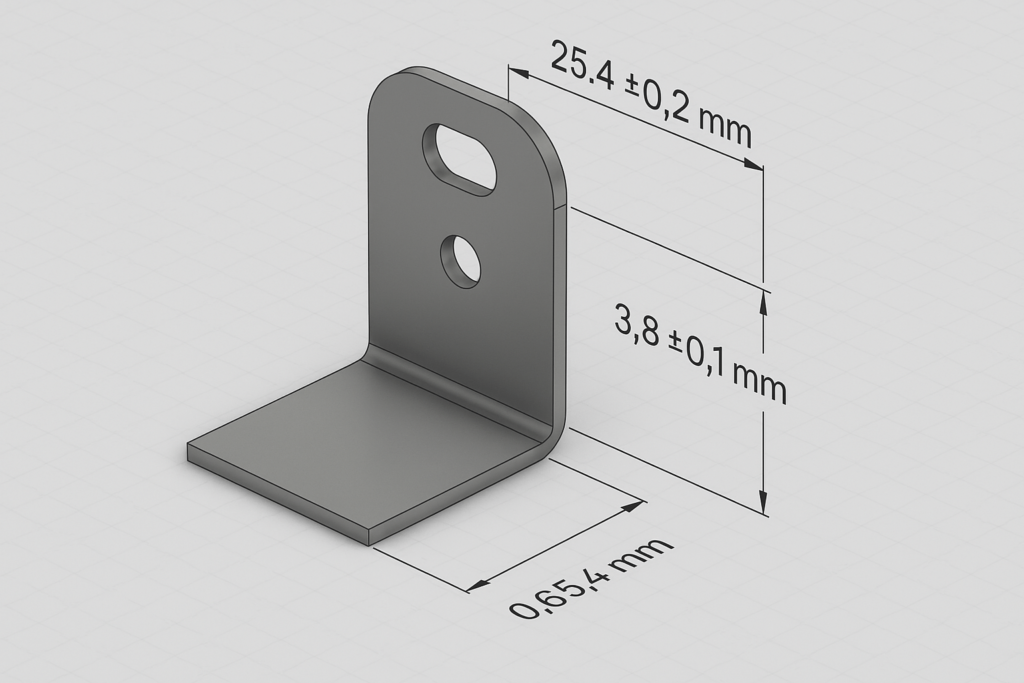
Types of Tolerances Are Not Categories—They’re Constraints
Functional Tolerances: Precision Where It Matters
Functional tolerances control features that affect fit, motion, or structural integrity. A hinge misaligned by 0.2 mm can misplace an enclosure door.
Critical features may demand tight controls like ±0.01 mm, but applying this level of tolerance universally inflates cost and restricts supplier choice. Buyers should assess whether such precision is essential for each design feature.
OEM buyers benefit from tolerance feasibility analysis—like whether a 0.1 mm flatness across a meter-wide frame is realistic using sheet metal fabrication.
What OEM Buyers Should Know About Tolerances
Confirm standards like ISO 2768 or ASME Y14.5 before quoting
Differentiate cosmetic and functional features
Evaluate tolerance-driven cost impact during DFM
Avoid defaulting to “tightest possible” specs
Dimensional and Geometric Tolerances: Specifying What Matters
Linear vs Spatial Control
Linear tolerances govern size. Geometric tolerances (GD&T) manage form and position. Both matter—especially in mating parts.
GD&T in Real-World Applications
A bolt hole within ±0.2 mm diameter tolerance may still fail if the position isn’t controlled. GD&T helps ensure form compatibility beyond mere dimensions.
YISHANG supports converting drawings into practical tolerancing frameworks based on production method and fit requirement.
Stack-Up and Fits: Understanding Assembly Realities
Stack-Up Risk Factors
Tolerance stack-up in multi-part assemblies often creates compounding errors. An accumulated 0.5 mm deviation can result in failure for tight-fit components.
ISO Fits and Sourcing Precision
Fits like H7/g6 define how parts interact. Specifying these correctly avoids friction fits where clearance fits are needed—or vice versa.
Over-specifying reduces manufacturability. Use functional fit tolerances to keep your RFQ aligned with real supplier capabilities.
The Cost Equation: How Tolerance Impacts Budget and Lead Time
Why Tighter Tolerances Cost More
Reducing a tolerance from ±0.2 mm to ±0.01 mm can increase production cost significantly. Processes like EDM or surface grinding may be required.
Laser cutting supports ±0.1 mm efficiently. Stricter tolerances require specialized setups, slowing lead times and raising QA costs.
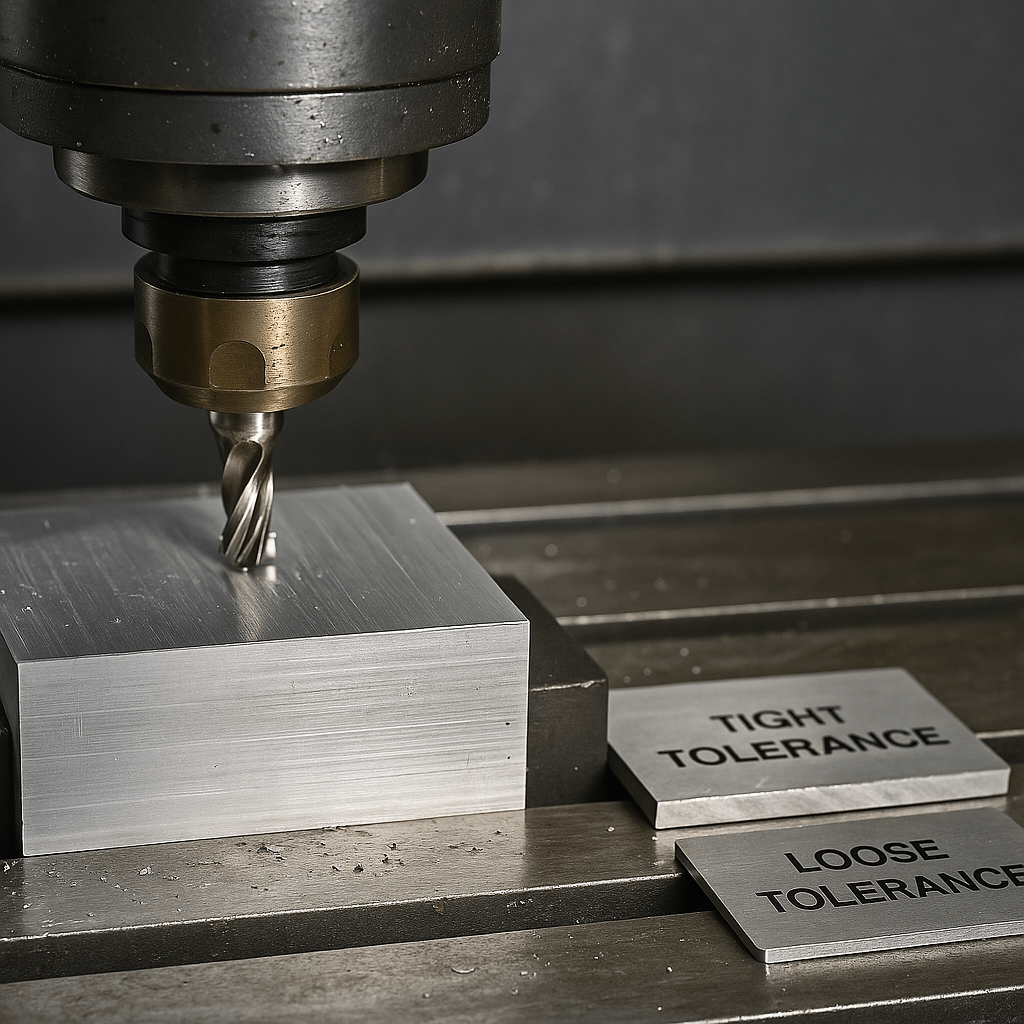
Smart Cost Trade-Offs in Procurement
Don’t pay for precision that doesn’t impact performance. Relaxing flatness from 0.15 mm to 0.4 mm on a kiosk enclosure saved one client 23%—with no functional loss.
Base tolerance targets on functionality. Over-tightening specs inflates machining, inspection, and scrap costs.
Tolerance Errors and Their Impact on Procurement & Delivery
Risks of Undetected Tolerance Deviations
Minor misalignments during fabrication can trigger significant downstream issues—especially in modular assemblies or final-stage QA.
Aligning RFQ Specifications with Capabilities
Define tolerance zones clearly in your RFQ. Ambiguity increases supplier rejection risk and delays. For assemblies with mating parts, tolerance callouts should be paired with inspection expectations.
Reviewing these early reduces post-sampling surprises and helps qualify vendors effectively.
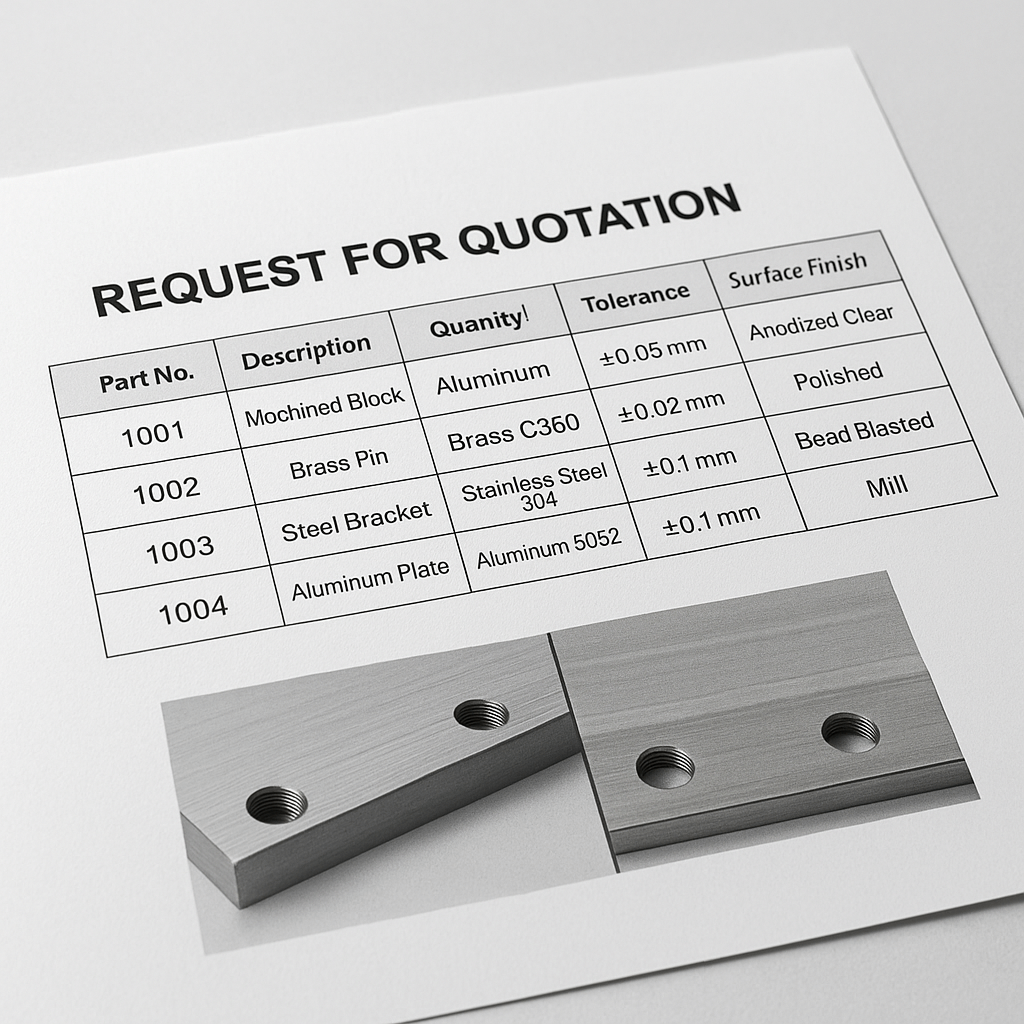
Industry-Based Tolerance Requirements: No One-Size-Fits-All
Precision Expectations by Sector
Medical and instrumentation often require ±0.01 mm or better. HVAC frames or energy storage boxes may operate well within ±0.5 mm.
Let sector expectations guide tolerance decisions—avoiding both overengineering and under-control risks.
Use-Case Optimization
For agricultural panels, alignment may matter more than appearance. For POS kiosks, cosmetic fit takes precedence. The key is matching tolerance to function.
This is where tolerance consultation pays off—balancing appearance, assembly, and cost.
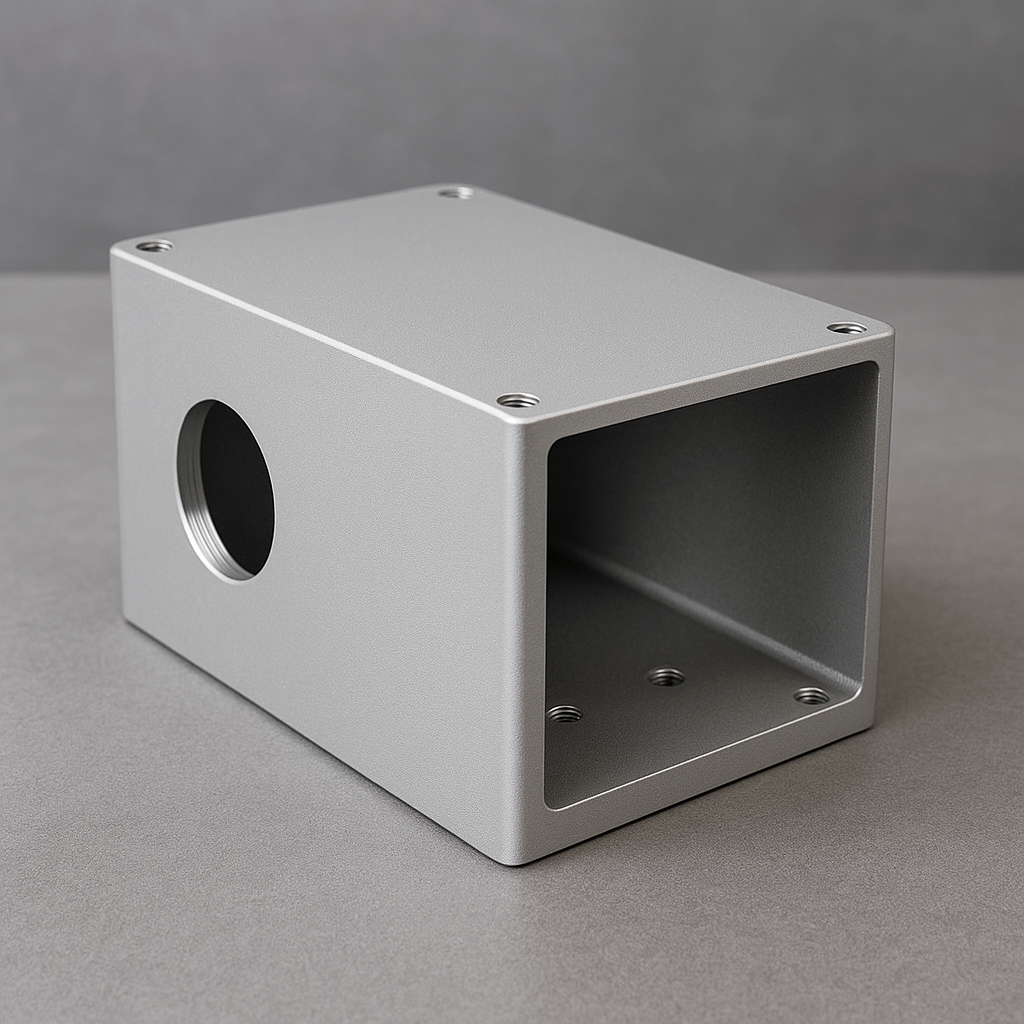
Digital Tools and Smart Tolerance Optimization
CAD and Stack-Up Simulation
Tools like tolerance stack-up analysis help visualize how dimensional variation accumulates across assemblies. These reduce uncertainty before production.
Data-Driven RFQ Preparation
Modern platforms enable tolerance feasibility checks and cost modeling. When requesting CNC parts or custom metal boxes, embedding tolerance insights in the RFQ results in more accurate pricing and lead times.
Early simulations reduce over-tolerancing—a common RFQ pitfall.
Final Thoughts: From Print to Production, Tolerance Drives Results
From Design to Supply Chain
Tolerance influences yield, lead time, and QA—not just part fit. In volume production, even minor misalignment can compound into systemic cost.
Buyer’s Role in Tolerance Planning
Rather than default to conservative specs, collaborate with your supplier to define achievable and functional tolerance bands.
YISHANG partners with OEM clients from drawing optimization through delivery to align engineering with manufacturing realities.
Need guidance defining tolerances in your next RFQ? Contact YISHANG for expert support.