In power electronics, industrial systems, and energy storage products, heat build-up is one of the most common causes of system instability. For OEMs, integrators, and bulk buyers, choosing the right heat sink is not just a thermal decision—it’s a strategic one.
This guide provides a comprehensive yet practical look at heat sinks: how they work, how they’re manufactured, and what purchasing professionals should evaluate. Whether you’re sourcing passive extruded heat sinks or custom skived profiles for high-power modules, YISHANG supports thermal solutions engineered to your needs.
Why Heat Sinks Matter in Thermal Management
A heat sink is a component designed to absorb and dissipate heat from active devices like IGBTs, MOSFETs, or LED chips. It works passively—meaning it does not require power—yet it’s a critical enabler of system reliability.
When not managed properly, thermal accumulation causes issues like derating, signal distortion, and physical damage. A typical power transistor loses 50% of its operating life for every 10°C increase above its rated junction temperature. The right heat sink reduces thermal resistance, allowing heat to flow efficiently away from components.
For bulk procurement professionals, understanding the function is important, but understanding performance outcomes is essential. Think lifespan extension, device stability, and reduced failure rates.
How Heat Sinks Work: A Quick Primer
Understanding how a heat sink works helps in making better sourcing choices. Three principles govern the process: conduction, convection, and radiation.
Conduction transfers heat from the component into the heat sink base. Materials like aluminum and copper are commonly used because of their high thermal conductivity. TIM (thermal interface material) further enhances this contact.
Convection occurs when heat is carried from the heat sink to the air. Fins increase surface area, allowing air movement—either natural or forced—to remove heat more effectively.
Radiation, though minor, also contributes. Finishes like black anodizing increase emissivity, enhancing heat dissipation in enclosed or low-airflow applications.
For buyers evaluating technical sheets, ask about simulated airflow, mounting orientation, and surface treatment—all of which impact the real-world performance of the heat sink.
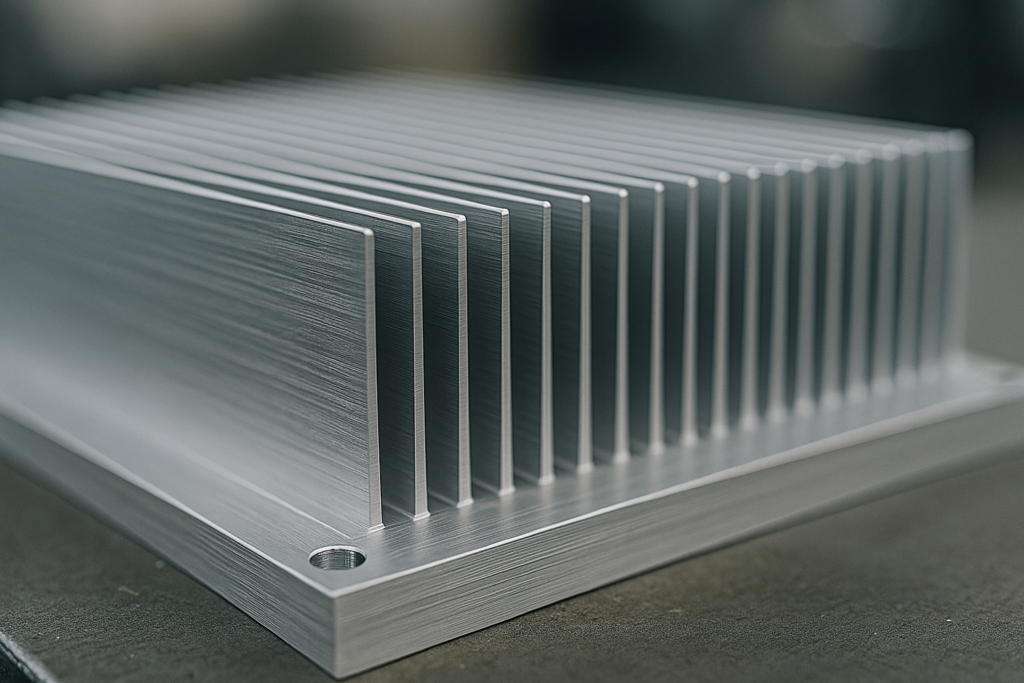
Heat Sink Types and Application Fit
The most effective thermal solutions align product characteristics with the operating environment. Let’s look at heat sink types in terms of their practicality for sourcing.
Passive heat sinks use natural airflow, are silent, and have no moving parts. They’re preferred in sealed or compact environments where simplicity and long-term reliability matter.
Active heat sinks include fans and require power. They provide better heat dissipation, ideal for high-wattage CPUs or power inverters, but come with added noise, power draw, and maintenance.
Other construction-specific types include:
Extruded aluminum heat sinks — widely used and cost-effective for mass production
Skived fin heat sinks — higher performance in compact spaces
Bonded or folded fin sinks — modular, often used in telecommunication systems
Vapor chamber heat sinks — for uniform temperature distribution in dense systems
Each type supports different thermal loads, airflow environments, and price points. A sourcing decision should factor in wattage, footprint, airflow access, and certification requirements. If you’re searching for bulk aluminum heat sinks for inverters or compact passive models for telecom, matching the sink type to the application is crucial.
What Materials Matter to Buyers
Material selection isn’t just an engineering concern—it directly affects procurement cost, weight in logistics, and certification paths.
Material | Thermal Conductivity (W/m·K) | Density (g/cm3) | Cost Level | Notes |
---|---|---|---|---|
Aluminum | ~200 | 2.7 | Medium | Common, lightweight, anodizable |
Copper | ~400 | 8.96 | High | Superior conduction, heavy |
Graphite | 150-500 (anisotropic) | <2.0 | High | For specialized designs |
Ceramic | 20-30 | 3.2-3.8 | Medium | Electrically insulating |
Aluminum (6061 or 6063) remains the most procured material for large-scale heat sink production. It balances cost, weight, corrosion resistance, and ease of fabrication.
For higher-performance modules, copper or hybrid sinks (copper base + aluminum fins) are often specified. YISHANG supports both types and can advise based on application. As a heat sink manufacturer with low MOQ and full material flexibility, we assist B2B buyers from concept to bulk delivery.
Manufacturing Methods and What They Mean for Procurement
Understanding how heat sinks are made helps evaluate cost, tooling, and lead time. Here’s how each method aligns with purchasing considerations:
Extrusion: Most common. Best for high volumes, standard shapes, and quick turnaround. Low mold cost. YISHANG maintains 60+ existing extrusion dies.
Skiving: No bonding; higher fin density. Strong option for compact, high-efficiency designs like EV inverters. Slightly higher per-unit cost. Looking for an OEM skived heat sinks supplier? This method supports small batches and consistent quality.
Bonded Fin: Modular. Allows taller fins and mixed materials. Used in telecom or energy storage systems. Good when extrusion limits design.
CNC Machining: High precision. Low-volume or prototype runs. Great for unique geometries or small batch OEM projects.
Die Casting & 3D Printing: Suitable for intricate shapes. Often used in high-end power products. Requires longer lead time and higher tooling.
Knowing the trade-offs helps buyers negotiate better terms and forecast production schedules.
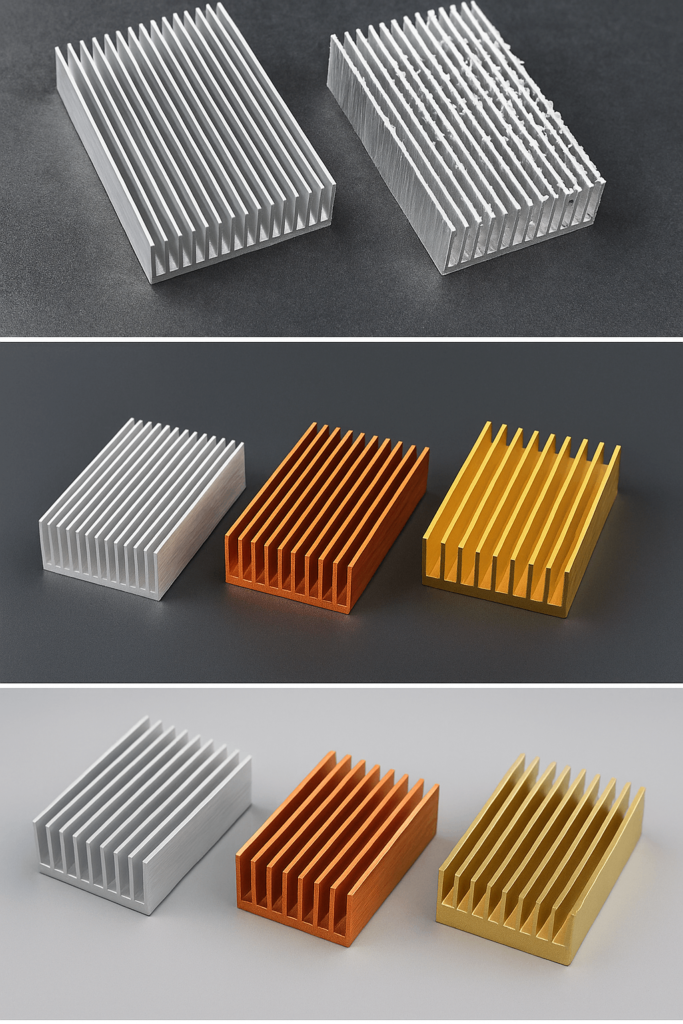
Heat Sink Performance: What to Look For
Buyers should look beyond datasheet numbers and understand how heat sinks perform in real use.
Thermal resistance (°C/W) is the key spec. It shows how much temperature rise occurs per watt of heat load. Lower values are better.
Real-world factors affecting performance:
Ambient airflow and fin orientation
TIM selection and mounting pressure
Enclosure constraints (is it sealed or ventilated?)
At YISHANG, we support CFD simulation for airflow modeling and thermal imaging validation for custom parts. This ensures what you source performs as expected in your application.
Interface Materials and Mounting Methods
Incorrect installation reduces thermal transfer. Interface materials and mounting approach must be specified clearly.
TIMs (thermal pads, pastes, phase-change materials) fill air gaps and increase conduction. For batch production, pre-applied pads help reduce assembly labor.
Mounting types:
Push pins and spring clips (tool-free assembly)
Screwed brackets (rigid and secure)
Adhesive pads (small, low-power devices)
YISHANG offers heat sinks with or without pre-mounted TIMs and supports custom mounting bracket integration.
What Procurement Teams Should Prioritize
When sourcing heat sinks for OEM projects, it’s not just about specs—it’s about fit, volume, reliability, and integration. Key points include:
MOQ Flexibility: Can you prototype first?
Production Capacity: Can your vendor deliver 10K+ units/month reliably?
Surface Finish Options: Anodized? Powder coated? Custom colors?
Certifications: ISO 9001, RoHS, REACH compliance
As a heat sink factory in China with full in-house sheet metal capabilities, YISHANG delivers scalable quality and fast prototyping support. We are proud to serve as an Asia-based heat sink OEM partner trusted by B2B buyers worldwide.
Case Studies: Solutions That Delivered Results
Power Inverter: A 70 kW inverter in Germany faced thermal shutdowns. After switching to a skived + extruded sink from YISHANG, failures dropped by 22%. We produced 5,000 units monthly with black anodizing.
EV BMS System: A North American EV startup needed passive cooling in a tight 32 mm height. YISHANG’s CNC-machined copper/aluminum hybrid solution reduced module temperatures by 11°C.
Consumer SSD: A client required passive heat sinks for high-speed SSDs. Our extruded and anodized profiles dropped idle temps by 9°C. Delivered within 14 days.
Why B2B Buyers Choose YISHANG
26+ years in precision sheet metal & thermal fabrication
Factory: 10,000 m² production area with full in-house processes
Exporting to 50+ countries across automotive, telecom, medical, energy
One-stop OEM/ODM services from design to packaging
ISO 9001 and RoHS certified with dedicated QA team
We support fast sampling, reliable lead times, and collaborative engineering. From custom design to volume fulfillment, YISHANG is built for B2B success.
Conclusion
Heat sinks are not commodity parts—they’re precision components that directly impact performance, reliability, and cost of your electronic systems.
Understanding how a heat sink works, what types exist, and how to align specifications with real-world performance gives OEM buyers a significant sourcing edge.
Whether you’re quoting 500 or 50,000 units, YISHANG delivers the experience, capacity, and support to match your thermal management needs.
Looking for a reliable supplier of high-performance heat sinks? Contact YISHANG today to request a quote or start your custom project.