Introduction: Why Brass Finishing Matters for Wholesale Projects
In the global OEM and custom fabrication markets, brass finishing plays a defining role—not just in how a product looks, but how it performs over time. For wholesale buyers, especially those managing large-volume orders across architecture, hardware, or electrical industries, surface finishing isn’t just cosmetic—it affects cost-efficiency, shipment quality, and end-user satisfaction.
From preventing corrosion in outdoor vending machines to ensuring consistent satin textures in hospitality builds, the right brass finish adds measurable value. This guide by YISHANG is crafted for sourcing professionals and decision-makers who need clarity in selecting the right brass finishing solutions that meet performance, timeline, and compliance demands.
The Role of Finishing in the Lifecycle of Brass Components
Brass, an alloy of copper and zinc, is inherently reactive and prone to surface oxidation. Over time, exposure to air and moisture leads to tarnishing. For architectural trim or medical fittings, this can create aesthetic inconsistencies or hygiene concerns. Left untreated, brass also becomes vulnerable to abrasion, which can affect mating parts or electrical conductivity.
A suitable finish counters these issues. In practical terms, choosing a reliable finish contributes to fewer product returns, more consistent color across batches, and improved compatibility with sealing or welding processes. This becomes essential in applications with tight tolerance finishes such as 32 microinch finish (equivalent to 0.8 μm or 32 Ra surface finish), often required in electronics and valve components.
Dimensional control is another key factor. Finishes like electroplating or PVD add measurable thickness. Without accounting for it during CAD or prototyping stages, interference fits may occur. For clients sourcing 3.2 surface finish in inches, we help validate tolerances during DFM reviews, preventing cost-heavy reworks.
Finishing Techniques and Their Procurement Relevance
Each finishing method offers different advantages based on end-use, cost, and durability. Our intent here is not to teach processes, but to help you choose wisely based on project-specific metrics.
Electroplating Brass
Electroplating involves depositing metals like nickel or chrome onto brass through electrolyte baths. It’s ideal for components requiring conductivity, enhanced wear resistance, or medical compliance. Products like diagnostic housings often call for 125 rms surface finish, which electroplating achieves reliably.
Electroplating suits medium-to-high production runs due to tooling setup costs. We maintain full RoHS-compliant baths and quality testing, delivering a consistent 125 finish across production batches. However, for small volumes or budget-sensitive applications, simpler methods like brushing may be more economical.
Antique Patination
Chemical oxidizers simulate age, creating depth in color with a vintage appeal. Though labor-intensive, patina finishes remain popular for boutique hardware and architectural trim. Their unpredictability in uniformity can be an advantage for brands seeking unique surface stories.
That said, wholesale buyers should be aware of handling sensitivities and longer lead times. This finish doesn’t suit precision mating surfaces or components where 1.6 surface finish or better is needed.
Brushed and Satin Brass
These mechanical finishes use abrasives to create directional grain (brushed) or diffuse low-gloss (satin) textures. Common in decorative elements and switches, they’re fingerprint-resistant and preferred in visible hardware.
From a supply chain view, brushed brass is ideal for scaling up in batches with minimal tooling. It aligns well with 32-125 surface finish requirements, often used in metal finishing services for kitchenware, retail fixtures, or HVAC covers.
Powder Coating Brass
This method uses charged resin powders cured onto brass to provide color and weather resistance. A powder coating matte finish is particularly effective for components exposed to sunlight or high humidity. In applications such as vending machines or exterior signage, we often recommend white powder coat finish to maintain visibility and UV protection.
As part of our metal finishing solutions, YISHANG offers pretreatment options to improve bonding and resistance, matching both powder finish paint standards and functional durability goals.
PVD Coating (Physical Vapor Deposition)
PVD finishes are high-performance, vacuum-applied coatings offering superior abrasion and corrosion resistance. Their thin-film application maintains dimensional control while enhancing surface hardness.
They are often selected for medical tools or luxury fixtures needing durability and color permanence. While the cost is higher, the ROI in reduced returns and higher client satisfaction makes it a strategic choice for long-life components.
Polishing and Burnishing
Used where reflectivity or visual clarity is required, these finishes provide mirror or soft-glow effects. Their use is common in art objects or sanitary fittings where visual continuity matters.
We often match to aluminum surface finishes charts and ensure lacquer compatibility. If a client requires a 16 ra surface finish or 25z surface finish for sealing performance, we measure and verify prior to shipping.
Unlacquered and Waxed Brass
For clients who embrace material aging, unlacquered brass offers a “living finish.” It darkens with time and touch, common in hospitality and designer builds. While visually compelling, this option needs buyer alignment on end-user expectations and care instructions.
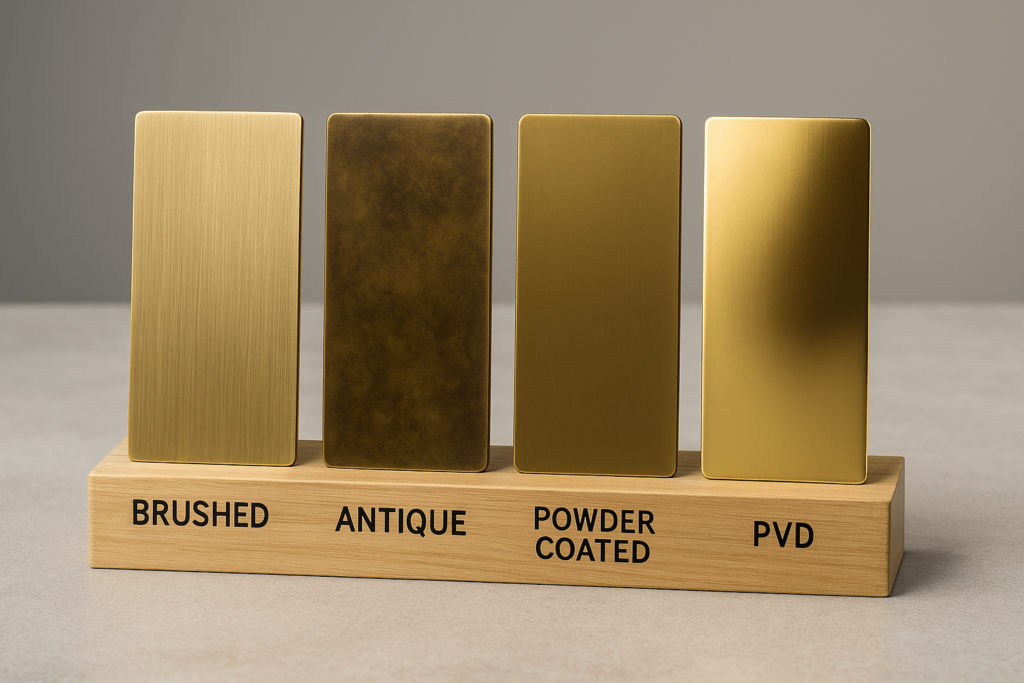
Sourcing Checklist: What Buyers Need to Validate
Brass finishing choices aren’t made in isolation. For large-volume buyers, the decision must account for batch uniformity, surface testing, and export readiness.
Checklist Includes:
Finish Repeatability: Especially important for projects requiring color matching across lots.
Surface Roughness Targets: Can your supplier hit 125 ra surface finish or finer repeatedly?
Pre-Shipment QC: Does your vendor inspect for pitting, adhesion, and final gloss level?
RoHS + Export Docs: Especially relevant for Europe, Australia, and North America.
Packaging & Handling: Are finishes protected during export to prevent scuffing?
We support clients with first-article inspection reports and surface validation photos/videos. From bead blast finish stainless steel options to aluminum brushed finish alternatives, YISHANG helps buyers evaluate based on logistics and project risks.
From Sample to Global Shipment: YISHANG's Finishing Workflow
For international clients, our workflow focuses on transparency and predictability:
Sample Lead Time: 5–7 working days with finish reports
MOQ: Starting at 100 pcs, scalable based on complexity
Standard Lead Time: 12–18 days with inline QC and lot segregation
Finish Testing: Adhesion, coating thickness, and Ra value as per drawing
Packaging: Foam interleaving, VCI bags, corner-reinforced cartons
We align our production with your packaging spec sheets and shipping labels, minimizing downstream bottlenecks.
Real-World Applications: Project-Based Recommendations
Case: Hospitality Projects in UAE A hotel group required satin brass electrical plates across 30 properties, uniform in 32 surface finish and sealed against humidity. Our brushed finish metal solution with nano-coating ensured easy cleaning and consistent sheen across 4,000+ pieces.
Case: Outdoor Retail Fixtures in Europe Powder coating matte finish in white was used for wayfinding kiosks in high-salinity environments. By integrating an epoxy primer under the powder coat, YISHANG extended durability beyond 1,000-hour salt spray resistance.
Case: Medical Diagnostic Panels (US Market) Precision brass housings required 125 machine finish and RoHS compliance. We applied nickel electroplating and post-machining passivation, then verified with 125 surface finish example charts during shipment QA.
Finishing Is a Specification—Not a Guess
Many component failures stem from incorrect or vague finishing specs. From a sourcing perspective, a well-defined finish helps ensure part performance, reduces rework, and aligns stakeholders from design to QA.
A 32 ra finish vs. a 125 ra surface finish makes a difference in gasket sealing or visual quality. Buyers who specify finishes upfront often report lower defect rates and better supplier accountability.
YISHANG supports clients in understanding and defining these targets early. Whether matching anodised finish aluminium in control panels or aluminum finishes chart references for lighting trims, we build with your outcomes in mind.
Trusted by customers in Europe, North America, and the Middle East since 1996. YISHANG is ISO 9001 certified and RoHS compliant. All brass finishing is performed in-house with surface inspection reports provided upon request.
Conclusion
Brass finishing is a detail that defines your product’s durability, consistency, and perceived quality. Choosing the right one isn’t just technical—it’s a sourcing decision that influences costs, timelines, and end-user experience.
YISHANG offers full-stack brass finishing services, integrating sampling, testing, and global export packaging into one seamless process. When you need precision, scalability, and dependable communication, we’re here to help.
Get in touch with YISHANG today to request a sample or start your next RFQ.