Introduction
Choosing the right milling cutter isn’t just a technical choice—it’s a strategic sourcing decision. For global procurement professionals focused on CNC parts, OEM components, or bulk precision fabrication, cutter selection directly impacts cost, delivery timelines, and batch consistency.
This guide speaks to those handling RFQs, managing supplier relationships, or building a vetted sourcing network. Backed by 26+ years of experience, YISHANG delivers more than theory—we offer practical, supplier-level insight on tool types, machining performance, and procurement-fit strategies that optimize your value chain.
Trusted by global buyers from 50+ countries, we continue to support international sourcing needs with certified manufacturing standards including ISO 9001 and RoHS compliance.
1. What Are Milling Cutters & Why They Matter in Procurement
Milling cutters are essential cutting tools in subtractive manufacturing. These tools rotate to remove material from metal workpieces, enabling contouring, slotting, facing, or profiling—core operations in most OEM part production.
For buyers, understanding milling cutters helps ensure you’re sourcing from a supplier equipped for accurate, efficient, and repeatable results. Cutter choice affects surface quality, lead time, and scrap rate—all critical to batch-level quality assurance.
Most cutters fall into two categories:
Solid tools: Best for tight-tolerance work and smaller-diameter machining.
Indexable tools: Designed for high-volume machining with replaceable inserts—ideal for cost control in mass production.
Tool geometry (flutes, rake, helix) and compatibility with machines determine production stability and lifespan. These factors translate directly into pricing accuracy and delivery predictability in your supply chain.
2. Overview of Cutter Types: From Concept to Capability
Understanding tool variety helps you assess whether a supplier’s equipment can meet your needs. Below are the most common types of milling cutters used in global CNC manufacturing:
End Mills: Versatile, used for pockets, profiles, and side milling.
Square End: General-purpose. Common in structural enclosures.
Ball Nose: Ideal for 3D features and mold cavity surfaces.
Corner Radius: Reduces chipping. Enhances edge durability.
Face Mills: Used for large flat surfaces—perfect for base plates and panels.
Slab Mills: Heavy-duty roughing tools, reducing excess stock before finishing.
Side and Face Cutters: Suited for groove and channel cutting, especially in brackets or frame components.
Thread Mills, Form Cutters, Shell Mills: Serve niche needs like custom threads, gear profiles, or flexible head swaps.
Fly Cutters: Useful in soft materials where surface quality matters more than speed.
When a supplier like YISHANG uses these tools correctly, it reflects capability—not just in machine setup, but in high-efficiency production planning.
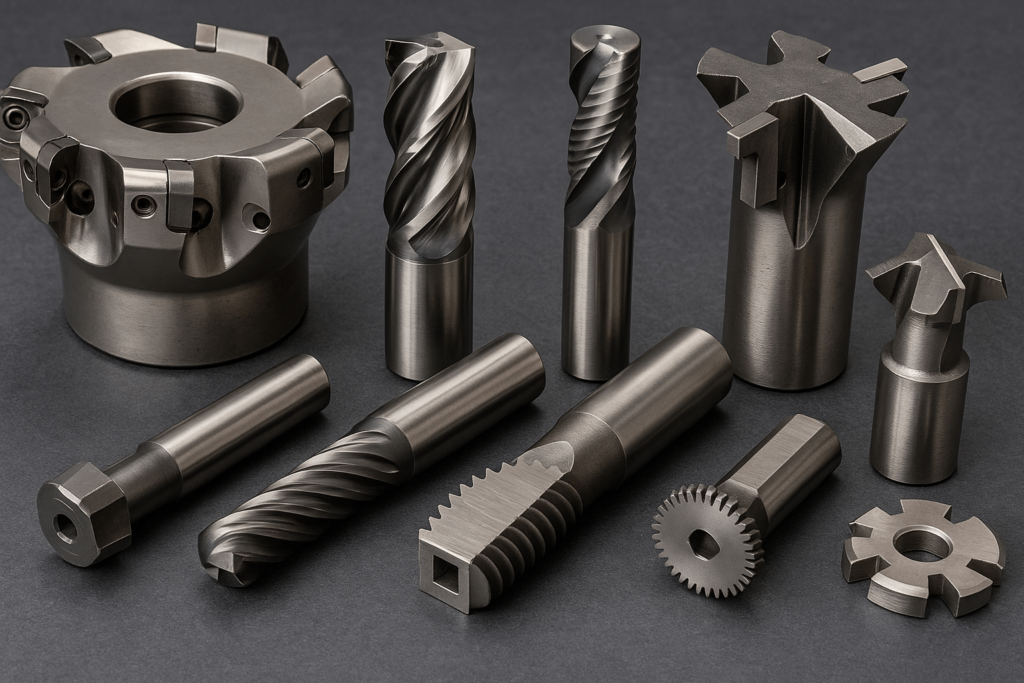
3. Choosing the Right Cutter: A Sourcing Perspective
A procurement-focused approach to cutter selection centers on three key aspects: material compatibility, production volume, and final finish.
Material Compatibility Soft metals like aluminum allow for high-speed cutting with HSS tools. But for stainless steel or titanium, buyers should expect their supplier to use carbide tools with heat-resistant coatings such as TiAlN. This minimizes downtime and ensures consistent results.
Volume and Tooling Efficiency In batch production, tooling cost per part must be stable. Indexable tools with insert replacements are often more efficient than solid mills over long runs. For repeat orders, YISHANG often optimizes toolpaths to extend cutter life and improve throughput.
If sourcing components for enclosure production lines or recurring monthly orders, ensure your supplier applies optimized cutter strategies tailored for high-run consistency.
Material | Tool Type | Coating | Typical Parts |
---|---|---|---|
Aluminum | HSS/Carbide | TiN | Control boxes, panels |
Stainless | Carbide | TiAlN | Hinges, mounts |
Brass | HSS | TiCN | Connectors, rings |
Titanium | Carbide | TiAlN | Precision housings |
Finish and Geometry Higher helix angles and more flutes offer smoother finishes—critical in visible assemblies. For technical interiors, durability and consistency may take priority over cosmetic perfection.
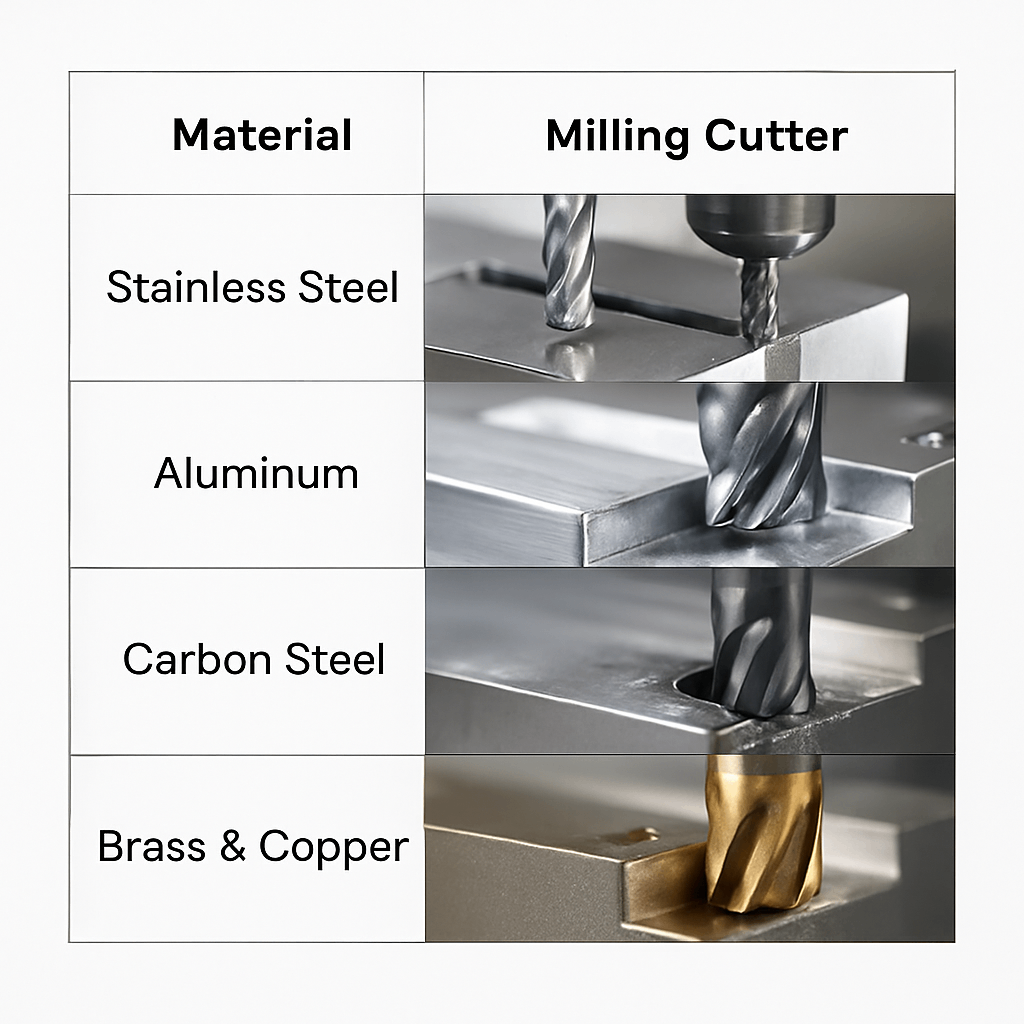
4. Geometry, Coating & Real-World Efficiency
Geometry affects both cutter performance and supplier reliability. Improper tooling leads to tool breakage or increased scrap—delays that overseas buyers can’t afford.
Flute Count Low flute counts clear chips fast—ideal for aluminum. Higher counts suit hardened metals, offering better finish.
Helix & Rake Angles A higher helix provides cleaner cuts with less force. Positive rake angles reduce wear and cutting effort—especially helpful in thin-wall parts.
Coatings
TiN: Good general-purpose solution.
TiAlN: Essential for long runs, especially in heat-intensive work.
DLC/CrN: Increasingly used for copper/brass alloys.
YISHANG chooses coatings not just for tool life, but also for performance per shift—keeping your delivery schedules intact.
5. Managing Tool Wear & Cost Control
Tool wear directly impacts unit pricing in long-term supply agreements. Unexpected tool failure leads to resets, longer machining time, and delivery deviation.
Common Wear Types
Flank Wear: Uniform dulling—manageable with planned replacement.
Crater Wear: Indicates high-temperature stress—use better coatings.
Edge Chipping: Can suggest improper feeds or part vibration.
At YISHANG, we track tool wear per project using historical cycle logs. This lets us build predictive maintenance schedules around customer orders—supporting stable pricing across months or even years.
Buyers should ask:
Does the supplier regrind or replace high-cost tools?
Is tool life tracked by material type or batch number?
How is tool performance linked to part QC checks?
When wear is managed proactively, tool cost per 10,000 parts drops significantly.
6. Machine-Tool Compatibility: Asking the Right Questions
Cutter performance is closely tied to the machines they run on. Mismatched tools lead to inconsistent finishes or tool breakage—especially in tight-tolerance parts.
Tool Holding Systems
Collets: Great for small end mills and low-force cuts.
Hydraulic Chucks: Used for high RPM, better damping.
Arbor Mounts: Standard in large slab or face milling.
Machine Configuration
3-axis: Can handle most jobs, if properly fixtured.
5-axis: Enables angle-specific cutting—ideal for aerospace or die work.
Use this table as a vetting guide:
Tool Type | Holding Method | Machine Type |
Face Mill | Arbor Mount | 3-axis CNC |
Ball Nose | Hydraulic | 5-axis CNC |
End Mill | ER Collet | Manual or CNC |
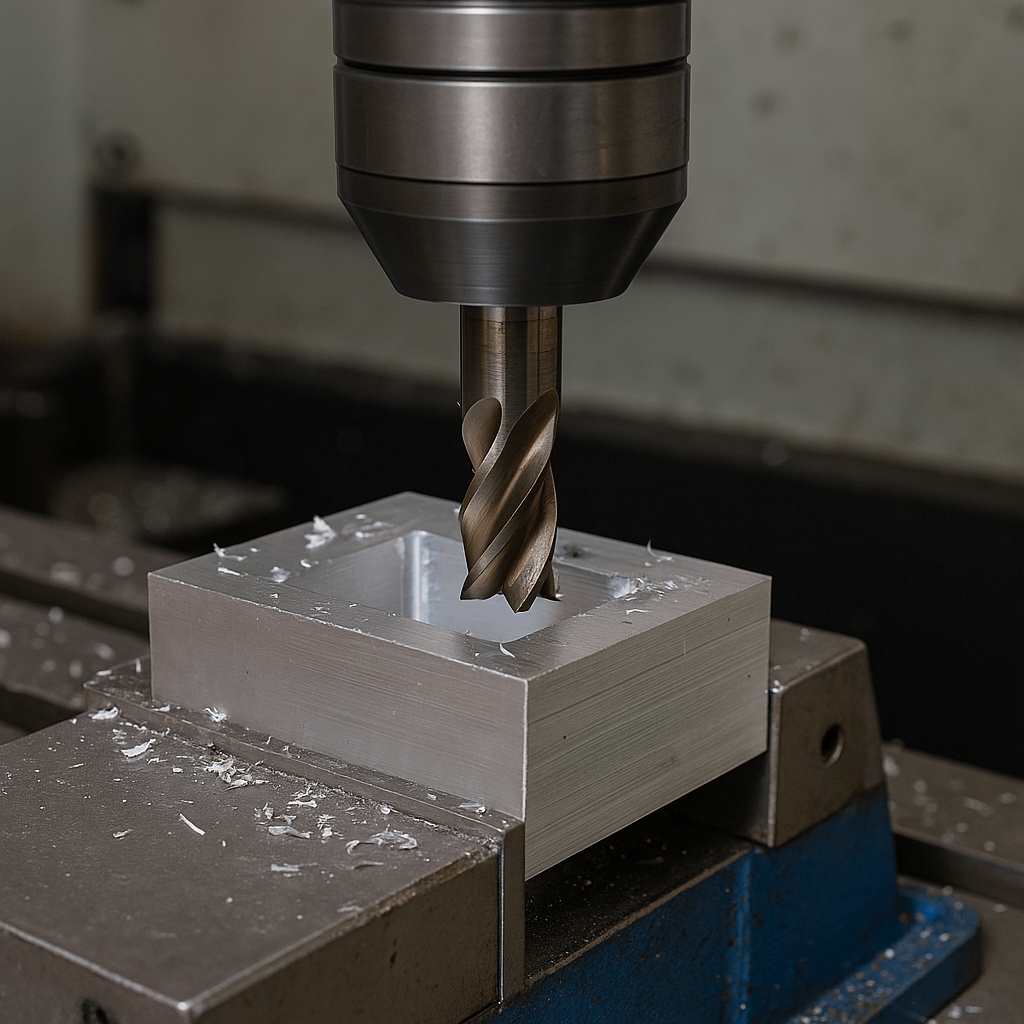
7. Smart Tooling for High-Volume Procurement
For procurement professionals managing high-volume part orders, smart tooling strategies make a tangible difference.
Adaptive CAM Toolpaths Software-optimized paths reduce load on the cutter—extending life and improving finish without increasing tool cost.
Performance Tracking Top-tier suppliers monitor tool life per project and adjust feeds or cutter geometry between batches. This keeps dimensional accuracy and price stability aligned.
Modular Cutter Heads Instead of replacing entire tools, modular heads allow for quick swap-outs—reducing setup time and keeping per-part costs low.
At YISHANG, we apply these strategies across all high-volume orders. These recommendations are based on YISHANG’s real-world CNC production history of over 10 million milled parts.
Backed by our in-house engineering team with decades of tooling optimization experience, we build every batch strategy with cost, consistency, and delivery in mind.
FAQs – For Sourcing Clarity
Can one cutter do both roughing and finishing? Technically yes, but we usually split them to control finish and tool wear.
Do I need to specify cutter types in my RFQ? No, but if you care about tolerance, finish, or cost targets—telling us helps.
Can we audit your cutter choices? Yes. Transparency is part of our process. We’re happy to explain why we use a certain tool for your project.
How does cutter choice impact lead time? Optimized tooling reduces cycle time and rework. That translates to more reliable shipping.
Do you offer quality inspection reports? Yes. Full inspection reports can be provided upon request, based on your required specifications or project standards.
Conclusion
For wholesale buyers, the cutter isn’t just a shop-floor detail—it’s part of the pricing formula, quality promise, and supply chain consistency. Whether you’re sourcing 1,000 or 100,000 units, having the right tool strategy behind your parts makes a measurable difference.
YISHANG’s team works behind the scenes to match each part’s requirements with the right cutter and process plan. It’s how we help buyers hit their cost, quality, and delivery targets—every time.
Ready for a quote or need cutter recommendations for your part drawings? Our engineers are here to help.