Beyond the Definition: What Tensile Strength Really Tells Us
Why Tensile Strength Matters in Purchasing
This concept is more than a physical property—it’s a practical benchmark that determines success or failure in multiple industries. Tensile strength directly impacts performance in sectors like vending machine hardware, power distribution frames, telecom switch housings, solar panel brackets, and even pet enclosure frames.
At YISHANG, we’ve supported purchasing teams in these fields by helping them match material performance with application-specific load demands. Whether it’s selecting 4130 steel for aerospace-grade clamps or evaluating the tensile reliability of brass inserts for medical panels, tensile strength influences long-term durability and cost-effectiveness.
Misunderstandings That Lead to Failure
Tensile strength measures how much stress a material can endure before it breaks under tension. For wholesale buyers sourcing components for structural assemblies or metal enclosures, this value is far more than a number on a datasheet.
In our experience at YISHANG, tensile strength is often misunderstood. Take a vending system client: their aluminum brackets failed not because the material was weak, but because forming stresses exceeded their expected load range. The misalignment between material properties and use case cost them weeks in retooling.
How Better Understanding Prevents Risk
Smart procurement goes beyond verifying a value. You want to know whether tensile limits align with forming, joining, and service conditions. That understanding prevents product recalls and field failures.
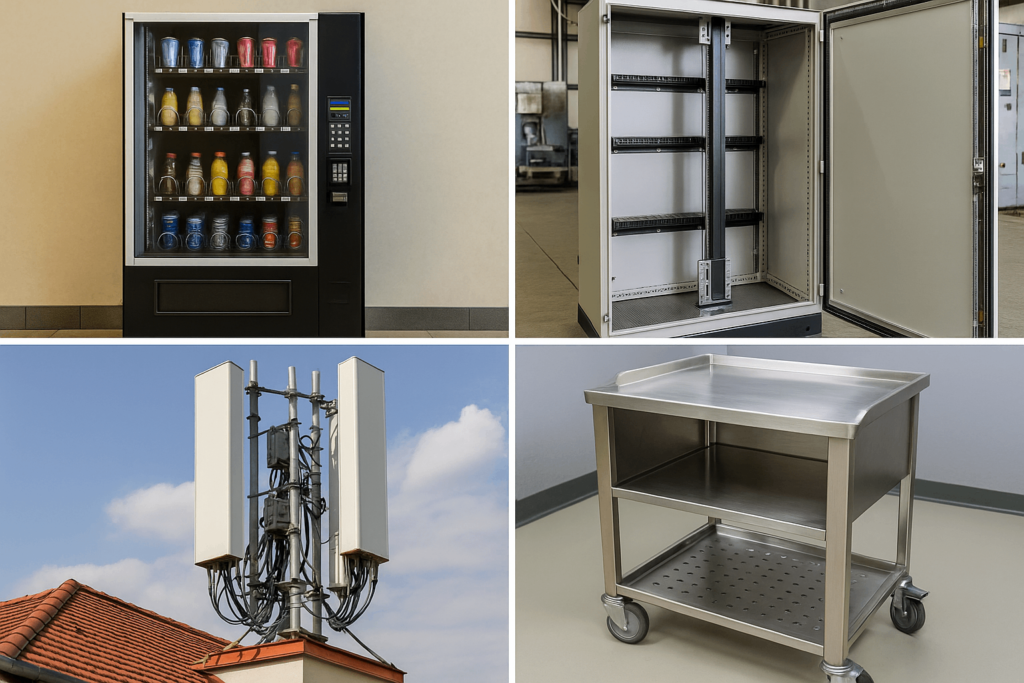
Invisible Mechanics: What Happens to a Material Under Tension
Deformation Starts at the Micro Level
Tension affects materials from the inside out. At the micro level, dislocations in the crystalline lattice start to move—this movement is plastic deformation. As tension increases, materials reach a point of necking, where they thin before failure.
Why Grain Structure and Alloying Matter
With carbon steel, fine-grain structures improve tensile strength by impeding dislocation motion. In aluminum alloys or brass, the grain size and alloying elements shift how the material performs under tension. That’s why 4130 steel tensile strength differs substantially from cold-rolled low carbon steel.
How Cutting Direction and Temperature Impact Performance
The tensile properties of a copper hinge plate influence not only formability but failure under load. If you’re sourcing brackets or mounts, ask whether grain direction has been aligned during cutting. YISHANG integrates such controls in our CNC cutting process.
Temperature and strain rate also play a role. Fast-loading scenarios (like snapping motion) favor materials with high strain-rate sensitivity. Heat exposure, on the other hand, softens most metals, reducing UTS. This matters if your assemblies operate outdoors or near machinery.
How Engineers Measure It—And Often Misread It
How Testing Is Done
Tensile strength is tested using standards like ASTM E8 or ISO 6892. Material samples are pulled apart using a universal testing machine. Force and elongation are recorded, and UTS is calculated.
Why Test Values Vary
However, test values can mislead. Differences in grip method, sample prep, and even ambient humidity impact results. Overseas procurement teams often compare values from different vendors, unaware that results may not be comparable unless tested under identical conditions.
Case Example: Misinterpreting UTS Equivalence
A frequent issue: assuming that stainless steel 304 and 4130 steel with similar UTS perform similarly. One may deform significantly before breaking, while the other may fracture abruptly. In critical applications, such as robotic joints or mounting arms, this distinction determines reliability.
Typical UTS Values by Material
Material | Ultimate Tensile Strength (MPa) |
---|---|
Mild Carbon Steel | 370–550 |
Stainless Steel 304 | 515–720 |
Aluminum 6061-T6 | 290–320 |
Brass (70/30) | 300–450 |
Carbon Fiber Composite | 600–1800 |
For projects requiring validation, YISHANG provides tensile test reports and batch traceability upon request.
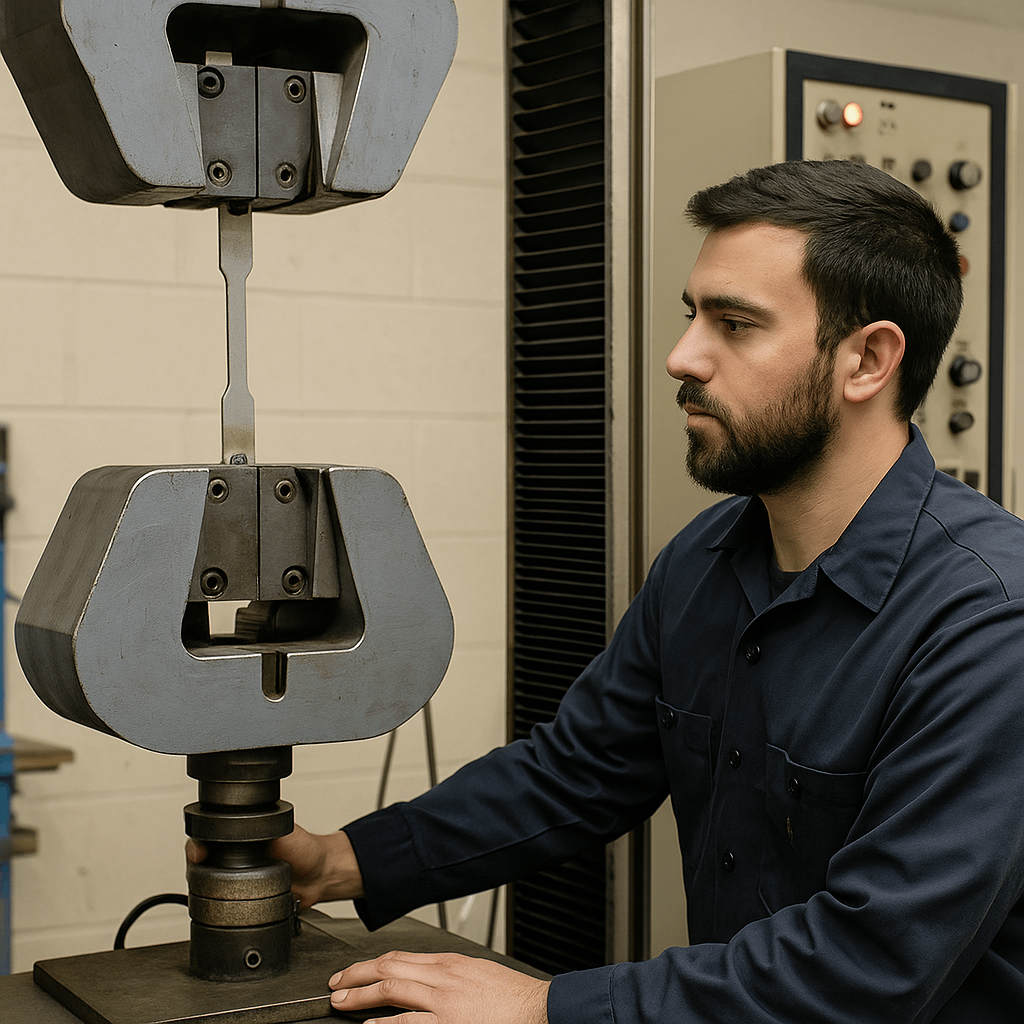
Beyond the Number: 5 Dimensions Hidden Behind UTS
Strength Isn’t One-Dimensional
UTS is only one piece of the puzzle. For sourcing engineers, focusing solely on it can lead to poor fit between material and application.
Supporting Metrics that Matter
Yield strength tells you when deformation begins—critical for enclosures or fasteners. Proof strength helps gauge the load-bearing limit for non-ferrous alloys like brass. Tensile strength at break defines the stress point just before rupture—important for parts under shock or fatigue loads.
Young’s modulus reflects stiffness. In structures that must flex slightly without permanent deformation—like some signage or cladding systems—this value matters as much as strength.
We often see buyers request materials with “the highest tensile strength.” But what they really need is the right balance. That’s why our engineers recommend a full mechanical profile review before confirming the material spec.
How Tensile Strength Shapes Real-World Design
Design Adjustments Based on Tensile Behavior
Every successful project starts with realistic mechanical expectations. In automotive structures, engineers use ultra-high-strength steel in frame components and controlled-ductility zones in crash elements.
At YISHANG, we’ve delivered precision-fabricated parts for energy cabinets, medical equipment, and industrial enclosures. For one customer designing battery housing frames, aluminum 6061 offered excellent machinability—but needed edge stiffeners to avoid distortion under tensile load.
Tensile data informed that design adjustment. Without it, the housing would have warped in transport.
Procurement Triggers to Watch
As a buyer, it’s not enough to know that a material is “strong.” The question is: strong enough for what? At what thickness? After what fabrication steps? If a bracket is CNC cut from 4130 steel, is it also heat treated to meet load-bearing expectations?
We help clients avoid surprises by proactively analyzing these connections between tensile data and downstream process behavior.
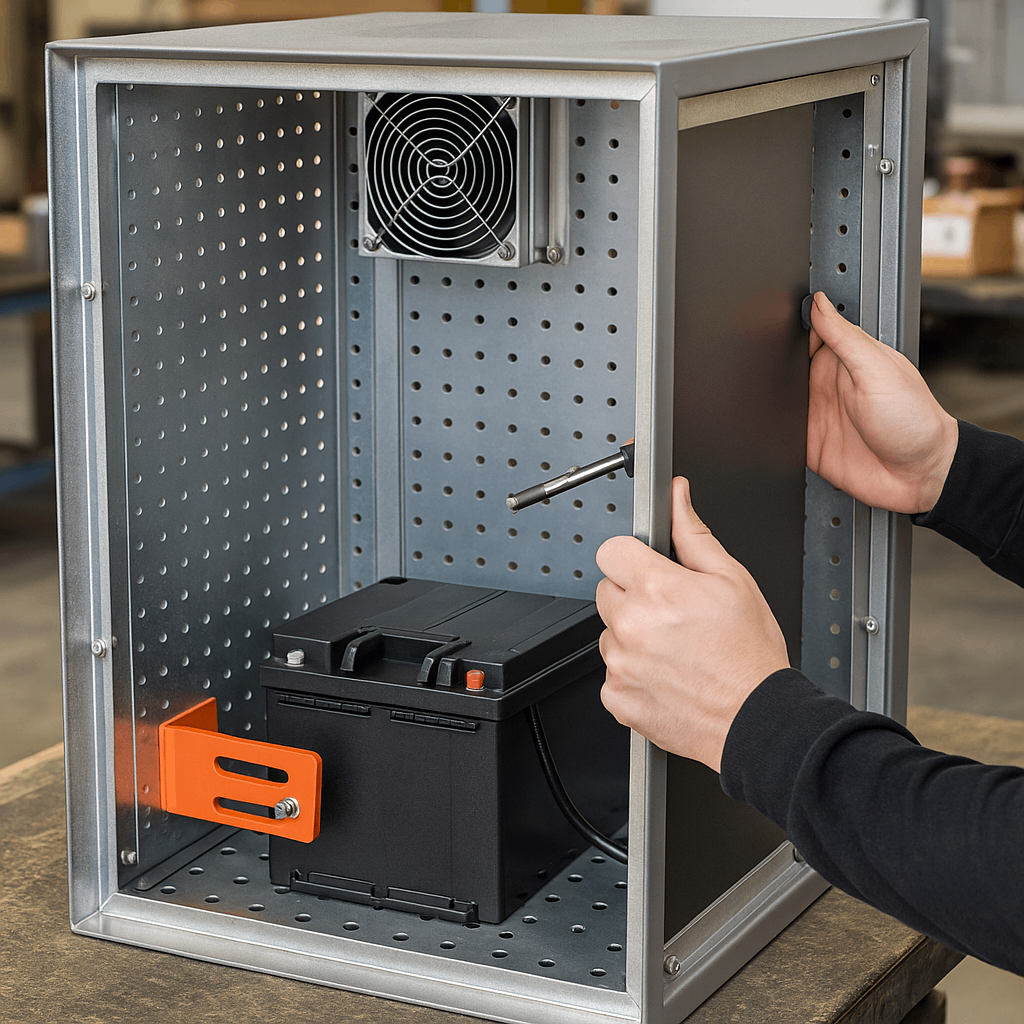
Making Procurement Safer with Stronger Material Understanding
International buyers often juggle multiple vendors, price lists, and spec sheets. When you add in unclear tensile requirements, it’s a setup for long-term risk.
At YISHANG, we support procurement teams with reliable data and practical insights. We don’t just send you a sheet with “carbon steel tensile strength = X.” We tell you if that X holds up after bending, welding, or laser cutting.
This has helped clients in telecom infrastructure and display systems reduce failure rates by over 20% after switching from a low-carbon sheet to a refined high-strength variant, with matched processing paths.
If you’re working with parts that require structural reliability—mounts, racks, hinge plates—don’t just look at price and UTS. Ask: has this material been used in similar applications under similar stress? Can the supplier provide comparative performance data?
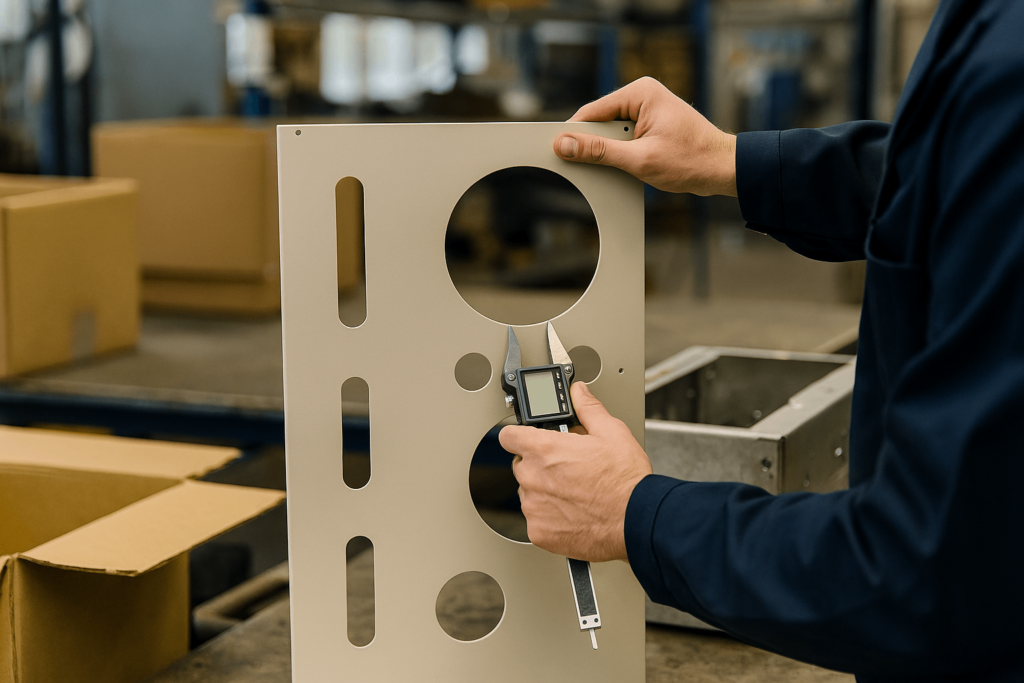
Common Questions from Buyers
Q1: What’s the difference between tensile strength and yield strength in a purchasing context?
Tensile strength is the maximum stress a material can endure before breaking. Yield strength is the stress at which it starts to deform permanently. For procurement teams, yield strength often determines if a material will hold shape under assembly pressure or shipping loads—making it especially relevant in frame or panel sourcing.
Q2: Is higher tensile strength always better?
Not necessarily. A higher UTS may reduce formability and make parts prone to cracking during bending or stamping. Many successful products rely on materials with moderate strength but better ductility and corrosion resistance. Balance matters.
Q3: Can UTS change after fabrication?
Yes. Welding, heat treatment, or cold forming can raise or lower tensile strength. It’s critical to confirm whether strength values apply before or after processing. YISHANG helps clients verify this with post-process validation.
Q4: How does brass ultimate tensile strength compare to carbon steel?
Brass typically has lower UTS than carbon steel, but its machinability and corrosion resistance often outweigh that limitation in connectors and decorative hardware. For structural load-bearing parts, carbon steel is more commonly used.
Q5: Should I request a tensile report from every supplier?
You should—especially for high-risk or load-sensitive components. It ensures the material has been tested under comparable conditions and helps avoid costly mismatches.
Need support choosing the right metal for your load-bearing or fatigue-sensitive parts? Contact YISHANG’s technical team for a tensile profile consultation or request a recent test report.