Introduction: Why "Rust-Free" Aluminum Still Demands Engineering Attention
Many OEM buyers and sourcing professionals assume aluminum is rust-proof and thus requires little attention to corrosion control. While aluminum doesn’t form iron oxide like steel, it is far from invincible. For industries sourcing aluminum sheet metal parts, enclosures, or outdoor-use components, understanding corrosion behavior is not a luxury—it’s a necessity.
This article, based on 26+ years of manufacturing experience at YISHANG, is designed to support wholesale supply chain decision-makers with actionable insight. We combine engineering advice, RFQ-ready recommendations, and surface treatment strategies to help OEM buyers avoid costly performance failures.
Why Aluminum Doesn’t Rust—but Still Corrodes
Rust, by definition, refers to iron oxide—something aluminum can’t form due to its lack of iron. Instead, aluminum forms a protective aluminum oxide layer when exposed to air. This natural passivation is what makes aluminum appear “rust-free.”
However, that oxide layer is just a few nanometers thick. It can be compromised by environmental exposure, galvanic reactions, or poor surface finishing. Once broken, corrosion spreads beneath the surface, often unnoticed until functional damage occurs.
This is especially critical when sourcing aluminum CNC parts, powder-coated enclosures, or aluminum extrusion profiles intended for high-humidity or marine applications. Misjudging corrosion performance can result in warranty claims, product recalls, or reduced equipment lifespan.
What Causes Aluminum to Corrode in Real Use
Environmental Factors
High-chloride environments, such as coastal zones or roads treated with deicing salt, are aggressive to aluminum. Chloride ions penetrate the oxide layer and initiate pitting corrosion.
Polluted air containing sulfur dioxide or nitrogen oxides reduces surface pH. Acid rain events have been recorded with pH below 4.5—more than enough to dissolve aluminum oxide and initiate underfilm corrosion on uncoated aluminum extrusion enclosures or brackets.
Galvanic Contact Risks
Many OEM buyers unknowingly combine stainless steel fasteners with aluminum base materials. This creates a galvanic cell that accelerates aluminum corrosion. We have seen cases where laser cut aluminum panels degraded within one year due to mixed-metal assembly without electrical isolation.
If you’re sourcing aluminum for commercial kiosks, vending enclosures, or signage brackets, confirm that all joining systems are isolated or treated with non-conductive finishes.
Design-Induced Failures
Poor drainage, crevices under gaskets, and areas lacking airflow all increase corrosion risk. At YISHANG, we often help buyers optimize drawings before CNC machining or aluminum die casting to eliminate moisture traps. Upload your drawings for a corrosion-resistant quote—we can help you design it right.
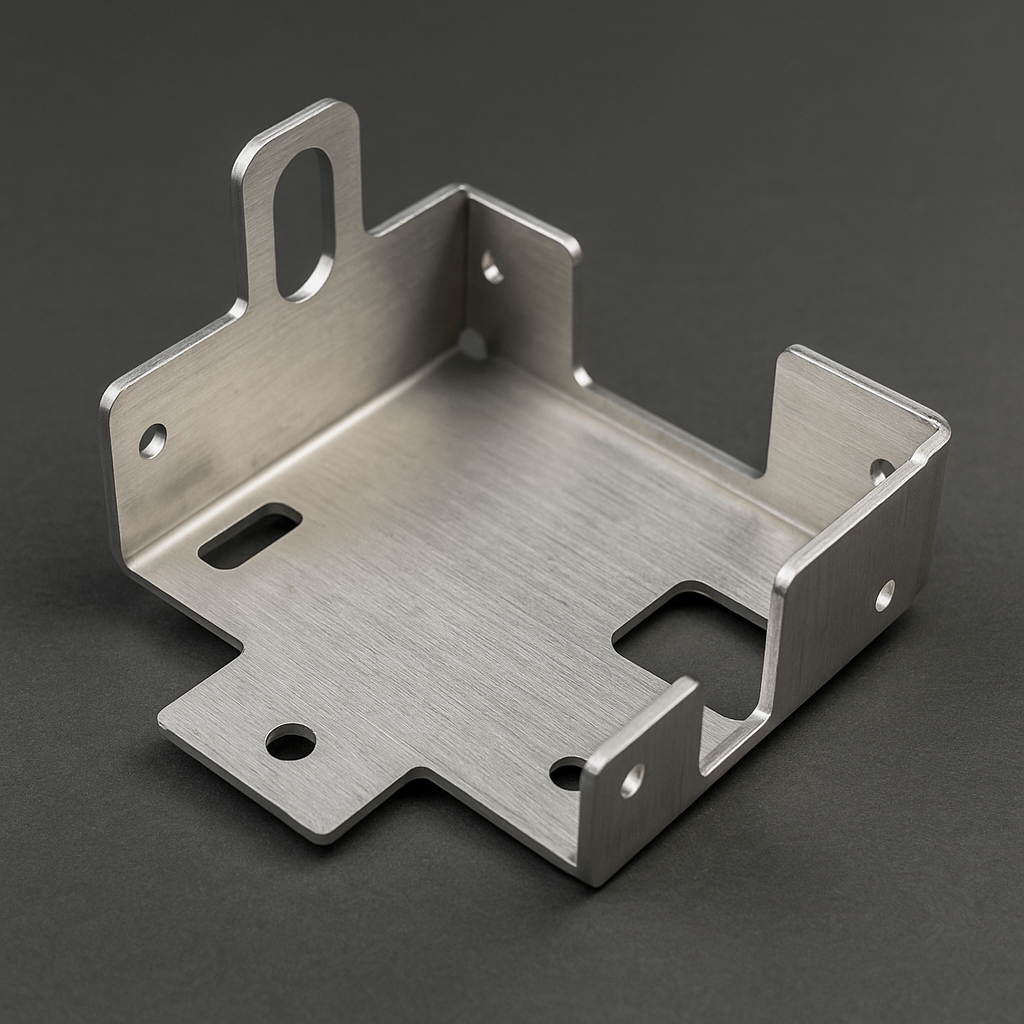
Forms of Aluminum Corrosion and How to Recognize Them
Pitting Corrosion
Pitting presents as small holes but often extends deeply beneath the surface. It’s common in marine-use aluminum cast alloys or where aluminum anodizing services were improperly applied. 5052 aluminum alloy performs better in these environments than 7075 aluminum due to its higher magnesium content.
Crevice Corrosion
Crevice corrosion arises under washers, seals, or joints—where stagnant water collects and oxygen exchange is limited. In one field case, a vending enclosure built from 6061 aluminum suffered failure due to crevice corrosion, despite powder coating. Design—not material—was the weak link.
Galvanic Corrosion
As described, mixed-metal joints (e.g., aluminum + stainless) are hotspots for galvanic corrosion. Make sure to specify aluminum anodizing or Alodine treatment before assembly. Our aluminum fabrication shop includes pre-coating services as part of our RFQ-ready solutions.
How to Engineer Durable Aluminum Parts: A Guide for OEM Buyers
Selecting the Right Alloy
Different alloys yield drastically different corrosion resistance. Here’s a comparative chart used at YISHANG:
Alloy | Yield Strength (MPa) | Pitting Resistance | Typical Use |
---|---|---|---|
5052 | 193–228 | Excellent | Marine, HVAC panels |
6061 | 240–290 | Very Good | Structural, CNC parts |
7075 | 503–572 | Moderate | Aerospace, high-load frames |
Don’t let “6061 aluminum hardness” or “7075 aluminum yield strength” be your only selection criteria. Match alloy properties to environmental risks.
Surface Treatments That Work
Aluminum anodizing improves durability and is available in a full aluminum anodized color chart.
Alodine for aluminum is widely used before aluminum powder coating or painting to prevent corrosion.
Aluminum powder coat finishes are preferred for high-traffic or outdoor enclosures. We offer both finishing and aluminum anodizing services in-house.
Request surface finishing samples today—we support full color-matching, weather resistance, and project-specific coating advice.
Design Best Practices
Procurement teams frequently share extrusion files or casting drawings. Our team can validate:
Drainage for extruded aluminum enclosures
Fastener isolation methods
Avoidance of blind crevices in aluminum casting die tooling
Use our DFM review to reduce corrosion failures before mass production.
Common Missteps by Wholesale Buyers—and How to Avoid Them
Assuming All Anodizing Is Equal
Not all anodizing processes are alike. We advise RFQs specify Type II or Type III anodizing and reference standards such as ASTM B580 or ISO 7599.
Ignoring Environmental Fit
If you’re sourcing for coastal or humid areas, avoid high-strength alloys with poor corrosion tolerance. For instance, using 7075 aluminum in a marine project may look good on a spec sheet—but not in the field.
YISHANG regularly advises wholesale supply partners to align alloy, coating, and usage scenario.
Overlooking the Role of Design
Aluminum corrosion risk isn’t just about material—it’s about how it’s shaped and sealed. Submit your drawings for review and we’ll provide a corrosion-optimized design suggestion at no additional cost.
Why Aluminum Remains a Top Choice—When You Source Smart
Aluminum offers strength, low weight, and excellent machinability. When paired with the right surface treatments, it’s ideal for high-volume industrial applications.
YISHANG supports OEM buyers sourcing aluminum extrusion, aluminum die casting, and CNC aluminum parts for telecom, medical, energy, vending, and EV enclosures. Our aluminum extrusion services ensure tolerance precision and surface quality for global wholesale distribution.
With proper anodizing, powder coating, and assembly engineering, aluminum meets both cost and corrosion resistance targets.
FAQ: Smart Sourcing Questions About Aluminum Corrosion
Why do my aluminum parts corrode even when anodized?
Anodizing protects against many forms of corrosion, but if the part is scratched, unsealed, or exposed to galvanic metals, failure can still occur. Always confirm anodizing specs and secondary coatings.
Can aluminum corrode in coastal conditions?
Yes. Use marine-grade alloys like 5052 and apply a sealed anodizing or aluminum powder coating. Contact us for advice on sourcing aluminum for salt air environments.
Should I choose anodizing or powder coating?
Use anodizing for hardness and surface conversion, and powder coating for mechanical abrasion resistance and aesthetics. Combined systems deliver best performance.
What alloy should I specify for outdoor kiosks?
6061 works well for general use; choose 5052 for coastal projects. We’ll help evaluate your project and suggest the most suitable aluminum alloy extrusion.
Can I get a corrosion-resistant sample part first?
Yes. Contact us with your specifications—we offer RFQ-ready samples and surface finish validation.
Conclusion: Durable Aluminum Begins with Informed Procurement
Aluminum doesn’t rust—but it does corrode if not properly engineered. Buyers focused on long-term durability must balance alloy selection, coating choice, and component design.
YISHANG delivers end-to-end aluminum solutions—from extrusion and casting to powder coat and anodizing—to help OEM buyers and global distributors prevent failure and increase value.
Upload your RFQ or drawings today—YISHANG will help you source aluminum the smart way.