Cutting stainless steel isn’t about tools—it’s about consistency, material behavior, and downstream finish. Whether you’re sourcing 12,000 precision-cut vending machine panels or low-volume brackets for EV enclosures, the cutting method you specify affects tolerances, surface condition, and your entire QA pipeline.
This guide walks you through how industrial buyers should think about cutting stainless steel—beyond just “how to cut stainless steel sheet metal” or “how to cut stainless steel pipe”—from a supply chain and quality perspective.
Why Stainless Steel Is Different from “Steel”
Let’s address the search intent head-on: what is the difference between steel and stainless steel? Stainless steel isn’t just steel with shine. It’s alloyed (usually with chromium, sometimes molybdenum or nickel) to resist corrosion. That affects how it behaves when you cut it.
Harder, work-hardens faster: especially 300-series grades like 304 and 316.
Conducts heat poorly: heat builds up faster during mechanical or thermal cutting.
Has different edge oxidation behavior: especially critical for medical or visible parts.
Compared to mild steel, stainless dulls blades faster, is more prone to edge discoloration, and requires tighter thermal management. That’s why cutting stainless steel can’t be a generic process—it has to be tailored.
Not All Stainless Steel Is Equal
The cutting approach changes depending on grade, gauge, and surface finish requirements. Let’s break it down:
Stainless Steel Grade | Typical Application | Cutting Impact |
---|---|---|
304 | General-purpose industrial | Easier to cut than 316, less corrosion resistant |
316 | Marine, food, medical | More corrosion-resistant, work-hardens quicker |
430 | Decorative, appliance | Ferritic; magnetic; can warp under heat |
316L | Welded structures, medical | Lower carbon; slower feed rates to avoid warping |
Cutting methods must be adjusted for each type. For example, 316 stainless steel requires better cooling during laser cutting due to its heat sensitivity.
✅ Bonus insight: Looking to powder coat stainless steel? You’ll need a cleaner cut edge and tight prep. Yes, stainless can be powder coated—but prep determines durability.
The Real Decision Tree for Cutting Stainless Steel
Most articles ask: “how do you cut stainless steel?” But that’s not the right question for industrial buyers.
Instead, ask:
What’s the part’s function? (Decorative vs. structural)
What’s the required tolerance? (±0.2mm? ±0.05mm?)
What’s the volume? (Prototypes? Batches of 10,000?)
What happens after cutting? (Bending? Welding? Anodizing?)
Each answer eliminates methods. If you’re cutting 1mm 304 for a welded medical cabinet, you probably need fiber laser with nitrogen assist—not plasma.
Which Method Is Right? Industrial Cutting Techniques
Here’s how manufacturers choose cutting methods for stainless steel:
Fiber Laser Cutting
Best for: Thin to medium sheet metal (≤12mm)
Pros: Clean edges, low HAZ, high speed
Notes: Ideal for 304 and 316, especially where finish matters
Waterjet Cutting
Best for: Thick plate, heat-sensitive parts
Pros: No heat, no hardening, multi-layer cutting
Notes: Slower than laser, but precision is excellent
Shearing & Mechanical Cutting
Best for: Straight cuts on sheet/coil
Pros: Fast, low-cost per part
Notes: Can deform thin stainless without precise blade setup
EDM (Wire or Sink)
Best for: Precision cuts in hard or thick stainless
Pros: Micron-level accuracy
Notes: Slower, expensive, used for aerospace/medical
Plasma (with Nitrogen)
Best for: Structural stainless >10mm
Pros: Low cost
Notes: Heat-affected zone must be cleaned or passivated
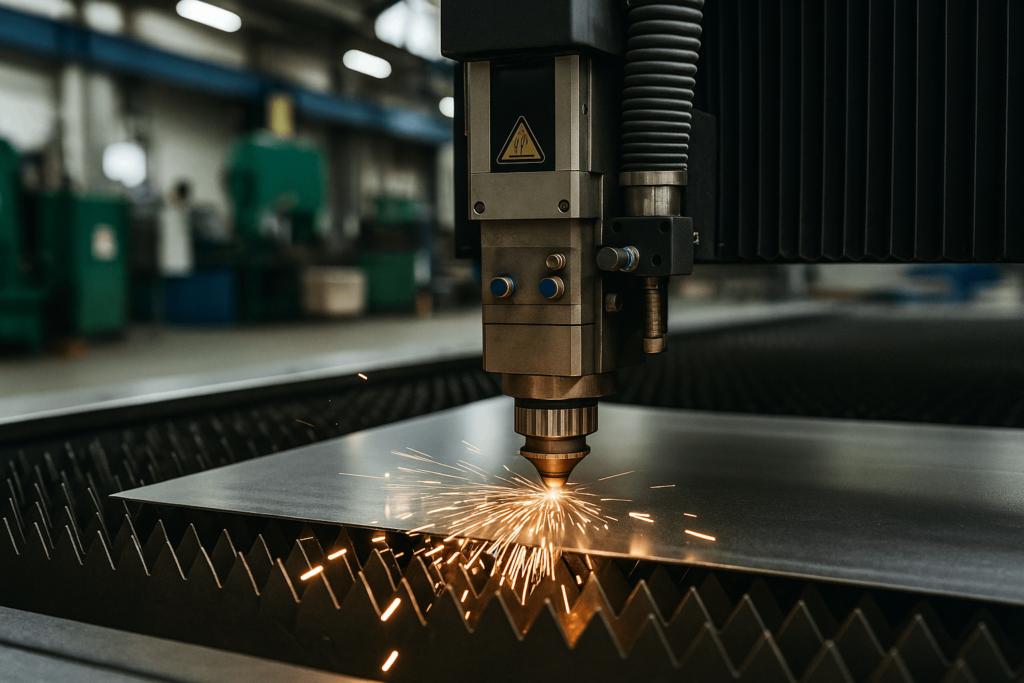
What Happens After the Cut Matters More
Cutting stainless steel is only half the process. The post-cut condition affects welding, bending, powder coating, and even corrosion.
Post-Cut Operation | Why It Matters |
Deburring | Sharp edges interfere with assembly and safety |
Passivation | Removes heat tint & restores corrosion resistance |
Forming / Bending | Requires consistent grain direction + clean edges |
Welding | Edge prep affects fusion and contamination risk |
✍️ Curious how to bend stainless steel tubing after cutting? Start with a clean edge and consistent radius. YISHANG forms thousands of stainless brackets monthly without microcracks.
Finish isn’t just cosmetic—it shapes product perception and determines compliance readiness.
Common Cutting Mistakes That Hurt Output
From experience with global OEMs, here are recurring problems:
Wrong blade or feed rate → chipping, edge hardening
Overlooking HAZ effects → bending or welding failure later
Specifying “cut only” without tolerances → inconsistent fit during assembly
Assuming all stainless behaves like 304 → 316L or 430 may need different cutting chemistry
📌 Need Ra < 1.6µm post-cut? Don’t just ask for “laser cutting”—specify a process path with finishing.
From Cutting to Supply Chain Asset
For stainless parts—whether 3in pipe or laser-cut control panels—what truly matters is repeatable quality at scale.
At YISHANG, cutting stainless steel means one thing: repeatable quality that meets compliance—batch after batch.
Our cutting solutions support your quality system with scalable, repeatable results. YISHANG ensures your stainless parts meet compliance, batch after batch.
FAQ
What is the difference between 304 and 316 stainless steel?
316 offers superior corrosion resistance; 304 is more machinable and budget-friendly. YISHANG guides your choice based on application lifecycle and environment.
Can stainless steel be powder coated?
Yes—but only if surface prep is exact. We use bead-blast and chemical pre-treatment to ensure bonding.
How do you cut stainless steel without discoloration?
Use nitrogen-assist laser or waterjet. We maintain color-neutral edges even on mirror-finish parts.
What rod is used to weld stainless to mild steel?
Usually 309L filler. YISHANG also recommends MIG with tri-mix gas for dissimilar joints.
Can stainless steel be anodized?
Not in the conventional aluminum sense. But we use electrolytic tinting and PVD for color-tuning.
Have a more specific spec to discuss? YISHANG engineers can walk you through stainless solutions by use case.