Introduction: Making Informed Equipment Choices in Industrial Procurement
For industrial buyers, selecting between desktop CNC milling machines and traditional milling machines is not a matter of convenience or trend—it’s about aligning machinery with output expectations, precision requirements, and unit cost performance.
At YISHANG, we’ve worked with procurement managers across more than 50 countries. We’ve seen how a mismatch between machinery and production goals can create delays, inflate costs, or reduce product consistency. That’s why this guide goes beyond technical definitions and helps you evaluate what really matters: long-term ROI, production flexibility, and the capacity to scale.
Whether you’re sourcing for 500-unit aluminum prototypes or 20,000 precision-finished stainless parts, understanding how each machine performs under real-world manufacturing conditions is key. This article is crafted specifically for wholesale buyers and sourcing agents who need more than product specs—they need strategic insight.
Desktop CNC Milling: Smart Investment for Agile, Low-to-Medium Batch Runs
Desktop CNC milling machines—sometimes referred to as benchtop CNCs or compact mills—have gained traction in recent years. For good reason: they’re budget-friendly, space-saving, and highly adaptive to short-run projects or iterative prototyping.
Modern desktop models now include ball screw drives, integrated tool paths via CAM software, and spindle speeds over 20,000 RPM. Many support 3 axis and even entry-level 4 axis milling setups. For buyers in electronics, medical accessories, or custom device sectors, this enables precision cuts on aluminum and soft stainless materials without significant investment.
In a recent EU-based POS hardware rollout, a client used two desktop CNC units to complete over 3000 anodized aluminum front panels. Surface finish reached Ra 3.2 μm, with a consistent ±0.05 mm tolerance—sufficient for housing integration. Compared to outsourcing, this approach reduced their prototyping cycle by 40%.
YISHANG recommends desktop CNCs particularly for:
Initial market testing and limited-release production
Projects needing frequent design adjustments
Customers aiming for in-house quality validation before scale-up
Insight: For low-volume custom parts or frequent iteration cycles, desktop CNCs offer a practical balance of cost, control, and lead time.
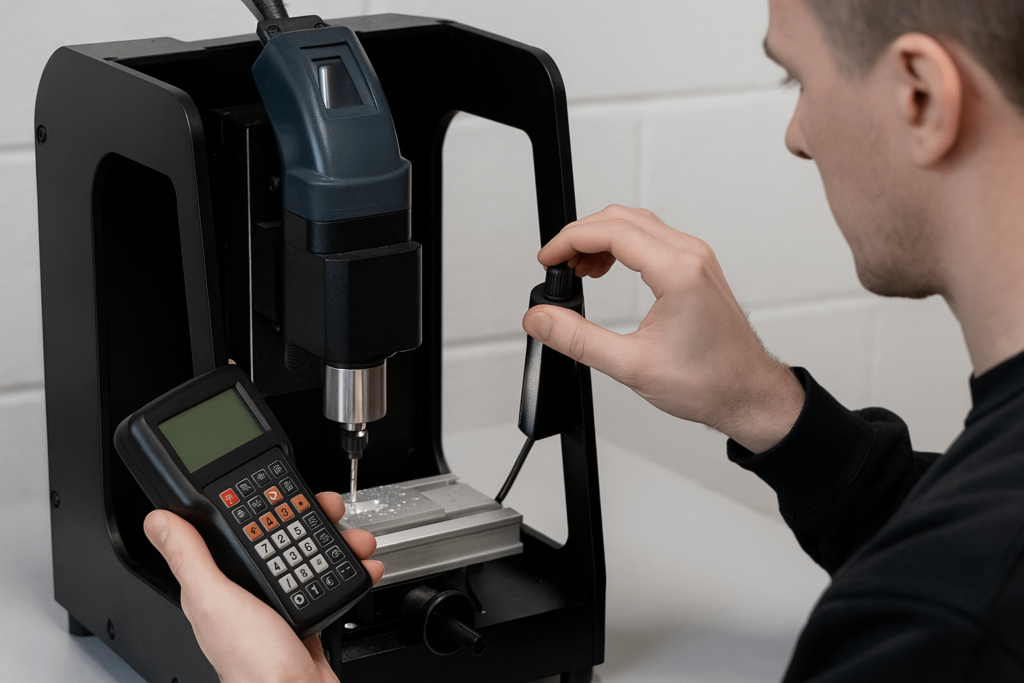
Traditional Milling Machines: Robust Throughput for High-Volume and Heavy-Duty Production
Traditional milling machines—including manual and full-sized CNC systems—are still the gold standard for bulk production and hard-material handling. These machines feature cast-iron bodies, robust spindles with torque ratings up to 20 HP, and multi-axis capabilities including advanced 5 axis milling services.
They accommodate deeper cuts (up to 6 mm per pass), heavier feed rates, and tougher materials like high-carbon steel, titanium, and tool-grade alloys. In industries like construction hardware or EV battery components, where tight tolerances and durability are mission-critical, traditional systems outperform lighter machinery by a wide margin.
For example, in a US-based vending system production contract, YISHANG deployed vertical mills with 4th axis milling integration to manufacture 12,000 galvanized steel casings in under six weeks. Tolerances stayed within ±0.01 mm, and surface roughness hit Ra < 1.6 μm, exceeding client specifications.
Insight: When lead time assurance, unit price optimization, and round-the-clock operation matter, traditional milling machines deliver consistent ROI and production reliability.
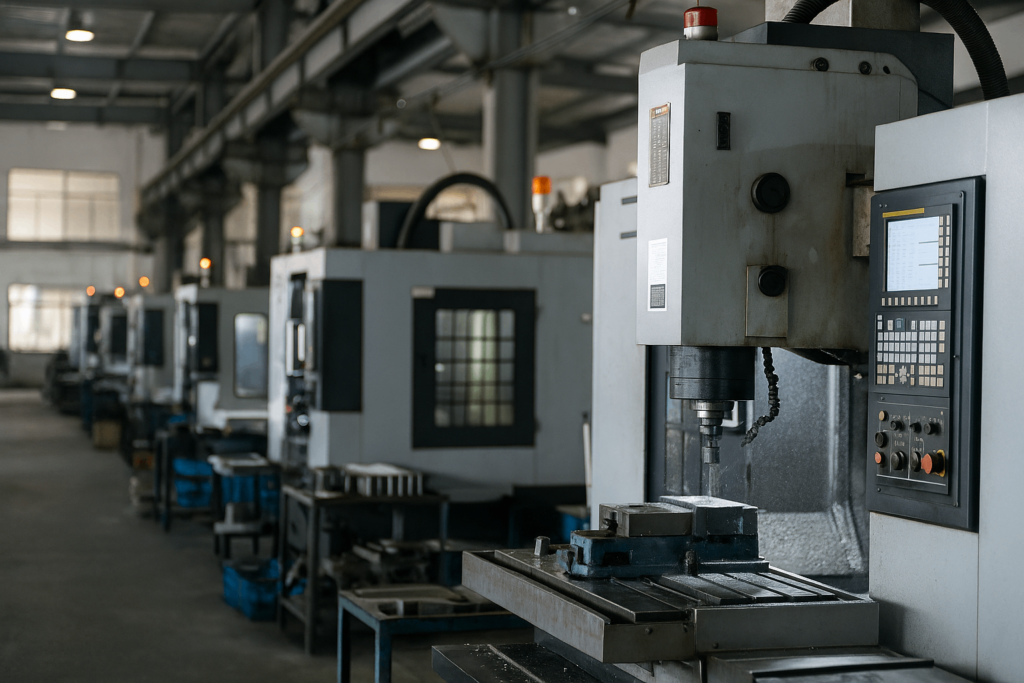
Comparing Performance: Precision, Materials, and Workflow Fit
Accuracy & Stability
Desktop CNCs reliably maintain ±0.03–0.05 mm tolerance for aluminum and composite materials. However, in steel, deflection and thermal expansion affect performance—especially without integrated coolant systems.
Traditional machines—especially 3 axis and 5 axis mills with closed-loop feedback—reach ±0.01 mm with fewer toolpath deviations. When high repeatability and finish quality are priorities, particularly in large-batch runs, they remain the preferred choice.
Materials & Cut Depth
Material Type | Desktop CNC | Traditional CNC |
---|---|---|
Aluminum | Excellent | Excellent |
Mild Steel | Limited (light cut) | Ideal |
Stainless Steel | Fair | Excellent |
Plastics / ABS | Excellent | Excellent |
High-Carbon Steel | Not recommended | Fully supported |
Advanced CNC milling machines now feature 4 axis and even 5 axis setups with synchronized rotary tables—ideal for complex geometries and undercut components. These setups are common in traditional environments but less so in desktop formats.
Insight: Evaluate by application. For structural parts or thicker materials, choose the power and rigidity of advanced milling machines for heavy duty use.
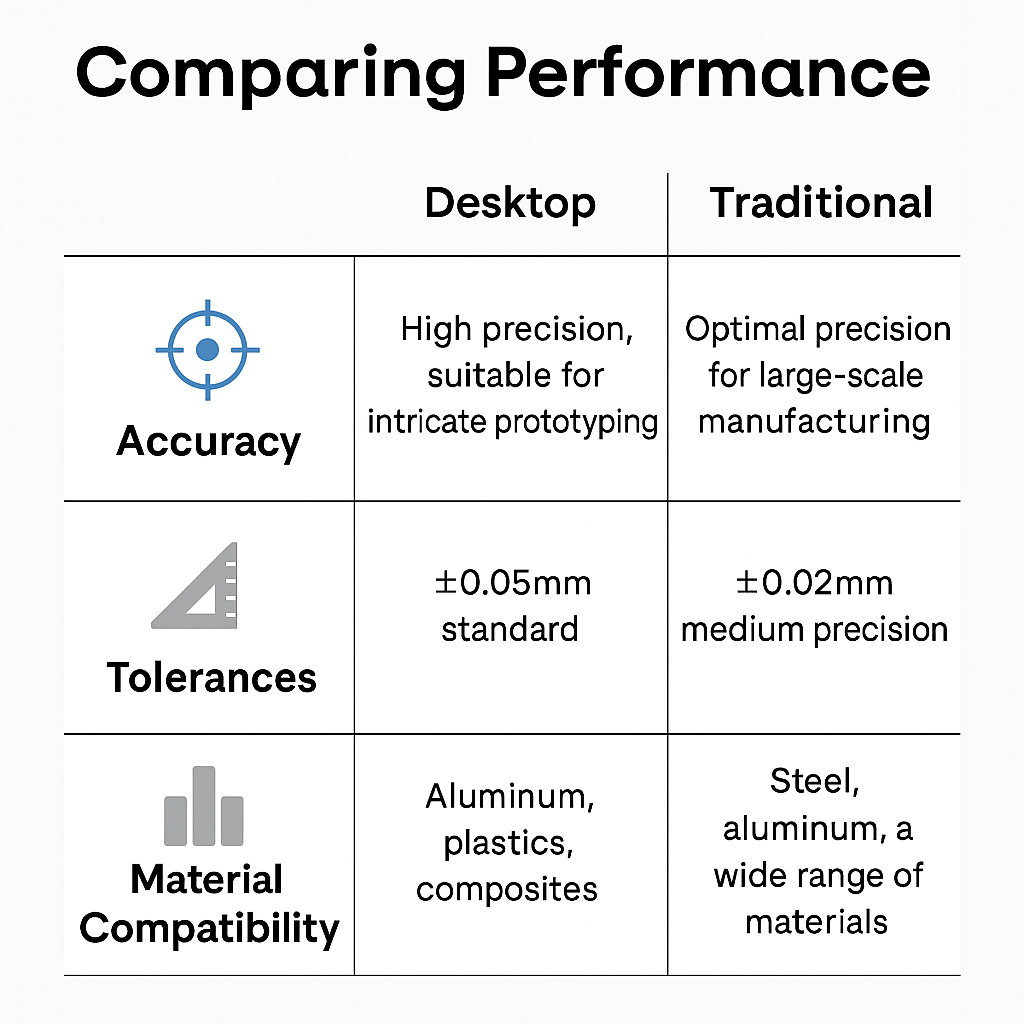
Cost Analysis: CAPEX, OPEX, and Hidden Trade-Offs
Capital Cost (CAPEX)
Desktop CNC: $2,000 – $10,000
Traditional CNC (including 5 axis milling machines): $20,000 – $150,000+
Operating Cost (OPEX)
Desktop CNCs: Lower energy consumption (<500W), minimal training, smaller footprint
Traditional Mills: Higher energy draw (2–10kW), requires experienced operators, larger space allocation
Hidden Costs
Tooling compatibility: Some desktop units have limited spindle taper support
Fixture repeatability: Desktop setups often lack the clamping precision needed for tight-repeat jobs
Training and transition: Shifting from 2nd hand milling machine operation to automated 5-axis CNC milling can require retraining, but long-term gains outweigh initial learning curves
Insight: For consistent orders over 2,000 units/month, the per-part savings of traditional mills outweigh their upfront cost.
Workflow Considerations: Flexibility vs Automation Integration
Desktop CNCs are ideal for lean manufacturing models. They enable same-day design-to-prototype cycles and empower internal QA teams. However, they lack the PLC or robotic integration options that traditional machines offer.
Full-sized CNCs with 4 axis or 5 axis milling can sync with automated pallet changers, part feeders, and ERP systems. In high-volume lines, this reduces downtime and labor dependency—essential for clients working under strict SLA terms.
Insight: If your facility is scaling into smart manufacturing or Industry 4.0 readiness, traditional CNCs with automation compatibility provide future-proofing.
Industry Usage Scenarios
Scenario A: Low-Volume Customization
An aluminum milling service provider in Canada produces 200–400 customized lighting brackets per order. Using 3 axis CNC mill setups, they’ve achieved fast iteration and delivery within five business days. Their shift to desktop units improved their tooling amortization by 22%.
Scenario B: OEM Batch Fulfillment
A German automotive subcontractor sources bulk bracket manufacturing from YISHANG. Using our 6 axis milling machine line, we’ve completed monthly orders of 15,000 parts with <0.5% defect rate and optimized aluminum cutting speed milling profiles for cycle efficiency.
Insight: Match machine type to frequency, scale, and customization need—not just material type.
Decision Matrix for Buyers
Application Type | Volume | Tolerance | Machine Type |
Rapid prototyping | < 500 | ±0.05 mm | Desktop CNC |
Custom fixtures | 500 – 2000 | ±0.03 mm | Desktop / 3 axis CNC |
High-volume OEM | > 2000 | ±0.01 mm | Traditional / 5 axis CNC |
Also consider if post-processing (deburring, anodizing) is needed—desktop setups often require manual transfer, while traditional lines can integrate finishing operations.
Misconceptions and Clarifications
“Desktop CNCs can’t do real metal work” – False. With proper endmills and feeds, they handle aluminum and light steel.
“Traditional machines are outdated” – False. Modern 5-axis CNC milling machines are integrated with IoT monitoring and predictive maintenance features.
“More axes mean better performance” – Not always. A 3 axis milling machine may outperform a 5 axis setup if geometry is simple and job setup is optimized.
FAQ
Do you support DDP shipping or custom packaging?
Yes, YISHANG offers Incoterms-compliant DDP shipping, including export foam, crates, and custom labels.
Can you optimize unit price for monthly batch orders?
Absolutely. We offer volume-based pricing, tooling amortization strategies, and multi-shift production scheduling.
What is your average lead time for a 5,000-part aluminum order?
Typically 12–15 working days with inline quality checks and final packaging.
Do you offer 5 axis milling services?
Yes, including contour milling, undercut features, and multi-surface machining.
Can you match my local milling service’s tolerance spec?
We regularly meet ±0.01 mm in steel and aluminum using calibrated measuring systems and ISO-certified processes.
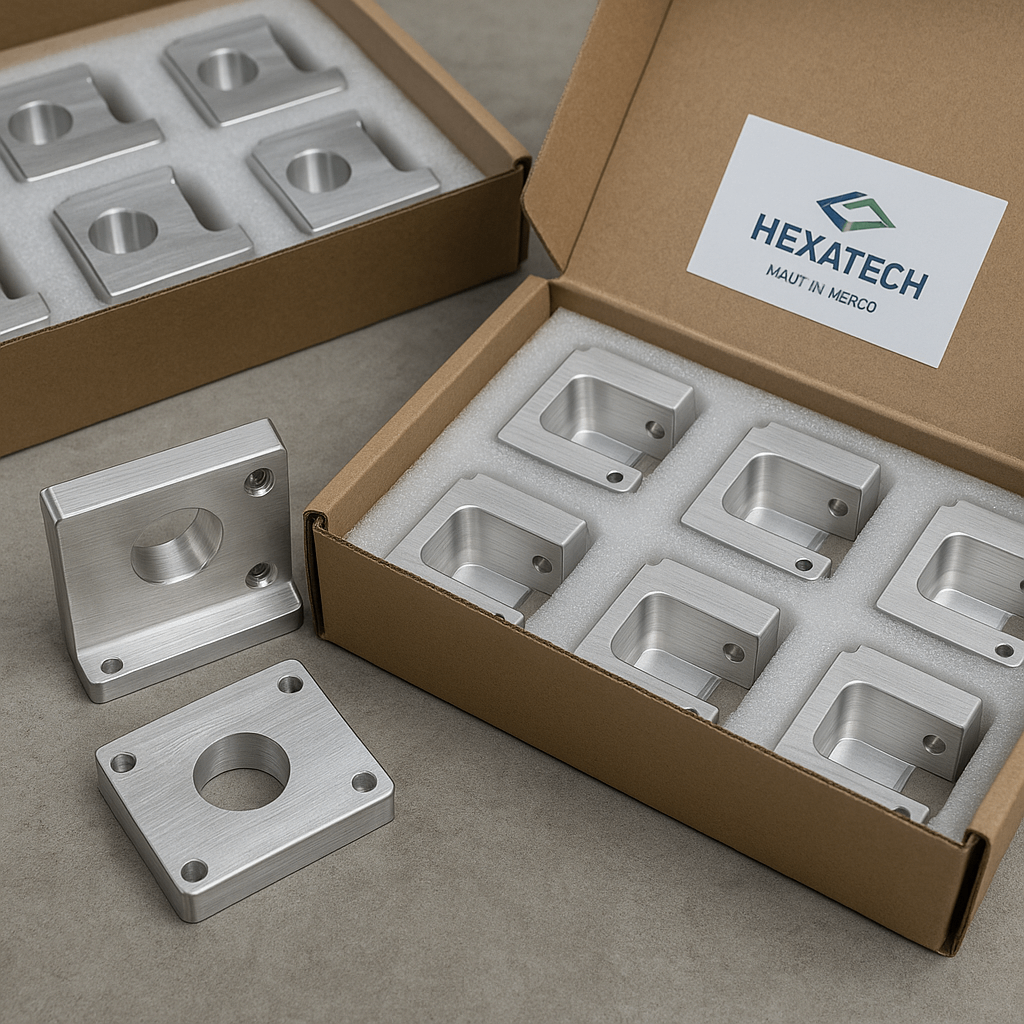
Conclusion
Both desktop CNC and traditional milling machines have valid use cases—but only one fits your production model.
Choose desktop CNC if you prioritize speed, flexibility, and limited output. Choose traditional milling for volume reliability, cycle time reduction, and per-unit efficiency. YISHANG supports both paths.
📩 Contact YISHANG today for tailored recommendations on your CNC procurement goals.